Tato stránka není v současné době k dispozici ve vašem jazyce. Automatizovaný překlad můžete zobrazit pomocí nástroje Google Translate. Neodpovídáme za poskytování této služby a výsledky překladu jsme nekontrolovali.
Potřebujete-li další pomoc, kontaktujte nás.
The world’s No.1 semiconductor assembly & packaging equipment manufacturer benefits from Renishaw’s innovative products
ASM Pacific Technology Ltd (ASMPT), the world's largest supplier of wafer assembly and packaging equipment for the semiconductor industry, aims to offer complete factory automation solutions and satisfy customers' needs through its innovative and cost-effective products.
ASMPT was founded in 1975 and has a strong global presence, with more than 30 offices worldwide and multiple R&D and manufacturing sites in Hong Kong, Singapore, Malaysia and China. As a leading high-tech enterprise, ASMPT's 15,000 employees share the goals of providing high performance machines and strong after-sales service. Innovation and quality are critical to this success. ASMPT only work with suppliers who are capable of meeting their expectations, and have been using a range of Renishaw's encoder, calibration and Coordinate Measuring Machine (CMM) products for more than 15 years. In 2011, ASMPT acquired the Electronics Assembly System division from Siemens AG and entered the surface-mount technology market for the first time.
A wide variety of Renishaw encoders is employed in various ASMPT machines including the TONiC™ incremental optical series and the RESOLUTE™ absolute optical range as well as the LM10 magnetic encoder system by RLS, a Renishaw associate company.
Renishaw encoders are found in:
- AB559 series wedge bonders, designed with a large aluminium bonding area of 8 inches x 4 inches and speeds to 4.1 wires/sec
- High speed MCM12 die bonders: a fully automatic multiple die, SMD, and flip chip bonding system, up to 14 types of picking tools and 12 inch wafer handling capability
- SMD and flip-chip bonders with up to 300 mm wafer handling capacity
- UV Cured Die bonders: used in image sensor applications with resolutions to 50 nm and speeds to 3.5 m/s in operating temperatures as high as 300 ºC
Benefits
ASMPT's equipment is renowned for high precision and high stability. Consequently, it demands reliable and high quality positioning systems. Renishaw has a long history of developing high performance encoder products that are capable of meeting the diverse and demanding requirements of industrial automation. One good example of such requirements is the ‘dirt immunity' capability, achieved with specially designed and patented optical schemes, which are built into every encoder readhead to withstand a variety of contaminants such as grease, dust, particles and scratches. ASMPT Technical Manager Dr. Joseph Choy noted: “The positive feedback from our customers has proven that Renishaw's encoders have excellent dirt immunity and can run reliably with little or no maintenance.”
Another requirement is size; most bonders from ASMPT are extremely compact in their design and have limited spaces for mounting encoders - each bonder can have up to 17 moving axes each requiring independent position feedback. Renishaw's TONiC™ series encoders are well suited for this application and these compact readheads are used in conjunction with RGS tape scales (not recommended for new designs, alternative upgrade: RKLC scale), which are the lowest mass scales on the market weighing a mere 15 g/m with a thickness of 0.2 mm. “In many applications, the scale is the moving part with a speed of up to 3 m/s back and forth, so inertia is an important factor for the required acceleration and deceleration. Renishaw always keeps on the top of technology trends, delivering innovative encoder products to industries. We can concentrate our efforts on new product development as Renishaw's technology always keeps pace with us. A good example is their latest RESOLUTE series,” adds Dr. Choy.
