Le soluzioni di produzione intelligente aiutano a dimezzare i tempi di lavorazione dei componenti per turbine a gas
Doncasters Precision Castings – Deritend, è un'azienda leader nella produzione di superfici aerodinamiche per turbine a gas, realizzate con superleghe a base di nichel e cobalto tramite microfusione e lavorazioni a macchina.
L'azienda ha delineato una strategia votata all'espansione, che viene supportata da costanti investimenti nel campo delle lavorazioni snelle e della prototipazione rapida. Tale impegno ha portato a una crescita significativa dell’offerta di servizi di lavorazione a macchina utensile, la quale supporta l'attività principale di microfusione. A sua volta, l'aumento della domanda ha portato a investimenti importanti, superiori ai due milioni di sterline, per l'acquisto di macchine utensili Mazak, infrastrutture e software per la lavorazione di 14 nuovi prodotti.
Background
Prima di investire nei centri di lavoro a 5 assi Mazak, le lavorazioni venivano effettuate utilizzando macchine convenzionali a 3 assi, con supporti di fissaggio fissi. I processi portavano via molto tempo e richiedevano operatori altamente specializzati. La lavorazione di un ugello, comprendente l’impostazione della macchina, richiedeva mediamente quattro ore di lavoro, oggettivamente troppo tempo per far fronte all'aumento della domanda. Inoltre, il team tecnico dell'azienda reputava che le attrezzature di fissaggio fossero una soluzione ormai obsoleta ed eccessivamente costosa. Per tutte queste ragioni, venne deciso di intervenire con un investimento importante in nuove tecnologie produttive, acquistando tre centri di lavoro verticali VORTEX i-630V/6. Tali macchine avrebbero consentito a Doncasters di continuare la produzione in sede per fornire ai clienti prodotti provenienti da un unico fornitore.
Come parte dell'investimento, le macchine vennero dotate di sonde Renishaw RMP600 ad elevata accuratezza, con tecnologia estensimetrica brevettata, RENGAGE™. Le loro eccellenti prestazioni in applicazioni con forme e contorni 3D complessi rendevano queste sonde l'accessorio ideale per il lavoro da svolgere. Tuttavia, in occasione delle nuove lavorazioni, il cliente ebbe bisogno di ulteriore supporto e Renishaw potè contare sul know-how di una delle sue aziende consociate, Metrology Software Products ltd (MSP).
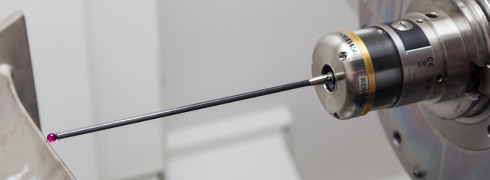
La sfida
L'obiettivo era quello di produrre "pezzi perfetti al primo tentativo", al fine di eliminare i rischi di errore umano e di aumentare la produttività complessiva. Ollie Macrow, Engineering Manager di Doncasters, spiega: "Quando ci si occupa di stampi per superleghe con un valore di migliaia di sterline, è rassicurante avere la certezza già prima di iniziare la lavorazione che il pezzo finale sarà corretto. I costi sono un problema da tenere sempre in considerazione: oltre a quelli dello stampo, bisogna calcolare il tempo di lavorazione e il costo degli utensili, che a causa dei materiali impiegati, risulta essere abbastanza elevato. Inoltre, bisogna ricordare che alcuni componenti non possono essere rilavorati, per cui se escono imperfetti dalla macchina diventano inevitabilmente degli scarti. Eravamo consapevoli della necessità di ispezionare i pezzi, ma dovevamo trovare il modo di farlo senza ricorrere alle attrezzature di fissaggio". Gli ingegneri di Doncasters non avevano una conoscenza approfondita delle sonde di ispezione perché fino a quel momento le avevano utilizzate solamente per regolazioni elementari e per l'allineamento dei piani. Fu così che decisero di affidarsi all'esperienza di Renishaw.
