Измерение формы деталей по 5 координатам в аэрокосмической промышленности: решение - измерительный контактный тензодатчик для станков
Компания Triumph специализируется на изготовлении деталей путем штамповки с растяжением и обтяжкой, так что в цеху компании редко бывают детали или штампы, у которых бы не было бы параболической или конической формы или же профиля, описываемого сложной кривой.
Отдел CAD/CAM компании выполнил разработку и усовершенствовал процедуру быстрого и точного измерения результатов обработки таких деталей, не снимая их при этом со станка. Такой подход способствовал реализации принципов рационального производства. Для этого был использован датчик RMP600 с тензоэлементами, который обеспечивает ювелирную точность "прикосновения", необходимое, например, для стабильного и точного измерения диаметров малых отверстий, контуров и контроля допусков на размер. Благодаря устранению лепесткового эффекта (т.е. наличию реальной трехмерной характеристики срабатывания) и повторяемости 0,25 мкм (0,00001 дюйма) этот тензодатчик обеспечивает высокую точность при срабатывании с любого направления. При этом требуется однократное выполнение процедуры калибровки.
Использование датчика RMP600 в сочетании с программным обеспечением OMV Pro компании Renishaw обеспечивает на портальном пятикоординатном фрезерном станке с системой ЧПУ (производства компании Zimmerman) возможности координатно-измерительной машины (КИМ): ведь теперь можно получать со станка детали с результатами измерений, точность которых стандартно выдерживается в пределах 0,025 мм (0,001 дюйма), что подтверждается при повторном контроле на других устройствах. В результате необходимость в проверках на самой КИМ по сути отпала, что принесло компании экономию за счет снижения часов простоя производства, исключения возможных поломок и решения проблем соблюдения точности, возникающих при снятии и повторной установке дорогостоящих деталей.
Компания Triumph Fabrications специализируется на листовой штамповке путем растяжения и обтягивания заготовок различного вида: листа, в том числе тонкого, профилей, полученных выдавливанием, и гнутых профилей, используемых в аэрокосмической промышленности. Усилия прессов компании лежат в диапазоне от 10 до 750 тонн, причем существует возможность вытяжки выворачиванием с использованием горизонтально-гибочных машин (бульдозеров) с усилием 150 и 400 тонн в комбинации с прессами производства компании Cyril Bath. Компания также имеет возможности выполнения операций обтяжки заготовок из разных металлов с формообразованием сложного вида в одной и нескольких плоскостях.
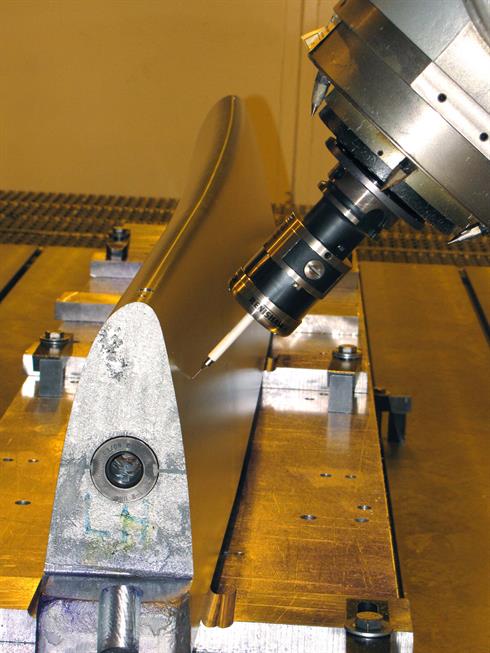
Компания Triumph Fabrications специализируется на листовой штамповке путем растяжения и обтягивания заготовок различного вида: листа, в том числе тонкого, профилей, полученных выдавливанием, и гнутых профилей, используемых в аэрокосмической промышленности. Усилия прессов компании лежат в диапазоне от 10 до 750 тонн, причем существует возможность вытяжки выворачиванием с использованием горизонтально-гибочных машин (бульдозеров) с усилием 150 и 400 тонн в комбинации с прессами производства компании Cyril Bath. Компания также имеет возможности выполнения операций обтяжки заготовок из разных металлов с формообразованием сложного вида в одной и нескольких плоскостях.
Руководитель отдела CAD/CAM Гари Медлок (Gary Medlock) говорит, что выполнение измерений на станках является исключительно важной составляющей для достижения таких целей, как снижение продолжительности цикла, устранение повторной обработки изделий и уменьшение количества ошибок, которые могут появляться в связи с многократным креплением детали. "Мы предпочитаем выполнять измерения сразу же после обработки, вместо того чтобы переносить деталь на КИМ", - сказал он. - Эти детали и так являются дорогими, а при каждой операции на станке Zimmerman их стоимость увеличивается. В случае таких деталей, как фасонный штамп для носка крыла (см. фото), нам пришлось бы или терять почти целый день для демонтажа, измерения и установки детали снова, или полностью закончить обработку детали, а затем выполнять контроль, надеясь на то, что повторная обработка не потребуется. Измерения в процессе обработки позволяют подтвердить на каждом этапе соответствие результатов установленным техническим требованиям до того, как мы будем выполнять дальнейшие операции, увеличивающие стоимость детали".
