IPC intelligent process control
Process control can be achieved with closed-loop feedback using Equator™ gauging data to update offsets directly on machine tool controls.
Real-time feedback
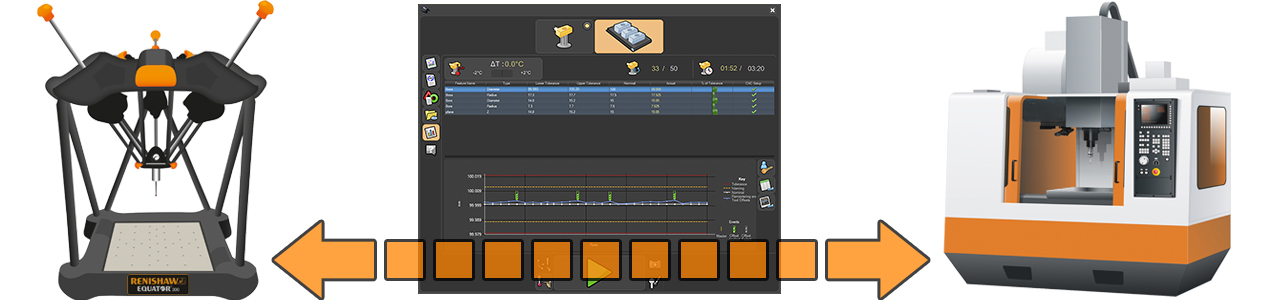
The gauging results can be easily read in real-time by IPC, which offers the ability to connect to certain modern machine tool controls. This allows offset values to be updated, enabling true automated process control. Data from the Equator gauge can be used to update offsets repeatably and reliably, compensating for common causes of process instability, for example tool wear and thermal drift.
Control process capability
Offsets can be statistically controlled to improve the capability of machining processes, resulting in improved quality and higher yield. This is achieved by using a running average of feature measurements to calculate compensation values and standard deviation to calculate control limits.
Cutting tool life management
When a tool has been compensated more than the maximum tool offset (user defined) a wear-limit warning is issued, informing the machine tool that the cutting tool needs to be changed. The machine tool can then decide to use a sister tool or to stop the process before the next cycle.
Update multiple machines
The Equator gauge can send offset update values to several machines on a feature by feature basis meaning you can update multiple tools on multiple machines simultaneously. For example, OP10 and OP20 processes can be controlled with one gauging cycle. All data is saved and time stamped for later analysis.
Key features
- Reduction in human intervention
- Reduction in machine downtime
- Errors recorded over several parts are averaged - leading to more accurate updates
- No time delay, due to proximity to machine tool
- Allows One-to-Many (Equator system to machine tool) updating
Easy dimension setup
- Select dimension to use
- Set control limits
- Set correction characteristics
- Select machine to update
- Set tool offset information