Ez az oldal az Ön nyelvén jelenleg nem elérhető. Az automatikus fordítás a megtekinthető a Google Fordító segítségével.
A szolgáltatás biztosításáért nem vállalunk felelősséget, a fordított szöveget nem ellenőrizzük.
Ha további segítségre van szüksége, lépjen kapcsolatba velünk.
Metal powders for AM
Renishaw's powder bed fusion technology uses a range of metal powders including titanium alloy Ti6Al4V, nickel alloys inconel 625 and 718, cobalt chromium, and aluminium alloy AlSi10Mg.
Powder metallurgy
Powder metallurgy (PM) is the general term for the consolidation of metal powders into solid components using heat and pressure to fuse the particles together, it is alternatively referred to as press and sinter. There are various technologies that fall under the PM umbrella such as hot isostatic pressing (HIP), metal injection moulding (MIM) and spark plasma sintering (SPS). All of these technologies can be used to manufacture near net shape components, reducing the requirement for subtractive machining which can create high levels of waste material.
Renishaw's additive manufacturing technology also uses metal powders as the feed material, however rather than using pressure and heat to fuse the particles together in a die, the powder particles are melted using a high power laser in sequential ultra-thin layers approximately the thickness of a human hair. The technique of using fine powders and very thin layers to build up metal components means that highly complex geometries are possible. The capability to include fine meshes, internal channels and to only place material where it is needed means that the technology can be used to reduce the material usage, increase functionality, consolidate multiple parts and manufacture geometries that are practically impossible by alternative methods.
Powder characteristics
Powder characteristics are very important for successful powder bed fusion. Renishaw make sure that the powders supplied for their additive manufacturing systems are of the highest quality.
What is important?
Good flow, close packing of particles and spherical particle shape are all important characteristics that lead to consistent and predictable powder dosing and layers.
Particle size
Renishaw's powder bed fusion systems use metal powders that range between 15 microns and 45 microns, the image on the right demonstrates the powders size in relative terms.
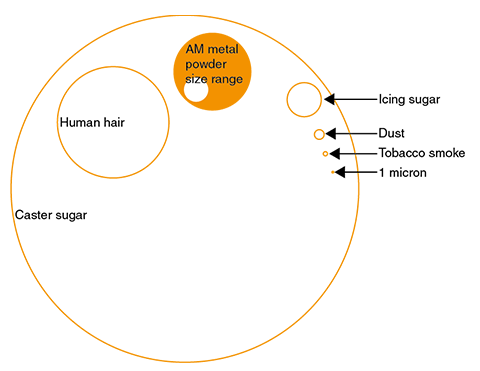
How is metal powder made?
The two main methods of metal powder production are gas atomisation and plasma atomisation.
Plasma atomisation
Generally used for the production of high purity reactive metals with high melting points such as titanium alloy Ti6Al4V. Metal feedstock in wire form is fed into the top of the atomiser, it is then melted using a plasma torch, as the molten metal falls it solidifies creating spherical particles.
Gas atomisation
Probably the most common method of metal powder production, it uses a molten metal pool which is forced through a nozzle, then broken up with a stream of inert gas such as argon or nitrogen. The inert gas stream causes the molten metal to solidify, and the spherical particles are collected at the bottom of the chamber.