製程前設定
使用測頭進行自動設定可比手動方式快達 9 倍。
Productive Process Pyramid™(金字塔生產製程解決方案)製程前設定層的控制元素在開始切削前便建立了工具機、工件與刀具之間的關係。這些自動化、預知型控制確保了首件成功率。
確保首件成功率
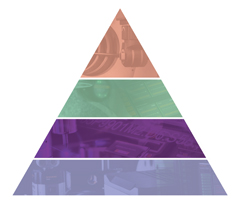
Productive Process Pyramid(金字塔生產製程解決方案)製程前設定層負責處理製程中的不確定因素來源,例如工件位置、刀具尺寸及機械偏置,並根據工件實際位置調整加工活動。
這些是應用於金屬切削即將開始前的預知型控制。
刀具設定可以建立
- 距離主軸量測線的長度,以確定高度補償並檢查長度是否在指定的公差範圍內
- 旋轉時的直徑,以確定刀具尺寸偏置
工件設定可以建立
- 組件識別以選擇正確 NC 程式
- 基準特徵位置,以建立工件坐標系 (WCS)
- 坯料/工件尺寸,以確定餘量狀態和粗切削順序
- 工件的方向(相對於工具機軸),以創建座標旋轉
工具機設定可以建立
- 組件定位與裝夾所需的旋轉軸、轉台或夾具組件的基準校準
- 轉台的旋轉中心位置和/或夾具元件上參考點位置
預知型控制
使用測頭進行自動設定,可比手動方式快達 9 倍,因此能夠節省出更多的時間用在金屬切削上。
測頭量測也可預知 — 您可以計算出檢測設定所需的時間,因此可以事先制定計劃。
通過機上測頭量測技術進行製程前設定時,完全由程式控制,因此不再需要專業技術人員執行多種量測、計算及輸入偏置修正等工作。
Renishaw 工件檢測測頭、刀具設定系統及 Productivity+™ 軟體是快速、自動、可重複設定金屬切削作業的重要工具。
文檔
-
產品型錄: 生產製程控制的量測解決方案
藉由專家級的製程控制技術的協助以改造您的製造量能
-
White paper: Survival of the fittest - the process control imperative [en]
In tough times, manufacturers focus on reducing their operating costs, but may not be able to afford to spend their way out by buying more productive machinery. With that pathway closed, what are the opportunities for radically reducing costs without replacing existing machines? This paper explores four areas where substantial savings can be found if firms are prepared to change the way they control their machining processes.