Diese Seite steht derzeit nicht in Ihrer Sprache zur Verfügung. Mittels der
Übersetzungsfunktion
von Google kann Ihnen eine automatische Übersetzung angezeigt werden. Bitte beachten Sie jedoch, dass wir keinerlei Verantwortung für diese
Dienstleistung tragen und die Übersetzung auch nicht von uns geprüft wurde.
Wenn Sie weitere Unterstützung benötigen,
kontaktieren Sie uns bitte.
Volumetric compensation through interferometry improves machine performance
Background
BOST Machine Tools Company is a premium manufacturer of vertical lathes based in Gipuzkoa, Spain. Their machines are used in sectors where complex and high-value parts are produced.
To ensure the quality of their machines, BOST frequently uses Renishaw's calibration products for machine installation and set-up; both at their own facilities and those of their customers. This calibration process involves the use of laser interferometry to apply volumetric compensation, which helps to improve the quality of the machine tool.
Challenge
The manufacturing industry is seeking more flexible and accurate production resources. BOST machine tools must exhibit high repeatability and minimal geometric errors to meet these demands. These geometric errors can result from several factors, such as manufacturing defects or wear, and can cause machines to be inaccurate in their positioning.
To address this issue BOST decided to use geometric compensation. This process involves measuring and calibrating a machine's geometric deviations at different points and directions. It is customised to suit a machines specific requirements, ensuring essential factors such as thermal stability.
Once applied, volumetric compensation improves the accuracy of the machining process, resulting in high-quality, accepted final parts while also reducing production costs.
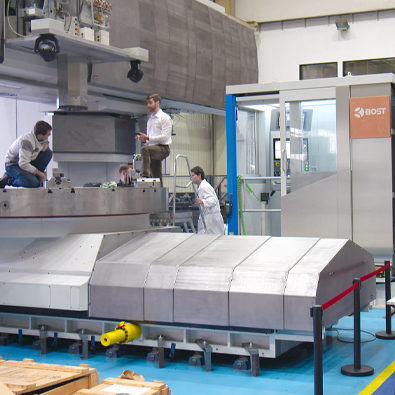
Solution
BOST sourced Renishaw's XM-60 multi-axis calibrator to carry out the volumetric compensation for their large diameter vertical lathes. This reduced the verification process from several days; to just a few hours, resulting in a decreased cost for machine calibration.
Using the XM-60 multi-axis calibrator, BOST is now able to measure all six errors from a single capture per axis: positioning, horizontal and vertical straightness, pitch, yaw, and roll. When the measurement is applied to the X, Y and Z axes, it increases the detection of errors to 18. The remaining 3 errors to be measured to reach 21, needed to volumetrically compensate the machine, are obtained using Renishaw's QC20 ballbar and XK10 alignment laser system.
Renishaw's calibration solutions enable this process to be carried out in below-average time periods, reducing cost and minimising the occurrence of problems, such as thermal drift.
The volumetric compensation of a machine tool enables you to improve its performance by a large percentage, ensuring the optimal function of the whole process.
BOST Machine Tools (Spain)
Conclusion
Renishaw offers a comprehensive range of solutions for all stages of the production process. These include process foundation, process setting, in-process control, and post-processing.
Calibration products and software play a crucial role in the process foundation stage. Renishaw is an expert in volumetric performance and compensation, providing customers with the necessary tools to maintain their machine tools for optimal machining processes. This is particularly important for large, complex parts with tight tolerances, where the entire volume of the machine must be calibrated under controlled environmental conditions.