Gniazdo do toczenia na twardo z kontrolą procesu zwróciło się w zaledwie 18 dni.
Programowalne sprawdziany Equator umożliwiły stworzenie w pełni zautomatyzowanego stanowiska do precyzyjnej obróbki łożysk i sortowania części.
Conroe (stan Texas, Stany Zjednoczone) – W Conroe Machine robimy to, o czym inni producenci mogą tylko pomarzyć – całodobowe toczenie na twardo rodziny części na bezobsługowym stanowisku z automatycznym sterowaniem. Zastosowano w nim robota FANUC z uniwersalnym sprawdzianem Equator wraz z oprogramowaniem EZ-IO firmy Renishaw w celu zapewnienia wszechstronnych funkcji komunikacyjnych, 100-procentowej kontroli części oraz automatycznej kompensacji parametrów dwuwrzecionowej obrabiarki Okuma 2SP-250. Na stanowisku odbywa się także pakowanie części w pudełka i układanie gotowego produktu na paletach. Zdaniem firmy stanowisko do toczenia zwróciło się w zdumiewający sposób w ciągu 18 dni.
Firma Conroe to dowód na to, że każdy zakład, który chce wykorzystać umiejętności inżynierów automatyków, może używać nowej technologii w postaci programowalnego sprawdzianu Equator firmy Renishaw. Oprogramowaniem i samym programowaniem zajęli się programista maszyn CNC James Wardell i technik ds. robotów Jeff Buck. Ten sam zespół automatyków zdecydował się na utworzenie w pełni zautomatyzowanego gniazda do pomiarów i sortowania części. Tym razem członkowie zespołu połączyli dwa sprawdziany Equator, robota FANUC oraz system optyczny i kilka linii przenośnika niskoprofilowego. W obu zastosowaniach system Equator demonstruje moc programowanego rozwiązania do pomiarów porównawczych, umożliwiając ekonomiczny i szybki pomiar rodziny bieżni łożysk, i to bez mocowania ani problemów związanych ze środowiskiem hali produkcyjnej.
Conroe Machine to względnie młoda firma założona przez Murraya „Tippy” Touchette'a w 2000 roku, z zamiarem produkowania części przy użyciu najlepszej, dostępnej technologii. Firma szybko rozrosła się i zatrudnia ok. 150 pracowników, którzy pracują w zakładzie produkcyjnym o kontrolowanej temperaturze i powierzchni 6000 metrów kwadratowych. Choć profil firmy Conroe ma charakteru ogólny, jej położenie w pobliżu Houston pozwala na nawiązanie współpracy z wieloma firmami z sektora wydobycia ropy naftowej i gazu i produkcję podzespołów do urządzeń wydobywczych. Jednym ze stałych zleceń firmy jest produkcja bieżni łożysk oporowych do pomp płuczkowych. Firma produkuje tysiące tych podzespołów przez całą dobą w cyklu tygodniowym.
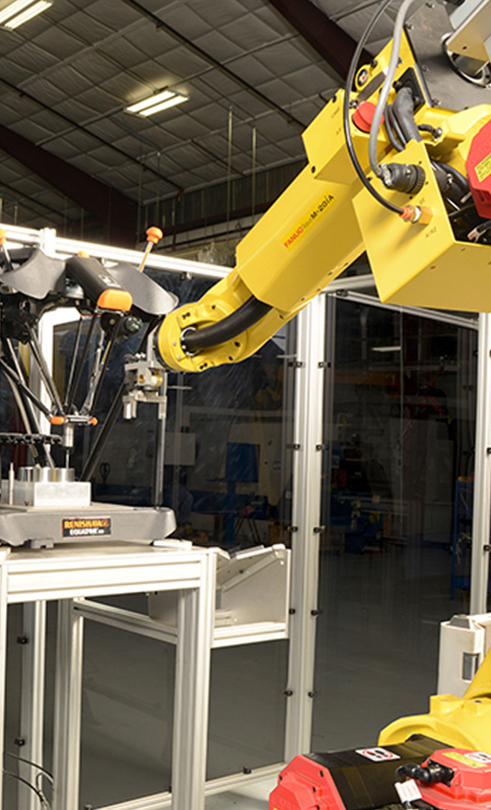
Podniesienie poprzeczki automatyzacji
Obróbka zgrubna łożysk odbywa się aktualnie na czterech tokarkach Puma firmy Doosan. Początkowo obróbka zgrubna i wykańczająca odbywały się na tych samych tokarkach obsługiwanych przez czterech operatorów. Maszyny podzielono aktualnie na dwa gniazda, które są ładowane i rozładowywane przez roboty FANUC; odbywa się w nich jedynie obróbka zgrubna. Są to jedne z wcześniej zautomatyzowanych gniazd w firmie. Na wpół gotowe są wysyłane do hartowania do twardości HRC 65 na głębokość 1,7 mm przed toczeniem wykańczającym.