Every Renishaw encoder is well-designed to meet the needs of the most demanding applications. Renishaw was the first manufacturer to introduce the non-contact optical encoder with a set-up LED, for optimal installation with minimal effort. Dr Choy continues: “From RGH to RESOLUTE, we have experience with every generation of Renishaw's encoders. Although the technology has been significantly enhanced, the installation is still as simple as ever. The set-up LED makes our job easier. Imagine how cumbersome it is when you have to tune more than 10 encoders per machine using an external plug-in device. Simple installation means cost reduction and greater efficiency in production which is absolutely essential for maintaining our competitiveness and leading position in the market. Moreover, Renishaw's TONiC DSi ultra-high accuracy rotary encoder system with dual readheads enables to us to eliminate the errors associated with rotor eccentricity, removing the need for compensation, which again reduces our costs.” Renishaw's TONiC series encoders feature unique AGC (Automatic Gain Control) which maintains an analogue signal amplitude of 1 volt to further enhance the accuracy and stability of the position feedback.
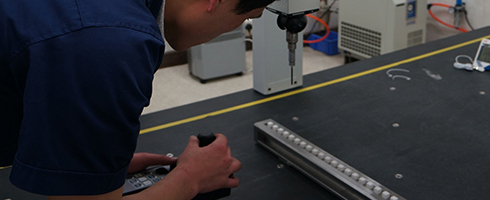
Custom made solutions
The semiconductor industry is unforgivingly fast-paced and competitive. ASMPT's leading position depends on its ability to remain at the forefront of continuous technological advances. Success hinges on solid technical strengths from R&D, years of experience, and components which can match certain special needs. Renishaw understands this and has strongly supported the development of these machines often by providing custom solutions to optimise the design, which in turn drives Renishaw to be innovative with its encoder products, illustrating the closed loop of innovation possible between Renishaw and its customers.
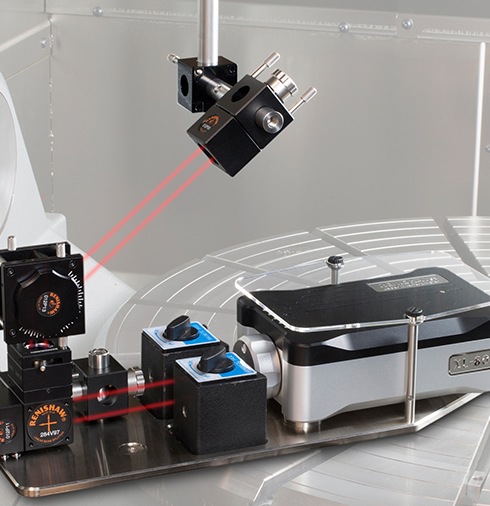
Performance verification, inspection and service
Overall machine performance also needs to be verified, and ASMPT has invested in several of Renishaw's calibration products, including the XL-80 laser calibration system, RX10 rotary axis calibrator and QC20-W ballbar system. These are used by R&D engineers for performance verification of ASMPT's machines, including positioning accuracy and dynamic characteristics, and by ASMPT's production staff to regularly calibrate their CNC machine tools to ensure the accuracy of manufactured parts. Jimmy Siu, ASMPT's Maintenance Manager explains: “Many parts are made in-house. Our role is to ensure all the machine tools are functioning well every day. Before Renishaw, we used hand tools to perform the maintenance work but we have realised that the traditional methods no longer satisfy our needs as our production capacity expanded. In our Huizhou's plant alone, we have over 400 machine tools, so you can imagine how heavy our workload is. Additionally, hiring experienced employees is not an easy task in China. Renishaw calibration and ballbar systems allow us to identify potential errors early to minimise scrap and downtime. It's truly portable and the ballbar, especially, is much simpler than I imagined. I can operate it after one day of training from a Renishaw engineer”.
ASMPT emphasises the quality control of all produced modules. Mr Lee, a Production Engineer at ASMPT explains: “We use the Renishaw XL-80 laser calibration system with an RX10 rotary axis calibrator to examine the accuracy of each direct-drive rotary (DDR) motor. The XL-80 complies with international standards and quality assurance. It is calibrated by recognised and traceable systems and methods, giving us confidence in the measured result. Renishaw has also done very well in support. When our XL-80 had been sent out for calibration, Renishaw provided us with a spare system for temporary use to avoid any stoppages in our production.”