Контролируемый процессом модуль твёрдого точения окупает себя в течение 18 дней.
Программируемые измерительные системы Equator помогают создать непревзойдённый автоматизированный модуль для обработки подшипников и сортировки деталей.
Конро, Техас, США – компания Conroe Machine занимается тем, о чём в большинстве механических цехов только мечтают: круглосуточным точением семейства закалённых деталей в автоматическом модуле, в котором выполняется саморегулируемый технологический процесс. В производстве интегрирован робот FANUC и универсальная система цифровых шаблонов Equator, работающая с программным обеспечением EZ-IO компании Renishaw. Этим обеспечивается простое всестороннее взаимодействие для стопроцентного контроля деталей и автокомпенсации двухшпиндельного токарного станка Okuma 2SP-250. Модуль также упаковывает готовые изделия в коробки и укладывает их на поддоны. Компания утверждает, что токарный модуль удивительным образом окупил себя всего за 18 дней.
Conroe – доказательство того, что на каждом предприятии, готовом использовать таланты сегодняшних экспертов в области автоматизации, можно применить новую технологию, такую как программируемая система Equator компании Renishaw, с программным обеспечением и технологией программирования, разработанными технологом-программистом Джеймсом Уорделлом (James Wardell) и робототехником Джеффом Баком (Jeff Buck). Та же самая служба автоматизации создала для своего клиента автоматический модуль измерения и сортировки деталей, в котором в этот раз объединены две системы Equator, робот FANUC, видеосистема и ряд линий низкопрофильного конвейера. В обоих случаях система Equator демонстрирует ценность программируемого сравнительного контроля путём быстрого измерения семейства обойм подшипников, который выполняется с оптимальными затратами и без крепёжных приспособлений или проблем, возникающих из за влияния производственной среды.
Conroe Machine – относительно молодая копания, основанная Мюррэем "Типпи" Тушеттом (Murray ‘Tippy' Touchette) в 2000 г. Основной задачей компании было производство деталей с применением самой лучшей из существующих производственных технологий. Компания быстро выросла, и в ней работают 150 человек на заводе с управляемым микроклиматом площадью 65 000 квадратных футов (6000 квадратных метров). Несмотря на то что завод имеет общий профиль производства, благодаря местоположению компании Conroe рядом с Хьюстоном большая часть заказов поступает от нефтегазовой промышленности, в основном на компоненты бурового оборудования. Одним из постоянно повторяющихся заказов, поступающих в компанию из этой отрасли промышленности, является производство обойм упорных подшипников для забойных электродвигателей. Эти детали производятся тысячами еженедельно в круглосуточном режиме.
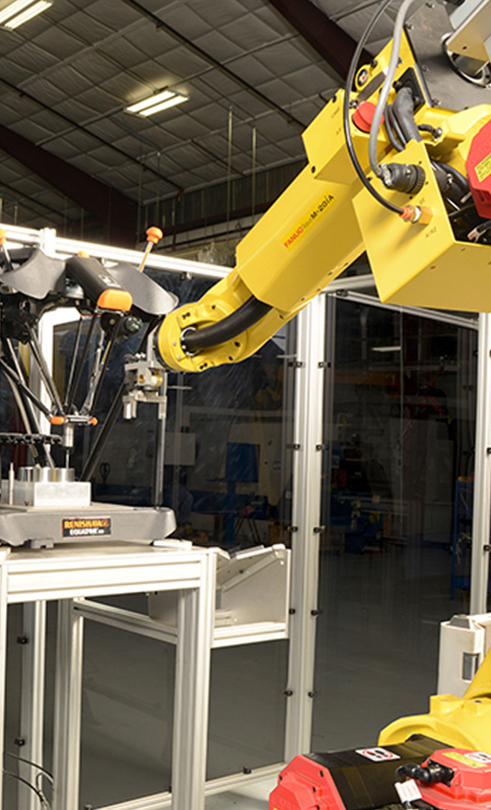
Подъём по лестнице автоматизации
Черновая обработка подшипников сейчас производится на четырёх токарных станках Doosan Puma, на которых раньше выполнялась и черновая, и чистовая обработка и которые обслуживались четырьмя операторами. Эти станки теперь разделены на два модуля, их загрузка и разгрузка выполняется роботами FANUC, и выполняют они только черновую обработку – эти модули были в числе самых первых проектов автоматизации цеха. Детали, прошедшие черновую обработку, отправляются на поверхностную закалку до HRC 65 на глубину 0,070 дюйма (1,7 мм), после чего выполняется их чистовая обработка.
