What are the benefits of using encoders in motion control?
Explore the position feedback benefits of using Renishaw optical encoders
Our robust and high-performance position encoders can solve your precision measurement challenges. We provide expert solutions for the diverse requirements of industrial automation. Some of the main benefits of using encoders in motion control are:
- High-accuracy
- Easy installation
- Superior reliability
- Low Sub-Divisional Error (SDE)
- High-speed operation
- Non-contact design
- Incremental and absolute measurement options
- Open and enclosed encoder technology
Encoders are used in a wide range of applications and industries to provide precision position measurement through electrical feedback signals. Renishaw encoders offer absolute and incremental position measurement to solve a range of position measurement and motion control challenges.
See real-life examples of our optical encoders in action:
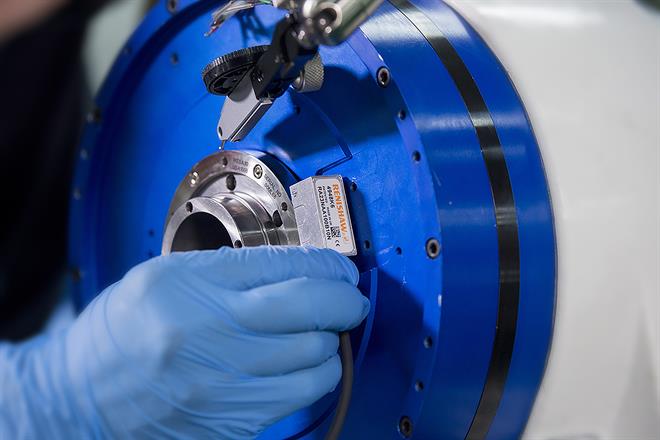
See how others have trusted Renishaw encoders. Our case studies and application notes showcase our robust and high-performance encoder products in industry. The applications vary from electronics and precision manufacturing to aerospace and medical.
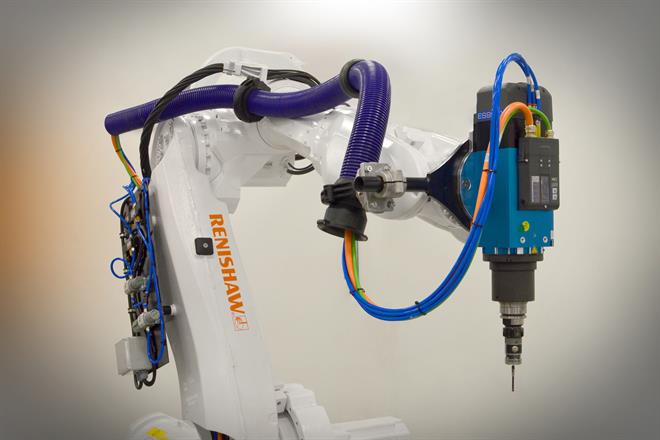
Read our range of insightful articles about encoder usage and trends in industry. Find out about Renishaw's encoder technology, products and industry knowledge. Discover how our encoder technology works and can benefit your manufacturing processes and systems.
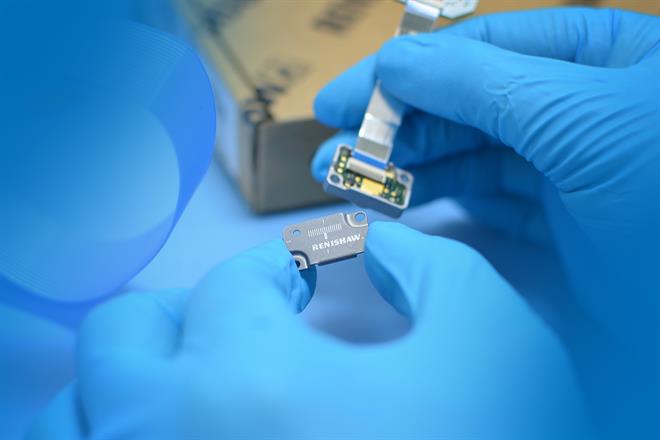
Download technical white papers about Renishaw optical encoders. The purpose of our papers is to share our expertise about varied complex issues such as thermal performance of linear encoders, accuracy of angle encoders, safety aspects and vibration resistance.
