Precision calibration products help produce high-quality, high-end machine tools
Increasing machining precision has always been the goal for machine tool manufacturers. Machining accuracy can be affected by various factors, including guide rail installation errors and assembly defects which cause geometric and spatial positioning errors. If these errors are not eliminated or reduced, they will directly affect the final machining accuracy of the machine tool, thereby impacting product quality and efficiency. Machine tool manufacturers need to find solutions to this challenge.
As technology advances, traditional measurement tools are no longer able to meet the machining precision and efficiency requirements of today's machine tools. The single-beam laser interferometer is a commonly used measurement tool that assesses the positioning accuracy of a machine tool by measuring parameters at a specific location. However, this method can only analyse the positioning accuracy of the machine tool based on the measurement results at that specific location and is unable to comprehensively evaluate machine tool error as a whole. An issue that is even more apparent with five-axis machine tools.
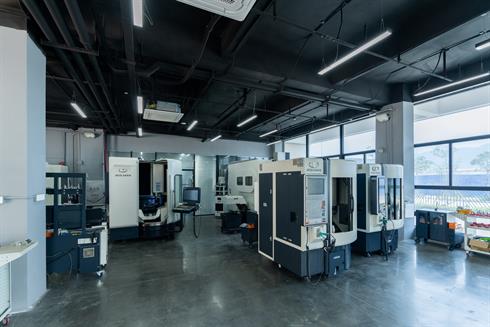
To solve this problem, Guangdong Jinke Machine Tool Co., Ltd (Jinke), one of China's most advanced manufacturers of five-axis machining centres, began using Renishaw's comprehensive machine calibration solutions. They use them to check the quality of their machine tools, from assembly, full machine calibration and acceptance inspections, to troubleshooting and daily precision maintenance.
The machine tool industry is very demanding and has stringent requirements in terms of the consistency of function, performance and precision. We started using Renishaw's full range of calibration products early on and benefited from very comprehensive support from their Technical Support Team. In the process, we also acquired a great deal of technical knowledge regarding measurement.
Jinfu Kuang, General Manager,
Guangdong Jinke Machine Tool Co., Ltd. (China)
Challenge
Machine tool assembly
Benchmarking of machine tools plays a crucial role in the accuracy of machine tool assembly and adjustment. Particularly for precision machine tools where it is vital to control accuracy, starting with the casting of the machine tool base.
Jinke primarily uses the Renishaw XK10 alignment laser system during the machine tool assembly process to check various measures of geometric precision, including straightness, flatness, perpendicularity and parallelism. Before the introduction of the XK10 laser system, the machine assembly process was based on traditional tools such as digital test indicators, dial gauges, granite squares and autocollimators. However, these tools needed a lot of storage space and several operators working together to complete the calibration. Traditional tools are heavily reliant on operator expertise which requires regular maintenance, manual recording and archiving of inspection data.
This changed with the implementation of the XK10 laser alignment system which has replaced all the traditional tools previously used and can be used with different models of machine tools. The technology not only simplifies and speeds up operations but it also automates data archiving for easy traceability and management. This digital display unit brings convenience to the machine tool assembly process and improves overall efficiency and accuracy. Mr Jianzhuo Shao, Technical Director at Jinke, explains: “The XK10 alignment laser is very lightweight, freeing operators from handling heavy granite squares and improving our production efficiency by more than 200% compared to using conventional tools.”
Jinke was highly impressed with the XK10 system's ability to accurately measure straightness. With the XK10 system it is possible to obtain both horizontal and vertical straightness data in a single measurement. In the past, custom fixtures were required to measure parallelism of non-coplanar rails, increasing overall cost. It is impossible to use traditional tools to measure machines with unusual structures. As Mr Shao explains, “The XK10 alignment laser makes machine assembly more efficient and increases production capacity without increasing labour costs. This allows us to deliver products quicker, boost our competitiveness, and win more orders.”