Обычно детали, обрабатываемые на фрезерном станке Zimmerman, представляют собой штампованные заготовки из листового металла толщиной от 0,635 мм (0,025 дюйма) до 3,18 мм (0,125 дюйма), в которых требуется обработать отверстия и профили. Крепление этих деталей осуществляется с помощью вакуумных зажимных приспособлений. Сверление и рассверливание отверстий диаметром от 2,5 мм (0,098 дюйма) до 9,5 мм (0,375 дюйма) – типичных для конструкций самолетов – выполняется с точностью до 0,05 мм (0,002 дюйма) и с допусками на фактическое положение от 0,30 мм (0,012 дюйма) до 0,71 мм (0,028 дюйма). "Мы измеряем диаметр отверстия и координаты его фактического положения с помощью датчика RMP600, используя щуп из карбида вольфрама или нержавеющей стали с шариком диаметром 1 мм (0,039 дюйма), удлинитель длиной 50 мм (1,97 дюйма) и метод измерения в два касания", - объясняет Медлок. - Мы предпочитаем шарики из карбида вольфрама, так как они позволяют исследовать отверстие на большей глубине. Если следить за правильной ориентацией, то таким шариком можно измерять практически все. 50-миллиметровый удлинитель на датчике RMP600 не приводит к потере точности и позволяет держать датчик на достаточном расстоянии от детали, чтобы свести к минимуму вероятность поломки; заменить этот удлинитель, в случае столкновения, стоит дешевле. Мы пользуемся методом измерений по двум касаниям, поскольку мы выполняем калибровку при той же скорости, которая задана в программе, так что время и углы определены".
Надежность результатов калибровки станков является одним из ключевых факторов успеха компании Triumph. "Если не случается никаких поломок, то мы проводим калибровку станка раз в год, пользуясь лазером и системой ballbar", - сказал Медлок. - Кроме того, у нас на станке имеется маленькая калибровочная сфера, которая калибруется каждую неделю: станок поворачивается на известные углы и выполняется касание сферы датчиком. Результаты отображаются на гистограмме, одновременно с данными за последние два года, поэтому очень легко заметить любую тенденцию. Вдобавок, у нас есть эталон с прослеживаемым соответствием результатов измерений, имеющий различные элементы: конус, сферу, пазы и т.д. Измерение этого эталона мы выполняем каждый раз, когда имеет место изменение какого-либо компонента нашей программы контроля качества".
Компания Triumph работает на двух портальных фрезерных станках Zimmerman. Более новая модель FZ-30 производства 2008 года оборудована системой ЧПУ Siemens 840D. Характеристики этого станка: перемещения по линейным осям X-Y-Z соответственно 6 x 2,8 x 1,5 м (236 x 110 x 59 дюймов), углы поворота головки - 110 градусов по оси A и 360 градусов по оси Z. Максимальная мощность шпинделя 40 кВт, крутящий момент 48 Нм, предельная скорость вращения 25 000 об/мин. Сам завод является термоконстантным. "Объемная точность этого станка составляет 0,1 мм (0,004 дюйма), и для крупногабаритного, интенсивно используемого станка эта величина весьма хорошо соответствует точности типичной КИМ", - объясняет Медлок.
Одним из важнейших преимуществ датчика RMP600 оказалось то, что, пользуясь щупом с шариком диаметром 1 мм, мы можем измерять фактический диаметр очень маленьких отверстий, вплоть до 2,5 мм (0,098 дюйма)".
Triumph Fabrications (Великобритания)
"Без датчика нам пришлось бы переносить детали в цех для КИМ, измерять их, приносить обратно и снова устанавливать на станок", - говорит Медлок. - Нам нужно было бы добавить контрольную канавку или найти какой-то еще способ, который позволял бы гарантировать, что каждая установка идентична всем параметрам самой первой установки. А это означает увеличение стоимости детали, не говоря уже о потерянном дне для проведения полного цикла проверки.
Такого рода задержки, а также погрешности, которые накапливаются с каждой новой установкой, являются совершенно неприемлемыми, если мы хотим работать с минимальными затратами. В среднем наш цикл измерений датчиком требует примерно столько же времени, сколько цикл обработки. Это, однако, очень приблизительное усреднение: контроль некоторых деталей можно выполнять намного быстрее, это зависит от количество элементов. Например, среднее значение при проверке отверстий составляет по 8 секунд на каждое".
