ASMPT chooses Renishaw for high-quality motion control
ASMPT is committed to the advancement of semiconductor assembly and packaging equipment and offers solutions for industrial automation in a wide range of semiconductor applications.
It operates in over 30 countries with research centres, production facilities and commercial offices spanning Asia, Europe, and the Americas. More recently, ASMPT expanded through a series of targeted business acquisitions, adding several equipment brands including ALSI, AMICRA, NEXX, and the AEi team.
These acquisitions have enabled them to provide customers with a broader range of process solutions.
With its exceptional market insights as a leading manufacturer of electronics and semiconductor process equipment, ASMPT has progressively introduced industry-specific equipment to meet new and demanding market requirements and it is consistently ranked among the top global manufacturers of semiconductor process equipment.
Renishaw's relationship with ASMPT is now in its 25th year. Both companies have accumulated extensive shared experience in areas such as position encoder applications, customised solutions and machine testing for quality control, whilst building a close business relationship.
Challenge
Modern semiconductor packaging and assembly processes require demanding performance in position accuracy and stability, machine size and weight, quality control and process throughput. Position encoders play a crucial role in motion control, and suppliers need to develop new technologies and introduce innovative solutions to meet the rigorous demands of this market.
In the realm of assembly and packaging process equipment, selecting the right encoder is critical. ASMPT highlights several essential features that buyers should consider:
Speed
