Produttore di macchine speciali investe nel sistema di allineamento Renishaw per ottenere maggiore accuratezza
Al fine di offrire i migliori risultati nei progetti dei clienti di dimensioni più grandi, il produttore di macchine speciali Metecno Oy ha collaborato con Renishaw all’implementazione di un sistema di misura degli errori geometrici. Il sistema di allineamento laser XK10 di Renishaw ha consentito a Metecno Oy di gestire internamente più processi di controllo qualità, soddisfacendo le specifiche per i nuovi clienti ed estendendo al contempo le proprie capacità di fornire macchine di alta qualità.
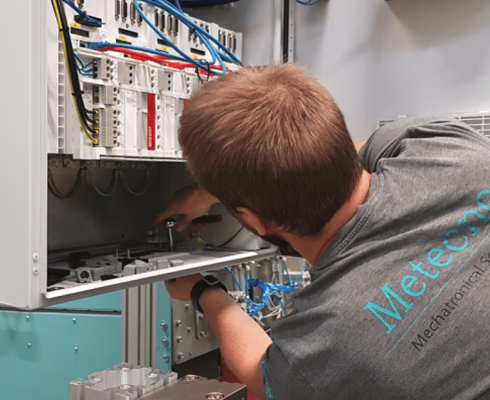
Tecnico Metecno Oy mentre assembla una macchina CNC
Background
Fondata nel 2008, Metecno Oy è un produttore finlandese di macchine speciali a conduzione familiare specializzato in macchine CNC, progetti per l’automazione e per l’integrazione robotica. Il suo team costituito da 12 persone offre macchine pesonalizzate e soluzioni per l’automazione chiavi in mano, progettando e fabbricando macchinari di produzione che migliorano la produttività, tra cui macchine utensili, centri di lavoro e fresatrici. Metecno Oy propone soluzioni a qualsiasi produttore che abbia bisogno di un macchinario di produzione dedicato. L’azienda opera in diversi settori, tra i quali il nucleare, il siderurgico, il minerario e l’alimentare.
È inoltre uno dei pochi produttori finlandesi a progettare e costruire macchine CNC personalizzate. Di conseguenza il giro d’affari è cresciuto rapidamente rispetto all’inizio, con un fatturato record di 1,2 milioni di € nel 2021 e un futuro più che promettente.
La sfida
L’azienda era stata contattata da un cliente che aveva bisogno di una macchina CNC personalizzata molto più grande di quelle solitamente costruite da Metecno. Il cliente aveva inoltre requisiti molto specifici sia in termini di tolleranze che di qualità superficiale.
L'accuratezza è fondamentale quando si tratta di sviluppare una macchina: un assemblaggio scorretto può pregiudicarne il funzionamento. Ad esempio, le fresatrici sono caratterizzate da guide lineari, per manovrare la tavola della macchina su ciascun asse. Eventuali errori durante l'assemblaggio del telaio sugli altri componenti della macchina possono portare le guide fuori dalle tolleranze. Le piccole inaccuratezze possono non avere conseguenze sulla qualità del prodotto, ma il rischio è quello di ridurre la vita della macchina. Inoltre, una volta fabbricata, il team Metecno Oy posiziona la macchina presso il cliente e questo può avere un impatto sull’accuratezza della stessa.
Oltre ad assicurare che gli assi siano accurati, i produttori di macchine CNC come Metecno Oy devono tener conto della perpendicolarità del mandrino. Se non è in squadra, sul pezzo di lavoro resteranno dei segni dell’utensile da taglio che pregiudicheranno la finitura superficiale dei pezzi lavorati.
“Tutte le macchine speciali da noi prodotte devono superare rigidissimi processi di gestione della qualità prima di essere consegnate al cliente”, spiega Mikko Similä, System Design Engineer in Metecno Oy. “Per essere certi che le macchine da noi consegnate siano accurate e affidabili, solitamente affidiamo i controlli di qualità a un nostro subappaltatore. Questa soluzione funziona per le nostre macchine più piccole, ma quando ci viene richiesto un progetto più grande con tolleranze più rigide, vogliamo effettuare le verifiche internamente, per poter consegnare una macchina di alta qualità prevedendone correttamente il ciclo di vita.”
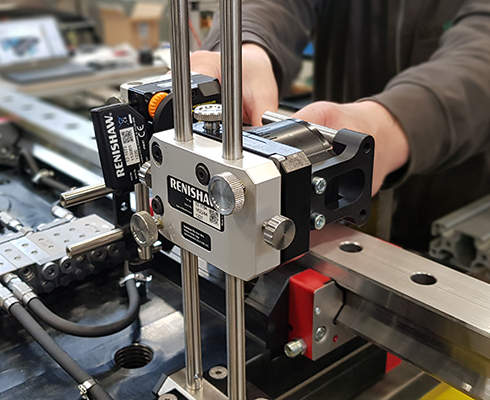
Allineamento del pentaprisma del sistema XK10 per eseguire un test di parallelismo
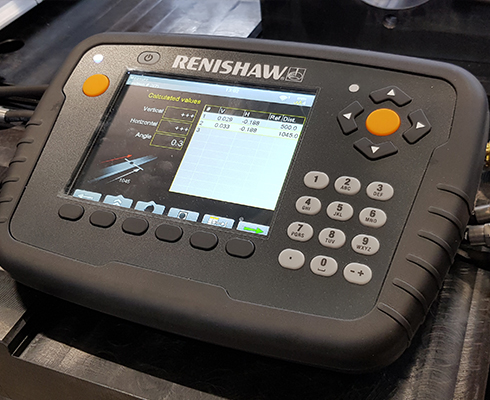
Feedback in diretta con l’unità di visualizzazione portatile del sistema XK10
Soluzione
Dopo aver visionato diverse soluzioni, Metecno Oy ha ritenuto che il sistema di allineamento laser XK10 di Renishaw fosse la soluzione migliore, anche dal punto di vista economico.
