Renishaw brings AM innovation to Olympic track bike components
Background
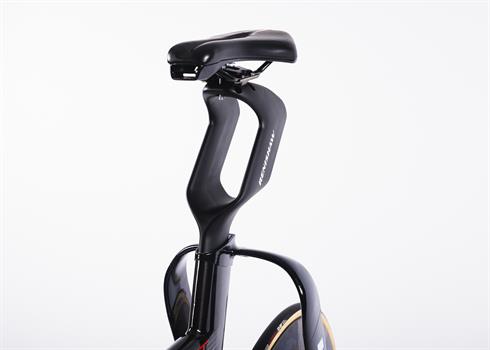
Track cycling is one of the fastest Olympic sports, with fractions of a second deciding who will take home a medal. Speed, balance and aerodynamics are integral to a rider's performance. Therefore, when designing a new track bike for the Paris 2024 Olympic Games, the British Cycling team considered how different manufacturing methods could achieve performance gains. As part of this, it turned to its partner, global engineering technologies company, Renishaw, for additive manufacturing (AM) expertise.
As the national governing body for the sport of cycling in Britain, British Cycling provides opportunities for riders of all backgrounds and abilities to fulfil their cycling potential in disciplines that include BMX racing, BMX freestyle park, cycle speedway, cyclo-cross, mountain bike endurance, mountain biking gravity, road and track. Three of these disciplines are in the Olympic Games; BMX, road, and track.
British Cycling has an active research and development team that design innovative bikes for the Olympic track cycling team. As part of the track event, athletes race in endurance and speed tests around an Olympic velodrome, where they can reach speeds of 60 miles an hour. Aerodynamics are therefore a significant factor when engineering bikes for track cycling and any opportunities to reduce the bike's weight, without compromising strength, can make a difference to a rider's performance on the track.
Challenge
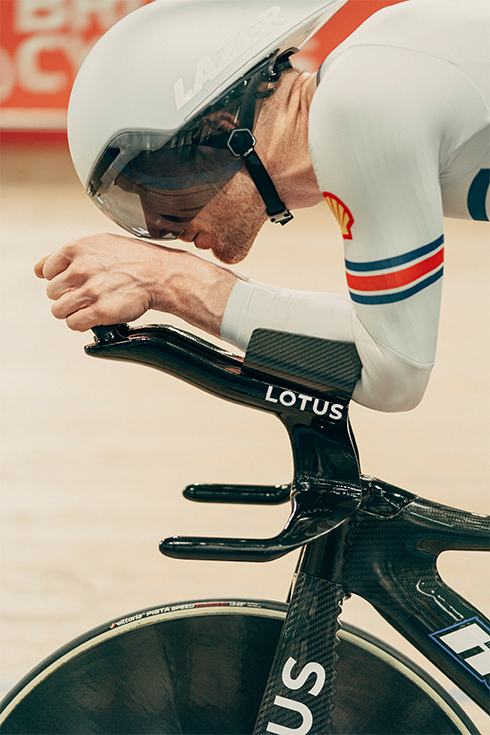
To develop a new track bike for Tokyo 2020, British Cycling partnered with Lotus Engineering, Hope Technology and Renishaw to develop and manufacture the HB.T bike. This collaboration resulted in a track bike that helped Team GB reach the top of the cycling medal table with seven medals at the Tokyo Games, which took place in 2021 due to delays from the Coronavirus pandemic.
“After the Tokyo Games, we knew we wanted to extend our partnership with Renishaw to optimise the track bike design ahead of Paris 2024, but because of delays to the 2020 Games and shorter deadlines to present a new bike, we were under significant time constraints,” explained Dr Oliver Caddy, Lead Project Engineer at British Cycling. “Working to shorter deadlines meant that we wanted to find the quickest and most efficient ways to reduce part weight and improve aerodynamics.”
Core components of the track bike, such as the crank and seat posts, were originally developed using traditional methods, such as injection moulding and traditional machining, to produce parts in carbon fibre. Producing parts using these methods requires the manufacturer to first develop tooling that can then be used to develop the final part.
“The carbon fibre parts produced using traditional machining methods for the Tokyo bike met all the requirements we had, but time constraints for the Paris bike meant that this method was no longer viable for some bespoke parts,” continued Caddy. “Components such as the crank and seat post are customised to the rider, so we needed to find a way to develop different sized parts quickly, while also using a method that could deliver the performance gains required for the application.”
“After seeing the benefits of AM and what it helped us achieve on the Tokyo bike, we knew it could be a manufacturing method to explore further,” said Caddy.
“From working together on the previous iteration of the Olympic bike, the British Cycling team valued our input and understood the benefits of AM and how it could achieve performance gains,” explained Ben Collins, Lead Additive Manufacturing Applications Engineer at Renishaw. “We knew AM would be a good method for producing the customised cranks and seat posts, but achieving the optimal design would take some work.”
