Ta strona nie jest obecnie dostępna w Twoim języku. Możesz zapoznać się z tłumaczeniem automatycznym, korzystając z usługi Google Translate. Nie jesteśmy odpowiedzialni za świadczenie tej usługi, ani też wyniki tłumaczenia nie były przez nas sprawdzane.
Jeżeli chciałbyś uzyskać więcej pomocy skontaktuj się z nami.
FORTiS™ enclosed encoder enhances grinding precision and performance
After testing and evaluation, TGT selected Renishaw's FORTiS™ enclosed encoders for its latest series of tool grinding machines. The ease of installation and other leading-edge features of the FORTiS encoder system enable TGT to optimise its machines' performance.
Background
The machining accuracy of a CNC machine tool is affected by many factors, including machine mechanics, control electronics, machine rigidity, thermal stability and the geometric accuracy of the cutting tool.
Small cutting tools require precision grinding to ensure accurate tool geometries. Precision tool grinding is a machining-based production process that uses abrasives to obtain the required geometry and dimensional tolerances for a cutting tool.
Demand in India for precision machining has hugely increased, such that India's machine tool market is now one of the fastest growing in the world. To seize this opportunity and meet the increasing demand, India-based company, Tool Grinding Technologies Inc. (TGT), has developed a range of precision tool grinding machines equipped with linear motors and Renishaw's FORTiS enclosed absolute position encoders, which help to improve machining accuracy and process stability.
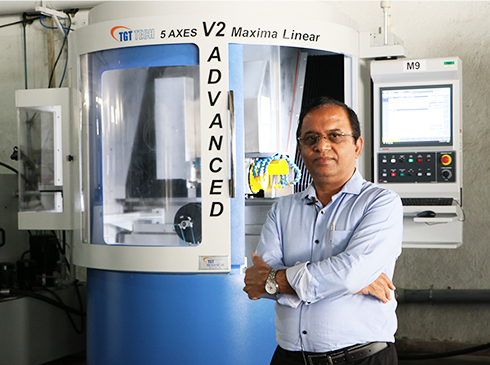
Mr Ranganatha, Director of Tool Grinding Technologies Inc.
Challenge
Linear motor technology has matured in recent years and has become important in industrial applications. Modern linear motor designs have achieved significant improvements in heat dissipation, thrust and cost. Automation systems and CNC machines, such as precision grinding machines, increasingly use linear motors in place of traditional ball screws. The precision and accuracy of a linear motor servo is heavily influenced by the quality of the linear position feedback from the encoder. Sub-Divisional Error (the measurement error within one signal period) is a critical specification for smooth velocity control, which, as tool grinding machine manufacturers know, is important for surface finish quality. Low positional jitter allows optimisation of servo loop gain.
CNC profile grinding employs small, incremental linear movements of the tool grinder's axes to produce the interpolated trajectory; therefore, accurate motion control is vital.
The working environment of a tool grinding machine is harsh and includes machining vibrations, and contaminants such as cooling fluid and grinding swarf. Vibrations in the machine can coincide with the natural resonant frequencies of position encoders. Therefore, positioning accuracy is improved if the encoder has the ability to damp resonant vibrations to prevent high-amplitude disturbances from entering the position control loop. In these cases, encoders with tuned-mass damping can significantly enhance CNC machine performance.
Mr Ranganatha, one of TGT's Directors, explained: “In the past, TGT's grinding machines used ball screws. To further improve the accuracy and to sustain this accuracy long-term, we decided to employ linear motors in our newest models. There are many technical aspects to the design. Issues that needed to be addressed included environmental protection of the linear motors, encoder installation, shock resistance, maintenance, and servicing requirements.”
Solution
The linear motors in TGT's latest models of tool grinder require linear position feedback from a suitable enclosed linear encoder designed for harsh environments. As a long-time customer of Renishaw, TGT collaborated with Renishaw engineers in testing and evaluating the FORTiS encoder.
The FORTiS enclosed encoder design is built upon industry proven RESOLUTE™ absolute encoder technology and provides high resistance to the ingress of liquids and solid debris contaminants. FORTiS encoders also feature integrated, specially-designed tuned mass dampers that not only deliver class-leading 30 g vibration resistance, but also ensure that vibrations at the encoder's natural frequency are strongly damped; thereby, considerably reducing the risk of disturbances to the servo control loop.
“We have had good experience of using Renishaw products over many years, such as the LP2 probe system and the RESOLUTE absolute encoder for direct-drive rotary tables, and the performance has been very good.” said Mr Ranganatha. “When Renishaw recommended the FORTiS enclosed optical encoder for our new grinding machines, the necessary testing and evaluation work was carried out without hesitation,” he continued.
As one of the leading tool grinder manufacturers in India, TGT has pioneered the introduction of precision tool grinders with linear motors in recent years.
FORTiS™ enclosed encoder inside TGT's tool grinding machine
V2 ADVANCED Maxima
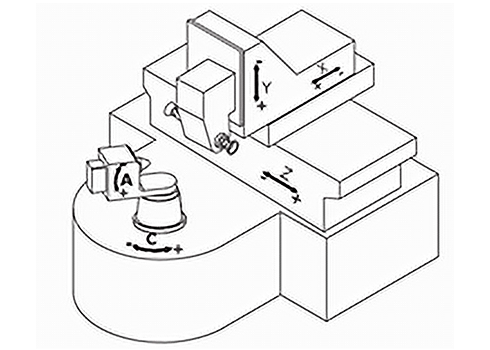
Schematic of TGT's V2 ADVANCED Maxima grinding machine
In 2021, TGT launched the V2 ADVANCED Maxima - a five-axis high precision tool grinding machine comprising three linear axes (X, Y and Z) and two rotary axes (A and C).