High-speed operation is a growing requirement. Analogue output and digital output encoders offer various advantages. Analogue encoders are well-suited to high-speed applications, whilst digital encoders provide position measurement with low noise at fine resolutions.
Jitter
Precise positioning demands low positional noise (jitter) when the machine is not moving. Low encoder signal jitter reduces heat generation in linear motors and enhances motion control performance.
Size
In space-constrained applications, the encoder readhead and interface must be as compact as possible.
Safety compliance
Compliance with international safety standards is essential. Encoders are tested against performance standards and regulations such as EMC (electromagnetic compatibility) and RoHS (Restriction of Hazardous Substances). Cables also undergo rigorous electrical and mechanical life tests.
Encoders are needed not only for higher resolution feedback in motion control but also to hold stable position. This poses a significant challenge for both controllers and encoders, but we have never doubted Renishaw's capabilities.
ASMPT, Singapore
Solution
ASMPT has employed various Renishaw encoder products over the years including the ATOM DX and VIONiC incremental encoder series and the RESOLUTE absolute encoder series. These encoders are used in a wide range of assembly and packaging process equipment including ASMPT's INFINITE — a 12-inch die bonder designed for general IC (integrated circuit) packaging.
This advanced system boasts innovative features such as precise epoxy dispensing control and inspection capabilities for measuring bond line thickness with micron-level accuracy.
As a crucial component in motion control systems, excellent encoder performance is fundamental to meeting the rigorous and increasing demands of the market.
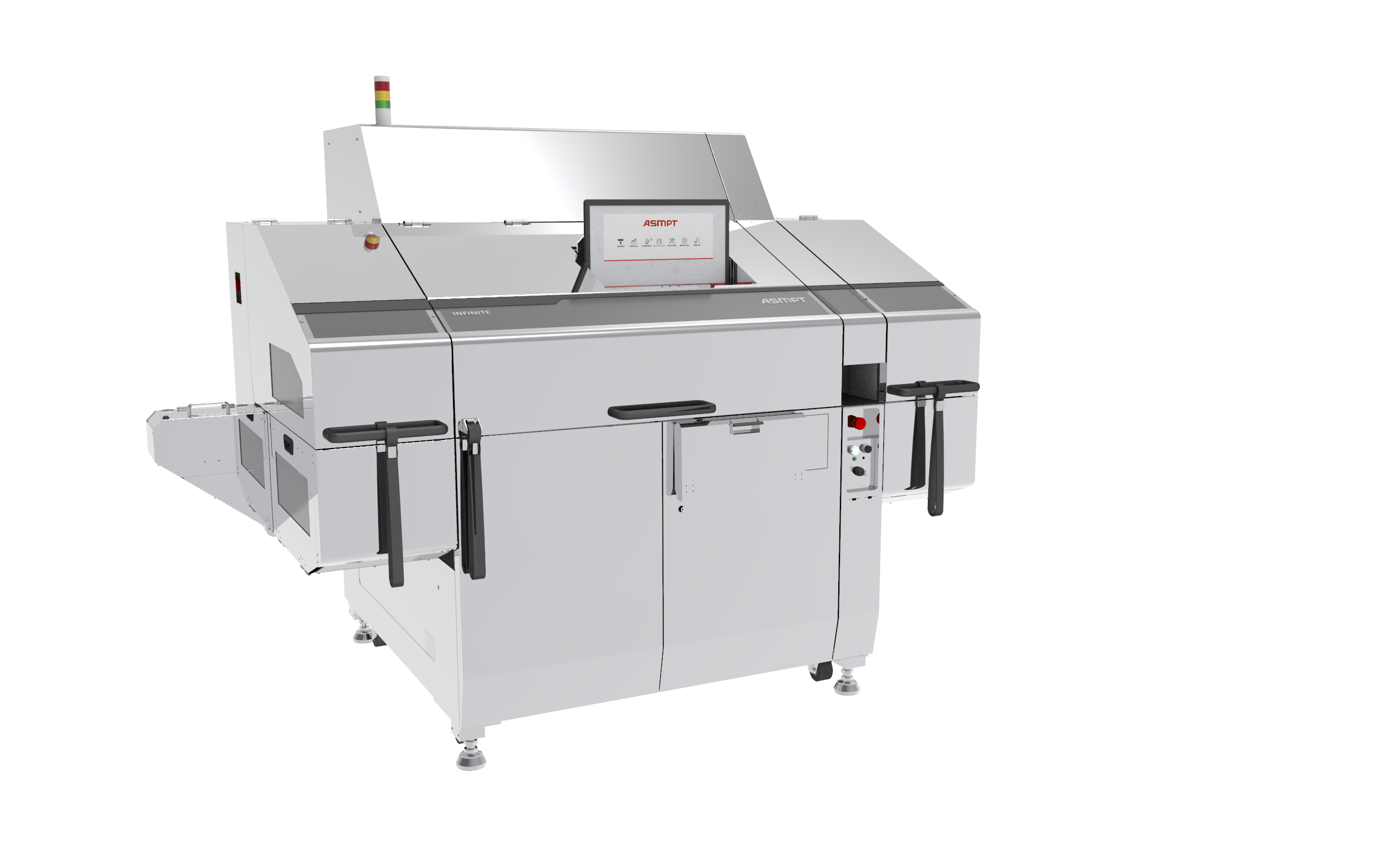