„Wydajność naszej produkcji w tych dwóch gniazdach wynosiła 800–1000 części na dzień, co oznacza 400–500 na gniazdo”, wyjaśnia James Wardell. „Jeden operator ładował części do maszyn i kontrolował je. Poprawna kontrola tak dużej liczby części zależała jednak od operatora, a my chcieliśmy zwiększyć wydajność.”
Dlaczego wybrano system Equator?
„Naszym kolejnym krokiem będzie w pełni zautomatyzowany proces obróbki wykańczającej: z automatycznym ładowaniem części, pomiarem po obróbce, automatyczną kompensacją narzędzi, grawerowaniem części oraz pakowaniem ich w pudełka i układaniem na paletach”, dodaje. „Mamy dobre pomysły na opracowanie takiego systemu, z wyjątkiem części odpowiedzialnej za kontrolę jakości i moduł wprowadzający korekty offsetów narzędzi. Inspekcja musi odbywać się szybko i nadążać za czasem cyklu produkcji części, który wynosi 98 sekund. Początkowo szukaliśmy systemu pomiarowego z białym laserem ze względu na jego szybkość, ale nasze części za bardzo odbijały światło. Interesowaliśmy się też dedykowanymi sprawdzianami oraz warsztatowymi maszynami współrzędnościowymi. Komparatory sprzętowe są bardzo drogie i wymagają konfigurowania, zaś maszyny współrzędnościowe nie są szybkie. Gdy współpracowaliśmy z firmą Renishaw w ramach innych projektów, menedżer regionalny Sheila Schermerhorn przedstawiła nam system Equator jako możliwe rozwiązanie.”
W wypadku naszego gniazda obróbkowego żadne inne narzędzie pomiarowe nie było tak opłacalne jak Equator.
Conroe Machine (Stany Zjednoczone)
Narzędzia i oprogramowanie do kontroli procesu
Equator to ekonomiczna i uniwersalna alternatywa dla dedykowanych sprawdzianów produkcyjnych. Do pomiaru wykorzystuje metodę porównania. Przedmiot wzorcowy o znanych wymiarach zmierzonych na maszynie współrzędnościowej służy do „zerowania” systemu Equator, a wszystkie kolejne pomiary są porównywane z tym przedmiotem wzorcowym. Bezpośrednio po porównaniu z przedmiotem wzorcowym gwarantuje się powtarzalność rzędu 0,002 mm. W celu skompensowania zmian temperatury można w dowolnym momencie wykonać ponowne zmierzyć przedmiot wzorcowy w systemie Equator. W systemie Equator zastosowano sondę SP25 do zbierania punktów metodą stykową, możliwość skanowania umożliwia analizę do 1000 punktów na sekundę. Trzpienie pomiarowe są przechowywane w sześcioportowym magazynie wymiany, a system programuje się z poziomu programu MODUS™ Equator. System Equator można obsługiwać ręcznie przy użyciu przycisków, ale w naszej aplikacji został on przystosowany do zintegrowania z systemami automatyki firmy Conroe za pomocą oprogramowanie EZ-IO.
„Na początku 2012 roku byliśmy na dniach otwartych centrum Hartwig i widzieliśmy system Equator w akcji, wraz z podwójną, dwuwrzecionową tokarką bramową Okuma”, mówi Wardell. „Poza gotowością do automatyzacji produkcji części naszego typu, dwutorowy układ sterowania OSP tokarki bazuje na systemie Windows® i ma otwartą architekturę komputera PC, która jest ważnym czynnikiem naszych planów rozwoju własnego oprogramowania do automatycznej kompensacji”.
System Equator w zautomatyzowanym gnieździe produkcyjnym
Panowie Wardell i Buck zdecydowali się na instalację gniazda produkcyjnego, w skład którego wchodzi maszyna Okuma 2SP-250H, jeden system Equator, maszyna do grawerowania oraz 6-osiowy robot FANUC M20iA. Podwójne karuzele są ładowane nieobrobionymi przedmiotami (ok. 300 sztuk). Podwójne ładowarki bramowe ładują wrzeciona i umieszczają gotowe przedmioty w rynnie prowadzącej do przenośnika, skąd są pobierane przez robota. Robot umieszcza przedmiot do kontroli w systemie Equator; jeśli jest dobry, przenosi go do maszyny do grawerowania, a na koniec układa w pudełkach i na paletach.