«Наше производство застыло на 800-1000 деталях в день, изготавливаемых на этих двух модулях, то есть по 400-500 на модуль, – поясняет Джеймс Уорделл. – У нас был один оператор, который занимался загрузкой станков и контролем деталей. Однако на оператора можно положиться, что он правильно проконтролирует только такое количество дералей в таком объёме, а нам нужна была ещё большая производительность».
Почему Equator?
«На следующем этапе развития мы задумали создать полностью автоматизированный процесс чистовой обработки с автоматической загрузкой, измерениями после обработки, автоматической коррекцией инструмента, высечением маркировки на детали, упаковыванием деталей в коробки и укладыванием их на поддоны, – добавляет он. – У нас были довольно хорошие задумки по компонентам такой системы кроме технологии измерения деталей, типа ЧПУ и программного обеспечения для коррекции инструмента. Контроль должен осуществляться быстро, чтобы успевать вложиться во время цикла обработки деталей, который может составлять всего 98 секунд. Вначале мы рассматривали вариант проведения контроля белым лазером из-за его скорости, но у деталей слишком светоотражающие поверхности. Мы также рассматривали вариант измерений с помощью шаблонов и цеховых КИМ. Измерение с помощью шаблонов было очень дорогим и требовало время для наладки, а у КИМ не было скоростного преимущества. Работая с компанией Renishaw по другим проектам, региональный менеджер Шейла Шермерхорн (Sheila Schermerhorn), представила нам систему Equator как возможное решение».
Ни один другой экономически выгодный измерительный прибор для нашего технологического участка не сравнится с системой Equator.
Conroe Machine (США)
Инструменты и программное обеспечение для контроля процесса обработки
Система Equator – недорогая универсальная альтернатива специальным системам измерения. В ней используется сравнительный метод измерений. Эталонная деталь с известными размерами, замеренными на КИМ, используется для внесения эталонных параметров в систему Equator, с которыми затем сравниваются данные всех последующих измерений. Повторяемость непосредственно после внесения эталонных параметров в систему составляет 0,00007 дюйма (0,002 мм). Для компенсации изменений температуры в цеху в любое время можно выполнить повторную выверку эталонных параметров системы Equator. В системе Equator используется датчик SP25 для контактного сканирования и сбора данных со скоростью до 1000 точек в секунду. Щупы хранятся во встроенном шестигнёздном магазине для замены щупов, а программирование системы Equator осуществляется с помощью программного обеспечения MODUS™. Система Equator может использоваться в ручном режиме с кнопочным управлением, но в этом случае она идеально подходит для интеграции в автоматизированные системы компании Conroe с использованием программного обеспечения EZ-IO для автоматизации.
«В начале 2012 года мы побывали на дне открытых дверей в компании Hartwig и увидели систему Equator в действии вместе с двухшпиндельным двухрамным токарным станком Okuma, – говорит Уорделл. – Помимо того, что этот автоматизированный токарный станок подходит для деталей нашего типа, его двухканальная система управления OSP на базе Windows® имеет открытую архитектуру на основе ПК с рабочей платформой, что было важно в нашем плане для разработки нашего собственного программного обеспечения с автоматической компенсацией».
Система Equator в автоматизированном модуле
Уорделл и Бак установили модуль, состоящий из Okuma 2SP-250H, одной системы Equator, гравировального станка, и 6-координатного робота FANUC M20iA. На практике в сдвоенные карусельные магазины загружаются заготовки в количестве приблизительно 300 штук. Двухрамные загрузочные устройства станка подают заготовки в шпиндели и помещают готовые детали в жёлоб, ведущий к конвейеру, с которого их снимает робот. Робот помещает деталь на систему Equator для измерения и в случае её пригодности отправляет её на гравировальный станок, после чего готовые детали упаковываются в коробки и укладываются на поддоны.