Considering that back-end equipment can accommodate up to twenty readheads, it is essential to minimise the impact of the space occupied by these interfaces within the machine design.
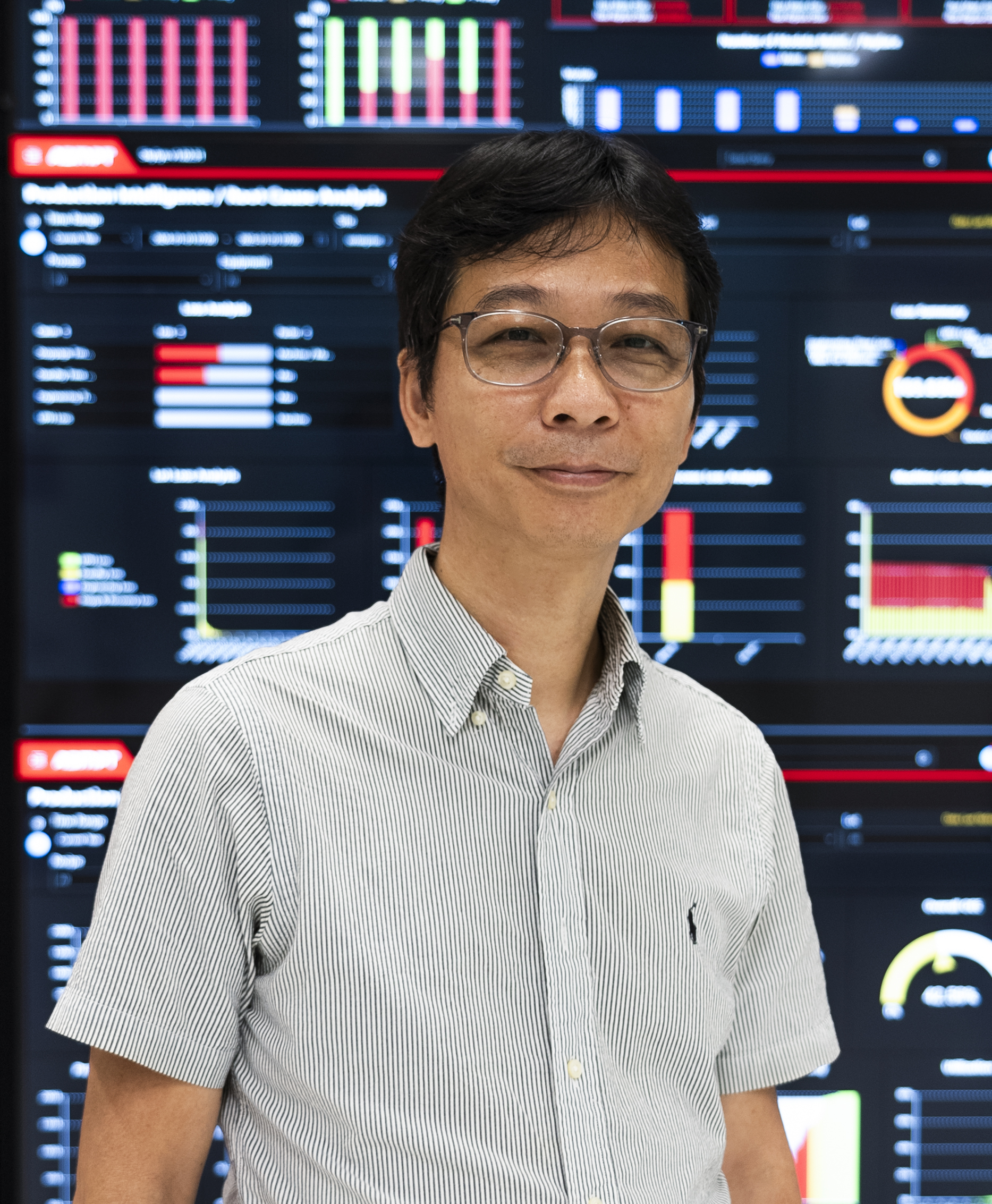
Given the application requirements of certain advanced packaging manufacturing equipment, it becomes imperative to utilise materials that exhibit less sensitivity to temperature for the working head; in other words, we need materials with a low thermal expansion coefficient, explained Dr. Joseph Choy, Senior Research and Development Director at ASMPT.
"However, these materials are typically heavier, which increases the overall equipment weight and introduces challenges in controlling inertia. Renishaw's ATOM DX encoder series solves this problem and significantly reduces the space occupied and weight, while improving the flexibility of our equipment design process."
The ATOM DX encoder directly outputs digital signals from the readhead and integrates all position feedback, onboard interpolation, and optical filtering functions within its miniature package. The readhead is designed to be extremely compact, with a minimum packaged size of 20.5 mm x 12.7 mm x 7.85 mm, allowing for installation in very small spaces without the need for additional connecting interfaces, saving significant space on ASMPT machines.
The ATOM DX encoder series delivers excellent performance with a resolution of up to 2.5 nm and advantages such as low Sub-Divisional Error (SDE) and low signal jitter.
To streamline maintenance procedures, precision semiconductor manufacturing equipment often features a design that allows the cables to be detached from the encoder readheads within a module.
These options include smaller-sized circular connectors or flying leads that can be soldered by the customer according to their specific requirements.
