Selecting UHV-compatible encoders for demanding semiconductor and scientific applications
Many high-end semiconductor manufacturing processes require the processing environment to be completely free of any contaminants that cause imperfections within the semiconductor wafer and transistors being created. As the semiconductor industry moves to smaller feature sizes, larger wafers and more complex components with more processing steps, acceptable levels of wafer contamination are increasingly small.
These critical industrial processes take place in a vacuum because the presence of significant amounts of air or other gases would be detrimental to the finished product. Processes like semiconductor manufacturing that demand precision motion control need vacuum-compatible optical encoders for position feedback. Locating the position encoders within the vacuum chamber ensures that the measurement device is as close to the working environment as possible, ultimately minimising errors.
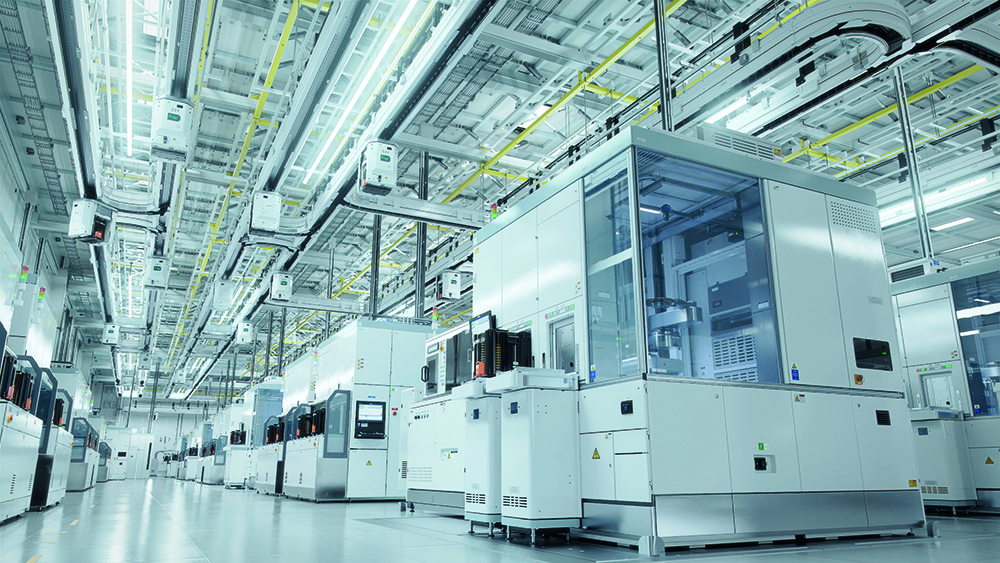
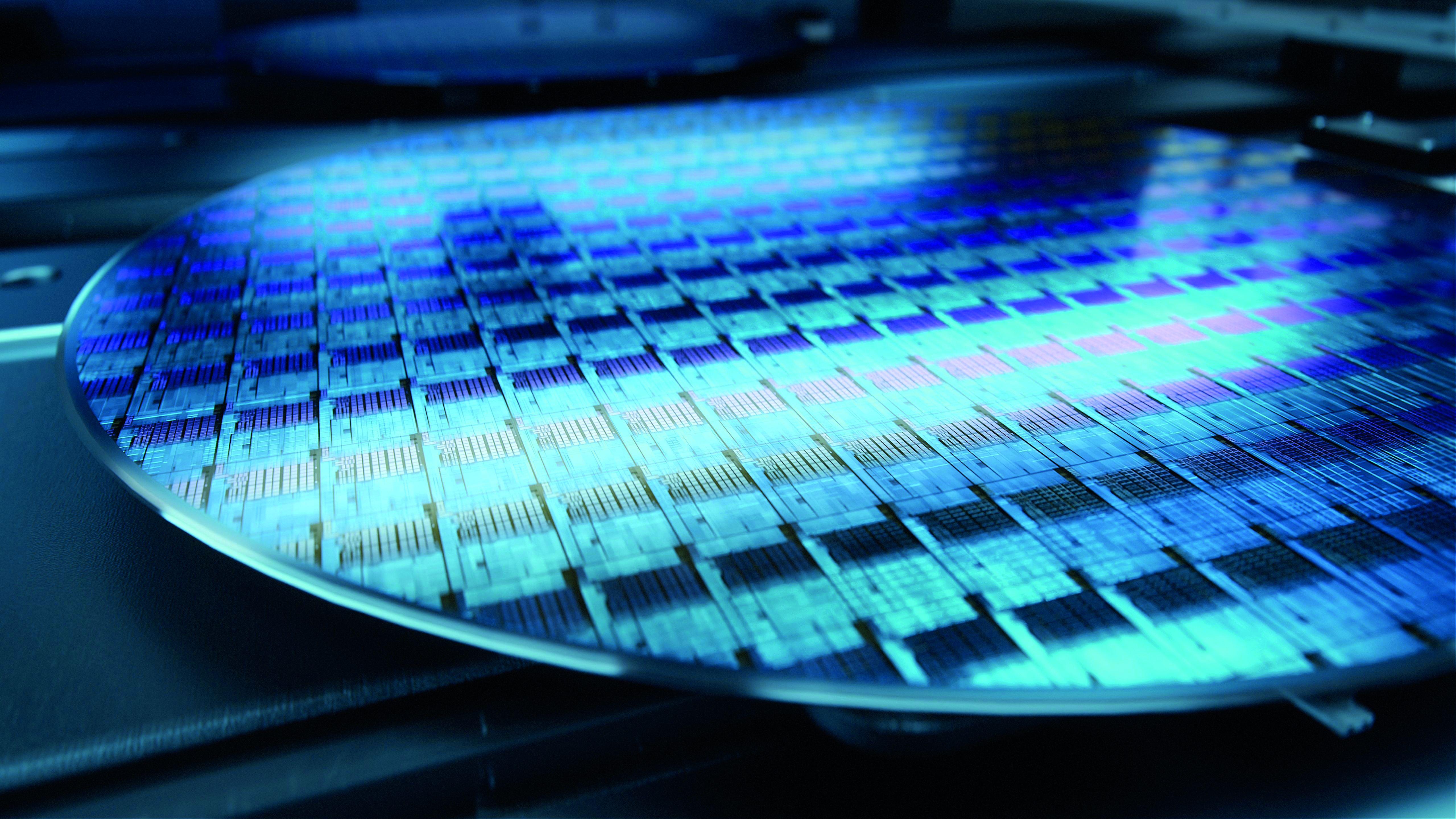
Optical encoder components, such as the readhead and scale, installed inside a vacuum chamber have several vital features including:
- High temperature resistance (>100 °C) to endure the bake-out procedures required for UHV.
- High cleanliness to eliminate surface fingerprints, oils, and lubricants.
- Low outgassing of contaminants into the process chamber.
- Air vents to ensure full venting of air spaces within the readhead.
- Cable with PTFE insulation and silverplated copper braiding.
Low outgassing characteristics and high precision are key requirements in most UHV applications.
Once these requirements are met, customers should consider the lifetime costs and risks associated with each potential solution. Component quality, pre-sales and after-sales support and delivery lead-times have a significant impact on the total cost of ownership of every encoder.
Wafer inspection
Wafer inspection is used throughout the semiconductor wafer patterning process. It is important for process control and helps to maintain high yields.
A wafer motion stage has at least two linear (X, Y) axes. Servo axis control loops use encoder feedback to deliver high levels of positioning accuracy.
An optical inspection head features high-resolution cameras with separate dark-field and light-field illumination sources. In automatic inspection, the head inspects the wafer and a comparison between each image capture and a ‘golden' or model reference image is used to locate defects.
