PAL Robotics integrates magnetic encoder technology into robots to achieve balance
This case study focuses on REEM-C, PAL Robotics' full-size biped humanoid robotics research platform. It is one of a family of robots that are used for many applications. REEM-C provides a fully customisable basis for research into exciting areas such as navigation, machine vision, human-robot interaction, artificial intelligence, grasping, walking and speech recognition.
Background
Imagine a world where robot companions improve your productivity at work, carry your bags at the airport or even provide assistive living to the elderly. This is the reality that PAL Robotics SL in Barcelona, Spain, hope to create. Located in the heart of Barcelona's technology district and only a short walk from the world-famous Las Ramblas promenade, this innovative company is pioneering the development of such robots.
The design, programming and assembly of the robots all take place in PAL Robotics' bustling Barcelona offices where a team of engineers work to constantly advance the capabilities of their robots.
Challenge
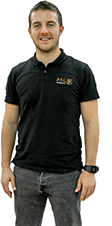
Luca Marchionni (pictured left), Chief Technology Officer at PAL Robotics, notes that one of the most difficult challenges is maintaining balance while walking, which humans take for granted.
Walking involves the generation and execution of trajectories for many degrees of freedom simultaneously while the feet interact with the environment. The control system of a biped robot has to deal with transitions between two phases: the double support, with both feet on the ground and the single support when only one foot is planted.
PAL Robotics (Spain)
Designing control laws to enable this is difficult due to the non-linearities associated with robot dynamics. Often, this cannot be done analytically and is too complex to accomplish by mere trial and error. Instead, a numerical approach is applied called trajectory optimisation, where an ‘ideal path' of the robot is prescribed and a numerical method calculates the best possible approximation to this path, where the criterion for ‘best' is determined by a specially chosen cost-function which accounts for both the ideal path and the physical limitations of the robot.
There are strict space and weight constraints in the design of joints for humanoid robots to keep robot volumes and inertias as low as possible; many of PAL Robotics' robots are human-sized and exhibit up to 40 degrees of freedom.
Solution
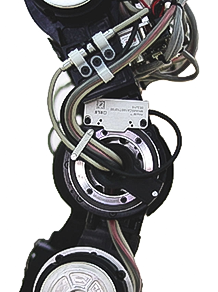
REEM-C and other humanoid robots from PAL Robotics have fully articulated joints capable of performing a range of complex movements depending on the task. High-quality encoder feedback is required for the servo-control of each joint in terms of applied torque, velocity and position.
Renishaw advised PAL Robotics on encoder selection for each application and leveraged a deep understanding of their business needs and products. Non-contact magnetic encoders by Renishaw associate company RLS were chosen as the solution. These included rotary encoders such as AksIM™ and Orbis™ which are integrated into knee (pictured left), wrist and elbow joints and the component-level incremental RoLin™ system.
The relationship with Renishaw has been really good. What we like most is the wide range of options and the ability to customise every component. RLS encoders have many configurations - it is possible to choose from many different communications protocols, sensor sizes, and interfaces. The more parameters for us the better, as every time we want to make robots that are lighter, more compact and more capable.
PAL Robotics (Spain)
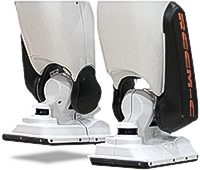
For balance control, a feedback-force system at each robot's foot is implemented to calculate the zero-moment point (ZMP), a metric that can be used to assess the stability of robots like REEM-C. The measured ZMP is then fed into a ‘fuzzy logic' PD controller to track the desired ZMP, achieving balance and disturbance rejection. The controller's goal is to adjust the robot's centre of mass (CoM) position to always maintain the ZMP point inside of the support region (under the feet). Successful biped dynamic walking requires precise control of the legs' joint angles in terms of position, velocity and acceleration via rotary encoder feedback.
Results
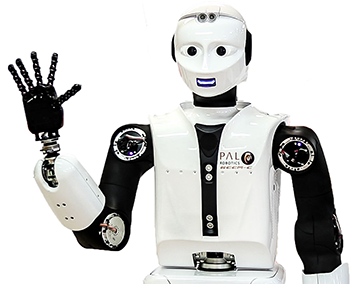
Balance control is particularly vital for stable biped locomotion and encoder outputs enable the estimation of robot posture and the generation of position, speed and acceleration references that every joint should follow.
Magnetic encoders provide PAL Robotics with a flexible position measurement solution and are capable of meeting stringent space and performance requirements. The selected encoders have an impressive range of capabilities enabling significant design freedom. Balance control is achieved by controlling the instantaneous torque acting on each joint, which enables correct positioning of each robot limb for stable walking motion. High encoder accuracy ensures that errors in the control signal are minimised, thereby enabling the controller to quickly adjust robot positions to always maintain the ZMP within the support region of the feet.
About PAL Robotics
PAL Robotics designs and manufactures highly advanced humanoids and service robots for a multitude of applications. The company was founded in 2004 by six engineers with a dream. PAL Robotics' first robot was called REEM-A and was born out of a project for a robotic arm to play chess. Since then, there have been regular additions to the PAL Robotics product portfolio, and it now offers 6 different robot models including TIAGO, which is designed to assist people in domestic and industrial environments. Another robot, TALOS, has been designed to work on production lines to perform tasks like tightening screws in difficult-to-reach places and assisting workers with heavy tools handling.
For more information about PAL Robotics visit www.pal-robotics.com
About RLS
RLS d.o.o is a Renishaw associate company. RLS produce a range of robust magnetic rotary and linear motion sensors for applications such as industrial automation, metalworking, textiles, packaging, electronic chip / board production, robotics and more.
For more information about RLS visit www.rls.si