Bu sayfa şu anda sizin dilinizde mevcut değildir. Google'ın Çeviri sistemini kullanarak
otomatikleştirilmiş çeviriye
ulaşabilirsiniz. Bu hizmeti sağlamaktan sorumlu değiliz ve çeviri sonuçları tarafımızdan kontrol edilmemiştir.
Eğer daha fazla yardıma ihtiyaç duyarsanız lütfen
bizim ile temasa geçiniz.
Post-process monitoring
Modern inspection technologies enable fully automated inspection.
The post-process monitoring layer of the Productive Process Pyramid™ focuses on the monitoring and reporting activities that provide information on the outcome and route of completed processes. These informative controls can be used to influence subsequent activities.
Traceable verification of conformance
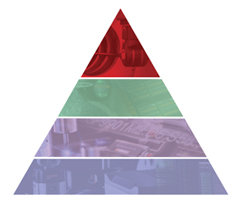
The post-process monitoring layer concerns checking the process and the finished part against their specifications, as well as logging process routes and outcomes.
These are informative controls applied after machining is complete.
Process logging records
- events that happen during the machining process such as manual or automated changes to process parameters, offsets or co-ordinate systems
- interventions to the process which may have influenced the outcome
On-machine verification enables
- inspection of critical features in the same environmental conditions as the metal-cutting process
- confidence in the stability of the machining process
Post-process reporting allows
- documented records of component conformance
- historical tracking of critical feature dimensions for machine condition monitoring and scheduled maintenance purposes
Informative controls
Modern inspection technologies enable fully automated inspection of even the most complex parts, often in a single set-up. This reduces the need for skilled inspectors to oversee quality assurance checks.
You can inspect parts 3 times faster on your CMMs using the latest 5-axis techniques. Versatile gauging systems provide rapid inspection and process feedback for medium- and high-volume parts.
On-machine verification can detect component non-conformance before the set-up is broken down, so any remedial work can be performed there and then.
Renishaw's REVO®, PH20 and the Equator™ system are essential tools for fast, traceable reporting of part conformance to specification and logging of the route and outcome of cutting operations.
Documents
-
Broşür: Verimli proses kontrolü için metroloji çözümleri [tr]
Üretim performansınızı proses kontrol uzmanlarından alacağınız yardım ile arttırın
-
White paper: Survival of the fittest - the process control imperative
In tough times, manufacturers focus on reducing their operating costs, but may not be able to afford to spend their way out by buying more productive machinery. With that pathway closed, what are the opportunities for radically reducing costs without replacing existing machines? This paper explores four areas where substantial savings can be found if firms are prepared to change the way they control their machining processes.