Additive manufacturing applications
Feature articles
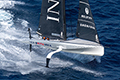
Renishaw is an official technical partner of the British sailing team, INEOS Britannia. The team has employed additive manufacturing to reduce the carbon footprint associated with race yacht manufacturing.
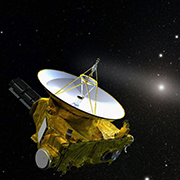
Marc Gardon spoke to the team at aerospace design and manufacturing expert, CiTD, to discuss AM's potential for space applications.
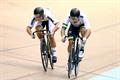
Bastion Advanced Engineering and Design (BAED) have unveiled a new and innovative line-up of products targeted at further improving the performance and competitiveness of athletes on the track.
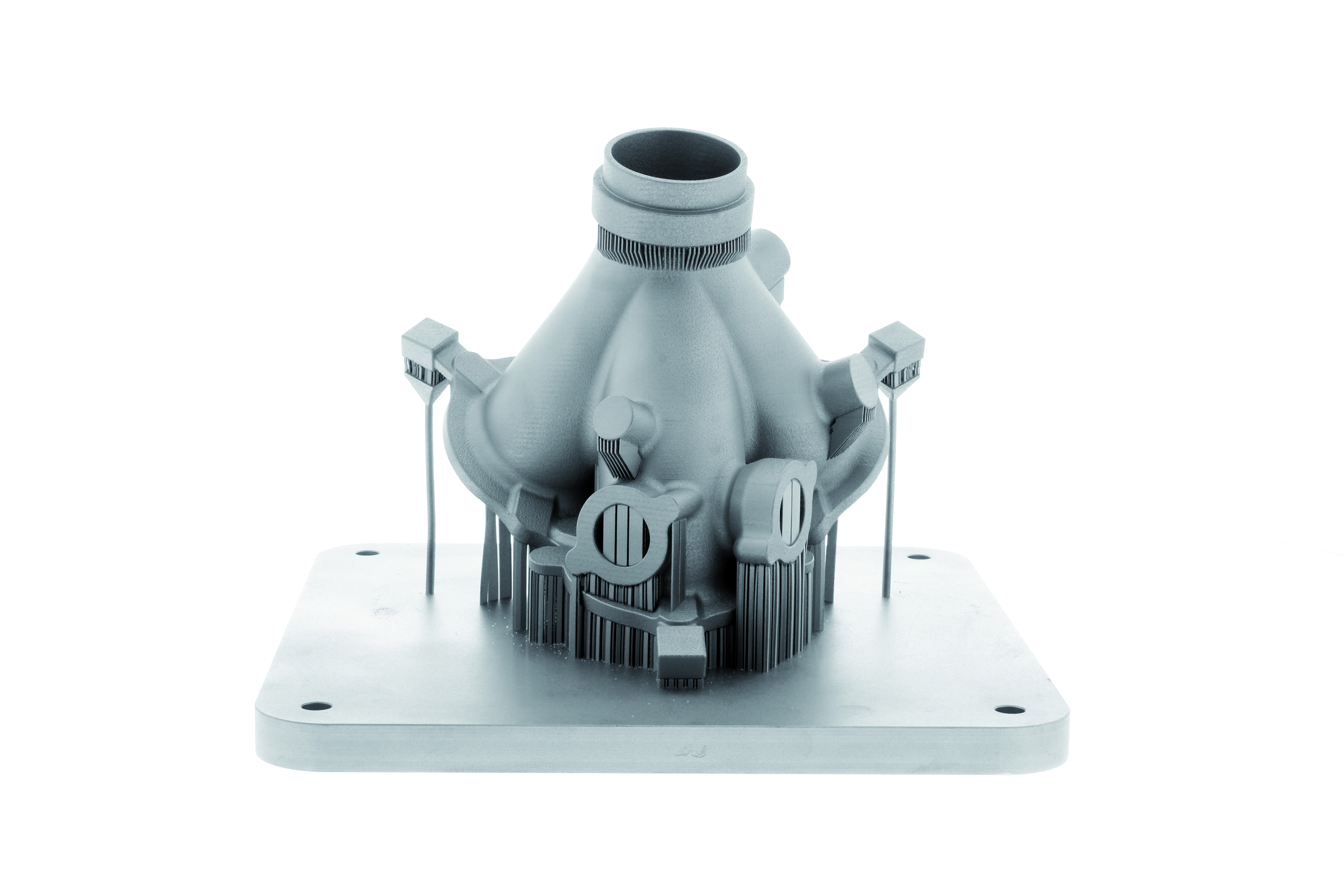
Metal additive manufacturing is quickly becoming the technology of the future, but few people know the full extent of the opportunities it offers or the nature of the partnership - in this industry - between Renishaw and Scuderia Ferrari.
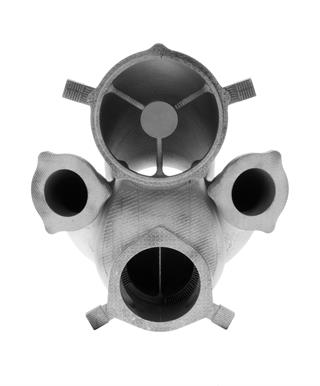
Ferrari is a legend, the most loved Italian brand in the world, and at the heart of this myth, their racing department, have two Renishaw additive manufacturing (AM) machines.
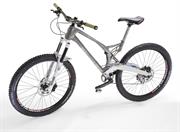
Demand for high specification bicycles has exploded in recent years as both professionals and 'prosumers' have sought a performance edge. In the case of mountain bikes, this has driven manufacturers to deploy advanced materials and construction techniques from aerospace and Formula 1.
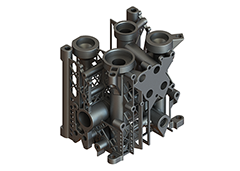
Renishaw has collaborated with a customer to redesign their current hydraulic block manifold with additive manufacturing in mind. The main goal of the project was to reduce the mass of the component whilst retaining its robustness. Due to the increased design freedom associated with additive manufacturing, an opportunity to increase the efficiency of the flow paths was also identified.

AM gives mould designers the freedom to create tools with complex internal cooling channels, which can be designed to maximise heat transfer to produce a rapid and uniform cooling effect. This leads to production cost savings in terms of cycle time, reduced scrap and longer mould life, and also to improved product quality.
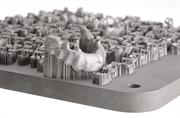
Too often 'design for AM' is about finding ways to build products that really haven't been designed for AM at all. This means that it is often necessary to add support structures to the part in order for it to build successfully, rather than reducing or eliminating the need for supports by considering the AM process constraints early in the part design phase. With sufficient thought, applied early, the quality and consistency of the part is improved and is fully controlled as part of the design process, not as an afterthought.
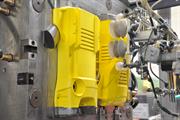
Injection moulding allows plastic products to be produced in complex and intricate detail, often in sizeable production runs. In this article, I look at how these techniques have been applied by leading cleaning systems provider Alfred Kärcher GmbH & Co. KG to boost production of one of their best-selling pressure washers.
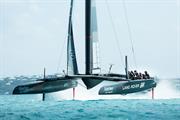
Land Rover BAR understood the potential of additive manufacturing to save weight and improve the efficiency of its hydraulic system. Put simply, this allowed the boat's designers to create a perfect balance between the performance of the hydraulic system and the energy required to run it. This in turn helps the grinders conserve energy whilst still allowing the boat to perform at the optimal level.