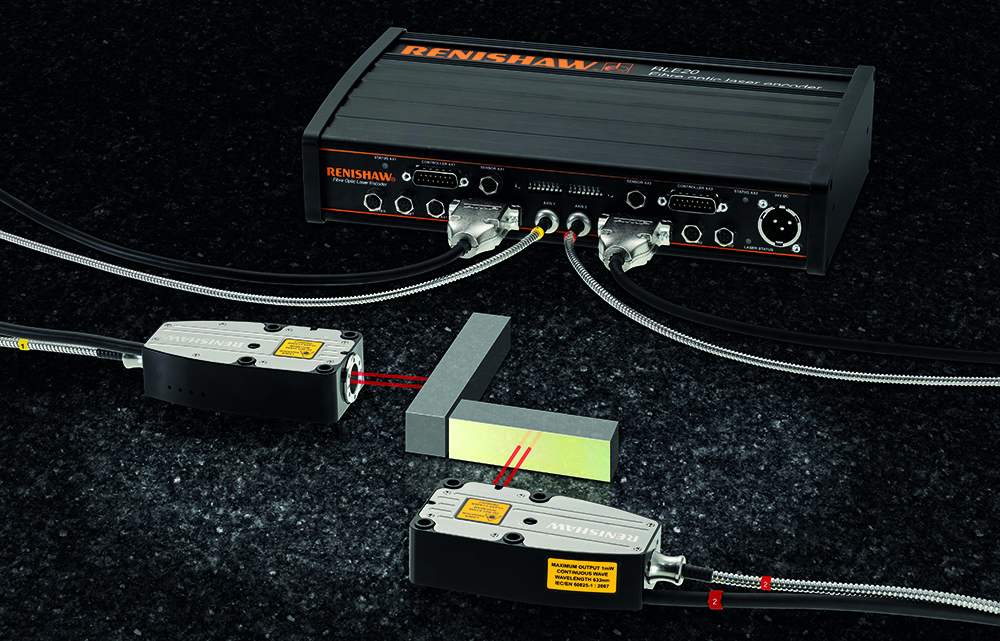
The head remains static while the wafer stage moves rapidly between positions to capture images of the subject. High-performance encoders enable faster positioning which helps to maximize throughput.
The sub-nanometre positional measurement provided by laser encoders enables multiple Scanning Electron Microscopy (SEM) images to be overlayed at a repeatable location for multi-layer defect review.
High-performance UHV optical encoders provide coarse position feedback to enable the wafer stage to follow the intended scan path with minimal torque ripple for smooth velocity control.
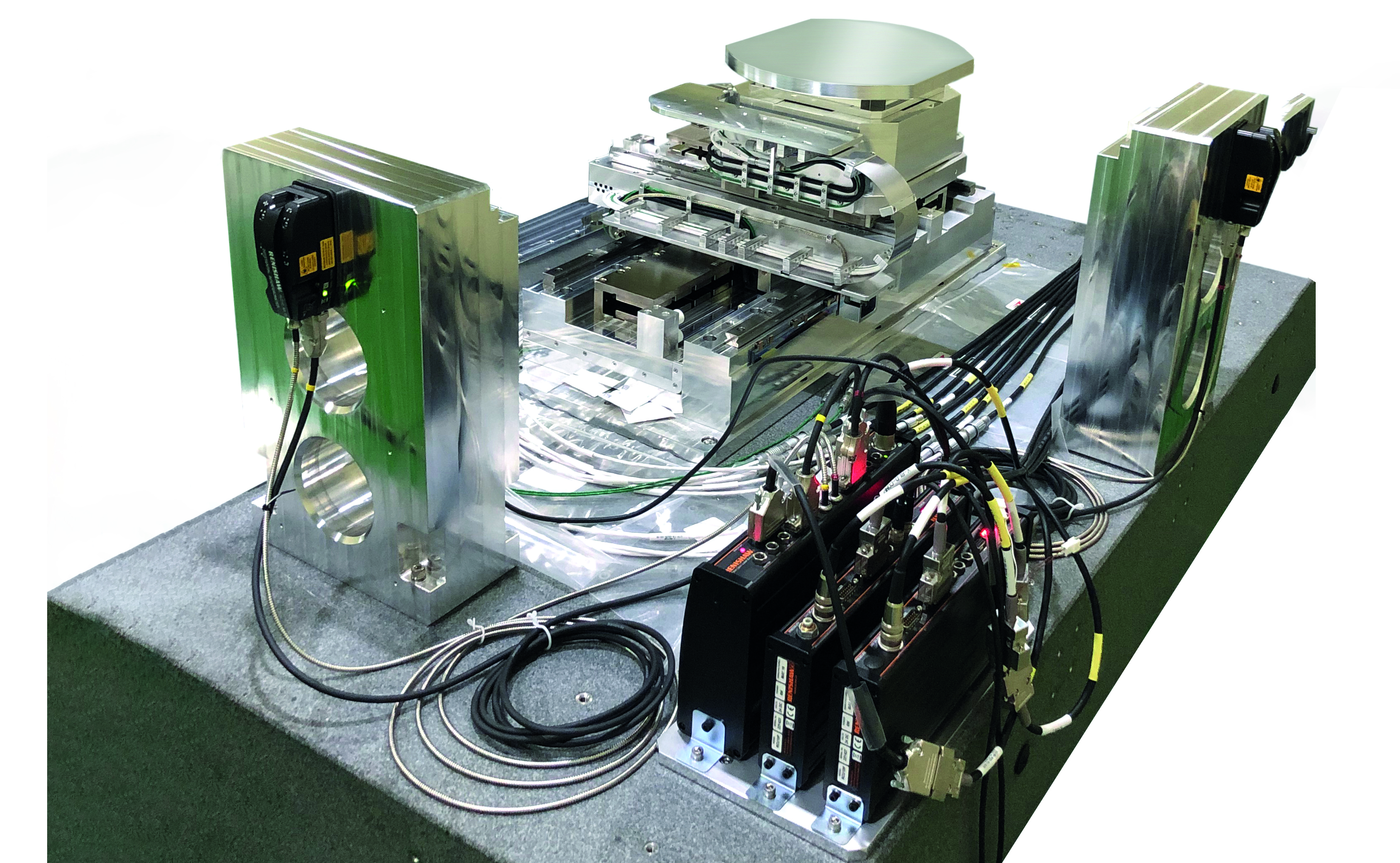
Semiconductor inspection stage with RLE laser encoder system
Encoder requirements for wafer inspection:
- Analogue signal outputs enable highest levels of interpolation and resolution.
- ≤1 nm jitter for exceptional servo control, static and dynamic stability, which is required to ensure successful image comparison and the stitching together of images.
- Non-contact measurement at the point of interest, to eliminate Abbe offset and mechanical errors.
- Measurement systems that can operate within ultra-high vacuum environments.
- Optical encoders with Functional Safety (FS) and dual analogue and digital output for the wafer scanning motion.
Encoder solutions for wafer inspection
Renishaw's RLE fibre optic laser is an interferometer-based system offering high resolution position feedback.
The differential interferometer head (RLD10) is designed to be mounted directly to the external wall of the process chamber and features a unique optical scheme to achieve a low Sub-Divisional Error (SDE) and high accuracy allowing output resolutions to 38.6 pm. Integrated beam steerers allow for pitch and yaw adjustment during set up which improves the alignment process.
TONiC™ UHV encoders are suitable for UHV conditions down to 10-10 Torr and offer resolutions as fine as 1 nm with low SDE to help realise superior motion control performance.
Renishaw's TONiC UHV encoders and accessories are constructed from vacuum-compatible materials and adhesives to give low outgassing rates, making them suitable for many semiconductor applications.
