Bu sayfa şu anda sizin dilinizde mevcut değildir. Google'ın Çeviri sistemini kullanarak
otomatikleştirilmiş çeviriye
ulaşabilirsiniz. Bu hizmeti sağlamaktan sorumlu değiliz ve çeviri sonuçları tarafımızdan kontrol edilmemiştir.
Eğer daha fazla yardıma ihtiyaç duyarsanız lütfen
bizim ile temasa geçiniz.
Process foundation
Machine condition optimisation is an essential element of the process foundation.
The controls in the foundation layer of the Productive Process Pyramid™ maximise the stability of the environment and the performance of the machine on which the process will run. These preventative controls reduce the chances of special causes of variation having an impact on the machining process.
Optimise your machine's performance
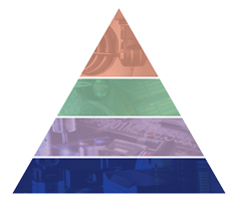
The base layer of the Productive Process Pyramid, as its name suggests, provides a firm foundation on which an automated, capable process can be built. It aims to design variation out of the process, providing a controlled, stable environment in which the machining process can operate effectively.
These are preventative controls applied in advance.
Machine condition optimisation
Machine condition optimisation is an essential element of the process foundation, as an inaccurate machine cannot make consistently accurate parts. A rigorous process of machine performance assessment, calibration and (where required) refurbishment can bring the machine's performance in line with the process requirements.
- Machine tool positioning errors are one of the most common causes of dimensional and surface finish rejects
- Positioning errors in the machine tool can be attributed to geometric, dynamic and play errors within the machine tool
- Errors can occur even in new installations due to changes between factory sign off and first use in the factory
- Wear in use and machine 'crashes' can also cause performance to degrade over time
- If machine performance is known and controlled, investigations into non-conformance can be focussed on the process and not the machine
Preventative controls
A machine that is 'fit for purpose' will deliver consistently good parts and will suffer fewer unplanned stoppages. This means more time available for metal cutting and also allows your maintenance staff to stop fire-fighting and become more proactive.
Regular checks of the condition of your machines with powerful diagnosis of the source of any errors, means that you can minimise reactive maintenance effort and focus on valuable preventative work.
Renishaw's XL-80 laser calibration, QC20 ballbar and AxiSet™ Check-Up systems are essential tools to gain a greater understanding of your machines' capabilities, to direct your maintenance efforts and keep control of the performance of your machines.
Other controls in the process foundation layer include:
Design for manufacture – an approach to product and process design based on a thorough understanding of current capability and a drive towards best practice rather than ‘reinvention of the wheel'. Key stages are:
- Rationalise machines, materials and tools
- Optimise cutting methods and parameters
- Characterise process performance
- Educate designers / customers about your actual manufacturing capabilities
Control of process inputs involves the use of process FMEA and similar techniques to understand and control all the upstream factors that can affect machining process outcomes. This can include ensuring consistent cutter geometry and tooling build standards, controlling clamping forces, locking down part programs and billet preparation.
Environmental stability addresses those external sources of non-conformance that cannot be eliminated in advance, but which are inherent to the operating environment. These include ambient temperature variation, whether the machine is warm or cold, machine and fixture cleanliness and tool life management. A key control here is a 'pre-flight checklist' to ensure that the machine tool is in an optimum condition before machining starts.
Process design can also have a big impact on process outcomes. A systematic approach to sequencing the manufacturing process gives the best opportunity for process stability and automation. This includes selecting machining strategies that allow tool offsets to be used to control the size and position of machined features, sequencing of rough and finish machining to avoid deflection and thermal distortion of finished surfaces, and integrating process feedback into the process at critical stages.
Documents
-
Broşür: Verimli proses kontrolü için metroloji çözümleri [tr]
Üretim performansınızı proses kontrol uzmanlarından alacağınız yardım ile arttırın
-
White paper: Survival of the fittest - the process control imperative
In tough times, manufacturers focus on reducing their operating costs, but may not be able to afford to spend their way out by buying more productive machinery. With that pathway closed, what are the opportunities for radically reducing costs without replacing existing machines? This paper explores four areas where substantial savings can be found if firms are prepared to change the way they control their machining processes.