Un'altra priorità era l'eliminazione delle attrezzature di fissaggio che risultavano costose e portavano via troppo tempo. "I fissaggi ponevano una serie di problematiche: erano costosi, richiedevano personale specializzato per il corretto posizionamento dei pezzi e, se si danneggiavano, potevano causare il blocco della produzione a causa dell'impossibilità di allineare i pezzi. Era quindi necessario avere una grande cura delle attrezzature e ciò comportava maggiori costi e perdite di tempo. Ci eravamo posti l'obiettivo di sostituire i nostri fissaggi con semplici soluzioni modulari, per ridurre l'intervento umano durante la fase di impostazione". Un elemento imprescindibile era il rispetto dei target di produzione, per cui si dovettero cercare metodi per ridurre i tempi di impostazione delle nuove macchine Mazak. Anche se le nuove macchine consentivano di svolgere internamente il grosso delle attività di lavorazione, vi era comunque la necessità di esternalizzare alcuni processi secondari. L'azienda mirava in ogni caso a ottimizzare la produttività in modo da riuscire a gestire in sede l'intero processo produttivo. "Se fossimo riusciti a ottenere tale risultato, l'impatto sulla produzione sarebbe stato estremamente positivo. La possibilità di lavorare tutti i componenti nella nostra struttura implicava un notevole risparmio di tempo, perché non avremmo più dovuto spedire i pezzi a un'altra azienda e attendere due giorni per ricevere il prodotto finito", ha affermato Macrow.
Sono assolutamente convinto che non saremmo riusciti ad arrivare a questo risultato senza l'aiuto di Renishaw e MSP. Ci hanno fornito un supporto eccezionale e si sono dimostrati disponibilissimi ogni volta che abbiamo avuto bisogno di loro.
Doncasters Precision Castings – Deritend (Regno Unito)
Soluzione
Dopo aver esaminato il progetto, l'Applications Engineer di Renishaw, ha consigliato di abbinare i software MSP (NC-PerfectPart e NC-Checker) alla sonda RMP600 per creare una soluzione che rispondesse al meglio alle necessità di Doncasters. Questa combinazione di hardware e software innovativi consente di identificare gli errori di posizionamento del pezzo e di valutare le prestazioni geometriche della macchina prima di procedere al taglio del particolare. Si inizia mappando la macchina utensile per creare un riferimento. NC-Checker verifica le prestazioni della sonda ed esegue controlli sui cinque assi della macchina. In questo modo, ancor prima di procedere all'impostazione e al taglio del pezzo, si ha la certezza che tutti i fattori che entrano in gioco durante le ispezioni e le lavorazioni rientrino nelle tolleranze previste. La verifica della macchina può essere ripetuta spesso, perché richiede solo pochi minuti e garantisce che la macchina operi sempre all'interno dei parametri impostati, producendo così pezzi sempre buoni.
NC-PerfectPart risolve i problemi di un eventuale allineamento sbagliato del pezzo nella macchina utensile. Si tratta di un accorgimento particolarmente importante quando si producono pezzi con forme complesse o che devono essere lavorati con macchine a cinque assi. In genere, l'impostazione di tali pezzi richiede tempo e difficilmente viene eseguita in modo accurato e omogeneo. Tutti questi problemi possono essere superati ispezionando il pezzo con la sonda RMP600m utilizzando un programma creato dal file CAD del componente.
Partendo da questa misura iniziale, si crea un allineamento per eliminare eventuali errori di posizionamento in macchina. A questo punto, l'allineamento viene registrato nel controllo della macchina e le compensazioni caricate automaticamente per produrre un programma perfettamente allineato al pezzo. L'impostazione è automatica, quindi i fissaggi non rappresentano più un fattore critico del processo. Eventuali errori derivanti dall'impostazione manuale vengono eliminati e il tempo richiesto per l'impostazione è di pochi minuti, anche nel caso di componenti molto complessi.
Inoltre, elementi quali condizioni del materiale, sistemi di caricamento del pallet e temperatura vengono definiti nella fase iniziale del processo di lavorazione, riducendo ulteriormente i rischi di produrre pezzi fuori tolleranza.