«Мы разработали собственное программное обеспечение для коррекции на инструмент, работающее на системе управления OSP, – добавляет Уорделл. – В данном программном обеспечении используются результаты измерения от системы Equator, переданные в форме файла CSV для коррекции инструмента в случае отклонения детали от допуска». При механической обработке с каждой стороны детали снимается около 0,015 дюйма (0,38 мм), при этом самый самый строгий допуск составляет ±0,001 дюйма (0,025 мм), а шероховатость поверхности составляет 8 микродюймов (0,5 мкм). Наружный диаметр деталей составляет от трёх до шести дюймов. «Система Equator свободно может выполнять измерения в пределах наших допусков с высокой точностью», – говорит Уорделл.
Контроль процесса обработки
«Размер наружного и внутреннего диаметров у нас остаётся неизменно точный с колебаниями по радиусу примерно 5 мкм. Мы комплектуем партии деталей по размеру, поэтому смена кулачков зажимного патрона и другой оснастки сведена к минимуму. Скорость системы Equator позволяет легко идти в ногу со временем. Мы выполняем повторную выверку один раз в день, потому что в нашем цехе поддерживается температура 72 °F” (22,2 °C).
Принципы контроля и автоматизированная универсальность
Методика измерений деталей на удивление проста. «Мы изготавливаем алюминиевый блок с отверстием в центре, который помещается в центр установочной плиты системы Equator, – объясняет Уорделл. – Мы используем это для определения нашего центра и для установки нашей системы координат. Каждая деталь размещается в центре этого блока. Контактным методом мы определяем центр детали, затем сканируем поверхность по всем остальным параметрам. Мы планировали, чтобы процесс измерений осуществлялся без смены крепёжного приспособления детали или щупа. С помощью автоматизированного программного обеспечения EZ-IO системы Equator робот выбирает, какую программу измерений запустить для каждого типа деталей. Мы знаем все особо важные параметры, которые необходимо измерить для того, чтобы убедиться, что деталь выполнена в пределах допуска».
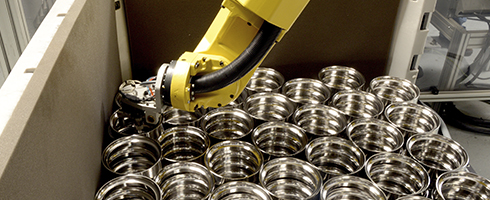
Измерение и сортировка использованных деталей
Модуль твёрдого точения теперь производит около 600-700 готовых изделий в день, поэтому теперь необходим только один модуль по сравнению с двумя, которые были необходимы ранее. Это привело к последующему проекту, включающему в себя модуль для сортировки деталей для клиента. На основании концепции, изложенной в общих чертах Тушеттом, Уорделл и Бак разрабатывают модуль измерения и сортировки для использованных обойм упорных подшипников забойных электродвигателей.
В нефтепромысловых сервисных мастерских использованные электродвигатели разбираются, ремонтируются и возвращаются в эксплуатацию. «Клиент выполнял визуальную проверку использованных обойм для определения возможности повторного использования деталей, и они знали, что выбрасывают часть хороших деталей – и деньги, – говорит Уорделл. – Мы хотели предоставить им систему измерения и сортировки типа "подключи-и-работай", в которой человеческая оценка была бы исключена из процесса, чтобы можно было восстановить большее количество хороших обойм».
Когда писалась эта статья, система всё ещё была в разработке, Бак и Уорделл собирают модуль, который состоит из двух систем Equator, 6-координатного робота FANUC LRMate 200iC, ряда линий низкопрофильного конвейера, видеосистемы FANUC iR Vision и устройства быстрй автоматической смены инструмента ATI для рабочих органов робота. Видеосистема сообщает системе Equator, какой номер изделия представлен и какую программу измерений необходимо запустить. После этого хорошие детали помещаются на соответствующий конвейер, а плохие детали помещаются на конвейер для отходов.
«Мы разработали эту систему для поставки в виде единого изделия, которое легко можно использовать в механическом цехе – необходимо просто включить питание и погрузить детали на конвейер», – говорит Бак.
«Ни один экономически выгодный цеховой измерительный прибор для нашего гибкого производственного модуля не сравнится с системой Equator, – добавляет Уорделл. «И мы надеемся, что выполненная нами интеграция модуля для клиента открывает в этой области новые производственные возможности для всей компании».