Por el momento, esta página no está disponible en español. Puede obtener una traducción automática mediante la opción de traducción de Google.
No podemos responsabilizarnos de este servicio puesto que podemos no verificar los resultados de la traducción.
Si desea más información, póngase en contacto con nosotros.
Jingdiao's refusal to compromise on quality sees its business take off
Beijing Jingdiao Company Ltd has collaborated with Renishaw as its business has continued to grow over the years, with the two companies working together to open up new pathways to innovation and deliver superior quality.
Based in China, Beijing Jingdiao Company Ltd (Jingdiao) specialises in the R&D and manufacture of high speed small cutting tool machines. They currently operate several dozen Renishaw laser interferometers, ballbars and rotary axis calibrators, which are used in the development of new products and refinement of manufacturing processes. Jingdiao's CEO Huang Shan explains, “We chose Renishaw products when our company was first founded because we admired their brand values and product performance. We compared precision calibration equipment, including laser interferometers and ballbars from a number of brands on the market, and found that of all the comparable products, Renishaw offered the most consistent performance and the most widely recognised measurement results.”
A discerning eye and uncompromising standards
‘Working with a sculptor's precision' is a fundamental part of Jingdiao's corporate DNA, so product quality has always been the first order of business. The company has put this philosophy into practice by procuring the most advanced measurement and testing equipment and instrumentation to ensure product quality, even in the early stages of Jingdiao's development when funds were limited. This arsenal of advanced equipment and instrumentation includes Renishaw's laser interferometers and ballbars, which are used to assess the precision of machining centres. Using world-leading machinery calibration equipment like the XL-80 laser interferometer and QC20-W telescoping ballbar has enabled Jingdiao to maintain strict control over product quality. Moreover, both laser interferometers and ballbars are equipped with a variety of dynamic testing features and fault analysis functions, which provide a wealth of invaluable data for use in new product R&D and the improvement of manufacturing processes for existing products.
Jingdiao invests heavily in updating its production and measurement equipment every year. Over a number of years, the company has bought several dozen Renishaw laser interferometers, which it buys exclusively, as well as Renishaw's updated next generation XL-80 laser interferometers, QC20-W telescoping wireless ballbars and XR20-W wireless rotary axis calibrators. Recently Jingdiao has ordered another five XL-80 and XR20-W systems in preparation for its next phase of large batch production and quality control for five-axis machining centres.
This specialised equipment and strict quality management ensure the high quality of Jingdiao's products. Jingdiao has a strong technology R&D team and comprehensive quality assurance systems. The company has developed its own data capture interface to utilise the automatic pitch error compensation features of Renishaw laser interferometers during product calibration; this system sends data from the laser interferometers directly to Jingdiao's machining centres via a USB interface, enabling rapid, efficient and precise calibration of machinery.
Unleashing potential through innovation and creativity
In order to meet requirements for improved product processing, Jingdiao has integrated Renishaw OMP40 and OMP400 probes as accessories for its machining centre products including its newly launched machine tool digital control machining centres. This enables the automatic update of component coordinate systems and automatic measurement of component dimensions. Jingdiao has also exploited the advantages of touch measurement by developing unique contour error compensation functions, which provide on-board compensation for the degree of deviation in component contours, enabling equivalent-depth cutting processing for contours to be processed.
Clamping or processing thin-walled components such as aluminium alloy parts can easily produce deformation of the component, making it difficult to ensure the precision of dimensions. This is when the OMP40 and OMP400 touch probes come into their own. Prior to processing, probes gather data on the outer contours of components and the results are stored in the machining centre's variable parameters; the processing cutting tools then follow this path as during profiling, thereby ensuring the precision processing of contours.
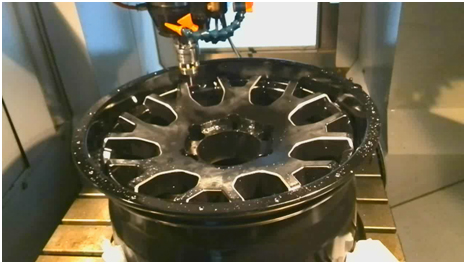
In 2013, Jingdiao went on to develop curved surface error compensation functions for its five-axis machining centres. This system provides on-board compensation for errors in curved surfaces, enabling the engraving of designs and reliefs on curved surfaces that follow surface errors.
We chose Renishaw products when our company was first founded because we admired their brand values and product performance. We compared precision calibration equipment, including laser interferometers and ballbars from a number of brands on the market, and found that of all the comparable products, Renishaw offered the most consistent performance and the most widely recognised measurement results.
Beijing Jingdiao Company Ltd (China)
Refined processing and precision measurement
CNC precision engravers are extremely demanding in terms of the precision of processing product dimensions for glass grinding. The number of broken edges during the CNC mould making process have a direct impact on the product's throughput yield. Jingdiao have sold more than 10,000 machines specifically for these applications. Jingdiao selected Renishaw's OMP400 high precision measurement probes and their NC4 non-contact laser tool setting system for these applications, which involve strict dimensional precision requirements and high batch production yield rates.
Processing of equivalent-width chamfering on deformed wheel hubsThe OMP400 offers the benefits of high-precision three-coordinate measurement; it has a measurement repeatability of up to 0.25 microns and can achieve a level of measurement precision in machining centre environments that compares favourably with CMM units. Using the OMP400 solves problems with batch production such as product positioning and product deformation, ensuring that products meet the highest precision requirements. The NC4 non-contact laser tool setting system utilises laser beams to measure the dimensions of grinding wheels, while the measurement data is able to automatically update cutting tool parameters. The NC4 can be used to monitor grinding wheel wear and make instant repairs, not only saving time on grinding wheel measurement, but also guaranteeing high levels of measurement precision.
The constant improvement of product performance and continual innovation enables Jingdiao to meet users' individual requirements. This win-win situation for both Jingdiao and its users is the company's ultimate goal. As Jingdiao's CEO Huang Shan says, “We are very satisfied with the performance of Renishaw's laser interferometers and ballbars, and for us, they are synonymous with high-precision measurement. Our experience over more than a decade of collaboration has let us experience first-hand the critical importance of the consistent operation of laser interferometers as precision references and the value of on-machine probing, in order to ensure high levels of performance for CNC engravers.”
Company background
Founded in 1994, Jingdiao has more than 10,000 customers around the world, and possesses integrated capabilities for independent R&D and manufacturing of CNC engravers, CAD/CAM software, numerical control systems and high-speed motor spindles. With more than 2,000 employees and annual production of more than 10,000 CNC engravers, Jingdiao is a high-tech enterprise that combines R&D, production and sales in a single company.