Другой ключевой составляющей успеха компании Triumph является программирование модели и геометрии. "Для того чтобы все работало, как нужно, на детали должны присутствовать все элементы", - подчеркивает Медлок. - Обычно мы начинаем с файла STEP, импортируемого в пакет OMV Pro для создания программы измерений вне станка. В программном пакете выполняется моделирование измерительной подпрограммы с целью выявления столкновений, при этом используется функция "автоориентации", что позволяет выполнять автоматическое выставление датчика в нужное положение для измерений, не требуя ввода нужного угла вручную. Элементы могут измеряться разными способами: например, отверстие может измеряться как окружность и как цилиндр".
После этого измерительная подпрограмма выполняется в системе ЧПУ для сбора данных измерений; эти данные анализируются затем вне станка в пакете OMV с применением алгоритмов, аналогичных тем, которые используются для КИМ. В программном пакете выполняется сравнение данных измерений с файлом, содержащим массив данных модели, и выдаются отчеты в числовом и графическом виде. В этих отчетах указываются отклонения от номинальных значений, и выводится график, отображающий диапазон отклонений.
Пользуясь "мастером" контроля размеров и допусков (geometric dimensioning and tolerancing - GD&T) в пакете OMV, программисты создают стандартизированные элементы отчетов с использованием признаваемых на международном уровне символов; это позволяет сравнивать результаты измерений на станке с технологическими чертежами. "В настоящее время мы используем такие параметры, как перпендикулярность, точность углов, контур поверхности и фактическое положение", - добавляет Медлок.
В отличие от традиционного датчика для станков датчик RMP600 с тензоэлементами не требует выполнения калибровки по каждому направлению, что позволяет существенно экономить время при наличии 5 координат. "Мы обязательно измеряем по всем направлениям, поскольку речь идет о случае с 5 координатами", - объясняет Медлок. - Благодаря системе срабатывания на основе тензоэлемента в датчике RMP600 мы получаем хороший результат - т.е. такое же показание - независимо от того, с какой стороны выполняется касание щупом, а это идеально подходит для случая 5 координат. При выполнении измерений по 5 осям датчик используется иногда с необычной ориентацией, и касание шарика может происходить с любого направления. Мы убедились в том, что при измерениях с датчиком RMP600 его показания идентичны, если приходится выполнять измерения еще раз. Одним из важнейших преимуществ датчика RMP600 оказалось то, что, пользуясь щупом с шариком диаметром 1 мм, мы можем измерять фактический диаметр очень маленьких отверстий, вплоть до 2,5 мм (0,098 дюйма)".Фундаментальное отличие датчика RMP600 от традиционных контактных датчиков для станков состоит в том, что используемый в нем запатентованный механизм считывания RENGAGE™ позволяет устранить лепестковый эффект - ошибку, присущую всем традиционным датчикам для станков. Если же лепестковый эффект настолько значителен, что он влияет на точность измерений, то пользователи таких датчиков должны компенсировать это влияние путем калибровки датчика по каждому направлению измерений. Это требует сложного цикла калибровки и учета многочисленных смещений датчика.
В датчике RMP600 все эти проблемы устранены. Тензодатчики измеряют усилие, приложенное к щупу в точке контакта, и формируют импульс срабатывания в тот момент, когда деформация превышает пороговое значение. Результат: более низкие усилия срабатывания, меньший изгиб щупа, субмикронная повторяемость (0,25 мкм 2σ), отсутствие лепесткового эффекта и реальная трехмерная характеристика срабатывания. Датчик RMP600 обеспечивает существенно более высокую точность измерений, особенно на трехмерных поверхностях, где существует множество направлений срабатывания, а также при наладке, когда векторы подхода к заготовке могут быть неизвестны. Логическая схема внутри датчика обеспечивает исключение нештатных срабатываний вследствие удара или вибрации путем определения того, является ли деформация, регистрируемая датчиком, результатом контакта с поверхностью детали или же представляет собой случайное событие.
"Исключительно важно иметь в виду, что в конечном счете точность датчика определяется точностью станка", - подчеркнул Медлок. "Зная характеристики данного станка, его состояние и историю калибровок, мы считаем, что измерения на этом станке равносильны выполнению контроля на КИМ. Проверка и калибровка данного станка выполняется, по сути, с соблюдением тех же требований, которые существуют для наших КИМ, так что на станке легко достижима точность контура деталей 0,38 мм (0,015 дюйма). Точность наших метрологических измерений мы можем проверить путем измерения известного эталона, имеющего все те элементы, которые могут встречаться в наших деталях. В связи с тем, что данный станок имеет высокую точность и является пятикоординатным, датчик с тензоэлементом оказался наиболее подходящим для соблюдения наших требований к измерениям. Выполняемые периодически повторные проверки на других измерительных устройствах редко выявляют отклонения, превышающие тысячную долю дюйма, что обеспечивает нам высокую степень уверенности в результатах и эффективность эксплуатации".