5축 CMM 검사로 "즐기자"
스캐닝 프로브는 미국 몬타나주 Maryville에 위치한 Kawasaki의 공장에서 형상-데이터 수집과 머시닝 셀로의 피드백 속도를 증가시키고, CMM 고정물을 줄이고, 프로브 캘리브레이션 시간을 수시간에서 수분으로 단축시키고 있습니다. 측정 처리량과 유연성 증가로 인해 제조부와 R&D 부서에 대한 피드백 제공이 빨라지며, 스캐닝 CMM은 기어와 캠 리프트에 대한 검사 시스템을 완전히 제거할 수 있습니다.
Kawasaki는 "즐기자"라는 모토로 오토바이 매니아들을 고무시킵니다. 그러나 다른 종류의 즐거움이 미국 몬타나주 Maryville의 작은 엔진 공장에서 일어나고 있습니다. 이곳에서는 5축 스캐닝 프로브 시스템이 CMM 검사와 프로브 캘리브리에션 시간을 단축시키고, 소형 엔진 부품의 가공에 대한 QC 피드백을 가속화하고 있습니다. Mitutoyo Crysta-Apex 121210 CMM에 장착된 5축 Renishaw REVO® 시스템은 기존의 3축 CMM에서 SP25M 스캐닝 프로브를 사용하는 2개의 PH10 연결 헤드를 교체했습니다. REVO가 장착된 CMM의 스캐닝 집중 분야 검사 시간은 절반 이상 단축되었고, 프로브에 대한 사용자 정의 구성을 할 필요가 없으며, 프로브 캘리브레이션 시간이 6~7시간에서 약 45분으로 단축되었고, 대량의 형상 측정 데이터를 수집하는 새로운 기능이 추가되어 부품의 품질이 개선되고 있습니다. 그 중에서도 제일 중요한 것으로 손꼽히는 것은 REVO 시스템의 검사 처리량 대폭 증가, QC 부서의 데이터 품질 및 유연성, 제조부와 R&D 부서에게 유용한 전략적 지원 자원으로써의 가치 증진입니다.
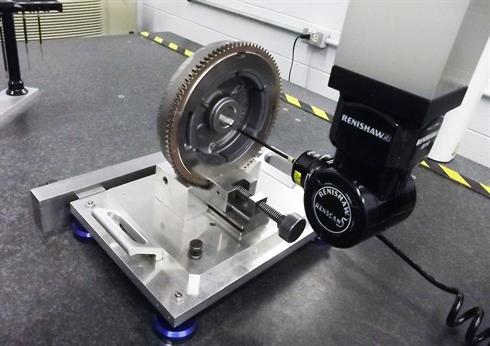
Kawasaki 생산 시스템
Maryville에서 1989년에 신설된 Kawasaki의 800,000평방 피트 규모의 공장에서는 상업용 및 소비자용 제초기 OEM과 ATV 및 Mule™ 유틸리티 차량을 제조하는 자매 공장을 위해 1000 cc 이하의 단일 및 이중 실린더 공냉식 및 수냉식 엔진을 생산하고 있습니다. Maryville 공장에서는 알루미늄 주조물, 플라스틱 사출 성형, 대량의 가공, 도장 및 조립 등의 작업을 수행합니다. 연간 약 50만 대 정도 생산되는 모든 엔진은 배송 전에 시범 가동합니다.
Maryville 공장의 품질 관리 기술부 책임자인 JC Watts는 "우리 공장은 Kawasaki 생산 시스템(KPS)을 활용하고 있으며, 비록 다양한 제품을 소량 제작하는 데 주력하고 있지만 품질 및 엔지니어링 요건은 자동차 업계 최고 수준에 견줄 만하다"고 말했습니다. 공장에는 50개의 가공 라인이 갖추어져 있으며 대개 가공 시작점과 종료점이 서로 마주 보고 있는 U셀 방식으로 배치되어 있습니다. Watts는 "원칙적으로는 한 부품이 고속으로 여러 공정을 통과하는 가공 라인에서 한 부품을 생산한다"고 설명했습니다. Kawasaki는 수많은 주조물과 그 외 몇 가지 가공 작업에서 Kawasaki 로봇을 통합시킨 자동화를 활용하고 있습니다. 크랭크케이스 라인 중 한 곳에서 로봇이 원자재를 싣고 완제품을 꺼내 재고로 옮기면 인출하여 조립합니다. 가공되는 부품은 알루미늄, 주철 및 강철입니다.
Watts는 "최상급 제품을 제작하기 위해 자동차의 동력 전달 장치에 적용되는 공차와 비슷한 수준을 유지하며, 알루미늄 부품에는 4~5개, 강철 부품에는 15개의 결정적 공정이 있다"고 덧붙였습니다. 형상에서 "마이크론 수준의 한 자릿수" 공차를 찾는 것은 드문 일이 아니며, 실제 위치 공차는 0.05 mm입니다.
