Prozessgesteuerte Hartdrehzelle amortisiert sich in 18 Tagen
Programmierbare Equator Prüfgeräte tragen zur Schaffung der bestmöglichen Automatisierungszelle für die Bearbeitung von Lagern bei.
Conroe, Texas, Vereinigte Staaten – Bei Conroe Machine ist das Realität, wovon die meisten Produktionsstätten nur träumen - Hartdrehen einer Reihe an Produkten, rund um die Uhr in einer unbemannten Zelle, die einen selbststeuernden Prozess ausführt. Im Prozess integriert ist ein FANUC Roboter mit dem Equator Prüfsystem, unter Verwendung der Renishaw EZ-IO Software, um einfache, umfangreiche Kommunikationsfunktionen für eine 100%-Teileprüfung sowie die Autokompensation einer Okuma 2SP-250 Drehmaschine mit Doppelspindel bieten zu können. Die fertigen Teile werden in der Zelle auch verpackt und palettiert. Nach Angaben des Unternehmens hat sich die Drehzelle in nur 18 Tagen amortisiert.
Conroe ist der Beweis dafür, dass es jeder Werkstatt, die bereit ist, das Talent junger Automationsexperten einzusetzen, möglich ist, neue Technologien wie das programmierbare Equator-System von Renishaw, mit einer von CNC-Programmierer James Wardell und Robotik-Techniker Jeff Buck entwickelten Software und Softwareprogrammierung, voll auszuschöpfen. Dasselbe Automationsteam hat sich anschließend der Schaffung einer unbemannten Teileprüf-/Sortierzelle für einen Kunden gewidmet. Diesesmal wurden zwei Equator, ein FANUC Roboter, ein optisches System und eine Förderanlage mit flacher Bauweise und mehreren Spuren kombiniert. In beiden Anwendungen zeigt Equator, wie wertvoll eine programmierbare Vergleichsprüfung ist, indem eine Reihe an Laufringen schnell geprüft wurde, und zwar kosteneffektiv und ohne Spannvorrichtungen oder Probleme aufgrund der Werkstattumgebung.
Conroe Machine ist ein relativ junges Unternehmen. Es wurde im Jahre 2000 von Murray ‘Tippy' Touchette gegründet, mit dem Ziel, Werkstücke mit der besten verfügbaren Fertigungstechnologie herzustellen. Das Unternehmen wuchs schnell auf ca. 150 Mitarbeiter, die in einer klimatisierten, 6000 qm großen Fertigungsstätte untergebracht sind, an. Obwohl es sich eigentlich um keine fachspezifische Werkstatt handelt, kommt, aufgrund der Lage von Conroe in der Umgebung von Houston, USA, ein hoher Prozentsatz der Aufträge aus der Öl- und Gasindustrie, hauptsächlich für Bohrarbeiten an Komponenten. Einer der kontinuierlichen Aufträge aus dieser Industrie ist die Herstellung von Axiallagerscheiben für Schrägloch-Sohlenmotoren. Diese Teile werden wöchentlich zu Tausenden, rund um die Uhr, hergestellt.
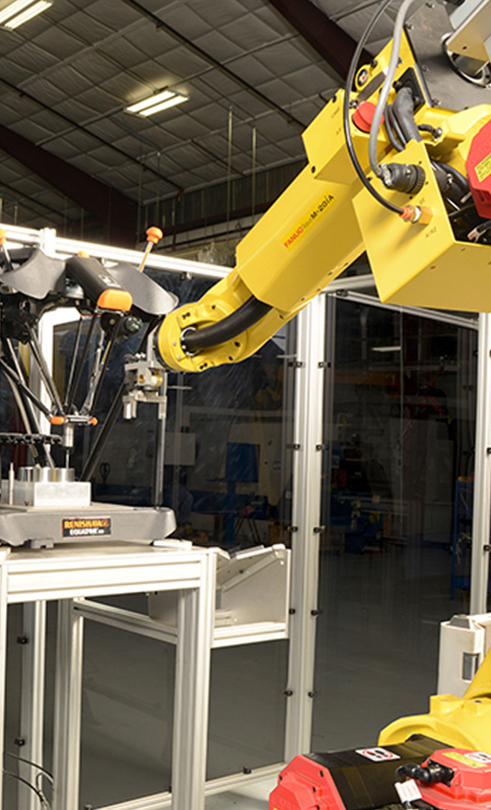
An der Automatisierungsleiter einen Schritt weiter
Die Lager werden derzeit auf vier Doosan Puma Drehmaschinen, die eigentlich Schrupp- und Schlichtarbeiten durchführten und von vier Bedienern betreut wurden, geschruppt. Diese Maschinen sind jetzt in zwei Zellen aufgeteilt, werden von FANUC Roboter be- und entladen und führen nur noch Schrupparbeiten durch - die Zellen sind ein Teil eines früheren Automatisierungsprojektes des Unternehmens. Die halbfertigen Teile werden dann zum Einsatzhärten (HRC 65 bis 1,7 mm) geschickt, bevor Sie fertig gedreht werden.
