Small wonder impresses Red Bull F1
Good things come in small packages or, in the case of JK Engineering, small spaces. However, what the precision engineering subcontractor lacks in floor space, it more than makes up for in business savvy, which is why its workshop is stuffed to bursting with the very latest manufacturing technology, including DMG CNC machine tools equipped with a variety of Renishaw touch probes and tool setters.
JK Engineering, located in Hertfordshire, north of London, is owned and managed by John Kenny, an apprenticed CNC machine operator with a background in aerospace and F1 engineering. The seeds for JK were planted during Kenny's stint at Red Bull F1, in its earlier incarnation as Stewart Grand Prix. Thanks to an unplanned change in his personal circumstances Kenny took the plunge and invested a property windfall in starting his own venture. “In time honoured tradition, I woke up one day and decided it was now or never,” he remembers. “I handed in my notice at Stewart, bought several second hand machines and went looking for business.”
With his feet planted firmly on the shop floor, Kenny realised that he wouldn't be doing a great deal of his work for his former employer. Not at first, that is.
“I didn't have the equipment to work for the likes of an F1 team. The technology you need to do a good job - 3D CAD/CAM software, 4 and 5 axis machines, etc. - is incredibly expensive. There's so little help for start-up firms that I had to find other, less complex work, just to pay the bills.”
JK's bread-and-butter came in the shape of dental and medical components for the likes of the Royal National Orthopaedic Hospital; income that still constitutes a healthy percentage of the company's current turnover and helps to even out the wild swings inherent with F1 revenue.
The move into multi-axis
“We did a lot of simple, three axis work that paid the bills and enabled us to slowly replace the older machines with multi-axis equipment. Once we had this, I went back to Red Bull and offered our services.”
According to Kenny, many precision engineering machine shops find it difficult to cope with the unique demands of an F1 client such as Red Bull F1.
“Much of the work we undertake is very small batch or one-off parts and components; the kind of thing that puts off a lot of companies. We've been successful for two main reasons: Firstly, we do whatever we must to get the job done on time and to the right quality standards. Secondly, just as importantly, we use the latest Renishaw tool setting technology to minimise set-up times and to get the maximum productivity from our machines. This is vital if you want to make a profit on such low-volume work. ”
In the case of the company's two, 5-axis Deckel Maho DMU 50 CNC machining centres, JK uses Renishaw OMP40 spindle touch probes and fixed Renishaw NC4 non-contact laser tool setters; the latter was quickly and easily fitted to the DMG machine by a member of Renishaw's UK engineering team.
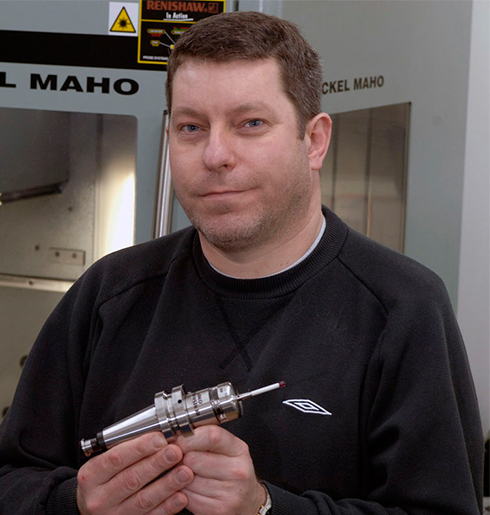
Coping with multiple tool changes
“Jobs are often loaded on the DMU's on small pallets and frequently require multiple tool changes, sometimes as many as 30!” explains Kenny. “We use the Renishaw OMP40s to quickly establish the part datum, then we use the NC4 to automatically set the tools and to monitor for tool breakage during the program.
The consequences of a machine left running unmanned with a broken tool would be nothing short of disastrous.
Material is ridiculously expensive, and getting more so all the time. We're using a lot of Titanium and aerospace grade alloys so we don't want scrap and, given the very small quantities and tight deadlines, we can't afford to be running a job twice.”
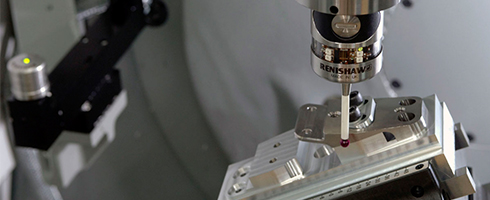
Upgrading every piece of machinery
In the seven years since Kenny started JK Engineering, he's replaced almost every piece of machinery and software with the latest equipment. As well as the two state-of-the-art DMU machining centres, there's a new Haas VF-2 Super speed VMC with 4th axis and two CNC Colchester turning centres with driven tooling. To generate the CNC programs there's a 3D Open Mind Hyper Mill CAM system and, to stay on top of finished part quality, a clean room inspection area. Everything JK needs to keep its very demanding F1 client happy.
“Having the equipment is only part of the story,” says Kenny. “Using it effectively and efficiently is vital.”
JK aims to keep everything running as much as possible. The Renishaw equipment allows the company to minimise unproductive set-up time, avoid costly errors and deliver a good quality product on time, every time.
“In the future, we plan to buy machines with even more tools, so set up and monitoring becomes increasingly important. It's not rocket science,” he says. “On the contrary, the Renishaw equipment is very easy to use. I know other companies that have invested in a similar combination of machine and probe technology to do similar work and they're successful, too.”