Dopo il taglio, NC-PerfectPart conferma l'accuratezza del componente finito prima della rimozione dalla macchina utensile e dell'ispezione tramite CMM.
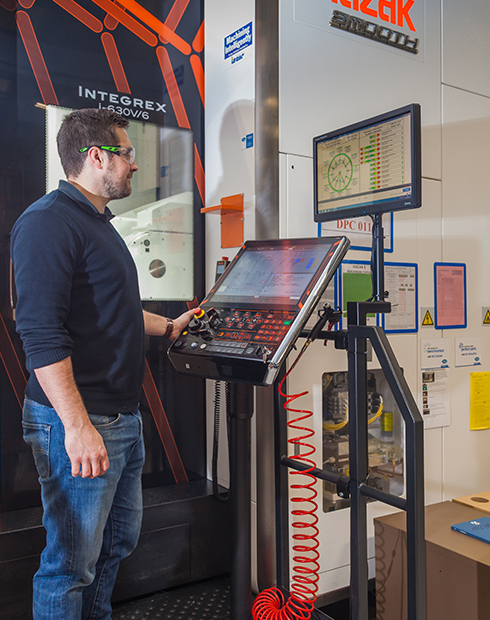
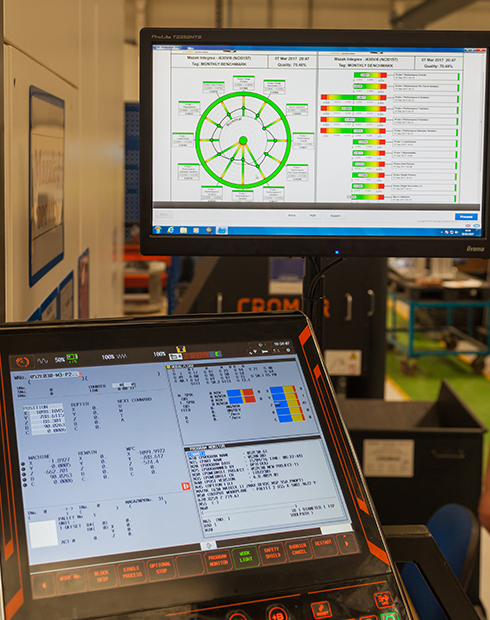
Risultati
Prima dell'adozione della sonda RMP600 e del software MSP ci volevano quattro ore per impostare e produrre un ugello di turbina a gas per uso industriale. Ora, lo stesso pezzo può essere ispezionato, lavorato e verificato in meno di due ore, con un aumento della produttività del 50%. Nel caso di componenti complessi, i tempi di lavorazione potevano arrivare anche a otto ore con la supervisione costante di un operatore qualificato. Oggi, gli stessi pezzi vengono completati con lo stesso ciclo di due ore usato per i pezzi più semplici, con un ritorno sull’investimento ancora maggiore. Grazie alla collaborazione con Renishaw e MSP, Doncasters ha migliorato i sistemi di allineamento, ottenendo nel complesso risultati eccellenti. Anche la correlazione fra misure in macchina, CMM e sistema di scansione Bluelight è migliorata.
Valutando l'ottimo risultato raggiunto, Ollie Macrow ha commentato: "Questa è una storia a lieto fine, che non avremmo potuto raccontare senza il supporto di Renishaw e MSP.
Quando abbiamo deciso di acquistare le macchine, abbiamo chiesto a Mazak un consiglio su come arrivare a questo risultato. I loro esperti ritenevano che la nostra configurazione non potesse farci raggiungere risultati così ambiziosi, poi sono arrivati Renishaw e MSP e ci hanno fornito esattamente la soluzione che cercavamo. Oggi riceviamo commenti positivi da tutti i nostri clienti e il numero di pezzi prodotti correttamente al primo tentativo è aumentato in modo esponenziale. Sono assolutamente convinto che non saremmo riusciti ad arrivare a questo risultato senza l'aiuto di Renishaw e MSP. Ci hanno fornito un supporto eccezionale e si sono dimostrati disponibilissimi ogni volta che abbiamo avuto bisogno di loro".