Ta strona nie jest obecnie dostępna w Twoim języku. Możesz zapoznać się z tłumaczeniem automatycznym, korzystając z usługi Google Translate. Nie jesteśmy odpowiedzialni za świadczenie tej usługi, ani też wyniki tłumaczenia nie były przez nas sprawdzane.
Jeżeli chciałbyś uzyskać więcej pomocy skontaktuj się z nami.
SOLPOWER rotary tables turn on RESOLUTE™ encoders
Advances in processing technology and the demand for higher quality products have prompted machine tool manufacturers to develop technology that addresses rising raw material costs while responding to the market trend towards higher cutting speeds and demand in areas such as the production of high-accuracy mould tools.
SOLPOWER, established in 1995, is a Taiwanese manufacturer of machine tool components such as Direct-Drive (DD) rotary tables, integrated spindle motors and linear motors.
SOLPOWER has been actively developing a number of high-performance direct-drive (DD) rotary tables for the precision machining industry that greatly enhance efficiency and yield. Renishaw's RESOLUTE absolute optical encoders are compatible with a variety of industrial serial protocols and provide high-performance feedback control of the DD mechanism.
DD rotary tables eliminate mechanical linkages, for example as required for traditional worm-drive stages. Benefits of a gearless rotary table include higher speeds (RPM), faster response times, zero backlash, low noise and space saving. This amounts to an overall reduction in processing times and costs for the end-user.
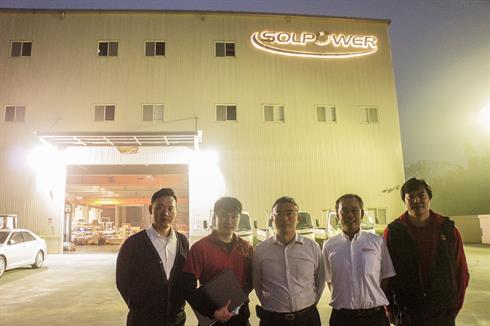
Challenge
With the recent drive to enhance processing technology in recent years, many machine shops are supplementing their traditional 3-axis machines with additional 4th and 5th axis rotary tables. Mr Bergan Peng, General Manager at SOLPOWER, shares his view of the rotary table market:
“A direct-drive rotary table is like a low speed integrated spindle motor with operating speeds in general of 200 RPM or less. Manufacturing cost control is vital to success in the machine tool industry. SOLPOWER has a wealth of mechatronics experience and the requisite wound-rotor motors and other components are manufactured internally, while the remainder are sourced from well-established Taiwanese manufacturers. Our rotary tables are frequently employed in 24-hour machining operations and we are a well-respected brand in this sector.”
Motion-control following errors come from many different sources. Typically, mechanical components, transmissions and position feedback systems (encoders) are among the main sources. In terms of the encoder error, there are several key components. These include: scale non-linearity, interpolation errors, installation errors, and signal jitter (noise).
All of these directly affect the system; generally, the smaller the encoder scale pitch, the better the interpolation cyclic error. The net effect of a reduction of encoder errors is to improve positional control and reduce velocity ripple, which allows a DD rotary system with smoother speed control and higher resolution. Clearly, these features are important for machine tool rotary tables in high-precision applications. RESOLUTE series encoders use 30 micron fine-pitch scale, have a cyclic error of less than 40 nm and jitter of just 10 nm RMS. When combined with generous installation tolerances and advanced scale types, there are few absolute encoders on the market that can offer this outstanding performance.
Encoder errors can be divided into repeatable (non-accumulative) or cyclic errors and random noise contributions. In enclosed-type encoder designs, cyclic errors are made worse by large contributions from bearing backlash, mechanical hysteresis and torsional motion resulting from insufficient stiffness. Error compensation, in this case, is only partially successful due to the presence of noise components. Open-type encoders, in contrast, do not rely on mechanical coupling between the scale and the encoder and, therefore, the vast majority of precision rotary tables specify open optical encoders.
