Enhancing the additive manufacturing process chain
The design freedom provided by additive manufacturing (AM) or ‘3D printing' technology is an important enabler in cutting-edge product innovation. As part of the revolution in digital manufacturing, AM can radically simplify the production of complex parts, while simultaneously improving functional performance, reducing part weight and minimising component counts.
To take full advantage of AM's unique capabilities, however, complementary software tools need to be optimised to satisfy the new requirements of ‘design for additive manufacturing' (DfAM) rules and guidelines. Dassault Systèmes, a world-leading provider of 3D design software, 3D Digital Mock Up and Product Lifecycle Management (PLM) solutions, collaborated with Renishaw to streamline its 3DEXPERIENCE® platform to deliver a no-compromise end-to-end AM design experience.
Background
The 3DEXPERIENCE platform comprises a whole suite of 3D software applications supporting the complete product life cycle, from design and development to simulation and reliability analysis. Available to users on premise or on-cloud, and accessible via a single user interface, it enables the creation of ‘social enterprises' where collaboration in the product innovation process becomes simpler and more efficient.
Topological optimisation is a key step process in the manufacture of 3D parts, ensuring material usage within a defined space is fully optimised. Dassault Systèmes' CATIA applications for generative design provide product modelling powered by the 3DEXPERIENCE platform.
Dassault Systèmes' companion DELMIA software application then enables users to design and test a product in a simulated production environment. Importantly, the software manages product build set-up and the generation of laser (scan) tool paths required by the AM systems. Simulation of the complete AM build process, including full product stress analysis and distortion prediction, is carried out using the 3DEXPERIENCE platform's simulation application.
In its close collaboration with Dassault Systèmes, Renishaw employed a broad range of its state of the art precision manufacturing and metrology products. These included the flagship RenAM 500M metal additive manufacturing systems with laser powder bed fusion technology, QuantAM build preparation software, machine tool probing systems, Equator™ gauging systems and CMM with REVO 5-axis measurement system.
Renishaw applied its technologies for characterisation of the build process, design validation and automated process control of a final subtractive machining operation. These, combined with the 3DEXPERIENCE platform's applications, delivered a seamless AM process and the end-to-end manufacturing solution required.
Challenge
The key challenge faced by Dassault Systèmes and Renishaw engineers was to achieve alignment of their respective virtual and real worlds - of 3D design, test and analysis software and metal 3D printing. Software needed to follow real AM build rules. The collaboration aimed to rationalise the AM design and manufacturing process so manufactures can move away from an expensive ‘design – build – test' approach to a ‘right-first-time' approach.
More specifically, the project ultimately aimed to remove any need for the export of native CAD source files in a universal .STL triangulated file format – an export long proven to introduce manufacturing errors and a prime cause of loss of quality control in successive product versioning.
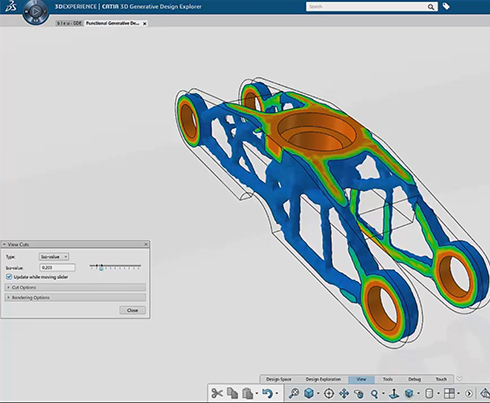
Solution
Using 3D design innovations in the automotive industry as a demonstration and test mechanism, this software enhancement project was based around the design and manufacture of a futuristic door hinge for Dassault Systèmes concept car, Bleu. A complex, lightweight, double-wishbone type component, the hinge presented Dassault Systèmes and Renishaw engineers with an authentic production scenario demanding close attention to structural optimisation, multi-material design and part consolidation.
Working within the 3DEXPERIENCE platform, a radical 3D hinge design was produced using the CATIA generative design capabilities. Associated tool paths generated by DELMIA applications were imported into QuantAM for additional processing prior to output to the RenAM 500M system.
Following an iterative, closed-loop sequence of hinge design adjustment, simulation, printing and precision inspection, the specific AM build rules that needed to be integrated within the 3DEXPERIENCE platform's software to achieve optimal 3D design and printing were determined.
Renishaw made an application programming interface (API) for its QuantAM software available to Dassault Systèmes for integration within the DELMIA application for the generation of right-first-time 3D printing tool paths.
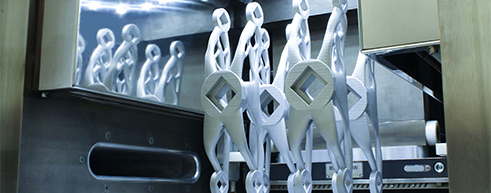
Results
As a direct result of the collaboration between Dassault Systèmes and Renishaw, 3DEXPERIENCE platform users can now print directly to the complete range of Renishaw AM systems from within the existing native CAD environment. There is no need to export data files to an external system for additional post-processing.
The enhanced CATIA, SIMULIA and DELMIA applications mean that innovative 3D product designs are now automatically optimised for both manufacture on Renishaw AM systems, and end functional performance. As a result, parts are produced more accurately from the outset, bringing lead time and material cost savings.
The focus of attention for the 3D design software developments and the ultimate by-product of the project, the conceptual hinge for the ‘Bleu' concept car, also provided further real-world evidence of the benefits to be achieved by 3D design and printing. The CATIA product design design is shown in the image in the "challange" section. The finished aluminium printed part is itself shown in the image shown in the "solution" section.
While in this case the original and optimised part volumes were virtually identical, all of the support structures were removed from the hinge design, creating a more elegant, more reliable and yet far simpler automotive product.
Subham Sett, Director of Additive Manufacturing and Materials, SIMULIA, Dassault Systèmes, commented, “Like Renishaw, Dassault Systèmes is committed to providing solutions which simplify the integration of 3D design and printing technology into all manner of production environments. This common thinking was instrumental in the project's success. Dassault Systèmes provides the functional generative design and physics-backed manufacturing simulations which are a key part of the metal 3D printing process chain.”