Additive manufacturing technology
Feature articles
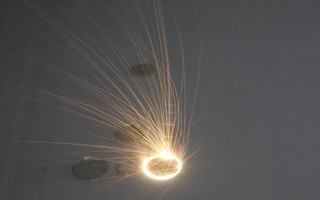
New optical schemes for selective laser melting systems provide more consistent control of laser processing conditions. Dynamic beam focusing offers new possibilities for tighter focus control across the build plate and in varying thermal conditions.
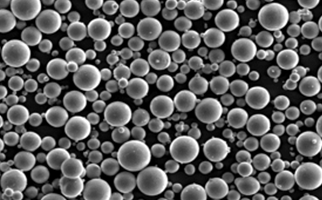
Any production process is only as reliable as the feedstock that it consumes. For additive manufacturing (AM) using metal laser melting, the properties of the powder and the machine parameters that are used to process it are closely related.
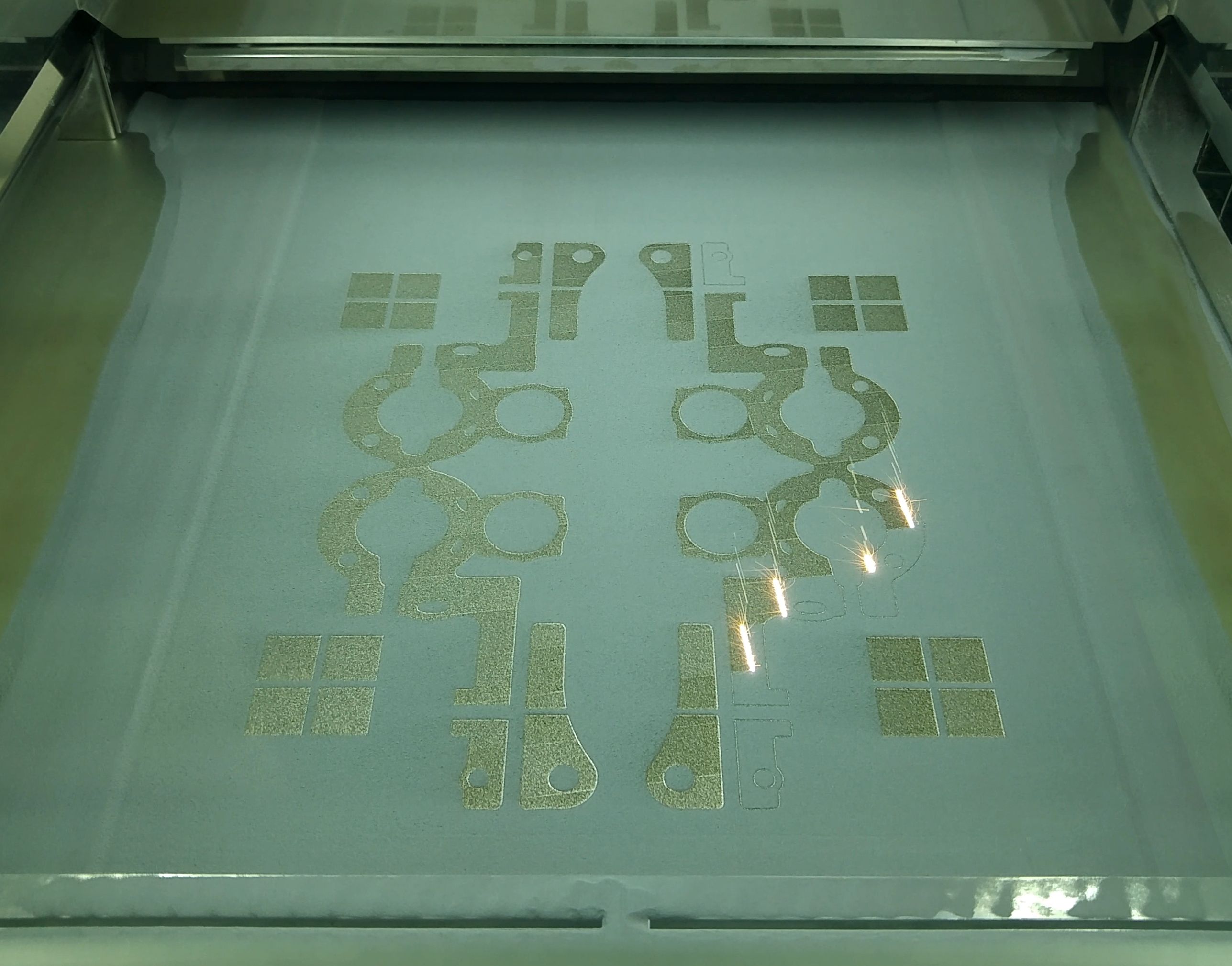
Production-orientated laser powder bed fusion (LPBF) machines increasingly feature multiple lasers to boost build rates. Overlapping fields of view enable these lasers to operate independently on separate parts, or to cooperate on single large components. Such flexible use of multiple lasers in close proximity to one another raises productivity and lowers part costs.
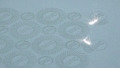
Additive manufacturing (AM) gives us the freedom to build a vast range of part geometries, consolidating multiple conventional parts into a complex whole. Multi-functional AM parts often combine the structural with the intricate, mixing relatively bulky geometries with fine details. Building such parts cost-effectively means that our AM process must be both productive and precise.
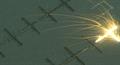
This article looks at the factors that drive the selection of Laser powder bed fusion (LPBF) processing parameters, and how these define an ‘operating window’ in which we must work. We will also look at the sensitivity of the process to changes in part geometry that may drive us towards application-specific parameter choices.
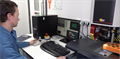
Multi-laser additive manufacturing (AM) is reducing the cost of AM components, making more applications viable for series production. By adopting flexible build strategies in which several lasers work together, they enable faster build rates than single-laser machines. But it is vital that higher productivity is accompanied by high and consistent quality, so that AM components are suitable for long operating lives in demanding applications.