QC 실험실은 125개의 다양한 대량 생산 부품과 공급업체 부품, 엔지니어링 개발을 위해 생산한 부품을 검사하는 업무를 담당합니다. 환경 제어 실험실은 가공 라인에 인접해 있으며 정기 검사를 위해 부품을 카트나 트레인(여러 개의 카트가 이어진 전기식 차량)에 실어 실험실로 바로 이송합니다. 중요한 부품은 라인 교체 중 또는 작업자가 문제가 있다고 의심했을 때 최우선 순위로 검사하기 위해 직접 이송됩니다.
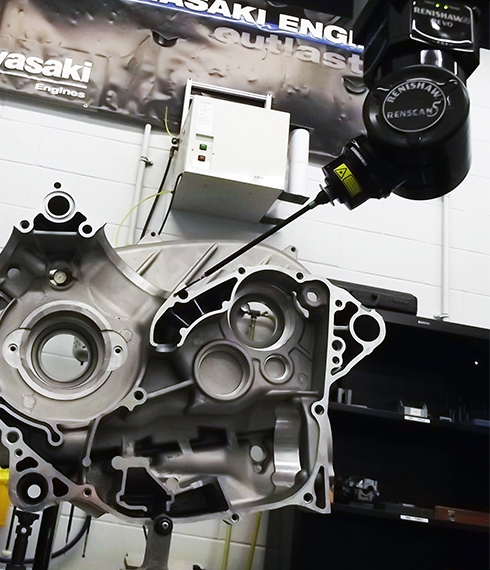
5측 스캐닝의 장점
Watts는 "이 공장을 가동하기 시작하면서 PH10 연결 헤드와 SP25 프로브가 장착된 3축 CMM 두 대, 그리고 고정식 프로브 헤드가 장착된 다른 CMM을 마련했다. 우리는 관절 프로브 헤드를 이용한 프로브를 구성했음에도 불구하고 기능에 제약이 있다는 점에 다소 실망했다. 우리 공장은 매우 다양한 프로브를 갖추고 있었기 때문에 캘리브레이션에 6~7시간이나 걸렸고, 결과적으로 처리할 수 있는 검사량에 한계가 있었다. 우리는 업계 표준으로 여겨지는 것보다 더 높은 수준을 원했기 때문에, 여러 가지 옵션을 검토하고 5축 REVO 시스템이 가장 빠르고 유연하다고 판단했으며, REVO 시스템이야 말로 우리 공장의 요건에 가장 적합하다"고 설명했습니다.
Kawasaki는 공장에 설치된 REVO 시스템으로 2009년에 신제품인 Mitutoyo Crysta-Apex 121210을 출시했습니다. 이어 첫 번째 기계를 가동하고 모든 파트 프로그램을 실행시킨 후 2010년에는 동일한 기계를 개조했습니다.
REVO 5축 스캐닝 프로브 헤드는 초당 최대 6000개의 데이터 점을 수집할 수 있습니다. 높은 정밀도를 요구하는 제품에 대한 정확한 검증을 위하여 대량의 데이터 수집이 필요한 곡면과 복잡한 형상의 고속 정밀 측정에 적합합니다. 2개의 로터리 축을 사용하는데, 무한 회전 및 위치 지정을 위해 이 중 하나는 수직면에 있으며, 다른 하나는 수평면에 있습니다. 5축 소프트웨어는 측정 헤드를 구동시켜 CMM의 리니어 축의 이동에 동기화시킵니다. 사전검증 알고리즘은 정확한 좌표 지정 연속 이동으로 프로브 경로와 CMM을 구동시킵니다. 초당 최대 500 mm의 스캐닝 속도로 이동 중 측정을 계속하고 스타일러스 팁과 변화하는 윤곽과의 접촉을 유지시키는 한편 헤드에서 위치를 조절합니다.