Tubular linear motors are employed on the crosswise X-axis and the longitudinal Z-axis of this machine with strokes of 300 mm and 680 mm, respectively. Both axes are equipped with the FORTiS-S™ enclosed encoder system, which is the standard-sized variant of the FORTiS encoder.
The vertical Y-axis is equipped with a ball screw system as standard, but customers can also choose a linear motor-driven axis with a FORTiS-S encoder if required. The rotary A-axis is mounted on the rotary C-axis and both axes control the orientation of the workpiece using direct drive motors, equipped with the RESOLUTE absolute rotary encoder, to reduce backlash.
Both the RESOLUTE and FORTiS-S encoders output BISS-C serial comms for direct interface with a Beckhoff controller. During processing, the A-axis rotates the workpiece, which is clamped on the workpiece spindle, while the linear axes (X, Y and Z) control the position of the grinding wheel.
This tool grinder is also equipped with Renishaw's LP2 series probe system for workpiece set-up prior to grinding. In the early stages of product development, TGT tested a range of FORTiS-S enclosed absolute encoders with resolutions from 10 nm down to 1 nm. To achieve the best overall machine performance, TGT selected the FORTiS-S encoder with a resolution of 1 nm.
Microma Auto
Schematic of TGT's Microma Auto grinding machine
The Microma Auto is a cylindrical grinding machine used for the preparation of cutting tool blanks such as regular drills, endmills and profile tools, and comprises four linear axes (X, Y, Z and V).
Prior to machining, the tool blank is clamped by a collet on the workpiece spindle and identified by the LP2 probe system. During processing, the workpiece rotates within a V-shaped holding tool (V-block), which is mounted on the V-axis, while being driven along the longitudinal X-axis, which is the feed axis. As the workpiece enters the grinding station, it is fed between two grinding wheels (roughing and finishing wheels) that are driven along the Y and Z axes, respectively, and are perpendicular to each other. One advantage of the Microma Auto is that the whole process is completed in a single pass.
A kinematic feature of this machine is that the workpiece spindle axis (X-axis) and the V-block axis (V-axis) are on the same linear motor guideway but driven by separate linear servo motors.
The X-axis and V-axis slides are attached to separate FORTiS encoder readheads but use the same enclosed absolute scale of the FORTiS dual-readhead system. The readheads feedback the X-axis position of the workpiece and V-axis position of the V-block, each with a resolution of 10 nm, to the controller. In this case, the FORTiS encoder enables a positioning accuracy of 3 µm on an axis with 150 mm of travel.
One of the major advantages of using the FORTiS dual-readhead enclosed encoder is that it simplifies the mechanical arrangement of the machine, which saves space and reduces cost. “One benefit of choosing the FORTiS dual-readhead linear encoder is that it enables faster and simpler encoder installation and servicing,” said Mr Ranganatha.
FORTiS optical enclosed encoders have an innovative non-contact mechanical design that eliminates components such as bearings, springs and guidance carriages. This design minimises wear and greatly reduces the risk of breakage during maintenance and servicing, thereby extending the life of the system.
FORTiS encoder readheads are equipped with Renishaw's patented set-up LED, and carefully designed installation accessories to ensure intuitive and right-first-time installation that is substantially faster than more conventional systems, even in restricted locations.
For enhanced functionality, installers can connect the Advanced Diagnostic Tool, ADTa-100, via a standard USB connector, to a PC running Renishaw's ADT View software. This provides a user-friendly graphical interface of advanced diagnostic information, including key encoder performance parameters such as signal strength along the axis length.
TGT technicians use the ADTa-100 hardware to connect the FORTiS encoder to the ADT View software interface during the machine assembly process. This software provides a snapshot of the real-time signal strength at different positions along a machine axis such that the technician knows where to make fine adjustments and can even enable calibration of the FORTiS encoder with the machine powered down.
Results
FORTiS encoders are quick and easy to install, which has helped TGT to save manufacturing and servicing time.
Mr Ranganatha explained, “The installation of the FORTiS enclosed encoder is very simple, which has greatly improved our productivity. Using the ADTa-100 tool and after receiving the appropriate Renishaw training, our engineers can complete a single-axis installation in only 15 minutes. If only the readhead LED were to be used, I believe the speed would be even faster. The LED allows us to quickly determine the status of the encoder, improving diagnostic accuracy when the machine is faulty.”
“Renishaw's professional team often talks with us about our technology. The FORTiS enclosed encoder can be specified with many options for axis length, position resolution, and serial communication protocols, which give us much greater freedom in machine design,” said Mr Ranganatha.
“Although we are using the FORTiS encoder for the first time, we have great confidence in its design. Our latest grinding machines have been equipped with the FORTiS encoder and are now entering mass-production. We are very optimistic about the future development of grinding machines. In recent years, we have benefited from a boom in India's domestic automotive and aerospace industries where there is a huge demand for cutting tools. We have also seen more and more competitors enter the market as the demand for grinding machines has grown. In the future, TGT will focus on optimising its machines' performance,” concludes Mr Ranganatha.

TGT V2 ADVANCED Maxima Linear grinding machine