In-process control
Active process control enables parts to be made ‘right first time'.
The in-process layer of the Productive Process Pyramid™ features controls that are embedded within the metal cutting process. These active controls automatically respond to material conditions, inherent process variations and unplanned events to minimise process non-conformance.
Keep control as cutting proceeds
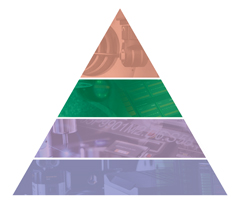
The in-process control layer of the Pyramid tackles sources of variation that are inherent to machining, such as tool wear and temperature variation, providing intelligent feedback to the process and decision-making as machining progresses.
These are active controls that are applied during metal cutting.
In-process gauging allows
- metal cutting to adapt to variations in the machining process such as part distortion, tool deflection and thermal effects
- updating of co-ordinate systems, parameters, offsets and logical program flow depending on actual material conditions
Broken tool detection recognises
- presence of a tool
- tool position - to ensure pull-out has not occurred
- broken and/or chipped tool edges
Active controls
Active process control enables parts to be made ‘right first time', so capacity needn't be set aside for rework and re-makes.
Automated in-process measurement means your machines will no longer be waiting for operators to re-start them.
In-cycle gauging gives your machine tools the intelligence they need to make decisions for themselves, enabling extended periods of ‘lights out' machining, boosting your productivity.
Renishaw's workpiece inspection probes, TRS2 tool recognition system and Productivity+™ software adapt metal cutting operations to the actual material and environmental conditions with automated feedback.
Documents
-
Brochure: Metrology solutions for productive process control
Transform your manufacturing performance with help from the process control experts