La cella di tornitura a processo controllato si paga da sé in 18 giorni.
I calibri programmabili Equator sono una parte significativa nella più avanzata cella automatizzata per lo smistamento e la lavorazione di cuscinetti
Conroe, Texas, USA – Molti vorrebbero riuscirci, Conroe Machine lo fa. Tornitura 24 ore al giorno di pezzi multipli in una cella non presidiata con un processo che si controlla da solo. Il sistema integra un robot FANUC, un calibro flessibile Equator e il software EZ-IO di Renishaw che fornisce le funzioni di comunicazione necessarie per effettuare l'ispezione del 100% dei pezzi e per la compensazione automatica di un tornio Okuma 2SP-250 a doppio mandrino. La cella può anche confezionare e pallettizzare i pezzi finiti. L'investimento effettuato nella cella di tornitura si è ripagato da solo in appena 18 giorni.
Conroe è la prova materiale di come un'azienda disposta a investire nel talento dei giovani per l'automazione possa fare uso di tecnologie innovative, come il calibro programmabile Equator di Renishaw e i software sviluppati da James Wardell e Jeff Buck, specialisti di robotica e controlli numerici. Lo stesso gruppo di lavoro ha creato per un cliente una cella automatizzata e non presidiata per la misura e la divisione dei pezzi, combinando due sistemi Equator, un robot FANUC, un sistema di visione e più linee di trasporto a sezione ridotta. In entrambe le applicazioni, Equator ha dimostrato il valore della comparazione programmabile, misurando serie di cuscinetti in modo rapido, efficace, economico, senza fissaggi e senza soffrire per l'ambiente di lavoro d'officina.
Conroe Machine è un'azienda relativamente giovane. È stata fondata da Murray ‘Tippy' Touchette nel 2000 con il preciso scopo di produrre componenti meccanici usando la migliore tecnologia disponibile. La società è cresciuta rapidamente, fino a contare circa 150 dipendenti che lavorano in uno stabilimento climatizzato di circa 6.000 metri quadrati. Nonostante il suo carattere di officina meccanica generale, la vicinanza a Houston fa sì che molte commesse arrivino dal settore petrolifero e del gas, in particolare componenti per perforazioni. Uno dei progetti più frequenti riguarda la lavorazione di piste per cuscinetti reggispinta da utilizzare nei motori da perforazione. Migliaia di pezzi prodotti senza sosta, ogni settimana.
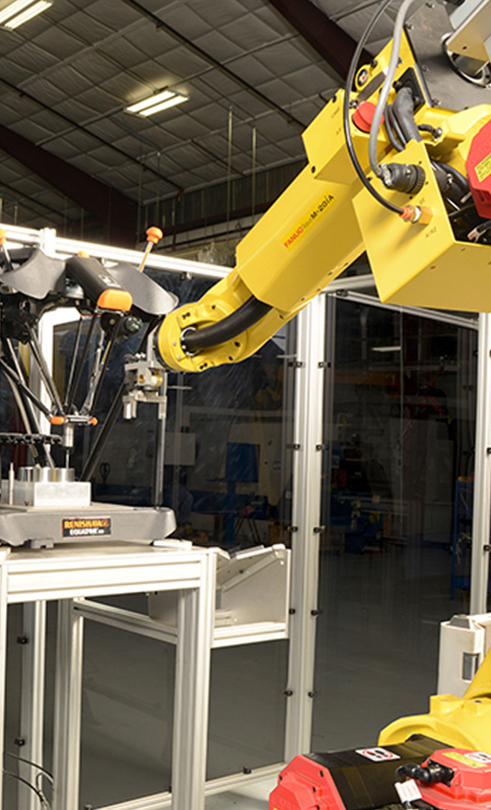
Alzare il grado di automazione
I cuscinetti sono sgrossati in quattro torni Doosan Puma che in passato eseguivano anche la finitura e richiedevano la presenza di quattro operatori. Uno dei primi progetti di automazione sviluppati da Conroe ha previsto di dividere le due macchine in due celle, caricate e scaricate dai robot FANUC e dedicate alla sgrossatura. I pezzi semifiniti sono temprati per indurirli a HRC 65 per una profondità di 1,7mm prima della tornitura di finitura.