"Unsere Produktion hatte mit diesen beiden Zellen bei 800-1000 Teilen pro Tag, also 400-500 pro Zelle, ein Maximum erreicht", erklärt James Wardell. "Wir hatten einen Maschinenbediener, zur Beladung der Maschine und Prüfung der Teile. Bei einem solchen Volumen kann man allerdings von einem Bediener nur eine bestimmte Anzahl von Prüfungen erwarten, und wir mussten unsere Produktion steigern."
Weshalb Equator?
"Für unseren nächsten Schritt nach oben haben wir uns einen vollautomatischen Prozess für die Schlichtarbeit vorgestellt, mit einer automatischen Werkstückbeladung, Prüfung nach dem Prozess, automatischen Werkzeugkompensation, Markierung von Teilen und Verpackung/Palettierung der Werkstücke", fügt er noch hinzu. "Wir wussten ziemlich genau, welche Komponenten wir für ein derartiges System wollten, bis auf die Werkstück-Prüftechnologie, den CNC-Typ und der Software für die Werkzeugkompensation. Die Prüfung muss schnell sein, damit sie mit den Zykluszeiten der Werkstücke mithalten kann - und das kann nur 98 Sekunden betragen. Wir wollten ursprünglich mit Weißlichtlaser arbeiten, aufgrund der möglichen Geschwindigkeit, aber die Werkstücke sind zu reflektierend. Wir haben uns auch über zweckgebundene Prüfvorrichtungen und KMGs im Fertigungsbereich informiert. Zweckgebundene Prüfvorrichtungen sind sehr teuer und benötigen viel Aufmerksamkeit bei der Einrichtung und die KMG-Lösung brachte keinen Vorteil in Bezug auf die Geschwindigkeit. Da wir an einem anderen Projekt schon mit Renishaw arbeiteten, hat uns die Regionalleiterin, Sheila Schermerhorn, Equator als eine mögliche Lösung gezeigt."
Für unsere Bearbeitungszelle gab es kein anderes kosteneffektives Prüfwerkzeug für den Einsatz in der Produktion, das mit dem Equator vergleichbar ist.
Conroe Machine (USA)
Werkzeuge und Software zur Prozessüberwachung
Equator ist eine kostengünstige, flexible Alternative zu zweckgebundenen Prüflösungen. Es verwendet die Methode der vergleichenden Messung. Eine Masterkomponente mit bekannten Abmessungen, die auf einem KMG ermittelt wurden, wird verwendet, um Equator zu "Mastern". Alle anschließenden Prüfungen werden dann mit diesem Master verglichen. Die Wiederholgenauigkeit beträgt unmittelbar nach dem Mastering 0,002 mm. Um die Temperaturschwankungen in der Werkstattumgebung zu kompensieren, kann ein Re-Mastering von Equator jederzeit durchgeführt werden. Equator verwendet ein SP25 Messtaster zur taktilen und Scan-Datenerfassung, mit einer Geschwindigkeit von bis zu 1000 Punkte pro Sekunde. Die Tastereinsätze werden in einem integrierten Wechselmagazin mit sechs Speicherplätzen gehalten und das System wird über die MODUS™ Equator Software programmiert. Equator kann manuell mit einfacher Knopfbedienung verwendet werden, aber in diesem Fall eignet sich das System ideal für eine Integration in Conroes automatisierten Systemen, mit der EZ-IO Software für die Automatisierung.
"Wir waren Anfang 2012 beim Tag der offenen Tür bei Hartwig und haben dort den Equator im Einsatz gesehen, zusammen mit Okumas Drehmaschine mit Doppelspindel und Doppelportal", so Wardell. "Abgesehen davon, dass die Drehmaschine automationsbereit für unseren Komponententyp war, besitzt die auf Windows® basierte OSP Dual-Path Steuerung der Maschine eine PC-basierte Betriebsplattform in offener Architektur, was für unseren Plan, eine eigene Autokompensationssoftware zu entwickeln, wichtig war."
Equator in der Automatisierungszelle
Wardell und Buck haben schließlich eine Zelle, bestehend aus der Okuma 2SP-250H, einem Equator, einer Graviermaschine und einem FANUC M20iA 6-Achsen-Roboter installiert. Die zweiteiligen Karussells der Drehmaschine werden mit rohen Werkstücken, ungefähr 300 Stück, beladen. Die Doppelportal-Lader der Drehmaschine bestücken die Spindeln und legen die fertigen Teile in eine Rutsche, die zu einem Förderband führt, wo dann die Teile durch den Roboter entnommen werden. Das Bauteil wird anschließend vom Roboter zur Prüfung in den Equator gelegt, und sofern es i.O. ist, weiter zur Graviermaschine befördert. Zum Schluss verpackt / palettiert der Roboter die fertigen Teile.