Il sistema XK10 è stato sviluppato per misurare gli errori geometrici e di rotazione delle macchine utensili. Utilizzare il sistema unitamente al kit di fissaggio della macchina utensile consente misure più facili e veloci rispetto ai metodi tradizionali come i comparatori. La possibilità di misurare gli errori geometrici e di rotazione in fase di assemblaggio, manutenzione e riparazione della macchina, consente di far raggiungere alla macchina stessa prestazioni ottimali grazie ad assi accuratamente allineati e regolati. Inoltre, si riducono i tempi di assemblaggio e di assistenza, incluse le operazioni di manutenzione e di riparazione. Il sistema XK10 è inoltre in grado di misurare l'angolo al quale sta puntando il mandrino e assicura un allineamento accurato su una rotazione completa di 360°.
“Il sistema XK10 ci ha permesso di migliorare i nostri processi di misura per le macchine più grandi” spiega Similä. “Nel corso di questo progetto abbiamo utilizzato il sistema XK10 per misurare la macchina sia durante l'assemblaggio, per verificare che gli assi fossero dritti sull’intero asse di corsa, sia a seguito dell’installazione.
Acquisire maggiore familiarità con il processo ci permetterà di monitorare i fattori esterni che possono influenzare la misura, come l’effetto delle variazioni ambientali. Inserire i parametri del test nell’unità di visualizzazione XK10 è facile, così come utilizzare il kit di fissaggio per controllare con semplicità un’ampia gamma di misure. Abbiamo inoltre identificato dove potremo utilizzare il sistema XK10 sui futuri macchinari.”
“Avvalersi di un subappaltatore consente a Metecno Oy di avere la certezza che tutti i suoi macchinari rispettino i requisiti di qualità, ma parlando con il team ci siamo resi conto di come gestire internamente alcuni processi potesse risultare vantaggioso anche per il produttore e i propri clienti,” spiega Isto Tuomisto, Area Sales Manager di Renishaw Finlandia. “Il sistema XK10 è stato sviluppato per facilitare l’assemblaggio delle macchine. Il team ha familiarizzato molto rapidamente con il sistema una volta installato, il che ha permesso a Metecno di consegnare la sua macchina con rapidità ed efficienza. Su questo progetto, verificare l’allineamento durante l’assemblaggio consente di identificare e risolvere eventuali errori prima che la macchina sia ultimata, quando è molto più difficile farlo” continua Tuomisto.
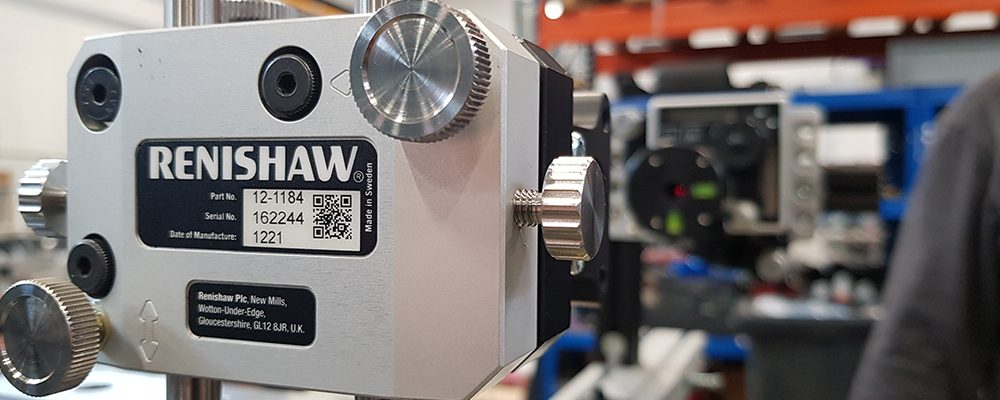
Kit parallelismo XK10 allineato all’asse della macchina
Risultati
“Investire nel sistema XK10 ci permette di convalidare l'accuratezza della macchina in più punti” afferma Similä. “Questo è stato particolarmente utile nel corso di questo progetto, poiché una volta completato, dovremo disassemblare la macchina per trasportarla presso il cliente. Una volta ricostruita la macchina nel reparto di produzione, potremo utilizzare il sistema XK10 per ricontrollare la macchina, garantendo al cliente l’accuratezza che si aspetta."
Nonostante il progetto sia ancora in corso, abbiamo già notato risultati positivi grazie all’investimento nel sistema di allineamento laser XK10: maggiore accuratezza, risparmio di tempo, minori costi. Abbiamo quindi già beneficiato di un ritorno sull’investimento. Inoltre, possiamo accettare progetti di dimensioni maggiori sapendo di poter comunque garantire qualità e accuratezza. Ora che conosciamo le capacità del sistema XK10, stiamo valutando di utilizzare altri sistemi Renishaw per gestire internamente ancora più processi di controllo qualità.
Metecno Oy (Finlandia)