Precision manufacturing case studies
Our metrology products help manufacturers to maximise production output, significantly reduce the time taken to produce and inspect components, and keep their machines running reliably. In the fields of industrial automation and motion systems, our position measurement and calibration systems allow machine builders to manufacture highly accurate and reliable products.
Manufacturing with process control
Challenge: Cookson Industrial wanted to make world’s most expensive metal viable for additive manufacturing.
Find out moreRonchini Milling (RM) Technologies specialises in CNC milling machines for non-ferrous metals, composites, and foam materials.
Find out moreChallenge: Machine tools can come out of alignment during transportation or operation so Autodesk wanted a reliable solution to check the accuracy of machine tool positioning performance.
Find out moreChallenge: Traditional measurement techniques, such as using granite squares, dial gauges and autocollimators, rely on manual operation and are susceptible to errors, rendering them unreliable.
Find out moreONENG’s wide range of motion platforms and micro positioning stages use Renishaw’s QUANTiC™ and ATOM™ series encoders and machine calibration products such as the XL-80 laser interferometer.
ONENG case studyChallenge: To design and build an air bearing motion stage providing high accuracy in six degrees of freedom.
Find out moreChallenge: To reduce the time taken to measure errors relating to volumetric precision.
Find out moreChallenge: To overcome part inspection bottlenecks, whilst introducing NIMS students to the precision measurement process.
Find out moreChallenge: Reduce manual intervention to boost component quality in high‑volume manufacturing.
Find out moreChallenge: To improve customer workflows by connecting the design to the machine using Fusion 360 and metal 3D printing.
Find out moreChallenge: Efficiently capture machine performance and calibration data to expand services to clients.
Find out moreSummary: An example of a machine shop applying innovative probing, tooling and workholding strategies to enable its turn-mill to machine castings complete.
Find out moreChallenge: To increase overall productivity, reduce turn around times and minimise human error.
Find out moreChallenge: To produce valves in the fluid power sector that are more efficient, sustainable and economical, to ultimately prevent the waste of millions of tonnes of CO2 per year.
Find out moreChallenge: Reacting to rapidly changing customer demand, which is becoming more complex and less predictable
Find out moreChallenge: Automate inspection processes and increase manufacturing capacity
Find out moreChallenge: Continuous improvement in part verification to address the demands of complex part designs.
Find out moreChallenge: Selecting a future-proof additive manufacturing system for flexible, high-quality end-use part production.
Find out moreChallenge: Eliminate inconsistent finish across batches of gears caused by manual deburring.
Find out moreChallenge: Inefficient and expensive process requires different instruments to measure individual parameters.
Find out moreChallenge: Maintain an accuracy of 15-20 microns and reduce non-productive time while machining aluminium die-castings.
Find out moreChallenge: Check the geometry of high-end machining centres before and after being transferred to new facility.
Find out moreChallenge: Reduce noise-induced positional errors would significantly improve tool performance.
Find out moreConsumer products
Challenge: Renishaw has collaborated with J.Laverack Bicycles on the development of a luxury bespoke bike, developing bespoke titanium lugs and components which pair to carbon fibre parts.
Find out moreChallenge: Create critical components, such as the boat’s runner, flap fairings, bowsprit and outhaul sheave box.
Find out moreChallenge: British Cycling needed to reduce part weight and improve aerodynamics.
Find out moreChallenge: Improve the handlebar performance and customisability of new Olympic track bike.
Find out moreChallenge: Transition from out-sourcing additive manufacturing to in-house production.
Find out moreChallenge: Increase productivity of existing injection moulding equipment.
Find out moreChallenge: To transition from out-sourcing additive manufacturing to gaining in-house capability. To streamline the finishing of high-end watch components.
Find out moreChallenge: To move from outsource to in-house production of vacuum cast juicer components.
Find out moreChallenge: A customised 2 wheel bike that matches the size and riding style of the rider.
Find out moreChallenge: Maximise machine up-time and to ensure consistent component precision.
