Переработка конструкции распределительного коллектора под аддитивное производство
Технология аддитивного производства (АП) прекрасно подходит для проектирования и изготовления коллекторов, поскольку она позволяет формировать внутренние элементы и каналы.
Компания Renishaw в сотрудничестве с заказчиком переработала текущую конструкцию распределительного коллектора с учетом возможностей аддитивного производства. Основной целью проекта было снижение массы компонента без ущерба для его прочности. Не менее важно и то, что аддитивное производство дарит большую свободу при проектировании и, соответственно, возможности оптимизировать каналы для движения среды.
Что представляет себя распределительный коллектор?
Распределительный коллектор направляет поток среды в гидравлической системе и связывает трубопроводную арматуру, насосы и приводы. Именно он позволяет конструктору обеспечивать работу гидравлического контура и объединять все компоненты в одном компактном узле.
Традиционная технология изготовления распределительных коллекторов
Традиционно распределительные коллекторы изготавливают из заготовки из алюминиевого сплава или нержавеющей стали. Заготовку обрезают и обрабатывают до нужного размера, а затем формируют каналы сверлением. В связи со сложностью операций сверления зачастую возникает необходимость в специализированной оснастке. Для правильного направления потока по системе в каналы необходимо устанавливать заглушки.
Подобный производственный процесс по своей сути приводит к тому, что каналы содержат резкие повороты, которые могут привести к разделению потока и/или образованию застойных зон, которые значительно снижают эффективность.
Коллекторы из алюминиевого сплава в целом дешевле из-за меньшей стоимости и лучшей обрабатываемости материала. Однако они менее стойки к абразивному износу, поэтому присутствие в текучей среде твердых примесей приведет к истиранию поверхностей и ускоренному износу. По этой причине в некоторых случаях предпочтительнее использовать коллекторы из нержавеющей стали, но она плотнее и тверже алюминия, и изделие получается значительно тяжелее и дороже.
Преимущества технологии АП в проектировании и производстве гидравлических коллекторов
- Оптимизированные каналы для повышения эффективности компонентов.
- Возможность в полном объеме использовать вычислительную гидродинамику в процессе проектирования.
Снижение требуемого количества станочной оснастки. - Минимальная необходимость в съемных опорных конструкциях.
- Возможность значительного снижения массы.
- Отсутствие необходимости в отверстиях для демонтажа коллектора.
- Полная свобода конструктивных решений позволяет значительно уменьшить габариты узла.
Прямая выгода для заказчика
- Снижение массы на величину до 79%.
- Цельная конструкция, меньший риск брака.
- Малая продолжительность стадий проектирования и разработки.
- Совместимость с существующей конструкцией.
- Повышение пропускной способности на величину до 60%.
Переработка конструкции под АП: объем работ
Аддитивное производство значительно расширяет спектр возможных конструктивных решений, поэтому геометрию компонента можно адаптировать под АП со снижением массы и повышением функциональности без увеличения габаритных размеров. Заказчик предусмотрел в задании для Renishaw определенные конструктивные и функциональные требования, которые приходилось учитывать при переработке конструкции компонента.
Геометрия
- Определенные соединительные элементы.
- Внутренний диаметр каналов.
- Толщина стенки каналов.
- Точки крепления и стыки.
Функциональные требования
Основным требованием заказчика было снижение массы без ущерба для жесткости и функциональности. Конструкторы Renishaw также внесли в объем переработки конструкции под АП задачу повышения эффективности каналов в системе.
Первая стадия проектирования
Первым этапом был анализ детали для выявления тех каналов, которые непосредственно обеспечивают функциональность распределительного коллектора. Пути движения среды исходной конструкции с перекрестным сверлением были смоделированы в CAD-системе (системе автоматизированного проектирования). Все каналы, не нужные для протекания среды, были удалены; осталась только необходимая сеть каналов.
Затем каждый гидравлический контур был уменьшен и упрощен в программе SOLIDWORKS Flow Simulation. Эта работа стала частью подготовки к точному гидродинамическому анализу.
Анализ позволил выявить зоны разделения потока и зоны застоя. Следующим этапом стала оптимизация путей движения среды.
Затем была вычислена толщина стенки. В данном случае мы руководствовались требованием заказчика, но в качестве альтернативы на этом этапе можно было выполнить моделирование с расчетом напряжений методом конечных элементов (МКЭ) с учетом величин давления, полученных в результате гидродинамического анализа.
Наконец, было выполнено проектирование постоянных опорных конструкций; их добавили к геометрии CAD, и получился устойчивый и эффективный узел. В целом опорные конструкции добавляют в конечную геометрию на этапе последующей обработки конструкции компонента, чтобы привязать объект к плите основания и рассеять тепло. Однако если сделать опоры единым целым с компонентом, можно избежать потенциальной потери материала, связанной со съемными опорными конструкциями или креплениями.
