Ta strona nie jest obecnie dostępna w Twoim języku. Możesz zapoznać się z tłumaczeniem automatycznym, korzystając z usługi Google Translate. Nie jesteśmy odpowiedzialni za świadczenie tej usługi, ani też wyniki tłumaczenia nie były przez nas sprawdzane.
Jeżeli chciałbyś uzyskać więcej pomocy skontaktuj się z nami.
REVO-2 and the ATOM™ encoder
The REVO® multi-sensor system is one of Renishaw's flagship products and enables CMM users to perform 5-axis measurement on a 3-axis co-ordinate measuring machine (CMM).
It measures 1000s of points/sec and operates at speeds up to 500 mm/s. As the head is much lighter and more dynamic than the CMM, it is able to quickly follow changes in the part geometry without introducing harmful dynamic errors.
REVO-2 is an improved version of the revolutionary multi-sensor 5-axis measuring head for use on CMMs. REVO-2 and its new CMM controller, UCC S5, build upon the successful REVO multi-sensor system with enhanced power and communications capability to carry the latest REVO sensors such as the RVP vision measurement probe. The head has an increased range of movement in the negative tilt axis which can improve part access and reduce complexity of stylus setups. Infinite positioning further ensures that RVP vision probes can be placed in front of features at any angle.
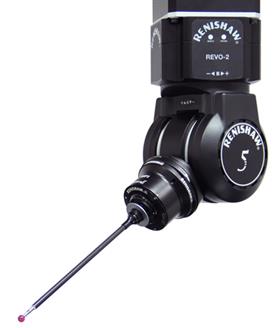
ATOM encoder solution
The REVO redesign has implications for the original onboard encoder, which was a custom design with a fine pitch 12 µm phase scale developed before highly accurate miniature encoders had been brought to market. REVO-2 incorporates Renishaw's latest ATOM incremental rotary encoder with RCDM rotary (angle) glass scales on both of its axes (yaw and pitch). It is the first product to have the ATOM encoder designed-in at the concept stage. ATOM was launched in 2014 as the world's first miniature encoder with advanced filtering optics and features the lowest cyclic error in its class. Each 20 µm-pitch RCDM glass disc (Ø68 mm) is face-read by a dual-readhead setup which helps to optimise REVO-2 performance by eliminating rotational eccentricity error. The ATOM readheads are connected, via an analogue filter and analogue-to-digital converter (ADC), to REVO-2's electronics. ATOM, with its advanced highly-automated manufacturing processes that minimise process variability to assure the best quality and the shortest lead times, was chosen by REVO-2's design team as the most cost effective solution.
In this application, ATOM offers leading-edge accuracy and speed that enable excellent servo-loop gain levels for outstanding position holding and accurate surface scanning of parts / components. The ATOM system was also chosen for several design features including:
- Its relative mechanical simplicity and optical disc alignment method using a microscope camera system for improved installed accuracy.
- Ease of setup in conjunction with REVO-2's electronics allowing both incremental signal calibration and auto-phasing of reference marks without oscilloscopes or external equipment.
- Availability of chrome-on-glass rotary scale, with a graduation accuracy which enables REVO-2 to achieve a resolution of 0.002 arc seconds, delivering high precision over the full operating temperature range.
In all, ATOM helps to streamline the REVO-2 manufacturing process, while still providing exceptional metrology performance.
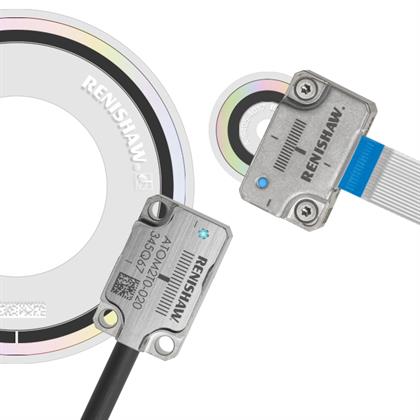
The ATOM encoder provides a level of plug-and-play convenience that simply didn't exist before. The ease of installation and alignment coupled with excellent technical support allowed the REVO-2 design team to fully meet the design specification while reducing overall production cycle time.
Renishaw plc (UK)
How does the ATOM encoder save time and money?
ATOM RCDM disc scales undergo acceptance testing before delivery, and are available in a comprehensive range of size options for every type of application. This has allowed Renishaw to bulk buy RCDM scale with absolute confidence in its manufacturing readiness level (MRL). Installation during REVO-2 manufacturing has also been streamlined by well developed procedures for mounting the ATOM readhead, with mounting brackets and shims available as orderable parts.
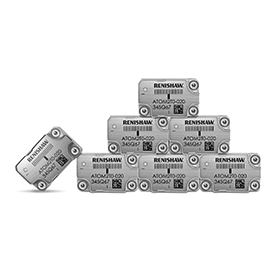
ATOM systems provide two different methods for disc alignment, one electrical the other optical, and REVO-2's dual readhead set-up allows either type to be used. In this case, optical alignment was chosen to give a simple and highly repeatable way of setting disc runout – to help minimise process variability. This technique uses a microscope, connected to a camera, to monitor the movement of the alignment band as the disc is rotated. The disc is adjusted until the total alignment band movement is to within design specifications. It had previously taken up to an hour or more to complete this operation and align and lock the custom readhead in place. Now, ATOM is designed to allow readhead / scale mounting and alignment within a couple of minutes.
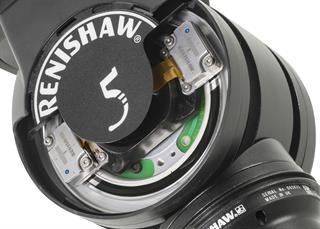
Another area of improvement has been in the setup calibration of the encoder once mounting and alignment has taken place. Prior to REVO-2, the reference signal was output to an oscilloscope in order to manually phase the reference marks on the scale - this procedure was time consuming and required a skilled operator. ATOM's set-up LEDs allow visual calibration and setting of encoder parameters in a way that is unparalleled in its class. An optional diagnostic kit is also available to further support set-up in situations where visual assessment of the readhead is difficult. REVO-2 has integrated electronics that allow direct interfacing with the CAL line and signal output channels and effectively perform the same function as the ATOM diagnostic kit, via a LabVIEW program.
Richard Toller, Technical Manager for Renishaw's CMM Products Division, explains: “The ATOM encoder provides a level of plug-and-play convenience that simply didn't exist before. The ease of installation and alignment coupled with excellent technical support allowed the REVO-2 design team to fully meet the design specification while reducing overall production cycle time.”
Choose the ATOM encoder to optimise your manufacturing process
Process optimisation may be the most important step in improving overall efficiency. The process engineer must ask: ‘How does each part, each machine and each production task affect the entire process?'
ATOM is designed to support manufacturing and servicing operations with unrivalled technical support, streamlined installation and robust calibration procedures. The end result is reduced process cycle times, higher unit yields, greater efficiency and lower production costs. REVO and ATOM are leading products that are now combined in the powerful REVO‑2.
For more information, visit www.renishaw.com/atom.