Al momento, questa pagina non è disponibile nella lingua scelta. È possibile visualizzare una traduzione automatica realizzata con Google Translate. Renishaw declina qualsiasi responsabilità relativa alla fornitura di tale servizio e specifica di non avere controllato la traduzione.
È possibile contattarci per richiedere ulteriore assistenza.
RLE20 interferometer enhances performance of Vistec Lithography’s latest e-beam tool
Raith's VB300 e-beam lithography tool is a development of the highly successful VB6 series introduced in 1993. In designing the new tool, Raith identified that a reduction of noise-induced positional errors would significantly improve tool performance. Through a combination of improved mechanical rigidity and integration of the Renishaw RLE20 differential interferometer based encoder system, these errors are now expected to be <3 nm.
Leica Microsystems Lithography Ltd (based in Cambridge, UK) introduced their first vector-beam lithography tool in 1993. Since its introduction the various versions of the machine have been employed in a diverse range of applications including nanotechnology, micromechanics, micro optics, NGL maskmaking, si-direct write and telecommunications.
The VB300 tool provides the ability to load and expose piece parts as small as 5 mm through to full 300 mm wafers with corresponding mask plate substrate sizes.
The tool provides rapid exposure with 50 MHz pattern generator and 20-bits resolution, has axis lengths of 330 mm x 330 mm, maximum stage velocity of 50 mm/sec, the capability of generating less than 10 nm lithography and an overall 3 sigma accuracy of 10 nm.
To achieve the stated specification the VB300 tool includes performance improvements in a number of key areas:
- height stability between the column and the sample,
- column electronics,
- and yaw and roll performance of the complete system.
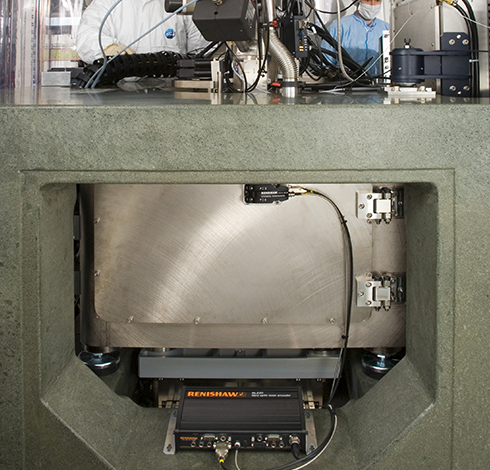
Improving noise induced errors
In addition to these improvements Raith wanted to improve noise induced errors and in particular to remove a peak mode at ~175 Hz that was attributed to the interferometer configuration and mounting arrangement. To tackle this issue Raith decided to change the interferometer configuration from a standard double pass interferometer to a differential interferometer enabling the differential position between the e-beam column final lens and the stage metrology / work piece location plate to be directly measured.
Having worked successfully with Renishaw on a previous project involving RGH optical encoders, Raith selected the RLE20 fibre optic launched laser interferometer based encoder system for integration within the VB300 tool.
John Tingay, R&D Manager states “We were impressed with the Renishaw RGH optical encoder product and aware of the RLE10 laser interferometer system, although the latter wasn't ideally suited to vacuum applications, which was necessary if it were to be incorporated into any of the current tools for both mechanical and thermal stability reasons.
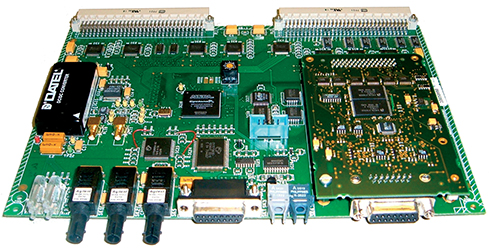
Overcoming vacuum issues
“Discussions provided us with information about a differential interferometer development program at Renishaw that would provide the same advantages as the RLE10, but would overcome the disadvantages outlined earlier by being mounted in atmosphere on the vacuum chamber wall. The differential interferometer configuration means that any mechanical perturbations of the mounting system are seen by both the reference and metrology beams i.e. common mode error and the system is self compensating. The only issue then is the stability of the reference mirror, which has been designed to have high intrinsic stiffness and correspondingly high modes of vibration. This design strategy has helped to eliminate the noise-induced errors seen on previous systems.
“We did review interferometers from other vendors, but chose the Renishaw system because of the significant reductions in installation complexity and set up time provided through the fibre optic laser launch, intrinsic optical alignment system and the ability to mount the interferometer outside the chamber without degrading system performance. Luckily for us we were made aware of the development program at a time that enabled us to influence final design, ensuring its compatibility with our requirements.”
The VB300 tool uses Renishaw RLE20 systems that include three differential interferometers; two to measure position (between the e-beam column and the wafer stage) on the X and Y-axes and the third to measure yaw. Tingay says: “With the improvements in stage accuracy achieved through redesign, material selection and machining techniques, we don't believe there is a real need to measure yaw; the capability is designed-in for monitoring purposes only at present with the possibility of yaw correction in the future if needed.”
Picometre resolution
The RLE laser interferometer system produces 1 Vpp sine and cosine signals with each 360° period representing 158 nm. To provide the high resolution required by the VB300 tool, these signals are interpolated by Renishaw's RPI20 parallel interface to provide a least significant bit (LSB) resolution of 77.2 picometres.
As well as the advantages offered by the RLE system and its fibre optic laser launch, Raith required a VME form factor and interface. The RPI20 allows, via a simple connector, integration of custom electronics that provide hardware and software interfaces, which effectively ‘clone' Raith's existing systems, enabling position data to be collected and utilised for beam error feedback and position control.
Improvement in error contribution
In comparison to previous systems the initial results from the VB300 show a marked improvement in the noise related error contribution. To clarify the improvement since the introduction of the RLE20, Raith have undertaken “beam on edge” measurements where the electron beam is parked on the edge of a metal mark and the variation in the intensity of the back-scattered electrons is measured. This technique is used as it provides a measurement of the total noise in the system; mechanical and electrical, both on the beam and on the video system monitoring the back scattered electrons.
Comparing the VB300 spectra to that taken from the VB6 tool it can be seen that the VB300 shows no evidence of the peak at 175 Hz, the identified feature that Raith wanted to remove. Additionally the peak at 240 Hz had been removed and the 150 Hz feature reduced.
Tingay states: “Noise measurements from the VB300 are very good, no mechanical vibrations can be seen, I expect the total noise to be about 2 nm – 3 nm with no observed contribution from the reference mirror or interferometry system.”