Watts는 "우리 공장의 SP25가 스캐닝 프로브이기는 하지만 3축 CMM으로는 스캐닝이 너무 느려서 95%는 접촉식 프로브 방식으로 작업했다. 접촉식 프로빙 방식이 부적절하다는 예시로는 실린더와 크랭크 보어가 적절할 것이다. 직경 80~100 mm, 길이 150 mm의 보어 형상을 측정하는 데 충분한 데이터를 정확하게 수집할 때 SP25 프로브는 시간이 너무 오래 걸리기 때문에, 기계 셋업이나 설계 부서의 특수한 요구를 검사하는 데 제약이 있었다. 현재는 측정하는 모든 크랭크케이스마다 REVO가 보어를 나선형 스캔하고 소프트웨어에 값을 출력한다. 또한 우리는 데이터 점으로 구성된 그래프를 공장 네트워크로 전송하여 QC, 엔지니어링 또는 생산 부서에서 누구든지 활용할 수 있도록 했고, 문제 해결에 정말 많은 도움이 되었다. 어떠한 문제가 생기면 눈에 보이는 실체로 나타낼 수 있다. SP25로 3~4분이 걸리던 작업도 REVO로는 10초 만에 측정한다"고 설명했습니다. REVO 스캐닝 헤드는 반드시 필요한 접촉식 프로빙 기능을 갖추고 있습니다. 현재 95%의 검사는 측정 시간의 제약을 가진 기존 프로브 대신 REVO 스캐닝을 활용하며, Kawasaki는 분석 중 컴퓨터의 처리 속도에 도전할 정도로 많은 데이터를 수집할 수 있습니다. REVO 프로브는 "헤드 접촉식" 프로빙 기능도 있으며, 상황에 따라 접촉식 기능이 필요할 때마다 기존의 기계-접촉식 프로빙 방식으로도 사용할 수 있습니다.
Watts는 "스캐닝으로 검사하면서 공장의 생산직과 기술직 직원들은 데이터의 유효성을 더욱 신뢰하게 되었다. 접촉식 프로빙은 샘플링 점이 7~8개 정도인 경우에만, 구형 상태를 벗어나게 하는 오염 물질을 편리하게 검사할 수 있다. 구형이 아닌 지점을 쉽게 찾을 수 있다. 우리는 접촉식 프로브로는 검출할 수 없었을 수 있는 특별한 편평도 오차 사례와 접촉식 프로브로 샘플링하는 데이터의 양 때문에 접촉식 프로브 방식으로 검출할 수 없는 실린더 보어 형상에 관한 사례를 기록해 두었으며, 여전히 부품이 출고되기 전에 이러한 문제를 검출하고 있고 해당 부품은 폐기 처분한다. REVO의 스캐닝 성능으로 인해 형상 오차를 검사 시 시간적 불이익을 받지 않고 더욱 빠르고 정확하게 찾아낼 수 있게 되었다. 예전보다는 확실히, 초반에 품질 문제를 미리 찾아내고 대응할 수 있게 되었다"고 덧붙였습니다.
REVO의 스캐닝 성능으로 인해 형상 오차를 검사 시 시간적 불이익을 받지 않고 더욱 빠르고 정확하게 찾아낼 수 있게 되었다. 예전보다는 확실히, 초반에 품질 문제를 미리 찾아내고 대응할 수 있게 되었다"고 덧붙였습니다.
Kawasaki (미국)
프로브 구성을 더욱 단순하게, 더욱 유연하게
현재 REVO를 사용하는 Maryville 공장에는 대량 생산 부품을 측정하는 프로브 구성이 2개 있으며, 일부 특수 사양을 위해 사용자 정의 프로브를 교체 랙에 보관하고 있습니다. REVO의 무한 위치 지정 앵글이 특수한 고정물이나 프로브 사용에 관한 고려 사항 없이도 부품을 측정할 수 있기 때문에 공급업체 부품에 대한 특별한 구성이 제거되었습니다. 캘리브레이션 시간은 약 46분으로 단축되었습니다. 이제 QC 기술자들은 매 교대 시마다 프로브 캘리브레이션 작업을 수행하는 대신, 캘리브레이션을 모니터링하고 있습니다.
Watts는 "이제는 2개의 구성만으로 모든 대량 생산 부품을 측정할 수 있다. REVO를 이용하는 경우 스타일러스와 공작물 간에 접근각도가 크기 때문에 볼 직경이 큰 스타일러스 구성이 필요없게 되었다. 스캔 중 REVO는 접근각을 유지하므로 실린더 보어와 같은 큰 원통형 형태도, 스타일러스를 탈거할 필요 없이 직경 5 mm의 보어를 측정하던 것과 동일한 스타일러스로 측정할 수 있다"고 말했습니다.
REVO 시스템의 유연성은 Kawasaki의 시간을 절약해 주는 것으로 입증되었습니다. Watts는 "고정물 몇 개만 있으면 특별한 캘리브레이션 없이도 기계로 어떠한 부품도 측정할 수 있다. 세 종류의 고정물에서 모든 부품을 측정하고 있으며, REVO 프로브는 먼저 정렬을 거친 후 부품 쪽으로 향한다. 부품 정렬 덕분에 측정 오차를 걱정할 필요가 없으므로, 특수 고정물을 활용할 필요도 거의 없어졌다"고 말했습니다.
