Ta strona nie jest obecnie dostępna w Twoim języku. Możesz zapoznać się z tłumaczeniem automatycznym, korzystając z usługi Google Translate. Nie jesteśmy odpowiedzialni za świadczenie tej usługi, ani też wyniki tłumaczenia nie były przez nas sprawdzane.
Jeżeli chciałbyś uzyskać więcej pomocy skontaktuj się z nami.
Where information really counts, fibre-optic broadband cables are fed underground with the help of Renishaw’s rugged encoders
With many countries moving to high-speed, fibre-optic broadband, there is a significant challenge to replace the mass of existing underground cables quickly and easily. The replacement of cables is made part icularly challenging by the fragility of individual glass fibre strands and of the sheathed fibre-bundles, which cannot be simply pushed or pulled into ducts. Renishaw's magnetic encoders help to provide a rugged solution to this extensive problem.
One telecommunications company has found that when threading a fibre-bundle into a sealed duct, air blown at high pressure provides a lubricating effect and also helps to propel the cable along. The result is that far less force is required to thread the bundle, considerably reducing the risk of damage to the fibres and potentially making the broadband upgrading process quicker, easier and safer.
UK-based Factair Ltd, an expert in air compressor systems, won the contract to manufacture the patented, field-based ‘fibre-blowing' machine. This machine uses caterpillar tracks to thread the fibre-optic bundle quickly into the duct, whilst introducing compressed air in order to ‘drag' the bundle along.
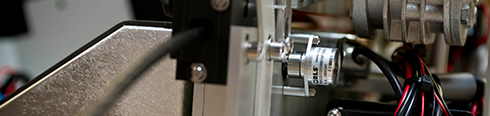
The rugged RM22 is perfect for these harsh environments as its body is machined from tough aluminium alloy and the magnetic actuator is enclosed in stainless steel to provide dirt immunity to IP68. These non-contact magnetic encoders, produced by Renishaw's partner company RLS d.o.o., use Hall-effect sensor technology where the rotation of the magnetic actuator is sensed by a custom encoder chip within a separate body, and processed to give the required output format. Seals are not needed as the encoder is immune to liquids, oils and dirty environments.
With a non-contact body of just 22 mm in diameter and speed capability to 30,000 rpm, the RM22 is frictionless, thus increasing durability, endurance and long-term reliability. Nitzan Gonen confirms, “We're very satisfied with the Renishaw encoders. They're built to work reliably at far higher speeds than we apply, and in far worse conditions than these machines will typically encounter.”
Nitzan Gonen concludes, “With the fibre-blowing machine the distance that engineers can feed the cable without damaging the sheath or fibres has increased, from perhaps a few tens of metres, to thousands of metres. We can now insert 4 km of cable from a single point, 2 km in each direction, at a rate of up to 60 m/min.”
Two Renishaw non-contact RM22 magnetic encoders are incorporated to detect slippage that would damage the surface of the sheath; with one monitoring the rate at which the bundle is threaded into the machine, and the other monitoring the rate at which the caterpillar belts are moving. The fibre-blowing machine's control unit counts the pulses from both encoders and if the difference in count rate (speed) is outside the tolerance setting, it interprets the difference as slip and reduces the speed of the motors. The motor is also ‘capped' to limit the push force if the cable's progress in the duct is hindered. This additional safeguard also prevents motor burnout should the bundle encounter an obstruction.
Nitzan Gonen, Factair's Design and Development Director, explains, “It was important to use non-contact encoders because the fibre-bundles are un-spooled on-site from large drums, which can be wet and dirty if the weather and local conditions are poor. A non-contact unit means it's more reliable and each encoder is expected to last indefinitely. A full-contact encoder would probably need to be replaced often.”
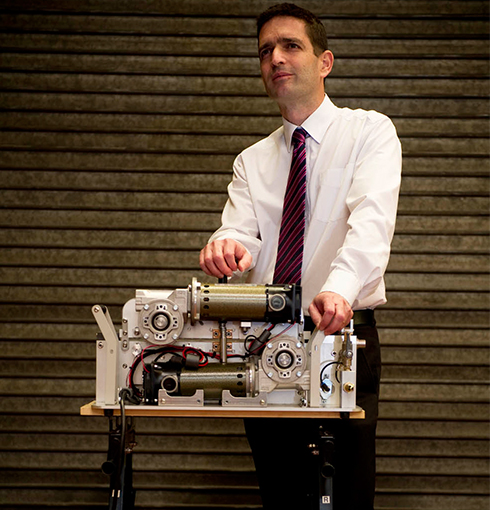