Zwiększenie dokładności pozycjonowania stołów obrotowych
Stoły obrotowe w obrabiarkach CNC odgrywają istotną rolę w wydajności wieloosiowych centrów obróbczych. Ponieważ dokładność i niezawodność stołu mają ogromne znaczenie przez cały okres użytkowania produktu, firma Matsumoto Machine Corporation (MMK) przyjęła pragmatyczne, dwuetapowe podejście do redukcji błędów indeksowania i poprawy wydajności. Doskonaląc zarówno technologię kalibracji produktu, jak i technologię enkoderów, firma ustanowiła nowe standardy dokładności stołów obrotowych.
Dodatkowe informacje
Założona w Japonii w 1948 r. firma Matsumoto Machine Corporation jest wiodącym dostawcą innowacyjnych, wysokiej jakości uchwytów szczękowych i sterowanych numerycznie stołów obrotowych stosowanych przez producentów obrabiarek przemysłowych na całym świecie. Kluczową cechą stołów obrotowych CNC firmy MMK jest opatentowany zespół przekładni ślimakowej i kołowej opracowany przez firmę OTT GmbH z Niemiec. W przeciwieństwie do przekładni ślimakowych z podwójnym prowadzeniem, przekładnia ślimakowa i kołowa OTT minimalizuje luzy, zapewniając wyjątkową dokładność i długą żywotność, wydajność i trwałość.
Zęby przekładni ślimakowej OTT są podzielone na część prawą i lewą (ślimak trzonowy i ślimak drążony) połączone pierścieniem rozstawczym, co pozwala zmaksymalizować powierzchnię styku z powierzchnią przekładni, a tym samym zmniejszyć niekorzystne efekty nacisku powierzchniowego. Ta unikatowa konstrukcja umożliwia regulację luzu przez zmniejszenie odległości między dwiema częściami. W takiej konstrukcji tylko jedna strona zęba ślimaka styka się z przekładnią kołową, pozostawiając luz po drugiej stronie. Dzięki temu dwuczęściowa konstrukcja przekładni dzielonej nie ulega zatarciu, nawet przy zerowym luzie.
Kolejną korzystną cechą stołu obrotowego CNC firmy MMK jest otwór przelotowy o dużej średnicy we wrzecionie stołu. Znacząco zwiększa to uniwersalność i sztywność maszyny, umożliwiając stosowanie większej liczby uchwytów i przyrządów oraz obróbkę dłuższych przedmiotów.
Dzięki temu, że większość operacji obróbki metalu może być wykonywana na jednej maszynie, zalety stołu obrotowego CNC firmy MMK są dalekosiężne. Należą do nich: oszczędność czasu i kosztów związanych z ustawianiem pojedynczej maszyny i ustawianiem pojedynczego mocowania, zmniejszenie liczby operacji związanych z przenoszeniem przedmiotów oraz eliminacja błędów tolerancji podczas przechodzenia przedmiotów obrabianych z maszyny do maszyny.
Kluczowe znaczenie w tym scenariuszu działania centrum obróbkowego, które ma produkować od razu prawidłowe przedmioty, ma zapewnienie wysokiej dokładności indeksowania i sterowania stołem obrotowym CNC przez cały okres jego eksploatacji.
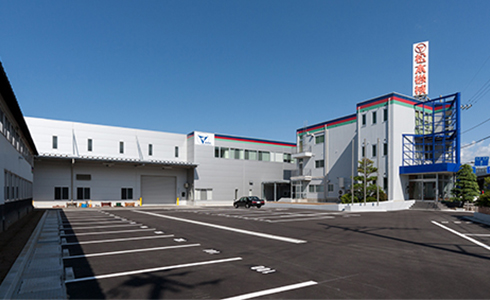
Wyzwanie
Podobnie jak w przypadku każdego rodzaju wyposażenia precyzyjnego, które jest wbudowane w centrum obróbkowe przez producenta obrabiarek, a które z kolei jest używane przez użytkownika końcowego w dowolnej liczbie gałęzi przemysłu, zapewnienie stałej dokładności i wydajności w czasie stanowi wyzwanie.