"Wir haben unsere eigene Werkzeugkompensations-Software entwickelt, die mit der OSP-Steuerung betrieben wird", fügt Wardell hinzu. "Die Software arbeitet mit den Ergebnissen von Equator, übertragen in Form einer CSV-Datei, um eine Werkzeugkorrektur durchzuführen, wenn ein Bauteil von der Toleranz abweicht." Bei der Bearbeitung werden ungefähr 0,38 mm Material pro Seite abgetragen, die engste Toleranz liegt bei ±0,025 mm und die Oberflächengüte bei 0,5 µm. Die Bauteile haben einen Außendurchmesser von ca. 7,6 mm bis 15,2 mm. "Das Equator-System hat keine Probleme, Prüfungen innerhalb unseres Toleranzbereichs mit Spielraum, durchzuführen", erklärt Wardell.
Prozesssteuerung
"Unser Innen-/Außen-Ø bleibt exakt, mit einer Radiusabweichung von ca. 5 µm. Wir verarbeiten Bauteile schubweise, um Spannbacken- und andere Werkzeugwechsel minimal zu halten. Dank seiner Geschwindigkeit kann Equator mit dem Prozess Schritt halten. Da unsere Produktionsstätte auf 22,2 °C klimatisiert ist, führen wir nur einmal pro Tag ein Re-Mastering durch.
Prüfprinzipien und automatisierte Flexibilität
Die Prüfmethode für die Bauteile ist erstaunlich einfach. "Wir haben einen Aluminiumblock mit einer Bohrung in der Mitte gefertigt. Dieser Block wird in der Mitte der Equator-Spannplatte positioniert", erklärt Wardell. "Wir bestimmen damit unsere Mitte und stellen unser Koordinatensystem entsprechend ein. Jedes Bauteil wird dann in der Mitte dieses Blocks platziert. Zur Bestimmung der Bauteilmitte werden diese angefahren, alle anderen Merkmale werden gescannt. Wir haben das Prüfverfahren entsprechend geplant, um ohne Bauteilspannung und Tastereinsatzwechsel auszukommen. Der Roboter bestimmt, über die EZ-IO Automatisierungssoftware auf Equator, welches Prüfprogramm für das jeweilige Bauteil verwendet werden soll. Wir kennen die kritischen Merkmale, die geprüft werden müssen, damit sich das Teil innerhalb der Toleranz befindet."
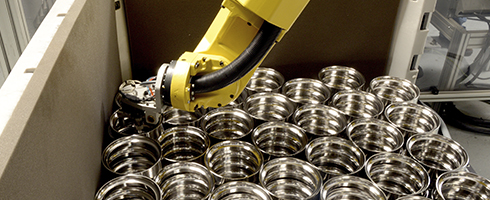
Prüfung/Sortierung gebrauchter Teile
Die Hartdrehzelle produziert zurzeit zwischen 600 und 700 fertige Teile pro Tag; d. h. jetzt reicht eine Zelle, und nicht mehr zwei wie bisher. Es hat außerdem zu einem weiteren Projekt geführt, das die Sortierung von Bauteilen für einen Kunden beinhaltet. Basierend auf einem Konzept von Touchette, entwickeln Wardell und Buck eine Prüf- und Sortierzelle für gebrauchte Axiallagerscheiben für Sohlenmotoren.
In Ölfeld-Reparaturwerkstätten werden gebrauchte Motoren zerlegt, instand gesetzt und wieder in Betrieb genommen. "Der Kunde hat bisher die gebrauchten Lagerscheiben visuell untersucht, um festzustellen, ob die Teile wieder verwendet werden können und wusste, dass einige gute Bauteile - und Geld - dabei weggeworfen wurden", so Wardell. "Wir wollten eine Plug & Play Prüf- und Sortieranlage anbieten, bei der die menschliche Einschätzung keine Rolle mehr spielt, damit eine größere Anzahl guter Lagerscheiben verwertet werden kann."
Buck und Wardell bauen eine Zelle, die, als dieser Artikel verfasst wurde, noch in der Entwicklung stand, mit zwei Equator-Geräten, einem FANUC LRMate 200iC 6-Achsen-Roboter, einer Förderanlage mit flacher Bauweise und mehreren Spuren, einem FANUC iR Vision System und einem schnellen ATI Werkzeugwechsler für die Endeffektoren des Roboters. Das Vision System teilt Equator die Teilenummer des Bauteils mit und welches Prüfprogramm ausgeführt werden soll. Die guten Teile werden daraufhin auf die entsprechende Förderspur gelegt, die schlechten auf einen Ausschussförderer.
"Wir haben das System so entworfen, dass es für die Lieferung als Einheit transportiert werden kann und für die Mitarbeiter in der Werkstatt einfach zu bedienen ist - anschalten und Teil auf die Förderanlage legen", erklärt Buck.
"Für unsere Bearbeitungszelle gab es kein anderes kosteneffektives Prüfwerkzeug für den Einsatz in der Produktion, das mit Equator vergleichbar ist", fügt Wardell hinzu. "Und wir hoffen, dass sich durch unseren ersten Schritt in die Zellenintegration für einen Kunden, neue Geschäftsmöglichkeiten für unser gesamtes Unternehmen erschließen.