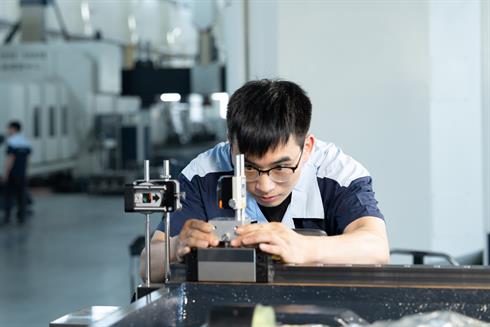
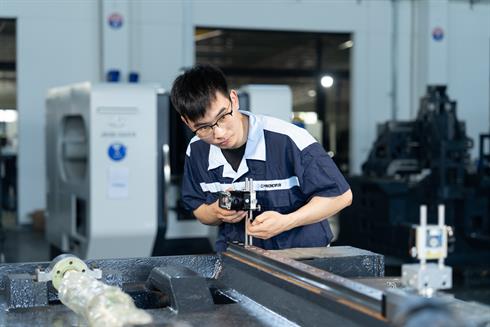
Machine tool verification
The structure of machine tools is becoming ever more complex as workpiece manufacturing processes require increased precision. It is not enough to simply measure linear performance. Frictional effects and other faults in the spindle structure can cause the spindle to rotate as it moves, leading to deviations between the specified and actual positions of the machine tool components. These angular and straightness impacts can result in significant positional errors or deviations in contours and surfaces, leading to non-conformity in workpiece dimensions, and increasing the scrap rate.
After assembly, technicians need to verify the performance and accuracy of the machine tool and calibrate or compensate, as necessary. Jinke uses the Renishaw XM-60 multi-axis calibrator for the verification of five-axis machine tools. This includes linear axis error source analysis, spatial accuracy testing, spatial accuracy compensation, dynamic straightness measurements, and positioning accuracy uncertainty analysis.
Jinke chose the XM-60 system because single-beam laser interferometers have limitations. They use single-parameter measurements that cannot accurately obtain displacement information in two directions of the optical path at the same time. They cannot measure angles on the tested machine at different positions during the measurement process, such as roll angle. This makes them unable to measure errors in spatial straightness and Abbe errors.
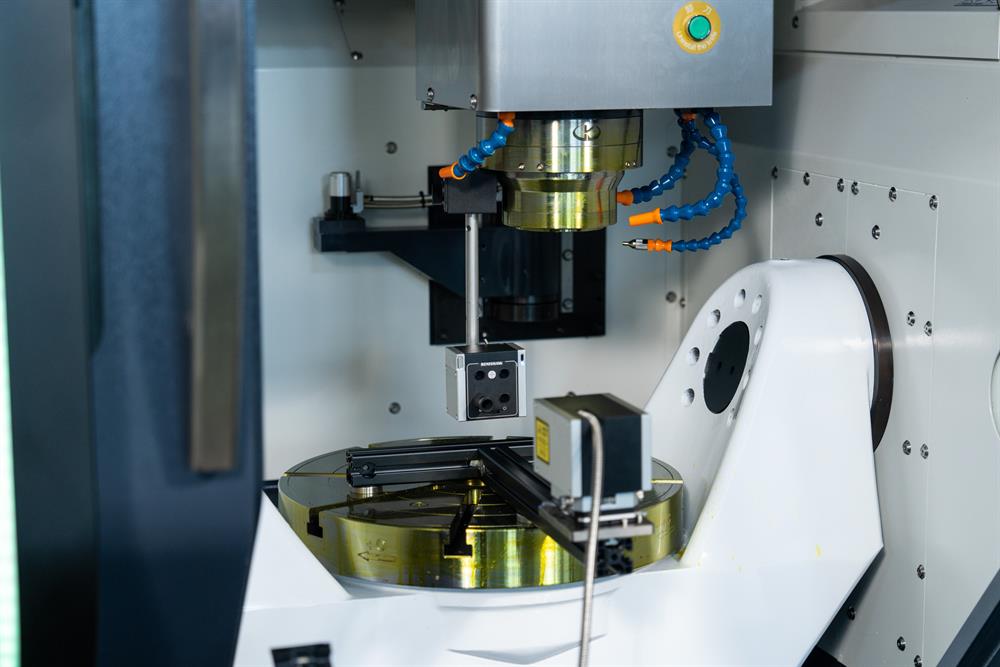
In the past, users of single-beam laser interferometers would consider a machine axis to be adequately meeting machining requirements if it passed a positional accuracy test on a specific location on the machine axis. However, in actual machining processes, there are situations in which a machine that has passed positional accuracy checks may experience issues with the quality of part machining. This is because a machine may suffer from a variety of large angular errors that prevent it from meeting the overall spatial accuracy requirements of the entire machine.
