Интеллектуальные производственные решения позволяют вдвое сократить время производства компонентов турбины
Компания Doncasters Precision Castings – Deritend является ведущим производителем лопаток газовых турбин. Лопатки изготавливаются из высоколегированных сплавов на основе никеля и кобальта методом литья по выплавляемым моделям и механической обработкой.
Компания стремится к неуклонному росту и подкрепляет это стремление готовностью инвестировать в постоянную оптимизацию процессов за счет бережливого производства и быстрого прототипирования. В результате компания смогла значительно увеличить спрос на свои услуги механической обработки, которые дополняют инвестиционную стратегию компании. В ответ на спрос были сделаны значительные инвестиции — более 2 миллионов фунтов стерлингов — в станки Mazak, инфраструктуру и специализированное программное обеспечение, что позволило эффективно обрабатывать более 14 новых изделий.
Предыстория
До инвестирования в пятикоординатные обрабатывающие центры Mazak подобные операции производили на традиционных трехкоординатных обрабатывающих центрах с использованием специальных установочных приспособлений. Технологические процессы не только отнимали много времени, но и предъявляли высочайшие требования к квалификации операторов станка. Продолжительность цикла изготовления типового сопла — с учетом наладки и механической обработки — составляла четыре часа, и имевшиеся производственные мощности просто не позволяли удовлетворить возросший спрос. Кроме того, инженеры рассматривали специальные установочные приспособления как устаревшее и экономически неэффективное решение. По этим причинам было принято решение сделать крупную инвестицию в технологию механической обработки, и были заказаны три вертикальных обрабатывающих центра Mazak VORTEX i-630V/6. Предполагалось, что эти станки позволят Doncasters производить весь объем механической обработки без привлечения субподрядчиков и стать единственным поставщиком для своих клиентов.
В рамках инвестирования для станков были закуплены высокоточные датчики Renishaw RMP600, основанные на запатентованной тензометрической технологии RENGAGE™. Они идеально подходят для выполняемой работы благодаря недостижимой для конкурентов точности: погрешность при измерении сложных трехмерных элементов и контуров измеряется в долях микрометра. Стоит отметить, что в ходе первоначальных обсуждений эксплуатационных вопросов специалисты компании пришли к выводу, что им потребуется дополнительная поддержка, и Renishaw привлекла к работе своего партнера, компанию Metrology software products ltd (MSP).
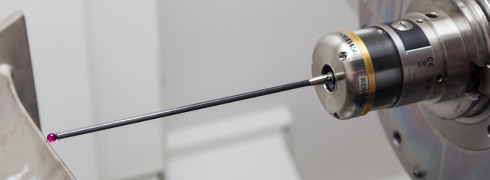
Задача
Задача заключалась в том, чтобы максимально повысить процент изначально годных и не требующих доработки деталей. При этом необходимо было устранить любую возможность появления брака и увеличить общую производительность. Олли Макроу (Ollie Macrow), технический директор Doncasters, пояснил: «Когда ставишь на металлообрабатывающий станок отливку из высоколегированного сплава стоимостью тысячи фунтов, хочется быть уверенным в том, что деталь получится годной. Не менее важны и другие затраты: в дополнение к стоимости самой отливки есть еще затраты времени и — учитывая материал — довольно значительные затраты на оснастку. Более того, некоторые детали вообще не подлежат доработке, и если какой-то допуск нарушен, то это - неисправимый брак. Мы понимали, что выполнять контактные измерения детали все равно придется, но мы хотели обойтись при этом без специальных приспособлений». Учитывая весьма небольшой опыт компании в выполнении контактных измерений — который, фактически, ограничивался лишь простой регулировкой и базированием на плоскости, — вклад Renishaw сложно переоценить.
Более того, в Doncasters хотели избавиться от дорогих, значительно увеличивающих затраты времени специальных установочных приспособлений. «Установочные приспособления приносят множество проблем: они дороги, они требуют высокой квалификации для правильного базирования деталей, и, если приспособление повреждается, приходится останавливать обработку, поскольку уже не получится добиться нужного положения заготовки. Вот почему приспособления приходится очень качественно обслуживать, а это тоже время и деньги. Мы хотели заменить эти приспособления на упрощенные модульные системы и свести к минимуму участие оператора в процессе наладки», — добавил Олли. Разумеется, производственный план тоже необходимо было выполнять. поэтому сокращение времени на наладку стало одним из основных доводов в пользу станков Mazak. Несмотря на то, что большую часть механической обработки компания производила на новых станках своими силами, некоторые вспомогательные операции все равно приходилось отдавать субподрядчикам. В будущем планируется отказаться и от оставшихся субподрядов за счет повышения производительности. «Это решение положительно скажется на нашей производительности. Если мы сможем выполнять всю механическую обработку сами, то нам не придется терять по два дня на транспортирование заготовок», — объяснил Олли.
Я действительно считаю, что мы не смогли бы успешно обрабатывать отливки без помощи Renishaw и MSP. Они оказывают нам прекрасную поддержку, они всегда на связи и готовы прибыть на объект тогда, когда нам нужно».
