Podstawa procesu
Zapewnienie optymalnego stanu obrabiarki jest niezbędnym i zasadniczym elementem procesu.
Kontrola w warstwie podstaw Productive Process Pyramid™ zapewnia maksymalizację stabilności środowiska oraz parametrów działania maszyny, na której będzie prowadzony proces. Tego rodzaju kontrola zapobiegawcza redukuje możliwość wpływu przyczyn zmienności na proces obróbki.
Optymalizuj stan techniczny swej obrabiarki.
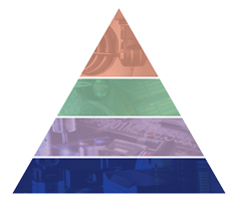
Podstawa piramidy Productive Process Pyramid, jak sugeruje jej nazwa, stanowi solidny fundament, na którym można zbudować zautomatyzowany proces o dużych możliwościach. Ma to na celu wyeliminowanie zmienności z procesu, zapewniając kontrolowane, stabilne środowisko, w którym proces obróbki może być efektywnie prowadzony.
Są to działania kontrolne zapobiegawcze, stosowane z wyprzedzeniem.
Optymalizacja stanu maszyny
Zapewnienie optymalnego stanu technicznego obrabiarki jest niezbędnym i zasadniczym elementem procesu, ponieważ niedokładna maszyna nie może wytwarzać części odpowiadających wymaganiom. Wnikliwy proces oceny parametrów obrabiarki, kalibracja oraz (gdzie jest to wymagane) modernizacja mogą poprawić parametry maszyny odpowiednio do wymagań procesu.
- Błędy pozycjonowania obrabiarki są jednym z najczęściej występujących powodów odrzucania detali ze względu na niewłaściwe wymiary oraz wykończenie powierzchni.
- Występowanie błędów pozycjonowania można przypisać błędom geometrii, dynamiki oraz luzów w obrabiarce.
- Błędy mogą wystąpić nawet w nowych instalacjach z powodu zmian pomiędzy ostatecznym odbiorem w fabryce i pierwszym użyciem w fabryce.
- Zużycie eksploatacyjne i „kolizje” obrabiarki także mogą powodować pogarszanie się stanu technicznego w miarę upływu czasu
- Jeżeli stan techniczny obrabiarki jest znany i podlega kontroli, badania przyczyn braku zgodności z wymaganiami powinny skupiać się na procesie, a nie na obrabiarce.
Kontrola zapobiegawcza
Obrabiarka „dopasowana do zadań” będzie zapewniać bezbłędną obróbkę w sposób stały i będzie w mniejszym stopniu narażona na nieplanowane przestoje. Oznacza to więcej czasu na skrawanie, a także umożliwia personelowi obsługi technicznej zaprzestanie zajmowania się naglącymi problemami i podjęcie działań proaktywnych.
Regularna kontrola stanu technicznego obrabiarek z rozbudowaną diagnostyką źródeł wszelkich błędów oznacza możliwość zminimalizowania zakresu obsługi technicznej i skupienia się na wartościowych pracach zapobiegawczych.
Systemy lasera XL-80 do kalibracji, QC20 ballbar oraz sprawdzian AxiSet™ są niezbędnymi narzędziami do uzyskania szerszego zrozumienia możliwości swych obrabiarek, ukierunkowania działań w zakresie obsługi technicznej oraz zachowania kontroli nad stanem technicznym swych maszyn.
Inne elementy kontroli w warstwie podstawy procesu obejmują:
Projektowanie ukierunkowane na produkcję — podejście do tworzenia i wdrażania projektu zakładające dokładne zrozumienie aktualnego potencjału oraz potrzeb i dążenie do wykorzystania najlepszych praktyk, a nie „wyważania otwartych drzwi”. Głównymi etapami są:
- Racjonalizowanie maszyn, materiałów i narzędzi,
- Optymalizacja metod i parametrów skrawania,
- Charakterystyka parametrów procesu,
- Informowanie projektantów / klientów o swych bieżących możliwościach wytwarzania.
Kontrola czynników procesu obejmuje korzystanie z FMEA (tzw. analizy rodzajów i skutków błędów) oraz technik podobnych, w celu zrozumienia i umożliwienia kontroli czynników, które mogą mieć wpływ na wyniki procesu obróbki. Może to obejmować zapewnienie stałej zgodności ze standardami geometrii ostrza i produkcji narzędzi, kontrolowanie elementów mocowania, zabezpieczenie dostępu do programów obróbkowych i przygotowania półproduktu.
Stabilność środowiska dotyczy takich zewnętrznych źródeł niezgodności, których nie można z wyprzedzeniem wyeliminować, a które są nieuniknione w środowisku produkcyjnym. Obejmują one zmienność temperatury otoczenia, fakt, czy maszyna jest rozgrzana, czy zimna, czystość maszyny i zamocowań oraz zarządzanie trwałością narzędzi. Głównym elementem kontroli w tym przypadku jest „przedstartowa lista czynności kontrolnych”, które mają dać pewność, że stan techniczny obrabiarki przed rozpoczęciem obróbki jest optymalny.
Projekt procesu ma także wielki wpływ na wyniki procesu. Systematyczne podejście do sekwencjonowania procesu wytwarzania stwarza najlepszą sposobność dla zapewnienia stabilizacji procesu oraz automatyzacji. Obejmuje to wybranie takich strategii obróbki, które umożliwiają wykorzystywanie offsetów narzędzi do kontroli rozmiarów i położenia obrabianych elementów, sekwencjonowanie obróbki zgrubnej i wykańczającej w celu uniknięcia odchyleń i odkształcenia termicznego wykończonych powierzchni oraz zintegrowanie w krytycznych etapach procesu informacji zwrotnych o procesie.
Dokumenty
-
Broszura: Systemy metrologiczne przeznaczone do kontroli procesu produkcyjnego
Poprawa produktywności dzięki usprawnieniu kontroli procesów produkcyjnych
-
Publikacja: Kontrola procesu produkcji warunkiem utrzymania konkurencyjnej pozycji firmy
Wielu producentów szuka sposobów na obniżenie kosztów produkcji, równocześnie nie jest w stanie pozwolić sobie na zakup bardziej wydajnego wyposażenia. Jakie są zatem możliwości radykalnego obniżenia kosztów bez wymiany maszyn? Niniejszy artykuł przedstawia cztery obszary, w których firmy gotowe zmienić sposób kontroli procesu produkcji, mogą odnaleźć oszczędności.