Renishaw уменьшает время механической обработки у производителя рабочих колес для авиакосмической промышленности
Honeywell Aerospace, часть группы компаний Honeywell, занимающаяся проектированием коммерческих и потребительских изделий, производством рабочих колес и моноколес для коммерческих воздушных судов.
Для изготовления пригодных для эксплуатации рабочих колес, которые фактически выполняют функцию радиальных и осевых компрессоров, очень важно выдержать требуемое положение базы заготовки на всех этапах процесса механообработки.
В противном случае, рабочее колесо будет признано негодным и отправлено на доработку, в ремонт или в отходы.
Чтобы обеспечить точность обработки Honeywell обратилась в глобальную проектную компанию Renishaw и заказала высокоточную станочную контактную измерительную систему RMP600 и пакет метрологического программного обеспечения на базе ПК Productivity+™ для обрабатывающих центров. Технология позволяет Honeywell выполнять измерения до обработки и выявлять любые осевые смещения на ранних стадиях технологического процесса.
Предыстория
Ассортимент производимых рабочих колес включает изделия диаметром от 14 до 17 дюймов. Почти все колеса изготавливаются из титана, и лишь одно — из алюминия.
Предприятие в Чиуауа поставляет свои изделия на сборочный завод Honeywell в Фениксе, Аризона. Там происходит сборка и испытание авиационных турбин.
Если база готовой детали сместится относительно центра, то рабочее колесо сдают на конструкторский анализ, в рамках которого конструктор изучает его и принимает решение о пригодности к эксплуатации.
Компания Honeywell распределяет это производственное время на двухнедельный период. Если будет выявлено смещение обработанной детали относительно центра, то потребуется еще неделя на анализ. Это приводит к простоям станка и прерываниям рабочего процесса, что сказывается как на сроках, так и на стоимости производства.
Задача
Причиной осевого смещения центральной точки отчета может стать неправильная установка детали из-за ошибки оператора, повреждения станочной оснастки и/или наличия заусенцев на заготовке, оставшихся от предыдущей операции.
Решение
Когда первый цикл процесса производства рабочих колес Honeywell подошел к концу, Луис Адриан Галлегос (Luis Adrian Gallegos), инженер-технолог Honeywell, обсудил со своим инженером по качеству продукции возможные меры по уменьшению погрешности положения заготовки во время обработки.
«После первого цикла необходимость улучшить технологию обработки стала очевидной, но нам хотелось сделать это без чрезмерно больших инвестиций, — рассказал Галлегос. — Мы встретились с представителями Renishaw и обсудили возможность применения высокоточных малогабаритных контактных датчиков и программного обеспечения Renishaw для измерения заготовок, что позволило бы нам выявлять и устранять все погрешности положения до обработки».
«Рассмотрев варианты, мы решили приобрести станочный датчик RMP600 с передачей данных по радиоканалу. Такое решение сочетало все преимущества автоматизированной подготовки к технологической операции с возможностью измерять геометрию сложных трехмерных деталей, таких как рабочие колеса», — добавил он.
В процессе обработки датчик Renishaw касается заготовки в различных точках и выявляет все погрешности положения.
«Контактный датчик помогает нам выявлять погрешности, не доводя до появления дефектов, — добавил Галлегос. Раньше мы могли выявить проблему только после того, как потратили 16 часов на механическую обработку и более часа на различные измерения. Теперь же мы заблаговременно получаем информацию о том, что с заготовкой что-то не так, и можем принимать меры, не теряя впустую драгоценное производительное время и ресурсы».
«Помимо контактных датчиков, компания Honeywell также остановила выбор на метрологическом программном обеспечении на базе ПК Productivity+ для обрабатывающих центров. Это удобная среда для программирования, которая позволяет включать в циклы механической обработки подпрограммы для измерения с помощью датчиков и алгоритмы оперативного принятия решений. Программное обеспечение упростило установку и проверку деталей, облегчило выполнение ключевых этапов обработки: подготовку техпроцесса и операции, идентификацию заготовки и инструмента. Более того, Productivity+ позволяет составлять отчеты после обработки, поскольку программа собирает информацию о выполненном техпроцессе и помогает принимать решения о последующих операциях и процессах», — дополнил Баррига.