"Con l'introduzione delle due celle, la produzione ha raggiunto gli 800-1000 pezzi al giorno ovvero 400-500 per cella" racconta James Wardell. "Inizialmente avevamo un unico operatore che si occupava di caricare le macchine e ispezionare i pezzi, tuttavia, con questi numeri, una persona è in grado di ispezionare solo una parte della produzione e noi avevamo bisogno di aumentare ancora la quantità".
Vantaggi di Equator
"Il passaggio successivo è stato quello di progettare un processo totalmente automatizzato per la finitura dei pezzi, che includesse il caricamento in macchina, le misure di postprocessing,la compensazione degli utensili, l'incisione dei pezzi e l'inscatolamento e la pallettizzazione dei pezzi". "Avevamo le idee abbastanza chiare sui componenti del sistema, tranne che per la tecnologia di misura dei pezzi e il software per la compensazione degli utensili. L'ispezione deve essere effettuata rapidamente, per non rallentare i tempi del ciclo che a volte non superano i 98 secondi. Inizialmente pensavamo di usare un laser a luce bianca, che garantiva la massima rapidità, ma i pezzi sono troppo riflettenti. Abbiamo preso in considerazione anche calibri rigidi e CMM da officina. Tuttavia questa opzione risultava eccessivamente costosa, richiedeva un'impostazione molto delicata e la CMM non dava alcun vantaggio in termini di velocità. Una nostra Regional Manager, Sheila Schermerhorn, stava collaborando con Renishaw per altri motivi e ci suggerì di valutare un sistema Equator".
Per la nostra cella di lavorazione nessun altro strumento di misura poteva essere redditizio quanto Equator.
Conroe Machine (Stati Uniti)
Utensili e software per il controllo dei processi
Equator rappresenta un'alternativa flessibile ed economica ai calibri rigidi. Per le misure utilizza il metodo del confronto: un pezzo campione con misure rilevate sulla CMM è utilizzato per "calibrare" Equator. Tutte le misure successive sono quindi confrontate con il campione. Subito dopo la calibrazione, la ripetibilità è di 0,002 mm. Equator può essere ricalibrato in qualsiasi momento per compensare variazioni di temperatura nell'ambiente di lavoro. Equator utilizza una sonda SP25 per la scansione e la raccolta dati a contatto e può raggiungere velocità di 1.000 punti al secondo. Gli stili sono conservati in un rack di cambio utensile integrato con sei posizioni, e il sistema si programma mediante il software MODUS™ per Equator. Equator può essere utilizzato manualmente con estrema semplicità, ma in questo caso particolare il sistema è stato integrato con i sistemi automatizzati di Conroe utilizzando il software EZ-IO per l'automazione.
"All'inizio del 2012 abbiamo assistito a una demo di Equator in azione, insieme a un tornio Okuma a doppio gantry e doppio mandrino" prosegue Wardell. "Oltre ad essere già predisposto per l'automazione, il tornio aveva un controllo a doppio percorso basato su Windows®, con piattaforma operativa con PC ad architettura aperta, un elemento molto importante per i nostri piani di sviluppo di un nostro software di compensazione automatica".
Equator in una cella automatica
Wardell e Buck sono successivamente passati alla creazione di una cella che comprendeva una macchina Okuma 2SP-250H, un singolo Equator, una macchina per incisioni e un robot FANUC M20iA a 6 assi. In pratica, i caricatori del tornio sono alimentati con i pezzi non lavorati (circa 300), I due caricatori a gantry alimentano i mandrini e posizionano i pezzi lavorati su uno scivolo che li porta su un nastro trasportatore, dove vengono prelevati dal robot. A questo punto, il robot posiziona il pezzo su Equator per le misure e, se accettabile, lo trasferisce alla macchina per incisioni. Infine i pezzi finiti sono inscatolati e pallettizzati.
