Renishaw riduce i tempi di lavorazione delle giranti nel settore aerospace
Honeywell Aerospace è una realtà che fa parte del colosso dell’ingegneria Honeywell e si occupa della produzione di giranti e blisk che vengono installati in moltissimi aerei di linea.
Le giranti sono in pratica dei compressori radiali e assiali. Per la loro lavorazione è richiesto un riferimento che deve rimanere costante durante l'intero processo per garantirne l'idoneità.
In caso di scostamenti del punto di riferimento, la girante viene considerata incompatibile e viene scartata o sottoposta a rilavorazione.
Per assicurare l'accuratezza del processo di lavorazione, Honeywell si è rivolta a Renishaw, azienda leader del settore, e ha acquistato un sistema di ispezione RMP600 ad elevata accuratezza abbinandolo al software Productivity+™ per centri di lavoro. Grazie a queste tecnologie, Honeywell è ora in grado di effettuare importanti misure prima dell’inizio della lavorazione, rilevando immediatamente eventuali scostamenti assiali.
Background
Le giranti vengono prodotte in varie dimensioni, con diametri che variano da 14 a 17 pollici. Nella maggior parte dei casi i pezzi sono prodotti in titanio, ad eccezione di un modello che è invece prodotto in alluminio.
La fabbrica di Chihuahua rifornisce la struttura di assemblaggio Honeywell di Phoenix, Arizona, in cui vengono montate e testate le turbine degli aerei.
Se il riferimento di un pezzo finito risulta fuori centro, la girante viene analizzata da un progettista per valutare se sia utilizzabile o meno.
Nella sede Honeywell, questi tempi produttivi sono spalmati su un periodo di due settimane. Se dopo la lavorazione il pezzo risulta fuori centro, le analisi possono rubare un'ulteriore settimana di tempo e causare ritardi e periodi di inattività, con un impatto fortemente negativo sui tempi e sui costi di produzione.
La sfida
Lo scostamento assiale del punto centrale di origine può essere causato da un'impostazione non corretta, dovuta a un errore dell'operatore, all'uso di fissaggi danneggiati e/o alla presenza di scorie lasciate da una lavorazione precedente.
Soluzione
Al termine del primo ciclo di produzione delle giranti, Luis Adrian Gallegos, Manufacturing Engineer di Honeywell iniziò a prendere in esame, insieme al responsabile della qualità, possibili soluzioni per ridurre i disallineamenti.
"Dopo il primo ciclo, era evidente la necessità di migliorare il processo di lavorazione," ha spiegato Gallegos. "Tuttavia, volevamo evitare investimenti troppo costosi." "Abbiamo contattato Renishaw per discutere della possibilità di utilizzare una sonda a contatto compatta e accurata insieme al loro software, al fine di misurare i pezzi e rilevare eventuali disallineamenti, correggendoli prima della lavorazione.
Dopo aver preso in considerazione varie opzioni, abbiamo deciso di acquistare una sonda a mandrino RMP600 con trasmissione radio. Tale strumento ci assicurava tutti i vantaggi derivanti da un'impostazione automatica dei lavori e consentiva di misurare la geometria di pezzi 3D complessi, come le nostre giranti".
Durante il processo, la sonda Renishaw tocca il pezzo in diversi punti per verificare che non vi siano errori o disallineamenti.
"La sonda ci aiuta a rilevare eventuali inaccuratezze prima che possano trasformarsi in errori", ha continuato Gallegos. "In precedenza non avevamo modo di identificare un problema se non dopo 16 ore di lavorazione e un'ora di misure. Ora invece, se il pezzo non è corretto, riceviamo avvisi tempestivi e possiamo correggere il problema senza sprecare tempo e risorse".
"Oltre all'investimento per la sonda, Honeywell ha scelto di acquistare il software di ispezione Productivity+ per i suoi centri di lavoro. Productivity+ mette a disposizione un ambiente di programmazione molto intuitivo che permette di combinare i cicli di ispezione con la possibilità di inserire funzioni decisionali in‑process. Il software ha contribuito a semplificare le operazioni di impostazione e verifica dei componenti e risulta utile in alcune fasi importanti del processo di lavorazione come l’impostazione dei processi e l’identificazione dei pezzi e degli utensili. Inoltre, Productivity+ consente di arricchire i report post-process con informazioni importanti sui processi, aiutando a prendere decisioni strategiche in relazione alle operazioni e ai processi successivi", ha commentato Barriga.
