현재 사용 중인 언어로는 이 페이지를 사용할 수 없습니다. Google Translate을 사용하여
자동 번역된 페이지
를 볼 수 있습니다. Renishaw에게는 이 서비스를 제공할 책임이 없으며 번역 결과를 저희가 확인하지도 않았습니다.
추가로 도움이 필요하시면
저희에게 연락해 주십시오.
Ducati relies on tool breakage detection to produce unique camshafts
Ducati has realised that the machining of valuable components for its Desmodromic engines must be carefully controlled. Different tools are used hundreds of thousands of times during the course of a year, with the constant risk of a chipped or broken tool being picked up from the magazine, which would result in serious problems. This has been solved using a Renishaw tool breakage detection system based on innovative non-contact laser technology.
The most important stage of the Ducati Desmodromic camshaft production process is carried out on two Stama machining centres. The machines work non-stop throughout the year producing camshafts for all the different Ducati engines.
Fulvio Abbondi, Manufacturing Technology Specialist at Ducati Motor, comments, “Great precision is required when making the shaft, with the rather elaborate machining process carried out entirely within our factory. This is a very expensive component. It is made of a special steel alloy and is already expensive when, as a blank, it reaches the machine tool, after its first rough-turning”.
A tool breakage during the camshaft production process would be particularly serious, and could result in scrap, costly re-machining and wasted time. There could also be damage to the machine spindle which, when added to the cost of the specialist tools themselves, would total thousands of Euro.
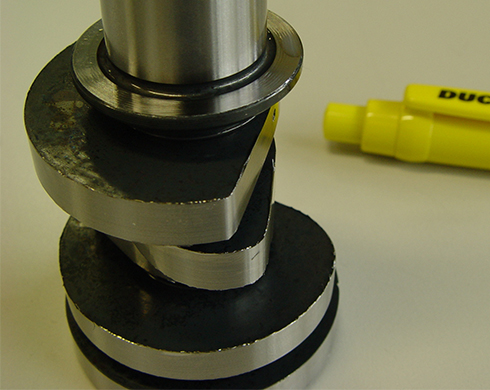
Taking control
Abbondi mentions the role played by tool breakage detection. “It is essential that checks be carried out on the work performed by the machines. Renishaw NC4 systems were installed on two work centres: immediately after a tool is loaded in the spindle ready for machining, it crosses the device's beam at a set height. If the cutting tip is broken, for example instead of being 100mm long it is 97mm, the laser system triggers an alarm. Clearly, each tool has its own length, diameter, etc. and the system takes this into account when the tool passes through the checking beam.”
He continues “The NC4 also allows us to check for breakages of small tools used to make keys and other reference points on the cam, which are vital if the engine is to operate properly. If it wasn't for the Renishaw system, the machine could, for example, operate with a broken cutting tip, with disastrous results. Furthermore, since tools are checked for breakage automatically, one operator can easily manage both machines: all he needs to do is load the pieces and ensure that everything is running smoothly”.
Process control critical to operations
As Abbondi describes; “the first thing we did was to install a system provided by the machine tool manufacturer which enables the power used by the spindle motor to be checked. This system checks the degree of wear of the larger bits, used to drill the deepest holes, in which the stress during machining is more apparent - if the torque increases, it means that the tool is worn and so the alarm goes off. But we also needed, quickly and reliably, to detect when tools break, even the smallest ones, which usually manage to escape most detection systems”.
Conventional contact-detection systems have certain weak points and are usually unsuitable for small tools - the tool is brought into contact with a “button” or “rod” which activates the device. There is also the danger that the contact itself could break or damage the tool. This means that work can only be done at low speed, which slows down the process and considerably lengthens cycle times. The systems must often be fitted inside the operating area, occupying valuable space and causing possible collision risks, not to mention poor reliability due to the fact that they tend to jam. This is why the Renishaw system was adopted, to replace these devices.
Checking with light
Improvements in laser technology have led to the development of non-contact detection systems, capable of safely measuring ever smaller tools. A laser beam runs between a transmitter and a receiver, fitted on the machine table or mounted on opposite sides of it, so that the beam crosses the operating area. When the tool enters the beam, the amount of light detected by the receiver is reduced, which generates a trigger pulse. If no reduction in light is detected, the system emits a tool-broken signal.
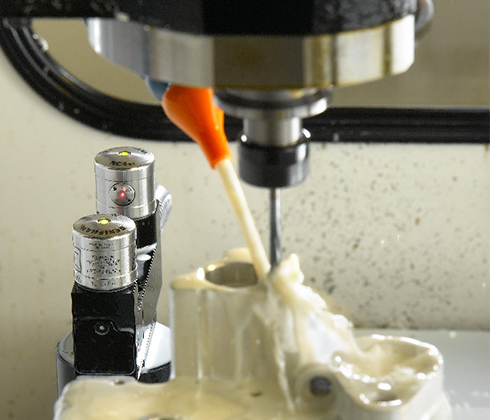
The Desmodromic system
The vast majority of the world's motor manufacturers use return springs in their engines to close the (exhaust and inlet) valves, these springs pulling the valve back to its original position after operation. The one exception to this is Ducati, achieving great advantages with a less conventional Desmodromic system. Desmodromic distribution offers greater engine reliability at high speeds, by solving the problem of spring inertia and reducing operating friction by about 30%. In theory the engine can easily top 20,000 RPM.
Desmodromic uses a mechanical system to close the valves, a concept originated in America but then abandoned due to excessive cost. Bologna's famous manufacturer had other ideas however, incorporating desmodromic distribution into its two-cylinder engines in 1972, and using this winning feature for decades. The valves are closed by a special cam rather than a simple spring, in every respect creating a strict link between the valve and its position - the term desmodromic originates from the Greek “desmòs”, meaning “link”.
The Desmodromic system introduces major complications to the design and manufacture of components such as camshafts. The cam itself is not a simple conventional cam shape, instead using special lifting ramps. Ducati's design team has carefully designed the shape so as to achieve the required acceleration and speed performance. Precision is everything; the “clearance” between the stem and the cam is adjusted by hand during assembly and is a critical operation. As Abbondi says “it's not possible to take up the slack as you can with hydraulic tappets on cars. We use one pad at the bottom and one at the top and these must be adjusted with extreme precision.”