Dr. Choy shared his views on future market trends:
"It is foreseeable that the specifications for encoders will evolve towards higher speeds, higher resolutions, and lower jitter. Encoders are needed not only for higher resolution feedback in motion control, but also to hold stable position. This poses a significant challenge for both controllers and encoders, but we have never doubted Renishaw's capabilities."
System diagnostics
Typically, the set-up LED on the encoder readhead provides sufficient status information to ensure a successful installation. In more challenging installation scenarios, Renishaw's Advanced Diagnostic Tool (ADT) can provide additional real-time data reporting, aiding installation and diagnostics. The ADT has thus played a pivotal role in ASMPT's equipment development and production processes, particularly for its high-end equipment models.
“Renishaw's ADT has been immensely helpful for us, allowing our engineers to quickly establish the installation status of encoders and identify the root cause of problems by assessing signal strength variations at different positions,” affirmed Ir George Chan, ASMPT Technical Manager.
In the era of Industry 4.0, many equipment suppliers in the market have introduced self-diagnostic capabilities, which help to identify potential equipment problems and trace the source of faults. Renishaw's ADT enables customers to capture real-time data from the encoder via connection to a computer running ADT View software.
Product safety
Ensuring the highest level of product safety is of utmost importance for ASMPT. It is committed to complying with local regulations and standards (e.g. RoHS, EMC, REACH, IEC) and other relevant safety certifications, to guarantee the safety and quality of its products. Due to the multidisciplinary nature of ensuring product compliance in different countries and regions, the verification process is subject to continual change.
As a component supplier, Renishaw collaborates closely with ASMPT to provide detailed verification documents and support. Ir George Chan elaborated further:
"Renishaw encoders have consistently demonstrated safety, stability and reliability, and the newly launched encoder models have also performed exceptionally well. The technical team possesses extensive knowledge in compliance, and Renishaw have dispatched engineers on several occasions from the UK to Hong Kong to assist us, providing valuable and practical solutions that were very much appreciated."
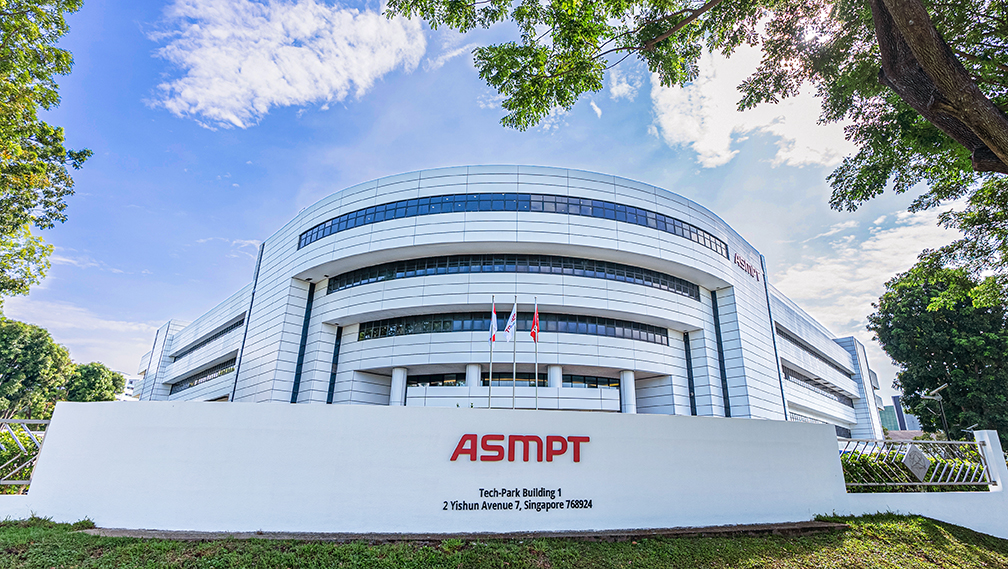
Calibration
ASMPT has multiple Renishaw XL-80 laser interferometers and one Renishaw XM-60 multi-axis calibrator. These systems play a crucial role in both process equipment manufacturing and regular preventative maintenance.
