Scania:工作機械のメンテナンス作業は投資です、コストではありません!
工場保全管理業務の請負企業、Dynamate AB 社 は、世界のトップ(大型)トラックメーカー、Scania 社の工場において自動者業界ではトップレベルの、最も包括的かつ高度に体系化されたメンテナンス戦略を実施しました。
ストックホルム近郊に所在するスキャニア・セーデルテリエ工場において、ダイナメイト社が導入した、画期的なメンテ業務の改革はその効果を如実に実証。機械の精度が著しく向上し、高精度パーツを生産する機械の能力が格段に増強されました。達成の要となったのは、標準機械検査・テストの中で定期的に機械性能の経時変化をモニターすることが重要であると、認識されたからです。
部品はできる限り内製するという方針の下、セーデルテリエ(エンジン)工場で生産された部品はスウェーデン、オランダ、フランス、ブラジル、アルゼンチンに所在の組立工場に供給されます。
ダイナメイト社の生産サービスマネージャー、カール・オルトン氏は、新規購入した工作機械について大変忌憚のないコメントを述べます:「工作機メーカーさんにとって我々は本当にイヤな存在です。当社の一連のテスト・検査で確認したところ、最近新規購入した 工作機械 34 台中、わずか 3 台しか ISO 標準をクリアできませんでした。スキャニア社からは現在、納品前の工作機械が正確に調整されるようにと、工作機メーカーに出向いて当社の機械テスト・検査を出荷前に実施する業務が委託されています。結果的には工作機メーカーさん側もサービス要員の派遣回数が減ることで利益があがりこの利益をメーカーさんの製品や技術改革にあてられるようになるのですが・・・。」
定期的に 20 分間のテストを実施
セーデルテリエ工場に設置の 500 台にのぼる CNC 工作機械のどれもが、最低でも年に一度、多くの場合もっと頻繁に数種の検査やテストにかけられ、所要時間はトータルで機械 1 台につき 1 時間かかります。この所要時間の中の約 20 分は、レニショー QC10 ボールバーを使用した機械の位置決め精度の性能テストに費やされます。このテスト結果から、機械のソフトウェア設定の調整などのテスト後即座に実行できる改善や、部品交換などのより基本的なメンテナンス作業をいつ実施すべきかが提示されます。
ボールバーテストの結果はすべて履歴グラフに記録/保存されるため、機械性能の経時変化の記録が残るようになります。これらのデータから、スクラップが発生するまでに機械の性能が悪化してからの後手後手な対応ではなく、メンテナンス作業がいつ必要か、実施時期を予測できるようになります。
ボールバーテストというのは、半径が特定された円を機械がトレースする CNC プログラムを、工作機械上で実行してテストします。ボールバーを構成する特殊な磁気ボールと磁気カップマウント部により、機械の主軸とベット/テーブルの間は連結されています。機械が円のトレースプログラムを実行していくに従い、QC10 ボールバーソフトウェアは「完璧」な円からのズレ量を記録していき、円の半径がモニターされます。
工作機械がどれだけ正確に円の経路どおりに移動できているかは、工作機械の位置決め性能の指標となります。さらに、QC10 ボールバーソフトウェアには 21 種の誤差要因を特定する機能があり、誤差全体の中で特定された要因が各々実際にどれだけ関与しているかを計算することができます。
このボールバー 20 分間テストのテスト方法は、どの持ち場のどのエンジニアも全く同様に行い、マシニングセンターにも旋盤にも良好に活用できます。ダイナメイト社は現在、研削盤と歯切り盤用にも同様のテストを開発しようとしています。
機械の性能を即座に改善
ダイナメイト社のメンテナンスエンジニア、シェル・ノーシュテット氏は、生産工程上の問題が多くの場合工作機械に起因することを証明してみせることができます。普通、生産現場ではそうは思わず、信じたがりません。ノーシュテット氏が行う最初のテストではしばしば、それまで分かっていなかったエラーが示されますので、テストの後、めざましい改善を実行することができます。ノーシュテット氏は典型的な事例を説明します:
「トランスミッションの部品を生産する 1 台の工作機械ではここ 2・3 年、部品寸法を許容範囲内に収めるために、2・3 時間ごとに手動で機械のプログラムを調整していました。私がボールバーテストを走らせ、ものの数分で 948 ミクロンの真円度誤差を検出しました。ボールバーの解析ソフトウェアに表示の数値を使って、バックラッシュ補正量を即座に変更することができます。その結果、真円度誤差は 400 ミクロン以下に改善されました。一旦モータを交換してしまえば、この誤差もほとんど消滅し、二度とプログラムの数値を調整する必要がなくなるでしょう。」
ノーシュテット氏は続けます:「この工場では従来から、品質確認のための測定は生産終了後に行われていましたが、生産開始の前に機械の性能を解析するための計測はほとんどやっていません。やっと、我々の言うことがわかってもらえたのです...。ここまでくるのに 20 年かかりました。」
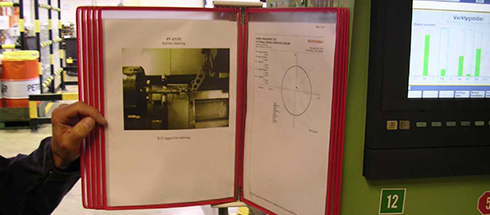
工作機械の状態を個々に把握
ダイナメイト社は、下の 5 つの基準に従って、すべての工作機械を A、B、C のカテゴリーにグループ分けすることを、スキャニア社の生産計画担当者に依頼しました。
- 安全性(保健と労働安全上の懸念点)
- 高リスクの重要形状加工
- 量産/切削時間
- 冗長性
- 将来の用途
分別されたカテゴリーごとに、ダイナメイト社は作業頻度と作業内容を明記するメンテナンス計画を作成して、どの機械が寿命ぎりぎりで問題を起こしやすい等の情報をスキャニア社に提示しました。どの機械が生産効率や生産工程のボトルネックで重要となるかの理解に、QC10 ボールバーは極めて重要な役割を果たします。
良品パーツの生産を何年継続できるか、修理の必要な機械、時には入れ替えが必要な機械などについてスキャニア社に報告するため、機械を 1 台 1 台、構造や動力系など様々な方面から分析しました。スクラップ発生という「症状」に対処するのではなく、問題の根本原因に対して対策を講じるため、既存の工作機械の多くは現在、高い精度を維持しながら耐久年数を伸ばして、生産活動ができるようになっています。
ダイナメイト社は成長し続けます
ダイナメイト社は、スキャニア社が全額出資の子会社ですが、独立企業として経営管理されています。総売上げ高は、1997 年度の €3000 万ユーロから 2004 年度の 1 億 3000 万ユーロに成長、従業員は 720 名です。「保全管理業務への頼もしい味方」という企業イメージを掲げスキャニアグループ以外の企業からもビジネスを獲得しています。特にその一つ、鉄鋼会社との 5 ヵ年契約は大きなビジネスです。オートン氏が述べるように、「最大の難関は、工作機械の性能をモニターすることが、生産活動への投資であって余分なコストではない、と説得することなのです。」
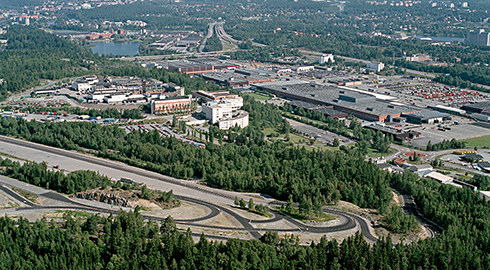