“We began with solid carbon fibre parts and had to find a way to create a lighter, yet more structurally integral component that could be customised to the rider and meet the stringent requirements set for the weight and strength tolerances of an Olympic bike. As a result, we knew that we had to experiment with the British Cycling team to find the optimum geometries and internal structures for these parts,” said Collins.
Solution
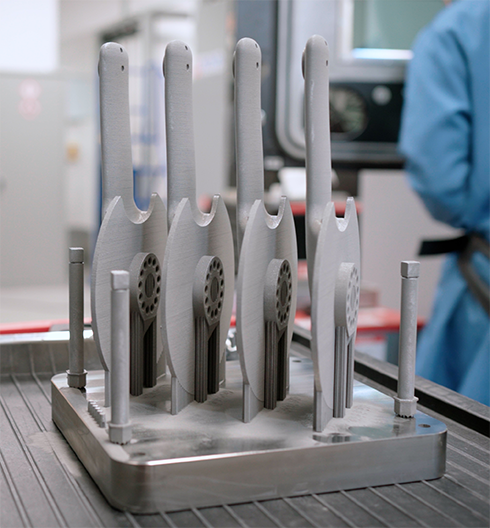
“We started by creating some additively manufactured prototypes in plastic,” continued Collins. “By taking the designs and findings from wind tunnel tests, we were able to create geometries that could improve aerodynamics and reduce the weight of the parts.”
After several rounds of prototyping and testing to make improvements, Renishaw and British Cycling agreed on the external designs for both the seat post and crank, as well as smaller components including the seat bridge and dropouts. Then, the teams collaborated to understand how to produce the final components in titanium.
“Additive manufacturing enabled us to create complex geometries that removed any unnecessary weight while delivering the strength required for the athletes to reach racing speed,” said Collins. “To develop a more aerodynamic seat post, engineers designed free-form geometries to hollow out the part as much as possible, something that would not be achievable using traditional methods.”
“The ability to add lattice structures was particularly useful,” continued Collins. “Latticing enables us to achieve the same stiffness as the original carbon fibre parts, but with reduced weight. Most commonly when using this method, latticing is consistent in thickness across the part. However, when evaluating the crank, we found that the strength and force applied to different areas added stress points — using the typical approach could have meant the part would fail under the force applied by the rider.”
To overcome this issue, Renishaw used topology optimisation software to create a more unique internal structure. Topology optimisation software enables engineers to submit the force applied to different areas of the part, so it can automatically determine the stress points and create a thicker structure, while designing in thinner lattices at low stress points for weight reduction.
The parts were then printed on the RenAM 500Q, Renishaw's four-laser metal AM system, designed to achieve high levels of productivity.
Results
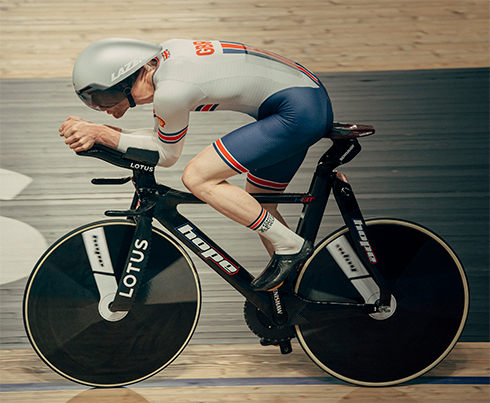
Following its work with Renishaw, British Cycling now has a first-of-its-kind aerodynamic seat post, featuring a hollow centre and backwards leaning design, allowing airflow through the centre of the bike. AM enabled the British Cycling team, alongside Renishaw, to rapidly produce these unique titanium seat posts to the exact measurements of the individual riders.
The new titanium crank contains an internal lattice structure to maintain the strength of the part but accommodate for the weight requirements. The crank has undergone ISO testing to ensure it can withstand the forces it will encounter through rides. A standard bike is tested against 1,000 Newtons, whereas an Olympic bike has to withstand 3,000 Newtons to account for the increased strength of the athletes.
“The Renishaw team has been incredibly reliable throughout the entire process of developing parts ahead of the 2024 Olympics,” explained Caddy. “The engineers have worked closely with our team to deliver any prototype or design iteration we need; it's clear that they are as committed as we are to delivering excellence on this project. It's also appreciated by the athletes that are working hard to ready themselves for their events and want as much practice on the bikes as possible.”
“Working with Renishaw has taught us a lot, not only about the specific parts we're producing for Paris 2024, but about where AM can deliver the most value in different applications and how design influences the properties of the final part,” concluded Caddy.
The new cutting-edge bike was ridden by Great Britain's track cyclists at the track cycling events, which took place between August 5th and 11th at the Paris 2024 Olympic Games National Velodrome.