ASMPT uses the XL-80 laser interferometer in conjunction with the Renishaw XR20 rotary axis calibrator to perform precision quality checks on each direct drive rotary motor during their manufacturing process. This helps ensure that the accuracy and quality of the production equipment meet the required standards. In terms of maintenance, ASMPT is responsible for the preventative maintenance of process equipment at various customer production sites.
This includes using the XL-80 laser interferometer for diagnostics and calibration to ensure the best equipment performance during operation.
The Renishaw XM-60 multi-axis calibrator simultaneously measures errors in six degrees of freedom with one set-up. This helps understand and characterise the accuracy and machining capabilities of all processing equipment. This allows efficient allocation of resources, ensuring optimised equipment operation and maximum efficiency.
Summary
The manufacture of assembly and packaging equipment faces significant challenges related to quality control and productivity.
Quality control is crucial in the manufacture of process equipment as it ensures specifications and reliability standards are met, guarantees process consistency and helps to minimise defects and variation.
ASMPT uses a range of Renishaw products including laser inspection equipment, position encoders and calibration equipment.
ASMPT has introduced new products designed to meet growing demand for semiconductors due to emerging technologies. Renishaw, a long-standing metrology supplier, offers extensive experience in quality control, encoders and customised solutions.
Encoder solutions include the ATOM DX miniature incremental encoder series, the VIONiC incremental encoder series, as well as the RESOLUTE absolute encoder series. Renishaw's Advanced Diagnostic Tool (ADT) and readhead set-up LEDs also play an important role in encoder installation and diagnostics.
Furthermore, ASMPT uses Renishaw XL-80 laser interferometers, XR20 rotary axis calibrators and XM-60 multi-axis calibrators for precision checks during manufacturing, verification and validation (V&V), and maintenance. These metrology products ensure the optimum level of process equipment performance and efficiency.
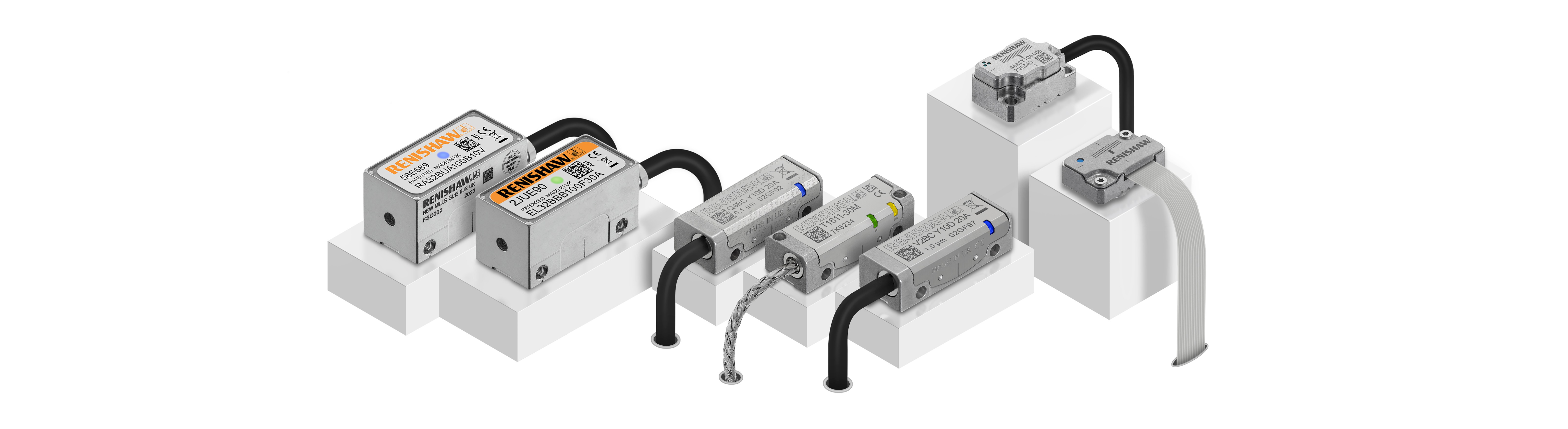