Navigation
Axis 0, Axis 1 and Axis 2 motor drive connectors (7W2 'D' socket)
Each machine axis is connected to the SPA3-2 via a 7W2 socket, as shown below:
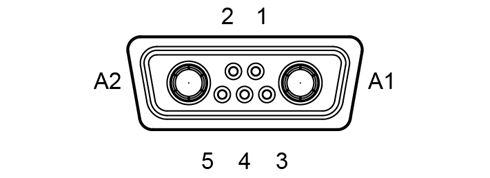
Pin number | Function |
---|---|
A1 | Positive motor connection |
A2 | Negative motor connection |
1 | Positive tacho input * |
2 | Negative tacho input * |
3 | Screen (tacho) |
4 | Negative tacho input * |
5 | Screen (tacho) |
Shell | Screen (motor) |
The table shows the default polarity configurations for all pins, both motor output and the tacho feedback signals can be reversed in UCCassist-2 during machine commissioning.
* NOTE: The motor tacho input supports a maximum differential input of ±100 V, tacho signals must be floating (i.e. not connected to ground or cable screen). Single-ended inputs can be used, however the maximum input in this configuration is ±18 V. It is therefore recommended isolated tachometers are used.
NOTE: The SPA3-2 is designed for a continuous combined output of 10 A at 80 V (800 W), and a peak output of 960 W for 1 second.
For ambient temperatures of between 40 °C and 50 °C the output power must be limited to 400 W.
CAUTION: Unused output connectors must be blanked off when not in use to prevent the risk of electric shock.
For SPA3-2 supply voltage of over 60 V, motor cables must have a minimum cross section of 0.75 mm² as specified in BS EN 60204-1:2018 (or current version) para.12.2 and have insulation rated to at least 150 V to provide adequate protection against electric shock.
CAUTION: Hazardous voltage warning labels must be fitted to motors where hazardous voltages are present.