„Opracowaliśmy własne oprogramowanie do kompensacji narzędzi, które jest uruchomione w sterowniku OSP”, dodaje Wardell. „W tym oprogramowaniu wykorzystuje się wyniki kontroli z systemu Equator — przesyłane w postaci pliku CSV — do obliczenia offsetu narzędzi, gdy przedmiot jest poza granicami tolerancji”. W trakcie obróbki usuwa się ok. 0,38 mm materiału z każdej strony przedmiotu, przy najwęższej tolerancji równej 0,025 mm oraz chropowatości powierzchni 0,5 mikrometra. Średnica zewnętrzna przedmiotów waha się od trzech od sześciu cali. „System Equator z łatwością kontroluje przedmioty w zakresie tolerancji z dużym marginesem”, mówi Wardell.
Kontrola procesów produkcyjnych
„Utrzymujemy średnicę zewnętrzną i wewnętrzną, mając odchyłkę promienia na poziomie ok. 5 mikrometrów. Części są zestawiane w partie według rozmiaru, dlatego też zminimalizowano wymiany szczęk uchwytów i innego oprzyrządowania. Dzięki szybkości systemu Equator nadążamy za procesem. Ponowne porównanie z przedmiotem wzorcowym wykonujemy tylko raz dziennie, ponieważ w hali produkcyjnej utrzymujemy temperaturę 22,2°C.
Zasady inspekcji oraz uniwersalność dzięki automatyzacji
Metoda pomiaru części jest zaskakująco prosta. „Wykonaliśmy blok aluminiowy z centralnym otworem, który umieściliśmy na środku płyty bazowej sprawdzianu Equator”, wyjaśnia Wardell. „Używamy tego do wyznaczenia środka i ustawienia układu współrzędnych. Każdy przedmiot jest umieszczany na środku tego bloku. Wykonujemy pomiar stykowy w celu określenia środka części, a następnie poprzez skanowanie wykonywana jest kontrola pozostałych cech. Zaplanowaliśmy proces pomiarowy bez wymiany mocowania przedmiotu ani trzpienia pomiarowego. Dzięki oprogramowaniu automatyzacji EZ-IO w systemie Equator robot wybiera program pomiarowy, który ma być zastosowany do wykonania kontroli. Znamy krytyczne elementy, które musimy zmierzyć, aby mieć pewność, że przedmiot jest w zakresie tolerancji.”
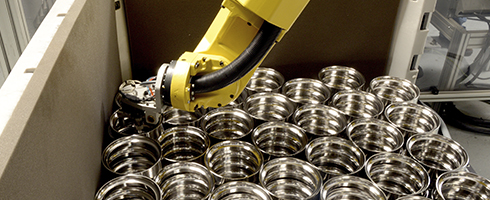
Pomiar/sortowanie użytych przedmiotów
Gniazdo do toczenia na twardo produkuje aktualnie 600–700 gotowych części na dzień. Dlatego potrzebne jest tylko jedno gniazdo, w porównaniu do dwóch używanych poprzednio. Jako kontynuację poprzednich prac opracowano projekt gniazda do sortowania części dla klienta. Na podstawie szkicu zaprojektowanego przez Touchette'a Wardell i Buck opracowali gniazdo do pomiaru i sortowania używanych bieżni łożysk oporowych do pomp płuczkowych.
Używane silniki pomp płuczkowych demontuje się w warsztatach terenowych, naprawia i przekazuje z powrotem do eksploatacji. „Dokonywano oględzin bieżni i oceniano, czy nadają się do ponownego użytku; klient był świadomy, że niektóre dobre części są wyrzucane, a to oznaczało marnowanie pieniędzy” mówi Wardell. „Chcieliśmy zapewnić im bezobsługowy system do pomiaru i sortowania, w którym wyeliminowano kontrolę dokonywaną przez człowieka, dzięki czemu można było odzyskać więcej bieżni”.
W trakcie pisania tego artykułu system był nadal w trakcie opracowywania. Buck i Wardell montują gniazdo, które składa się z dwóch systemów Equator, 6-osiowego robota FANUC LRMate 200iC, kilku linii niskoprofilowego przenośnika, systemu optycznego FANUC iR Vision oraz szybkiej zmieniarki narzędzi ATI dla siłowników końcowych robota. System optyczny przekazuje do systemu Equator numer części, na podstawie którego odbywa się wybór programu pomiarowego do uruchomienia. Dobre części są kolejno umieszczane na właściwym przenośniku, a złe części na przenośniku braków.
„System zaprojektowaliśmy tak, aby go załadować w całości na ciężarówkę, a jego obsługa była prosta dla personelu warsztatu — wystarczy włączyć zasilanie i ładować części na przenośnik”, mówi Buck.
„W wypadku naszego gniazda produkcyjnego żadne inne narzędzie pomiarowe nie było tak opłacalne jak Equator”, dodaje Wardell. „Mamy nadzieję, że przygotowanie systemu integracji gniazda dla naszego klienta otwiera dla całej naszej firmy nową ścieżkę działalności.”