Stran trenutno ni na voljo v vašem jeziku. Lahko si ogledate strojni prevod, ustvarjen s storitvijo Google Translate. Te storitve ne zagotavljamo mi in rezultatov prevoda nismo preverili.
Za dodatno pomoč se lahko obrnete na nas.
Transform your manufacturing
Transform your manufacturing performance with help from the process control experts and reap the rewards.
- More throughput from your existing assets
- Increase automation and reduce human intervention
- Reduce rework, concessions and scrap
- Enhance your capability and take on more work
Tackle process variation at source ...
Process variation is the enemy of competitiveness and profitability. It causes waste and inefficiency, leads to high quality costs and manning levels, and results in late deliveries and poor traceability.
The secret to consistent, automated, and productive machining is to understand where variation comes from and how to deal with it at source.
Renishaw's Productive Process Pyramid™ provides a framework within which to identify and control variation in your factory, backed by innovative technology, proven methods and expert support. Renishaw can help bring your goal of 'green button' or 'lights out' machining into reach.
... and reap the rewards
- achieve more throughput from your existing assets
- increase automation and reduce human intervention
- reduce rework, re-makes, concessions and scrap
- shorten manufacturing lead times
- increase your capabilities and traceability
- control your costs and boost your bottom line
The Productive Process Pyramid™
The Productive Process Pyramid™ shows how layers of control can build upon one another to systematically remove variation from the machining process, increasing throughput, maximising conformance and eliminating human error.
The four layers
Explore the four layers to unlock the key to predictable, productive manufacturing.
Process foundation
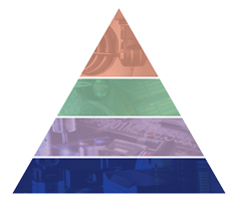
The process foundation layer is about providing a stable environment in which the process is to be performed. This includes optimising and monitoring the performance of the machine itself.
These are preventative controls that reduce the number of sources of variation before machining starts.
Process setting
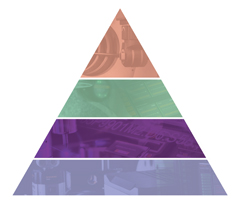
The process setting layer deals with sources of variation such as the location of the part, the size of tools, and offsets on the machine which could otherwise cause non-conforming components.
These are predictive controls that are applied just before cutting starts.
In-process control
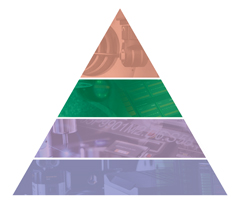
The in-process control layer tackles sources of variation that are inherent to machining, such as tool wear and temperature variation, providing intelligent feedback to the process and decision-making as machining progresses.
These are active controls that are applied during metal cutting.
Post-process monitoring
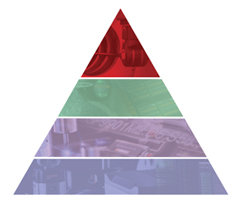
Finally, the post-process monitoring layer concerns checking the process and the finished part against their specifications, as well as logging process routes and outcomes.
These are informative controls applied after machining is complete.
Process control activities
Each layer of the Pyramid comprises a series of controls that together tackle all the sources of machining process variation.
Documents
-
Brošura: Merilno-tehnične rešitve za produktiven nadzor procesov [sl]
Izboljšajte zmogljivost vaše proizvodnje s pomočjo strokovnjakov za nadzor procesov
-
White paper: Survival of the fittest - the process control imperative
In tough times, manufacturers focus on reducing their operating costs, but may not be able to afford to spend their way out by buying more productive machinery. With that pathway closed, what are the opportunities for radically reducing costs without replacing existing machines? This paper explores four areas where substantial savings can be found if firms are prepared to change the way they control their machining processes.