The conclusions about the machine tool's positioning accuracy are based solely on measurements taken at one location. This is insufficient to provide a comprehensive representation of the axis spatial error information, making the results insufficiently thorough. In real-world applications of machine tool precision verification, it is often the case that positioning accuracy can vary widely between different positions on the same axis. An issue that is particularly apparent when machining with five-axis machine tools.
Solution
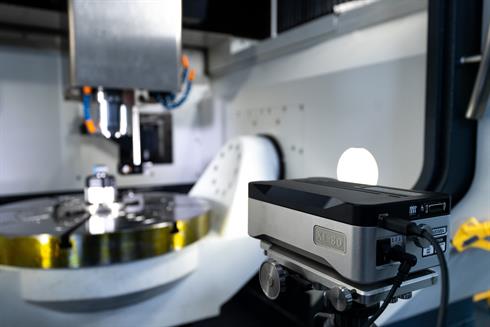
Before multi-beam laser calibrators were available, manufacturers used single-beam laser interferometers to measure precision machines and could only measure a single error parameter each time the device was set up. Jinke was no exception to this rule, using the Renishaw XL-80 laser interferometer and XR20 rotary axis calibrator to test their machines. As Technical Director, Mr Shao explains, “Since we began using the Renishaw XM-60 multi-axis calibrator, we have found that it measures more efficiently and simplifies both set up and operation. It can measure errors in six degrees of freedom with a single set-up, including roll angle measurements. The CARTO software quickly analyses the sources of the errors. Using the XM-60 system has increased efficiency by a factor of four or more.”
Jinke uses the XM-60 system for the calibration and verification of five-axis machine tools, analysing the root causes of major spatial and geometric errors, and laying the foundations to maintain mass production and precision assembly. For measuring other machine models, Jinke continues to rely on Renishaw's XL-80 laser interferometer.
Renishaw's XM-60 multi-axis calibrator is a compact advanced four-beam system that uses interferometer principles for both angular and linear measurements, combined with the simplicity of a position-sensitive detector (PSD) for measuring straightness. The XM-60 laser directly measures machine tool errors by collimating the laser beam with the machine axis. This method provides greater traceability than other measurement techniques that employ complex mathematical calculations to obtain machine error. In addition, unlike other products, the XM-60 system uses a patented optical roll measurement technology that enables the direct measurement of roll angle in any direction without relying on gravity.
Rapid fault diagnosis
After the machine tool has been verified and calibrated, Jinke's technicians use the Renishaw QC20 ballbar for rapid fault diagnosis, simulating actual operations to assess the overall accuracy of the machine tool. Before leaving the factory, they ensure that all machines are in optimal condition by correcting and compensating as necessary. Mr Shao explains: “The QC20 ballbar can detect multiple kinematic errors in a machine tool within 10 minutes. This helps us to quickly identify the reasons for substandard machining quality, making it easier to trace and resolve associated problems.”
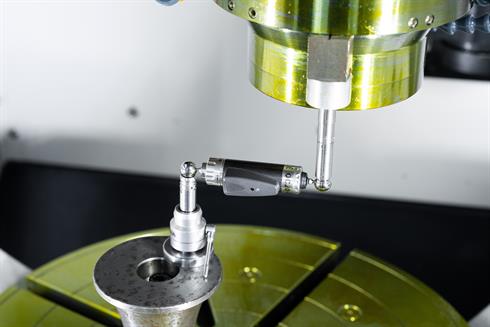
The Renishaw QC20 ballbar, in combination with Ballbar Trace software, allows for rapid verification of the accuracy of five-axis machine tools according to international standards, such as ISO 10791-6. This standard aims to verify the kinematic accuracy of four-axis and five-axis machines with three linear axes and one or two rotary axes. The tooltip tracking tests defined by this standard are performed using the QC20 ballbar. During multi-axis motion, the machine tool will attempt to maintain a fixed distance between the tip of the tool and a specific position on the workpiece. The ballbar measures any deviations between the tool tip and the workpiece and evaluates the contour machining performance based on this measurement result.