현재 사용 중인 언어로는 이 페이지를 사용할 수 없습니다. Google Translate을 사용하여
자동 번역된 페이지
를 볼 수 있습니다. Renishaw에게는 이 서비스를 제공할 책임이 없으며 번역 결과를 저희가 확인하지도 않았습니다.
추가로 도움이 필요하시면
저희에게 연락해 주십시오.
Scania – where machine tool maintenance is an investment, not a cost!
Dynamate AB, the plant maintenance company for world leading truck manufacturer Scania, has implemented one of the most comprehensive and well-structured maintenance strategies in it's industry.
The radical changes Dynamate has introduced at Scania's Södertälje manufacturing plant near Stockholm have proven their worth, with massive improvements in machine accuracy and considerable increases in the capability of machines to produce accurate parts. Central to this is recognition of the importance of regularly monitoring machine performance over time within a standardised test procedure.
Scania is very keen to produce as many components as possible "in-house", the Södertälje engine plant supplying assembly operations in Sweden, Netherlands, France, Brazil and Argentina.
Karl Orton, Dynamate's Production Service Manager, is happy to make some very blunt statements about new machines – "We are a pain in the backside for machine manufacturers. Only 3 of 34 new machines purchased recently have passed ISO standards, as checked with our series of tests! Scania is now happy to pay for us to go to the machine supplier before the machine is delivered and perform tests so that the machine can be set up correctly. In the end, suppliers are more profitable since there are less service calls – they can use these profits to improve their products and technology."
Regular 20-minute tests
At least once a year, in many cases more frequently, every one of the 500 CNC machine tools at Södertälje is subjected to several tests, taking a total of one hour per machine. About 20 minutes of that time is spent running tests of machine positioning performance, using a Renishaw QC10 ballbar. Results identify immediate improvements that can be made after the test, such as adjusting a machine's software settings, or indicate where more fundamental maintenance work should be scheduled, for example component replacement.
The results of every ballbar test are recorded on history charts so that changes in the machines' performance are recorded over time. This allows Dynamate to predict when maintenance tasks will be required, rather than just 'fire-fighting' when machine performance becomes so bad that scrap is produced.
The ballbar test involves running a CNC program on the machine tool to trace out a circle of specified radius. The ballbar is coupled between the machine spindle and bed with special magnetic ball and cup mountings. As the machine describes the programmed circle, the ballbar monitors the radius of this circle, with deviations from the 'perfect' circle recorded by the QC10 ballbar software.
How well the machine follows the circular path is an indicator of the machine's positioning performance, and the Renishaw software is able to identify 21 separate factors and calculate exactly how much of the total error is contributed by each factor.
This 20-minute test method, which is exactly the same for all engineers in each location, is very good for both machining centres and lathes. Dynamate is trying to develop the same test for grinding and gear-cutting machines.
Instant machine improvements
Kjell Norstedt, Maintenance Engineer for Dynamate, is able to prove that the machine tool itself is often responsible for process problems, which production staff usually don't want to believe. The first test that he does on a machine often shows errors that weren't known before, and he is then able to demonstrate dramatic improvements. Mr Norstedt explains a typical example -
"One machine producing transmission parts had its program manually adjusted every few hours over the last few years, to keep component dimensions within tolerance. I ran a ballbar test in a matter of minutes and found a circularity error of 948 microns! Using values from the ballbar's analysis software I was able to immediately change the backlash compensation and reduce the circularity error to less than 400 microns. Once I change the motors most of the remaining error will be removed and they won't have to touch the program values again."
He continues, "Historically, a measurement of quality has been done after production, very few measure before, to analyse machine performance. At last somebody understands what we are saying – I have waited 20 years for someone to listen."
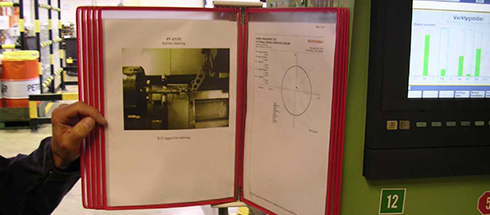
Knowing the status of every machine
Dynamate have asked the Scania production planners to classify every machine tool into A, B or C categories, according to five different measures:
- security (health and safety issues)
- high risk critical features
- high volume / time spent cutting
- redundancy
- intended future use
Within these categories, Dynamate plans the frequency and extent of the maintenance program and provide Scania with information on where machines are being stretched and problems are likely to occur. The QC10 ballbar is vital to this understanding of which machines are critical to production efficiency and bottlenecks.
Multiple aspects of each machine have been analysed, including structure and dynamics, to tell Scania how much longer it will produce good parts, which machines need renovating, and in some cases replacement. Many more existing machines can now produce higher accuracy parts for longer, because the root causes of problems are addressed rather then the scrap-part symptoms.
Dynamate goes from strength to strength
Dynamate is a wholly owned subsidiary of Scania, but runs as an independent business. Turnover has increased from €30 million in 1997 to €130 million in 2004, employing 720 people. New business has been won outside the Scania group, portraying themselves as a 'dynamic maintenance friend', in particular a very good 5 year contract with a steel company. As Mr Orton concludes "The biggest challenge is convincing people that monitoring machine performance is a production investment, not a cost."
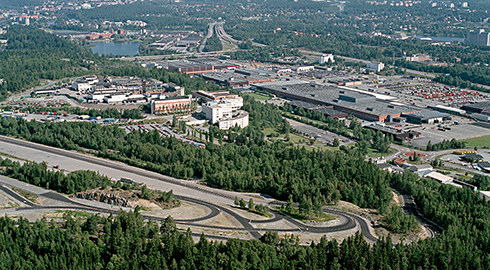