Navigation
MODUS 2 legacy software
The MODUS 2 metrology software suite brings new levels of clarity and efficiency to the programming and operation of CMMs.
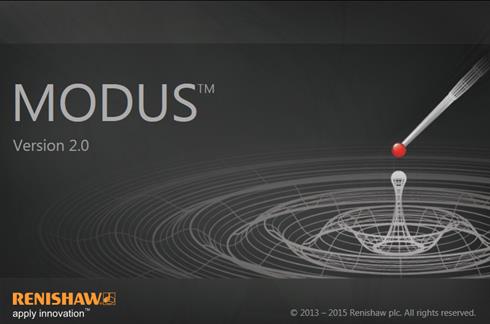
Designed with usability in mind, its clean interface is quicker for new users to learn, and faster to program.
Advanced algorithms calculate the most efficient measurement path across multiple axes, significantly accelerating collision-free motion.
As a result you can measure and inspect the critical features of more parts in less time.
MODUS 2 gives you timely process feedback – ensuring manufacturing to the highest specifications within today's tighter timescales.
Clarity
MODUS 2 features a node-based interface to reduce on-screen clutter. This clean design with its colour-coded section enables new users to rapidly become familiar with the system.
Operators can clearly identify and amend sequence details without searching through countless lines of complex code.
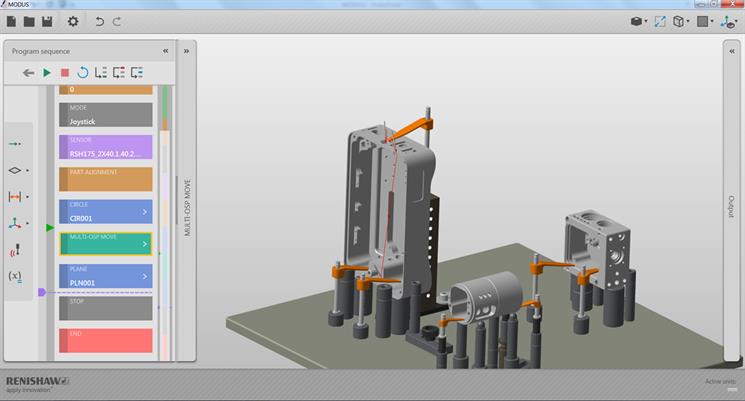
Usability
CAD models and the CMM environment itself are manipulated using direct interaction techniques.
Potential issues are highlighted on screen – the need for confirmation of actions in dialogue boxes has been removed.
Streamlined data entry and coding - inspection sequences for even the most complex workpieces are simpler to set up.
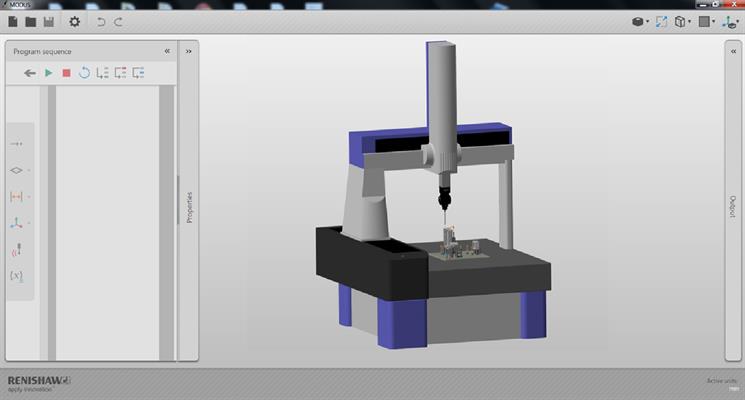
Efficiency
To save time MODUS 2 automates the intelligent extraction of CAD data, as well as enabling useful code sequences to be stored and reused.
As a result, individual users can now collaborate to develop one measurement strategy to be applied consistently across their organisation
Powerful off-surface motion planning algorithms generate efficient collision-free measurement paths around a workpiece.
These paths can be tested and tweaked on screen using the simulation feature.
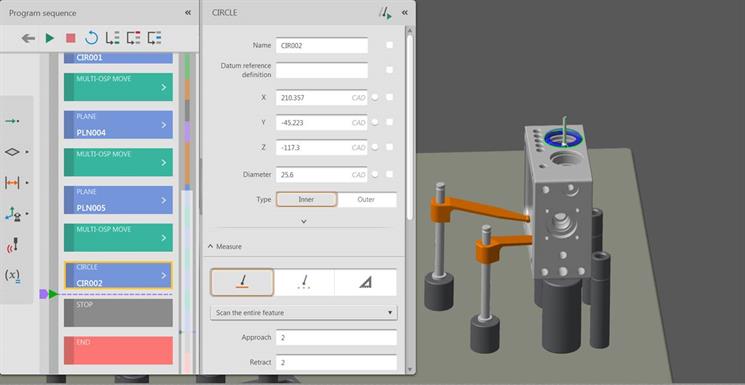
- Full support for I++ DME compliant metrology controllers, including Renishaw's UCC range of universal CMM controllers
- Full compatibility with 5-axis systems: PH20 and REVO
- CAD-driven offline programming, with support for neutral formats of IGES, STEP, Parasolid®, and VDA-FS
- High quality integration with CATIA® (v5 and v4), Siemens® NX™ (previously Unigraphics®), Pro/E® and Solidworks® CAD / CAM solutions
- Off surface planning for collision free measurement paths, including 5-axis paths
- Full motion simulation and path adjustment capability
- Native DMIS support
- Certified mathematical algorithms
- Powerful text and graphical reporting
- Flexible output of results data including certified Q-DAS
PC requirements
- 500 GB disk space (SSD drives and / or 1 TB recommended for high end applications)
- Intel (R) Core i7-6700 processor
- 8 GB RAM (16 GB recommended for large CAD models)
- 4 USB ports (for printers, memory devices, DK2 dongle, etc.)
- Network card required for PC connection to UCC controllers (further network cards may be required for connection to a company network)
- Minimum 4 GB RAM NVidia Quadro M series graphics card
- Dual monitors are recommended with 1600 × 1200 or HD 1920 × 1080 resolution
Supported operating systems
- MODUS 2 will run under the following operating systems:
- Windows 10 64-bit (for businesses, including Professional and Enterprise)
- Windows 7 64-bit Professional, Enterprise, Ultimate (Service Pack 1 minimum)
- To prevent possible data corruption occurring with newer hard drive types, it is recommended that you install the Windows hotfix available from this link:
- Windows XP, Windows 7 32-bit, Windows 8, Windows 8.1 and Windows 10 Pro 32-bit are not supported.
UCCsuite
- CNC (DCC) systems: MODUS 2 must be used with UCCsuite version 5.0.4 or above
- Manual systems: MODUS 2 M3 must be used with UCCsuite version 4.8.4 or above