Heavy industry
Precision at every scale
Manufacturing for the construction, agriculture, rail and heavy plant sectors requires high-quality and reliable large part machining capabilities. Renishaw offers a variety of solutions to solve the challenges associated with the machining of large scale, high-value parts on large machining centres.
Ensuring accurate motion of machining centres at every scale is vital for manufacturing process control at large scale. Machine calibration and maintenance are essential because small deviations in the movement of axes will become very pronounced on large machines. Machine movement can be tracked in real time to maintain precise motion using optical and laser position encoder systems.
Renishaw's machine tool inspection probe systems can be used to establish part location and material condition for parts such as large scale castings or forgings ahead of machining. A near net shape part can be placed into a machine tool with minimal setting; adaptive processes assess part position and alignment and determine stock to reduce set-up times and increase machining accuracy. Renishaw's tool setting systems monitor tool wear, especially while cutting hard-to-machine materials.
Many of Renishaw's machine tool inspection probes for part setting and in-cycle gauging are designed with large overtravel capabilities to compensate for the inertia of large machines. These probe systems communicate over long distances using robust radio systems for data transmission, so line-of-sight is not required.
CMM part inspection and verification is often essential for high-value parts. Renishaw's REVO® 5-axis measurement system offers a range of sensors to suit every inspection need, such as geometry and surface finish, with non-contact options available. Rapid motion from the CMM head reduces inspection time, while maintaining accuracy by minimising machine inertia and overtravel during inspection.
New manufacturing techniques, such as metal additive manufacturing (also known as 3D printing) are enabling manufacturers to produce stronger parts which could not be made using traditional methods. Additive manufacturing can also be used for prototyping new parts in fully dense metal, which can be invaluable during product design and testing.
Where we specialise
Machining
Heavy or complex parts can require multiple machining operations such as milling and boring, which require larger machine tools and are challenging to set up. Renishaw's range of metrology solutions enable tightly controlled manufacturing using inspection probes, tool setting systems and position encoders.
Inspection
CMM inspection is vital for high-value parts, ensuring that these components have met their design intent. Renishaw's CMM inspection systems offer rapid, accurate measurement to reduce overall lead time and to deliver precise, traceable results.
Strong structures
Metal additive manufacturing (also known as 3D printing) can be used to produce parts with advanced internal frameworks and structures to dramatically reduce the weight of a component, while maintaining its strength. As additive manufacturing produces shapes and structures that cannot be developed using traditional manufacturing, it creates the opportunity for internal cooling channels to be built into moulding tools, as well as custom cutting tools for niche applications.
How can we help you?
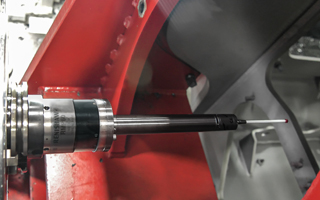
On-machine probing for in-process control
Machine tool probes are used for component set up, tool setting and in-cycle gauging, as well as first-off component inspection, to enable accurate machining processes.
Read the case study
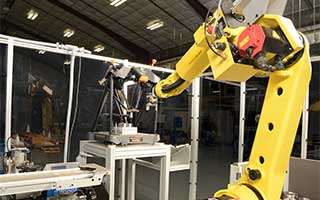
Shop-floor gauging
Renishaw's Equator™ gauging system delivers highly repeatable, thermally insensitive, versatile and reprogrammable gauging to the shop floor.
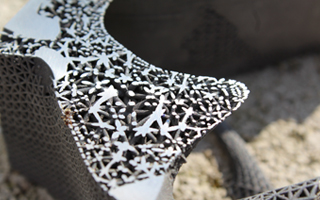
Additive manufacturing
Metal 3D printing using a range of metal powders to create strong but light components in forms impossible to achieve with traditional manufacturing.
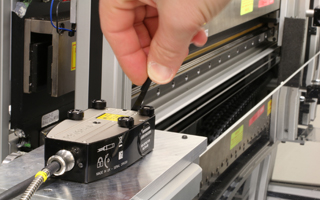
Laser encoders
Large components are common in heavy industries. The machining of these can be made accurate on long axes using Renishaw's interferometric laser encoders.
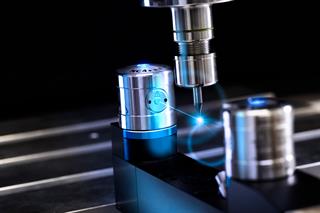
Tool setting and broken tool detection
Contact and non-contact tool setting systems to detect and adjust to the condition or wear of cutting tools.
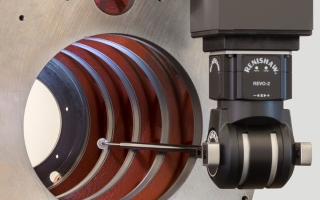
Inspection
Manufacturers around the world rely on Renishaw's CMM probing systems to achieve traceable inspection of a wide range of components.
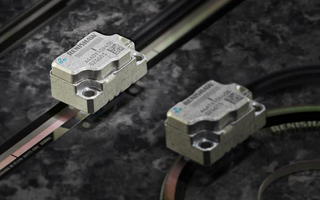
Position encoders
Interferometric laser encoders and optical encoders for high accuracy over long distances, or in tight spaces.
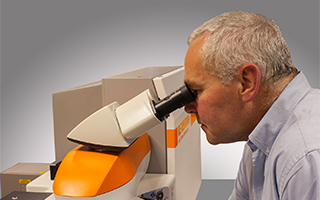
Raman spectroscopy
For checking the material make-up of specialist components and the quality of surface coatings.
Find out more
Want to know more about how we could help your business?
Heavy industry case studies