Plot of position jitter (nm) vs time (ms) for RESOLUTE series encoders
Plot of cyclic error (nm) vs position (µm) for RESOLUTE series encoders
RESOLUTE encoders also offer a wide range of rotary (angle) scale diameters providing greater flexibility in product design.
SOLPOWER (Taiwan)
Customised design
In the current market, PC-based controllers for low-end machine tools are on the rise, but still mainstream traditional controllers by FANUC, SIEMENS, MITSUBISHI and the like, remain popular because customers generally prefer the quality assurance of these brands. Mr Peng continues: “High-speed cutting is the future direction of machining. Our business focuses on providing rotary table solutions in accordance with customers' needs.
An essential requirement is direct interfacing with the customer's controller, which impacts the choice of encoder. Renishaw's RESOLUTE series encoders offer compatibility with many popular industrial serial communications protocols including BiSS (to the PC-based controller), FANUC, MITSUBISHI, PANASONIC and SIEMENS. RESOLUTE encoders also offer a wide range of rotary (angle) scale diameters providing greater flexibility in product design.”
Enhanced competitiveness
SOLPOWER takes full advantage of its years of experience and market position in the field of DD motors and continually develops its product offering to meet the needs of a highly-competitive industry. Mr Peng explains: “We developed the most cost-effective rotary table possible, which means that cost must be strictly controlled from design, parts procurement to production. Renishaw as a major supplier is an important part of our cost-efficiency strategy.”
SOLPOWER's SDRT series rotary tables have a single rotational axis and are designed to be compact with a high-torque and high-speed response. When integrated into the SDRT rotary table design, the RESOLUTE RESA absolute rotary encoder series offers 23-bit resolution; positioning accuracy and repeatability after compensation of ±10 arc seconds and ±4 arc seconds, respectively; maximum speeds up to 200 RPM and IP67 protection - sufficient to meet the requirements of the vast majority of precision light machining applications.
Mr Peng continues: “These rotary tables have limited space and so the encoder readhead volume, in particular, needs to be small; ease of installation is another important consideration.
Renishaw's rotary encoder has a unique patented taper mount that effectively reduces installation errors and improves our assembly-time efficiency. Renishaw's support engineers provided training to enable our staff to install the scale.”
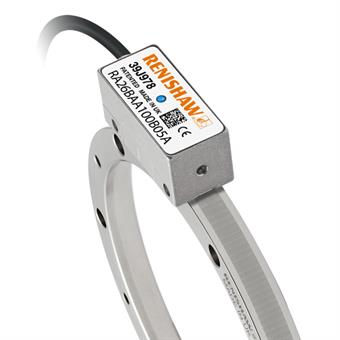
Quality verification
Product sales strategy in a competitive market is important, but the key in the final analysis is the quality of the product itself. Mr. Peng concludes: “Prior to leaving the factory, each of our SDRT rotary tables undergoes a strict quality testing regime. We currently use Renishaw's XR20-W rotary axis calibrator with XL-80 laser. The XR20-W calibrator features a measurement accuracy of ±1 arc second. Renishaw's calibration equipment is well respected in the international measurement community and greatly enhances the confidence of our customers.”
Renishaw is certified and audited regularly to the latest 9001 standard for quality management systems. This ensures all aspects of design and manufacture remain at the highest standards. All of Renishaw systems are factory calibrated and delivered with traceable certification.
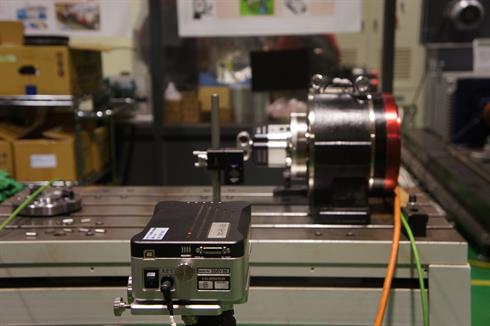
XR20-W rotary axis calibrator in-situ with Renishaw's XL-80 laser system in the foreground