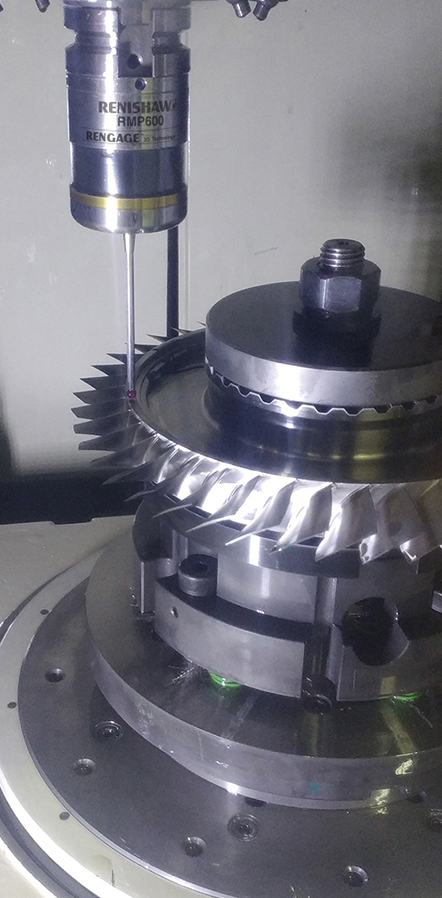
Благодаря датчикам и программному обеспечению Renishaw компания Honeywell может быть уверена в том, что процессе обработки не будет никаких неожиданностей. До внедрения новой технологии оператору станка приходилось устанавливать деталь, настраивать измерительный инструмент и контролировать диаметр и положение торцов. Если результаты отсутствовали или были неточными, или если станочная оснастка имела повреждения, то готовое изделие оказывалось бракованным. Теперь мы пресекаем дефекты на корню за счет своевременного обнаружения предпосылок их возникновения», — добавил он.
Honeywell Aerospace (Мексика)
Результаты
«Благодаря датчикам и программному обеспечению Renishaw компания Honeywell может быть уверена в том, что процессе обработки не будет никаких неожиданностей. До внедрения новой технологии оператору станка приходилось устанавливать деталь, настраивать измерительный инструмент и контролировать диаметр и положение торцов. Если результаты отсутствовали или были неточными, или если станочная оснастка имела повреждения, то готовое изделие оказывалось бракованным. Теперь мы пресекаем дефекты на корню за счет своевременного обнаружения предпосылок их возникновения», — добавил он.
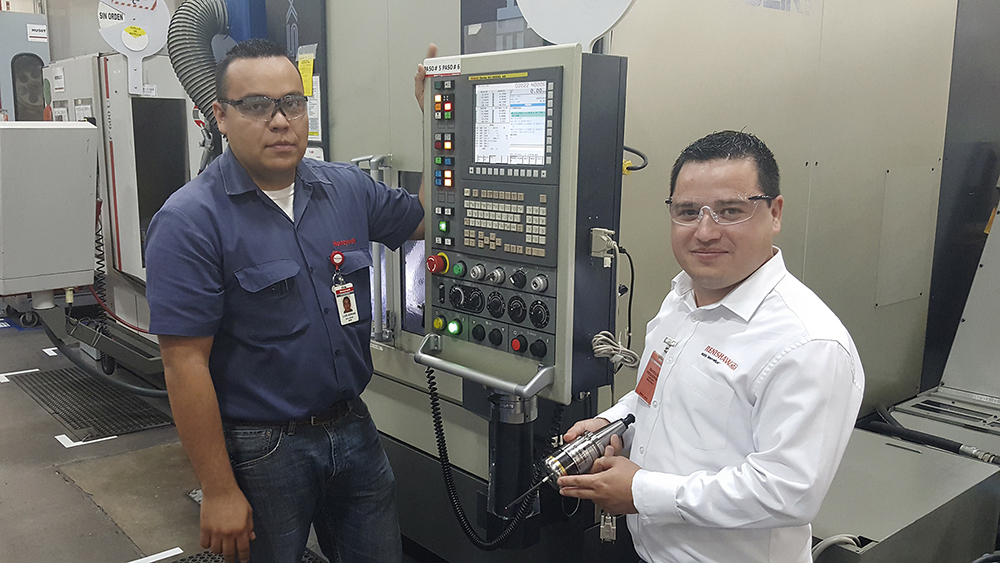
Взято из материалов Modern Machine Shop Mexico с разрешения редактора.
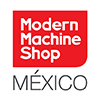