Podobnie jak w przypadku osi liniowych XYZ obrabiarki, oś obrotowa jest tak samo podatna na niekontrolowane zdarzenia, które mogą być przyczyną błędów pozycjonowania kątowego lub niewspółosiowości. Błędy te mogą wynikać z wielu przyczyn, w tym z błędów popełnionych podczas wstępnej instalacji maszyny, uszkodzeń powstałych w wyniku kolizji lub ogólnego zużycia w trakcie eksploatacji.
Firma MMK, ciesząca się światową renomą ze względu na jakość produktów i innowacyjność konstrukcji, postanowiła wyposażyć swoje stoły obrotowe CNC w wysoce precyzyjny i niezawodny system śledzenia i sterowania indeksowaniem produktu przez cały okres jego eksploatacji, niezależnie od typu obrabiarki, złożoności przedmiotu obrabianego i cyklu pracy.
Jednocześnie, na coraz bardziej konkurencyjnym rynku stołów obrotowych CNC, firma MMK chciała jeszcze bardziej usprawnić procesy kontroli jakości swoich produktów. W szczególności zaś firma postawiła sobie za zadanie rozszerzenie zakresu pomiaru kąta indeksowania jako kluczowego elementu procedur zapewnienia jakości przed wysyłką.
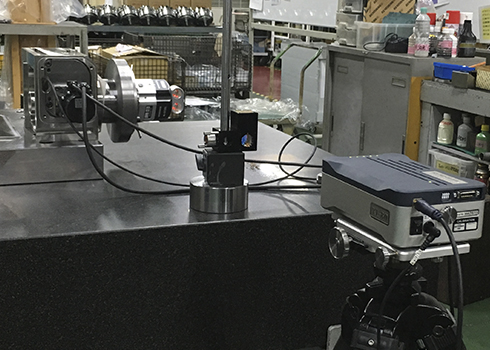
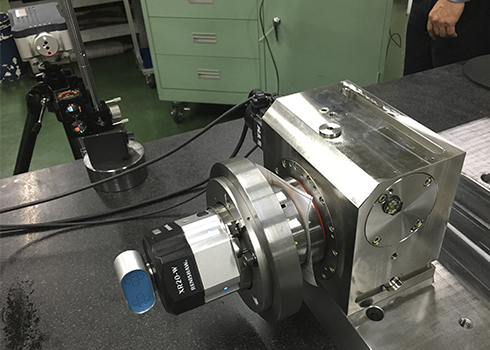
Rozwiązanie
Aby zapewnić producentom i użytkownikom obrabiarek możliwość dokładnego śledzenia i sterowania indeksowaniem stołu obrotowego CNC, firma MMK zdecydowała się na integrację systemu TONiC™ — bezdotykowego, optycznego enkodera inkrementalnego. Enkoder TONiC jest prosty w instalacji i ma miniaturową głowicę o wymiarach zaledwie 35 mm x 13,5 mm x 10 mm. Jest idealnym rozwiązaniem dla firmy MMK, z minimalną powierzchnią montażową i obsługując prędkości maszyny do 10 m/s i rozdzielczości do 1 nm.
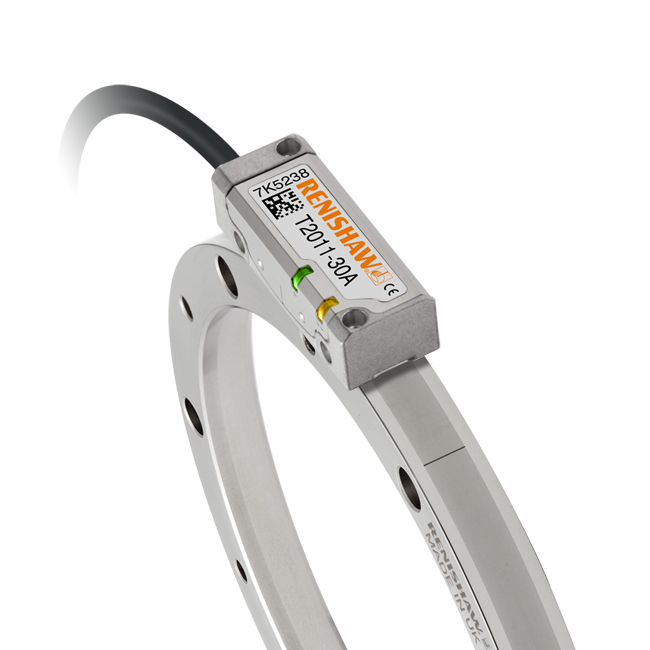
Głowica stołu obrotowego została zaprojektowana do stosowania w połączeniu z liniałem RESM firmy Renishaw' Jest to jednoczęściowy pierścień ze stali nierdzewnej z naniesioną na jego obwodzie skalą o podziałce 20 µm. Wyposażono go w optyczny znacznik odniesienia IN-TRAC™. Liniał RESM ma małą wysokość, dużą średnicę wewnętrzną i jest dostępny w zakresie średnic od 52 mm do 550 mm. Charakteryzuje się też wysoką stabilnością. Uzyskuje się w ten sposób uniwersalny i łatwy do zintegrowania liniał, który nadaje się do szerokiego asortymentu stołów obrotowych CNC firmy MMK.