The TONiC UHV encoder range offers a functional safety variant (SIL2/PLd) and the option of dual analogue and digital output to enable the synchronisation of devices such as cameras with a motion axis. For linear axis applications, available scale materials include low expansion ZeroMet™ for high accuracy in thermally varying environments.
Wafer handling
Semiconductor wafers are fragile and expensive, and they must be handled with care so that they are not damaged during the manufacturing process. Consequently, wafer handling robots are commonly used to move semiconductor wafers inside process equipment.
A wafer-handling robot has multiple degrees of freedom and consists of a body, an arm with multiple joints, and a wafer holding tool (paddle). Handling robots typically move a wafer from one transfer chamber to another or between process steps and their throughput has a direct impact on the overall performance of semiconductor fabs.
The straight line and angular motions of a handling robot must be accurate to avoid any contact that might result in either damage or contamination of the wafer surface.
Robot arm control is achieved with a motorized upper arm pulley and upper-arm spindle that drive a series of endless belts, which link the shoulder joint to the elbow and wrist joints of the arm.
A master-slave relationship requires that position commands for one motor are determined by position feedback from the other.
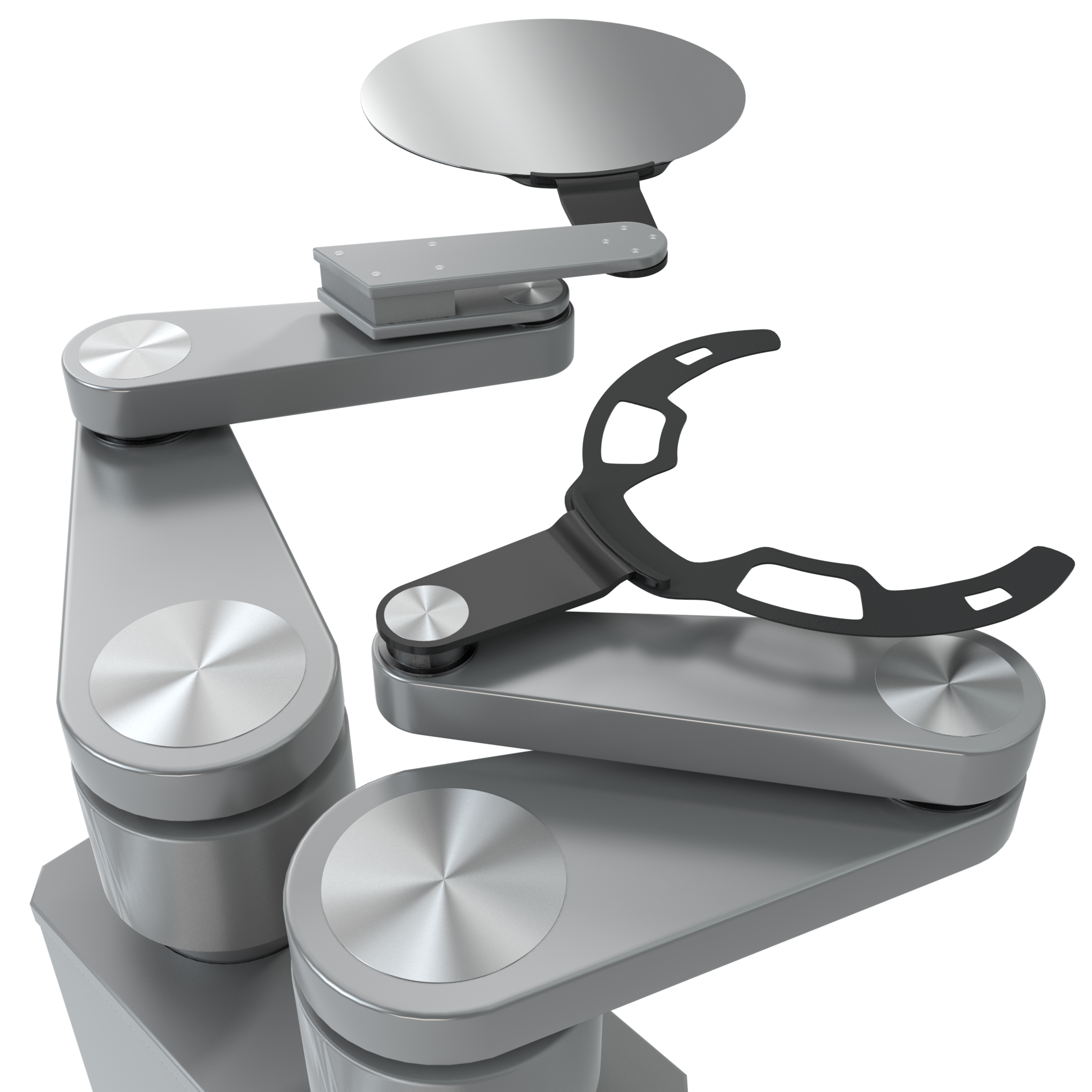
Encoder requirements for wafer handling robots:
- Absolute encoders may be preferred to eliminate the need for datum homing cycles and ensure that payloads remain under control even after power outages.