Doncasters Precision Castings – Deritend (Великобритания)
Действия по устранению
Изучив проект, технический специалист Renishaw пришел к выводу, что лучшим решением задач Doncasters является сочетание программного обеспечения NC-PerfectPart и NC-Checker от MSP с датчиком RMP600. Это сочетание оборудования и инновационного программного обеспечения позволяет выявлять погрешности базирования заготовки и позиционирования рабочих органов станка до начала обработки. Первым этапом является «изучение» станка и сбор исходных данных для сравнения. NC-Checker проверяет характеристики датчика перед контролем станка по всем пяти осям. При таком подходе оператор будет устанавливать заготовку и выполнять обработку, точно зная, что каждый параметр, влияющий на качество контактного измерения и металлообработки, находится в пределах допуска. Проверку станка можно выполнять регулярно: она занимает всего несколько минут. В долгосрочной перспективе она гарантирует, что станок будет работать в пределах заданных параметров и изготавливать годные детали.
NC-PerfectPart решает проблему, связанную с низкой точностью базирования заготовки на станке. Это особенно важно, если детали имеют произвольные формы и геометрически сложные элементы или требуют обработки по пяти осям. Установка таких деталей отнимает много времени, и бывает очень сложно добиться точности и повторяемости. Эту проблему можно решить контактным измерением заготовки с помощью датчика RMP600 и программой, сгенерированной из CAD-файла соответствующей детали.
По результатам этого первоначального измерения можно получить параметры компенсации погрешностей базирования заготовки на станке. Затем параметры компенсации загружаются в систему ЧПУ станка, происходит автоматический расчет величин компенсации и генерирование управляющей программы, идеально соответствующей конкретной детали. Наладка автоматизирована, а это значит, что установочные операции уже не играют особо важной роли в технологическом процессе. Происходит компенсация погрешностей ручного базирования, поэтому затраты времени на базирование даже самых сложных заготовок снижаются до нескольких минут.
Более того, на начальном этапе обработки можно учесть такие факторы, как состояние материала, наличие систем для загрузки паллет и температуру, что позволит дополнительно снизить риск появления брака.
По завершении обработки металла NC-PerfectPart может проверить точность обработанной детали до снятия со станка и контроля на координатно-измерительной машине.
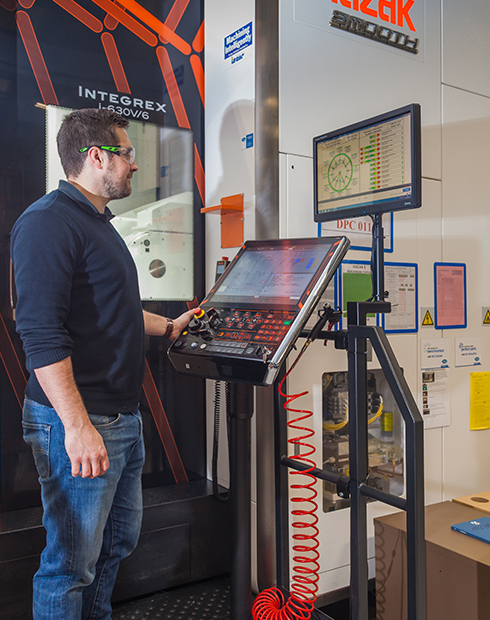
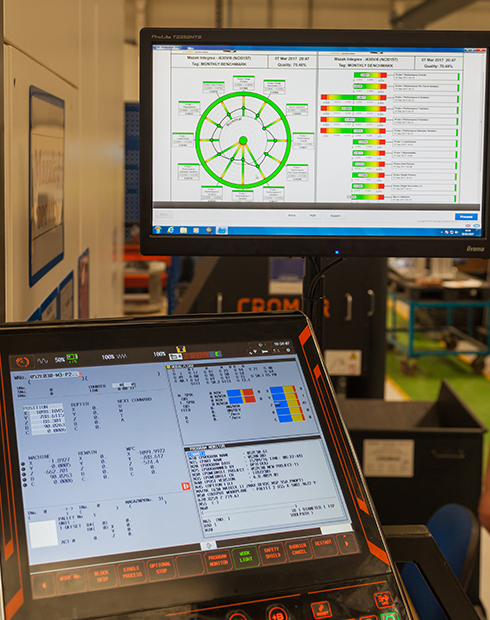
Результаты
До внедрения RMP600 и ПО MSP на установку и обработку типового сопла промышленной газовой турбины уходило четыре часа. Теперь для контактного измерения, обработки и контроля той же детали требуется менее двух часов. Другими словами, производительность Doncasters повысилась на 50%. Обработка более сложных деталей занимала до восьми часов и требовала присутствия высококвалифицированного оператора для контроля процесса обработки. Теперь на обработку таких деталей уходят те же два часа, что и на простых, поэтому экономия еще ощутимее. При помощи Renishaw и MSP компания Doncasters улучшила системы базирования и добилась впечатляющих общих результатов; также была улучшена корреляция результатов контроля на станке, результатов контроля на КИМ и данных системы сканирования Bluelight.
Комментируя успех, Олли Макроу подчеркнул: «Случившееся действительно стало положительным опытом для нас. Мы ни за что бы не смогли и приблизиться к этому результату без поддержки Renishaw и MSP».
Он продолжил: «Когда мы решили приобрести станки, то собрались с представителями Mazak и спросили: "Как же нам этого добиться?" Они ответили, что в рамках нашей текущей модели производства это невозможно, но затем появились Renishaw и MSP и предложили решение, которое нам было нужно. Мы смогли резко увеличить процент изначально годных деталей, и теперь получаем положительные отзывы от клиентов. Я действительно считаю, что мы не смогли бы успешно обрабатывать отливки без помощи Renishaw и MSP. Они оказывают нам прекрасную поддержку, они всегда на связи и готовы прибыть на объект тогда, когда нам нужно».