Our case studies demonstrate how Renishaw encoders are used in a varied range of industries:
- In the semiconductor industry, absolute position encoders deliver high precision and high stability for wafer assembly and packaging equipment. The set-up LED makes installation easy, reducing costs and increasing efficiency in production.
- In an observatory, encoders are attached to the telescope's axes and send a feedback signal that can be used to determine position, count, speed, or direction of the telescope as it moves. Encoder systems with stainless steel linear scales provide smooth velocity control to control the orientation of the telescope accurately.
- In precision industrial processes carried out in vacuum environments, UHV incremental encoders provide position measurement without contaminating the vacuum environment.
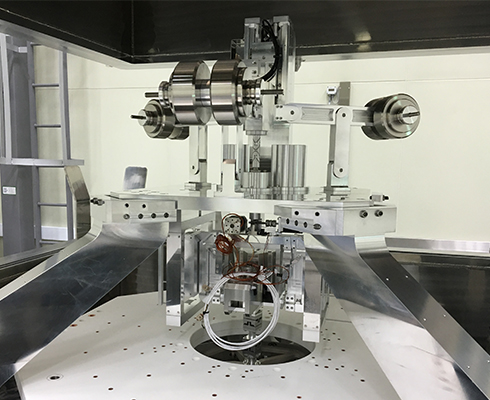
- The production efficiency of multi-axis rotary tables and their servo motors is enhanced by absolute rotary encoders. They can restart after machine stoppages and resume operation without losing position.
- In the harsh environment of precision tool grinding machines, position feedback for linear motors is provided by enclosed encoders. Benefits include improved machining accuracy and process stability. The result is enhanced productivity and optimisation of machine tool performance.
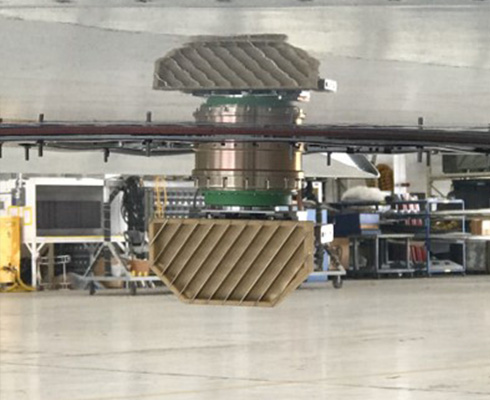
- Direct drive (DD) motors are designed for precision process equipment in the flat panel display (FPD) industry. Integrating miniature encoders for position feedback can satisfy end-users for size, weight, performance and reliability.
- In scientific applications, position encoders selected for in-vacuum stages are ultra-high vacuum (UHV) compliant and robust enough to endure sustained bake-out temperatures of 120 ºC. (IRELEC)
- Radar and radio frequencies (RF) communications systems for airborne applications need to be light-weight, compact and powerful. These systems must also be modular and easy to assemble. Encoders are critical components in communications and radar applications and need to be highly reliable, as a failure could potentially endanger lives.
- The thermal behaviour of encoder scales is an important consideration when selecting any encoder system for surface mount technology (SMT) applications. Floating encoder scales expand and contract with approximately the same coefficient of thermal expansion (CTE) as the scale material and have a known CTE, which can enable the effective use of active scale temperature compensation.
- In medical pathology equipment, digital slide scanners integrate position encoders for direct feedback to the controller. This enables operation at much higher speeds without compromising accuracy: higher automation reduces the level of operator interference required between micrographs, which translates to less time taken per slide and higher process throughput.
Our optical encoders are available in a variety of configurations, including incremental or absolute, and can be linear, rotary, or designed for partial arc applications.
Contact our sales team today
Get in contact with your local office to find out more information and speak to an expert.