Kawasaki는 Mitutoyo's Mcosmos 3.1 소프트웨어를 검사 루틴 프로그램으로 활용하고 있습니다. REVO 시스템으로 업그레이드하면서 공장은 자체적인 코드 개발을 통해 검사 루틴으로 사용할 모수적 및 모듈식 프로그래밍 개발을 추진했습니다. 이에 따라 부품마다 고유한 프로그램을 사용하게 되었습니다. Watts는 "공장에는 30종의 서로 다른 크랭크축이 있지만 크기와 위치만 다를 뿐 형상은 같기 때문에 동일한 검사 프로그램으로 모든 부품을 측정할 수 있다. 이것이 바로 우리가 얻은 가장 큰 장점"이라고 언급했습니다. 무한각 기능이 있는 REVO 시스템에서는 형상의 크기와 방향 때문에 부품 형상에 스타일러스가 걸릴 우려가 없기 때문에 모수적 프로그램을 간단히 생성할 수 있습니다. 프로브는 간단한 프로그래밍을 통해 일반 위치에서, 측정하고 있는 형상으로 자동으로 정렬됩니다.
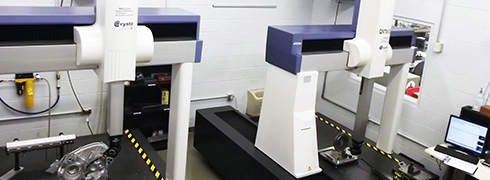
더 빠른 검사와 더 우수한 데이터: QC와 R&D
Watts는 "3축 프로그램에서 5축 프로그램으로의 전환은 어렵지 않으며, 초보 프로그래머도 3축 REVO 검사 프로그램을 작성할 수 있다고 말합니다. 그러나, 검사 속도를 최적화하기 위해서는 헤드 이동을 최대한 활용하는 것이 중요합니다. Watts는 "부품을 최대한 빨리, 측정 오차 없이 스캔할 수 있도록 지원한다. REVO는 다양한 가능성에 대해 열려 있고 제한이 적으므로, 초급 프로그래머나 고급자도 프로그래밍의 숙련 여부에 관계없이 원하는 속도를 얻을 수 있다"고 덧붙였습니다.
검사 결과는 가공 라인에 직접 전달하거나, 라인 작업자가 컴퓨터 로컬 네트워크를 통해 액세스할 수 있도록 조치할 수 있습니다. Watts는 "검사 보고서 중 일부는 머시닝 센터 좌표계로 직접 오프셋을 공급한다. 따라서 CNC 작업자가 오프셋 조정값을 보고서에서 바로 판독할 수 있고 입력해야 하는 값을 잘못 해석하는 실수를 방지한다. "최적 맞춤" 알고리즘의 여러 가지 장점을 활용하고 있으며, 생산 기술자가 정확한 조정과 동시에 여러 개의 공정을 조정할 수 있는 좀 더 복잡한 알고리즘으로 부품을 작업할 수 있도록 지원한다. REVO를 사용하기 전에는 얻을 수 없었던 기능이었으나 REVO는 모수적 프로그래밍을 활용할 수 있도록 지원하므로 더욱 편리하게 우리의 능력을 확장시킬 수 있다"고 설명했다.
Watts에 따르면, Maryville 공장의 5축 CMM 스캐닝은 속도, 데이터 품질 및 검사 능력의 측면에서 품질 관리의 판도를 변화시켰다. "우리는 2개의 기계에서 얻을 수 있는 커다란 이득을 향유하고 있다. 이 두 기계의 기능은 완전히 중복되므로 한 대가 고장나거나 캘리브레이션으로 인해 중단되더라도 별다른 문제 없이 다른 기계에서 핵심 부품을 측정할 수 있다. 이것은 QC 실험실에게 커다란 장점이 된다. 왜냐하면 QC 부서는 유사시 소형 CMM에서 큰 부품을 생산해야 하거나 현재 기계가 보유하지 않은 이상 각도의 프로브를 필요로 하는 부품을 생산해야 하기 때문이다. 우리는 특정 형상을 측정해 달라는 R&D 부서의 요청을 받곤 했는데 그럴 때마다 지정된 기간 내에 마치기에 거의 불가능했다. 이제 우리는 동료들이 신뢰할 수 있는 수준으로 데이터를 더 빨리 스캔하고 제공할 수 있다. 이러한 새로운 유연성, 고정물의 감소, 형태 측정, 모수적 프로그래밍 및 원자재 검사 속도는 부수적인 장점들"이라고 말했습니다.
Maryville 시설은 2대의 REVO 장착 CMM을 통해 50,000개 이상의 부품을 제작하고 있으며, Watts는 실행 가능성이 입증된다면 기어 검사와 캠 리프트에도 REVO 시스템을 사용할 계획이라고 내비쳤습니다. 아울러, "캠 리프트용 소프트웨어 안에 자체 알고리즘과 서브 루틴을 개발하고 있으며, 로브에서 리프트를 측정하기 위해 앵글과 프로브가 필요하기 때문에 이러한 작업은 REVO 시스템 없이는 어려울 것"이라고 말했습니다.
모든 이미지 및 텍스트 - 저작권 소유자: Renishaw