W celu zwiększenia niezawodności i odporności na degradację liniału spowodowaną upływem czasu, głowica TONiC ma wbudowany filtrujący układ optyczny trzeciej generacji charakteryzujący się niskim poziomem szumów (rozstrojenia). Jest dodatkowo wspomagana układem dynamicznego przetwarzania sygnału. Pozwala to na uzyskanie bardzo małego błędu cyklicznego (SDE): typowo ±30 nm. Enkoder TONiC jest zgodny ze standardowymi sterownikami przemysłowymi. Wyposażono go w odłączany interfejs analogowy lub cyfrowy w wytrzymałym złączu typu D, które może być umieszczone w odległości do 10 m od głowicy.
Firma MMK wybrała miniaturowy i lekki kalibrator osi obrotowych XR20-W firmy Renishaw do sprawdzania dokładności swoich stołów obrotowych podczas produkcji oraz bezpośrednio przed' System XR20-W był używany w połączeniu z interferometrem laserowym XL-80 firmy Renishaw w celu zapewnienia bezdotykowego pomiaru odniesienia' od testowanej osi, z dokładnością ±1 sekundy łukowej.
Dzięki temu, że system XR20-W jest napędzany serwonapędem, a rejestrowanie danych jest zsynchronizowane z ruchem osi, nie wymaga interwencji operatora podczas pomiarów. Dzięki zasilaniu baterią litową i łączności Bluetooth umożliwia szybką i łatwą konfigurację. Pozwala również uniknąć ryzyka związanego ze splątanymi kablami. Modułowa konstrukcja kalibratora i elastyczne systemy mocowań umożliwiają znacznie łatwiejszą konfigurację niż rozwiązania alternatywne. System można łatwo skonfigurować do pracy z wieloma różnymi stołami obrotowymi, uchwytami i wrzecionami.
Wyniki
Integrując system bezdotykowego enkodera optycznego TONiC firmy Renishaw ze swoimi stołami obrotowymi CNC, firma MMK uzyskała jeszcze wyższą dokładność i niezawodność swoich produktów w warunkach roboczych oraz wyjątkową skuteczność sterowania ruchem. W przypadku wielu różnych obrabiarek i zastosowań końcowych, połączenie miniaturowej głowicy i jednoczęściowego liniału pierścieniowego ze stali nierdzewnej zapewnia wyższy poziom tolerancji na kurz, zarysowania, smary i oleje oraz redukcję błędów indeksowania. Zdolność enkodera do generowania bardzo stabilnych sygnałów położenia o niezrównanej czystości oraz bardzo niski błąd cykliczny (SDE) zapewniły płynniejszą regulację prędkości, lepszą wydajność skanowania i zwiększoną stabilność pozycjonowania.
Wprowadzenie przez firmę MMK kalibratora osi obrotowych XR20-W firmy Renishaw oraz interferometru laserowego XL-80 skróciło czas pomiaru produktu o połowę w porównaniu z konwencjonalnymi technikami autokolimatora. Procedury pomiarowe zostały uproszczone i zautomatyzowane. Kalibrator, zdolny do wykonywania dokładnych pomiarów przy dowolnej podziałce kątowej indeksowania, umożliwia ocenę dokładności stołu napędzanego przekładnią ślimakową i kołową w wypadku bardzo precyzyjnych ruchów pomiarowych o skoku równym 0,001°. Umożliwiło to szczegółową ocenę i rozwiązanie problemów związanych z utratą kontroli nad ruchem oraz sprawności przekładni ślimakowych i kołowych. Działanie produktu jest teraz poparte dokładną analizą spełniającą normy jakości ISO.