- High quality position encoder feedback with low cyclic error is needed to ensure minimal toque ripple for smooth velocity control and high precision.
- Encoders with position checking algorithms and additional safety features to guard against common-cause failures.
- Absolute or incremental encoders that offer high resolution at high operating speeds.
- Encoder systems with dual analogue and digital output signals to synchronise the operation of wafer grippers or calibration cameras.
- Encoders with UHV capability if appropriate.
Encoder solutions for wafer handling
RESOLUTE™ UHV encoders bring absolute encoder technology to ultra-high vacuum applications down to 10-9 Torr, allowing customers to achieve higher throughput, reduce risks of damage and increase dependability.
RESOLUTE encoders offer outstanding metrology performance in UHV applications with resolutions down to 1 nm at a wide range of speeds.
TONiC UHV encoders are suitable for UHV conditions and use filtering optics and dynamic signal processing to give low Sub-Divisional Error which enables highly precise motion control.
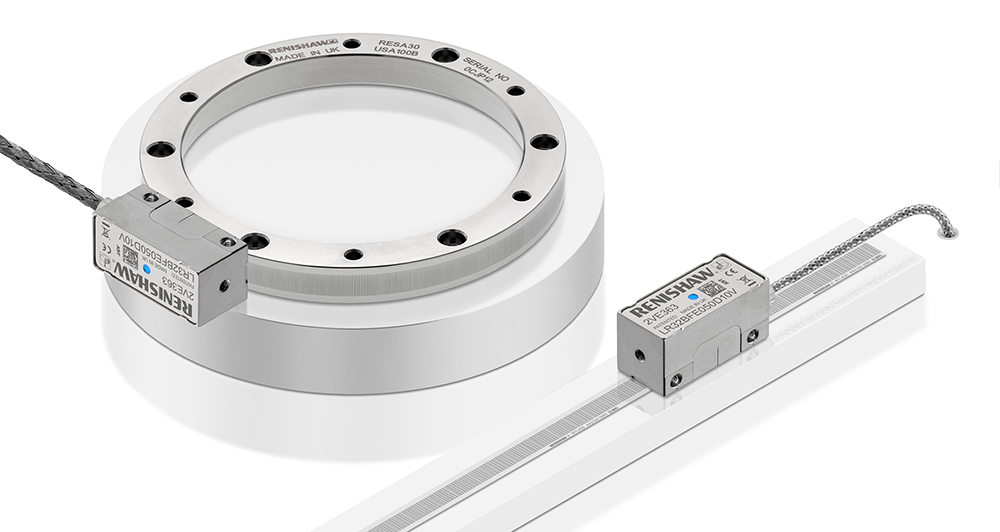
Synchrotron mirror bending
A synchrotron is a type of particle accelerator that provides an extremely powerful source of X-rays used for scientific research.