"Abbiamo sviluppato un nostro software per la compensazione degli utensili, viene eseguito dal CN", aggiunge Wardell. "I risultati di misura di Equator sono trasmessi in forma di file CSV e utilizzati dal software per correggere gli utensili nel caso in cui le misure del pezzo non rientrino nelle tolleranze". Con la lavorazione vengono rimossi circa 0,38 mm da ciascun lato del pezzo, con una tolleranza molto rigida (0,025 mm) e una finitura della superficie a 0,5 micrometri. Le dimensioni dei pezzi variano da 3 a 6 pollici (diametro esterno). "Equator non ha problemi a misurare i pezzi nelle nostre tolleranze, con un buon margine”, conclude Wardell.
Controllo di processo
"Le dimensioni dei diametri interno ed esterno sono sempre accurate, con una piccola variazione sul raggio. I pezzi vengono divisi in base alle dimensioni e in questo modo è possibile ridurre al minimo le sostituzioni dei morsetti del mandrino e altri interventi. La velocità di Equator evita che le operazioni di misura rallentino il processo. Effettuiamo la ricalibrazione solo una volta al giorno, perché la macchina opera in un ambiente climatizzato (22,2 °C).
Principi di ispezione e flessibilità dell'automazione
La metodologia di misura per i pezzi è incredibilmente semplice. "Abbiamo fabbricato un blocco di alluminio con un foro al centro e lo mettiamo al centro della piastra di fissaggio di Equator", spiega Wardell. "In questo modo, possiamo determinare il centro e impostare il sistema di coordinate. Ogni pezzo è posizionato al centro del blocco. Centriamo il pezzo quindi eseguiamo una scansione della superficie per tutte le altre misure. Il processo di misura è stato progettato in modo da funzionare senza elementi di fissaggio e senza bisogno di cambiare stilo. Il robot usa il software di automazione EZ-IO di Equator per selezionare il programma di misura da eseguire per ciascun tipo di pezzo. Sappiamo quali sono gli elementi critici da misurare per avere la certezza che il pezzo rientri nelle tolleranze".
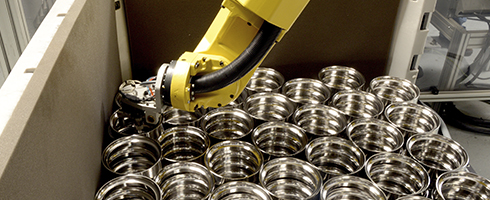
Misura/divisione dei pezzi usati
Attualmente, la cella di tornitura copre il lavoro che prima era svolto da due celle, ed è stato avviato un nuovo progetto che prevede la creazione di una cella di selezione dei pezzi per conto di un cliente. Partendo da un progetto concepito da Touchette, Wardell e Buck stanno sviluppando una cella per la classificazione dei pezzi usati in base all'usura.
Nelle officine dei campi petroliferi i motori in disuso sono smontati, riparati e reintrodotti in servizio. "Il cliente era solito eseguire controlli visivi delle piste usate per determinare se fossero ancora utilizzabili, ben sapendo che talvolta buttava anche alcuni pezzi ancora buoni e, con loro, del denaro", racconta Wardell. "La nostra idea era di fornire al cliente un sistema di classificazione di tipo "plug and play", per eliminare la soggettività dal processo e recuperare un numero maggiore di guide".
La cella ideata da Buck e Wardell era ancora in fase di sviluppo quando l'articolo è stato redatto e consisteva di due Equator, un robot FANUC LRMate 200iC a 6 assi, più linee di trasporto a basso profilo, un sistema FANUC di visione iR e un modulo ATI di cambio rapido per le pinze del robot. Il sistema di visione informa Equator sul codice del pezzo presentato e sul programma da eseguire. I pezzi utilizzabili sono separati dai pezzi danneggiati e vanno su un nastro trasportatore dedicato.
"Il sistema è stato pensato per essere consegnato come una singola unità che possa essere facilmente utilizzata dal personale dell'officina. È sufficiente accenderlo e caricare i pezzi sul nastro", afferma Buck.
"Per portare a termine questo progetto, nessuno strumento di misura poteva competere con Equator in fatto di convenienza economica e risultati", conclude Wardell. "E pensiamo che questo esperimento di integrazione per conto terzi apra alla nostra azienda le porte per intraprendere una nuova avventura commerciale".