Achieving reliable, accurate tool setting for Standard Tool & Mold
Background
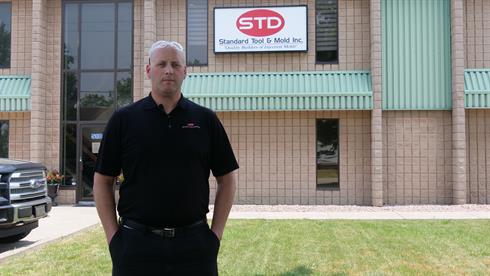
Founded in Windsor, Ontario, Canada, Standard Tool & Mold started in 1997 as a small machine shop and has since grown into a global business with facilities in Canada, China, and the US.
“Nowadays, we are involved in producing a variety of commodities, as well as supporting with product development, and we work hard to give customers exactly what they are looking for,” said Nathan Dyck, Engineering Manager at Standard Tool & Mold.
One common customer request from the automotive and heavy truck industry is the production of steel moulds for plastic injection, which Standard Tool & Mold manufactures on its 3- and 5- axis CNC machines. The company has a range of C-frame and bridge style CNC machines in different sizes, which it uses for small, medium and large machining projects, including fine detail cutting down to 0.5 mm.
“Standard Tool & Mold has been using Renishaw products since 2006, when we purchased a new machine that came with the NC3 tool setter already installed on it,” elaborated Dyck.
“Our non-contact laser tool setting systems use a beam of laser light, which passes between a transmitter and a receiver, positioned in such a way that the cutting tools can pass through the beam,” explained Brad Linscott, Business Manager at Renishaw Canada. “The tool passing through the beam blocks the laser light from reaching the receiver, then the tool moves out of the laser beam re-establishing the light reaching the receiver. This creates a trigger signal, which latches the position of the machine and provides the information needed to determine the dimensions and geometry of the tool.”
“It is also possible to identify broken tools using NC4 technology, by moving the tool into a position where it should intersect the laser,” continued Linscott. “If it doesn't, then the tool tip must be missing.”
Challenge
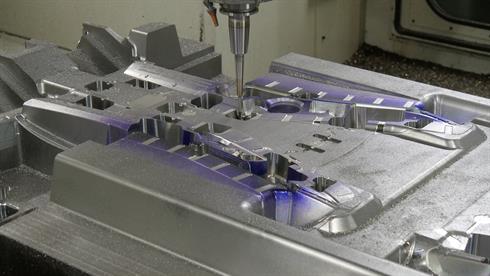
During machining processes, dimensional accuracy is dependent on several variables including: tool size deviation, tool run out, and tool breakage. Renishaw's NC4 systems allow users to control these variables, enabling the measurement of tools at production feeds and speeds, and minimising the risk of excessive tool wear or breakage, which is an important consideration for small and fragile tools.
“We have to be confident that there is no variability between different cutters, to prevent discrepancies in the moulds,” said Dyck. “Because we often do automated machining, where the machine is not attended by an operator, we need to be confident that when we change cutters, it is done precisely and that it blends properly, without marking the mould.”
“Our machines are running 24/7 for the majority of the year, which places a big demand on the laser technology,” said Dyck. “When one of the lasers on our machine failed, I contacted Renishaw to find out about replacing it.”
Solution
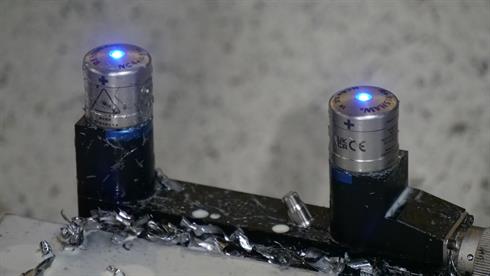
The NC4+ Blue non-contact tool setter includes an industry first — blue laser technology. Featuring improved optics, an operating gap of up to 240 mm, and an integral air blast, the product delivers a step change in tool measurement accuracy. The NC4+ Blue measures and detects tools down to Ø0.03 mm and to a repeatability of ±0.5 μm 2σ. It is suitable for machines with limited space due to its miniturised electronics and compact protection system, without a bulky shutter mechanism.
“Compared with the red laser sources used in conventional non-contact tool setting technology, blue lasers have a shorter wavelength,” added Linscott. “This improves the diffraction effects and optimises laser beam geometry. Ultimately, it enables Standard Tool & Mold to measure tools, including very small tools, while minimising tool-to-tool errors — a key consideration for a company that is using a wide range of cutting tools.”
"When we received the call from Nathan, we knew the new NC4+ Blue was a good option. This new tool setting technology provides high-precision, high-speed tool measurement and broken tool detection, enabling on-machine process control for a range of sizes and types of machine tool." Brad Linscott, Business Manager at Renishaw Canada.
Results
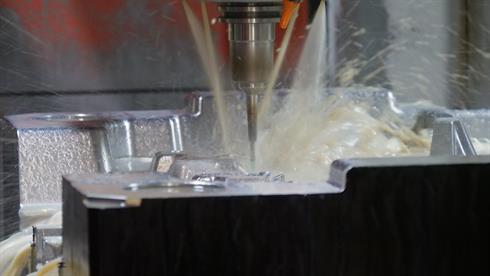
Renishaw supplied the new NC4+ Blue, which is able to accurately and repeatably measure the length of small diameter ballnose cutters, and specifically tool-to-tool length discrepancies.
With versatile mounting options, installing the NC4+ Blue systems was simple and fast; they were easily retrofitted to existing machines. The technology was supplied with Renishaw's latest non-contact tool setting software packages, which includes a new dual measurement mode and auto optimisation technology. This means even in wet conditions, the tool setter is fast and reliable, and can live up to the challenges of Standard Tool & Mold's demanding machining environment.
“Since we installed the NC4+ Blue, the machine has been consistently maintaining its accuracy,” added Dyck. “The machine that it's installed on gets both coolant chips and debris, and the NC4+ Blue has stood up well to this challenging environment and been very accurate and repeatable. The NC4+ Blue is working very well, and we haven't had any issues with it — there has been no need to stop machining to clean or maintain it.”
“The Renishaw team have attended our site to check we are up and running well, and gave suggestions on how we could improve quality,” added Dyck. “On another machine, we experienced a hard drive failure, and Renishaw helped us ensure we could connect the software on the new machine to the existing NC4+ Blue.”
“We're grateful to for the rapid turnaround — we've always found Renishaw to offer good support as well as great products, and this is essential to keeping our operations accurate and repeatable,” concluded Dyck.