The perfect shape for a focusing mirror is an ellipsoid, but ellipsoidal mirrors are difficult to manufacture. An alternative approach is to use a pair of mirrors arranged perpendicularly to each other which focuses the beam in two dimensions: a Kirkpatrick-Baez (K-B) mirror system is a well-known example.
K-B systems are usually mounted on a series of in-air and in-vacuum motion stages that use position encoder feedback to precisely control mirror translations and rotations in the beam. Due to the small grazing angles of incidence of the X-rays on each mirror, the correct mirror shape is achieved by the application of bending forces.
Actuators attached to the ends of each mirror also require encoder feedback to precisely control the mirror shape.
Encoder requirements for synchrotron applications:
- Translational accuracies of better than 0.5 µm.
- Angular resolutions down to 0.1 µrads.
- Robust design resistant to high levels of vibration.
- UHV-compatibility and resistance to 120°C.
Encoder solutions for mirror benders
RESOLUTE UHV encoders are suitable for use inside UHV enclosures. Renishaw's range of RESOLUTE UHV encoders are intended for high performance, semiconductor, and scientific applications.
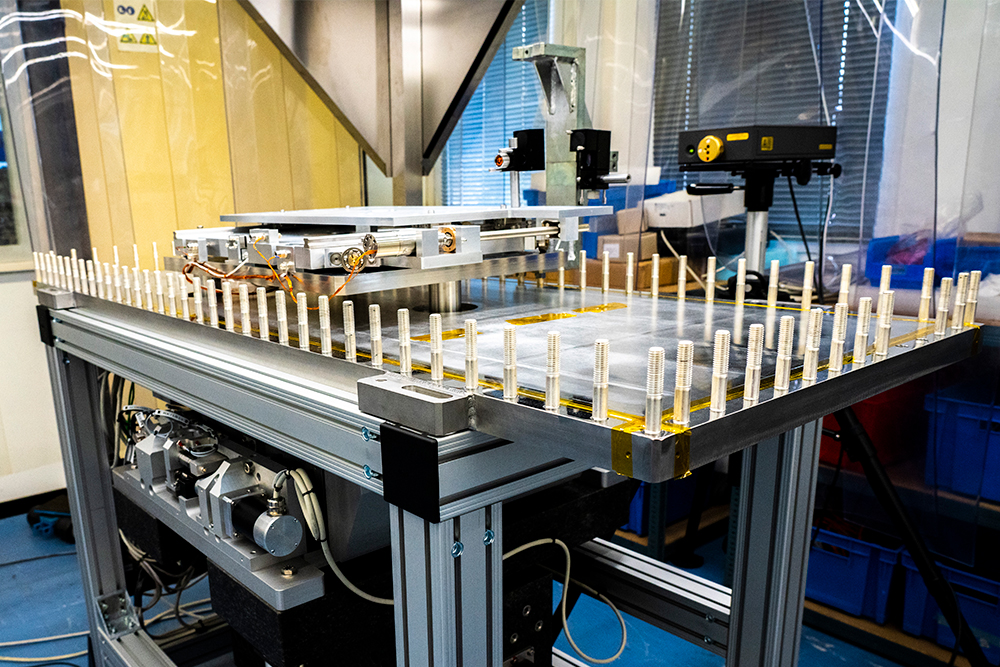
UHV motion stage for synchrotron mirror
Conclusions
When selecting a position encoder for semiconductor and scientific applications many of the normal considerations apply – does the process require absolute or incremental position feedback? How will the encoder interface with the rest of the motion system? What are the metrology requirements of the process? Are there thermal and environmental issues that impact the choice of encoder? How will the encoder system be installed and commissioned?
Strong application and customer support around the globe is essential to help customers answer these questions. For this reason, Renishaw customers enjoy working with us and our products.
By supporting customers with local technical expertise and responsive and flexible supply chains, Renishaw helps to reduce the lifetime costs associated with its encoder products.