На первой стадии проектирования удалось уменьшить объем на 52% по сравнению с исходным блочным коллектором и повысить пропускную способность на величину до 60%.
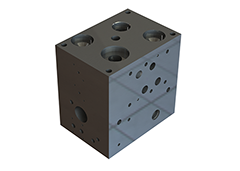
Исходный распределительный коллектор. Каналы получены сверлением и пересекаются; для направления потока некоторые из них заглушены.
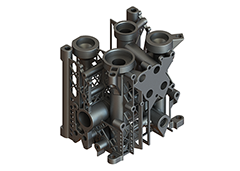
Геометрия после первой стадии проектирования. Пути движения среды выявлены и оптимизированы. Стенки имеют заданную толщину. Опорные конструкции служат для фиксации каналов и соединения точек крепления.
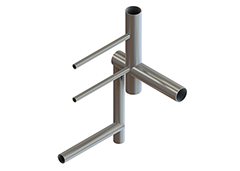
Часть выявленного пути движения среды; хорошо видны резкие повороты
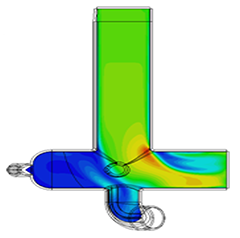
Пример гидродинамического анализа; видны зоны нарушения потока
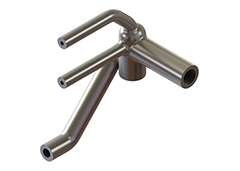
Часть пути движения среды, разработанного по результатам гидродинамического анализа. Резкие смены направления устранены для оптимизации потока
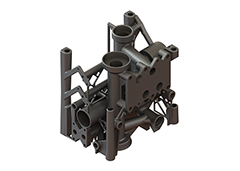
Геометрия после второй стадии проектирования. Отверстия для демонтажа коллектора были удалены. Опорная конструкция была переработана для повышения прочности и жесткости
Вторая стадия проектирования
Первая стадия проектирования прошла на предприятии Renishaw. Результат был представлен заказчику, который оценил новую геометрию коллектора с точки зрения функциональности. Исходный коллектор предназначен для использования по модульной схеме, когда несколько узлов устанавливают последовательно. Отдельные распределительные коллекторы необходимо будет периодически демонтировать с линии для обслуживания. Для этого в конструкции предусматривают резьбовые отверстия для демонтажа.
В геометрии коллектора для АП после первой стадии имеются элементы, которые инженер может использовать для демонтажа коллектора вручную без инструментов. Поэтому необходимость в отверстиях для демонтажа коллектора исчезла. Поскольку удаление этих отверстий с CAD-модели нарушило сложную сеть самонесущих конструкций, инженеры получили возможность доработать конструкцию.
Было высказано предположение, что во время механической обработки коллектора с геометрией, полученной на 1 стадии, могут возникнуть упругие деформации, скручивание и/или вибрация из-за уменьшенного объема материала по сравнению с цельным корпусом. В результате доработки была получена окончательная конструкция коллектора, которая не только отличалась повышенной жесткостью, но и составляла всего 21% объема исходной конструкции.
Столь значительное снижение объема дало возможность изготовить коллектор стадии 2 из более подходящего материала — нержавеющей стали 316L. В результате общая масса снизилась на 37% даже несмотря на то, что применялся материал большей плотности (плотность нержавеющей стали составляет 8 г/см3, а плотность алюминиевого сплава — менее 3 г/см3).
Общие результаты
Этап проектирования | Материал | Объем (см3) | Масса (кг) |
Исходный распределительный коллектор | Алюминиевый сплав | 9600 | 25,6 |
Конструкция для АП, 1я стадия | Алюминиевый сплав | 4650 (-52%) | 12,3 |
Конструкция для АП, 2я стадия | Нержавеющая сталь 316L | 2040 (-79%) | 16,3 |
Работа с Renishaw
В Renishaw понимают, что для изготовления максимально качественных узлов и деталей по технологии аддитивного производства (АП) пользователь должен понять, что проектирование под АП отличается большей свободой по сравнению с проектированием под традиционные технологии производства, например механическую обработку с удалением припуска и литье. Мы обеспечиваем обучение и проектирование для поддержки технологических процессов даже после покупки системы АП.
Глобальные центры разработки решений являются прекрасной отправной точкой для компаний, рассматривающих возможность интеграции АП в свои производственные процессы.
Центры разработки решений компании Renishaw обеспечивают надежные среды разработки, в которых пользователь может приобрести дополнительные знания и уверенность при использовании технологии аддитивного производства. Они оборудованы современными системами АП и укомплектованы грамотным инженерным персоналом, что позволит быстро развертывать технологию с фиксированными, прогнозируемыми затратами.
Подробнее
Чтобы узнать о том, какую пользу могут принести вам центры разработки решений для аддитивного производства, обратитесь в местное представительство компании Renishaw.