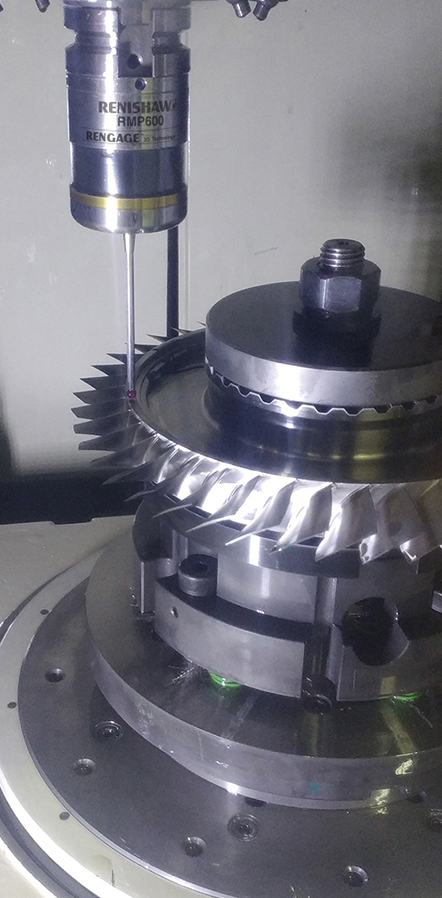
Grazie alla sonda e al software Renishaw, i processi di lavorazione di Honeywell vengono eseguiti senza imprevisti. Prima di implementare la nuova tecnologia, l'operatore doveva inserire il pezzo, impostare il calibro e definire il diametro e le superfici. Se uno solo di questi dati veniva dimenticato o era immesso in modo scorretto oppure se il fissaggio era danneggiato, il pezzo finito era da buttare. Ora possiamo individuare in anticipo i difetti e risolverli prima della lavorazione.
Honeywell Aerospace (Messico)
Risultati
Grazie alla sonda e al software Renishaw, i processi di lavorazione di Honeywell vengono eseguiti senza imprevisti. Prima di implementare la nuova tecnologia, l'operatore doveva inserire il pezzo, impostare il calibro e definire il diametro e le superfici. Se uno solo di questi dati veniva dimenticato o era immesso in modo scorretto oppure se il fissaggio era danneggiato, il pezzo finito era da buttare. Ora possiamo individuare in anticipo i difetti e risolverli prima della lavorazione.
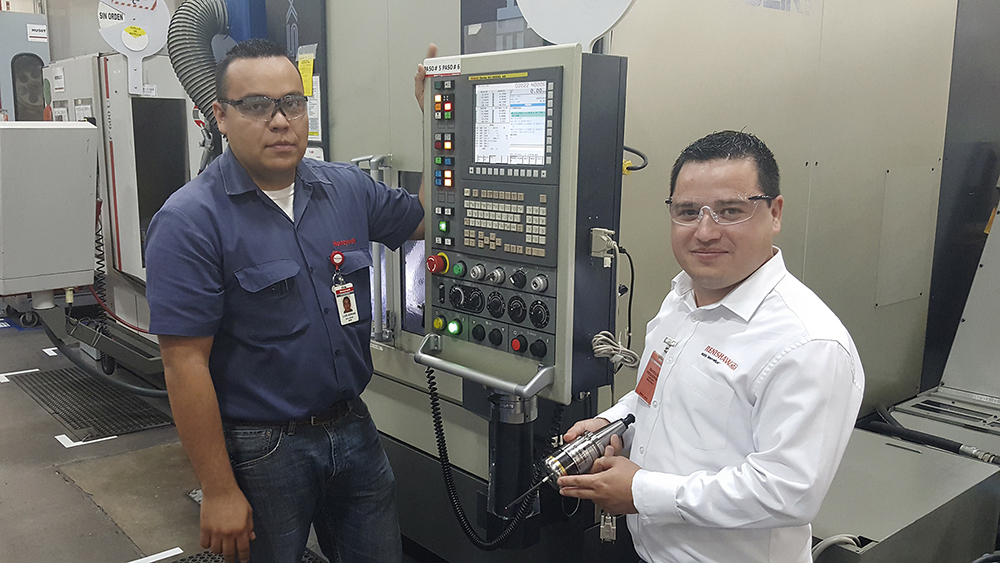
Riprodotto da Modern Machine Shop Mexico, con l'espressa autorizzazione dell'editore
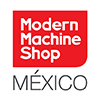