Find out moreIndustrial automation
RM Technologies sourced Renishaw’s RESOLUTE™ and FORTiS™ encoders, ADTa-100 diagnostic tool, RCS P-series probing system, and QC20 ballbar.
Find out moreChallenge: Constant velocity control is essential for many advanced industrial processes, but traditional motor designs give rise to cogging forces which generate ripples in the motor velocity.
Find out moreChallenge: The rapid development of new technologies, such as AI and IoT, has challenged OEMs to develop new manufacturing equipment that caters for the latest advanced semiconductors.
Find out moreChallenge: A new family of advanced DDR motors required an absolute rotary encoder solution compatible with strict size constraints and demanding performance requirements.
Find out moreChallenge: JUSTEK required a range of custom encoder feedback solutions for its precision process equipment designed for the semiconductor and FPD industries.
Find out moreChallenge: Increase the overall competitiveness of the company’s products, including developing a precision-driven rotary table for the development of precision machinery.
Find out moreChallenge: An encoder than can be used even if the weather and local conditions are poor.
Find out moreMould & die
Challenge: To reduce the amount of time machine operators spend manually setting up workpieces, tools and probes.
Find out moreChallenge: Reduce part set-up times in the manufacture of injection-moulded parts.
Find out moreChallenge: Achieve an 85% reduction in the inspection time of injection moulded parts.
Find out moreMore application examples
-
Case brief: High-volume manufacturing - increasing the yield of precision machined components
Case brief: High-volume manufacturing - increasing the yield of precision machined components
Generic case brief highlighting the production and process challenges faced by high volume manufacturing companies, how Renishaw systems helped overcome these challenges and the benefits of installing Renishaw systems.
[1.6MB] -
Case brief: Precision sub-contract engineering: process improvement through automatic tool setting
Case brief: Precision sub-contract engineering: process improvement through automatic tool setting
Case brief highlighting the challenges faced by a British sub-contractor (QEP) when producing a wide variety of products and how Renishaw systems helped overcome them.
[1.3MB] -
Case brief: Precision sub-contract engineering: process improvement through automatic part setting
Case brief: Precision sub-contract engineering: process improvement through automatic part setting
Case brief highlighting the challenges faced by a British sub-contractor (QEP) when producing a wide variety of products and how Renishaw systems helped overcome them.
[1.4MB] -
Case brief: Precision sub-contract engineering: increasing manufacturing efficiency through in-process control
Case brief: Precision sub-contract engineering: increasing manufacturing efficiency through in-process control
Case brief highlighting the challenges faced by a British sub-contractor (QEP) when producing a wide variety of products and how Renishaw systems helped overcome them.
[1.5MB] -
Case brief: Mould and die manufacturing: ensure optimum accuracy and consistency
Case brief: Mould and die manufacturing: ensure optimum accuracy and consistency
Case brief highlighting the challenges faced by an British end user (BK Tooling) when producing high quality mould tools and how Renishaw systems helped overcome them.
[1.4MB] -
Case brief: Mould and die manufacturing: reduce operator intervention and increase machine productivity
Case brief: Mould and die manufacturing: reduce operator intervention and increase machine productivity
Case brief highlighting the challenges faced by an British end user (BK Tooling) when producing high quality mould tools and how Renishaw systems helped overcome them.
[1.5MB]
Find out more
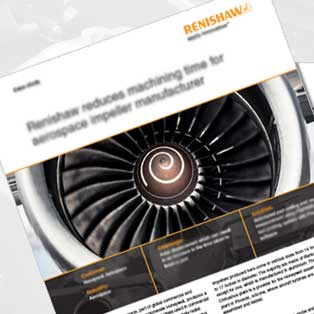
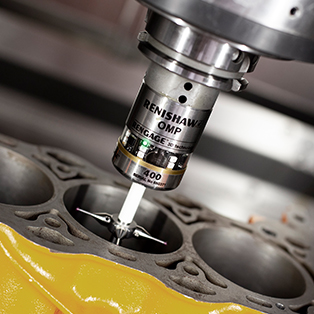