A folyamatszabályozással működő keményforgácsoló cella 18 nap alatt visszahozza az árát
A programozható Equator mérőkészülékek segítségével olyan automatizált cella alakítható ki, amely ideálisan alkalmas csapágyak megmunkálásához és alkatrészek válogatásához.
Conroe, Texas, USA – A Conroe Machine olyan munkát végez, amelyről a legtöbb megmunkálóüzem csak álmodik – egy egész alkatrészcsalád keményforgácsolását végzi folyamatos üzemben egy kezelő nélküli cellában, „önszabályozó” folyamat alkalmazásával. A Fanuc robotot és az Equator mérőrendszert a Renishaw EZ-IO szoftvere segítségével integrálják egy funkcionális egységbe, amely egyszerű, átfogó kommunikációs funkciókat biztosít a munkadarabok 100 százalékos ellenőrzéséhez és az ikerorsós Okuma 2SP-250 esztergagép automatikus kompenzálásához. A cella dobozolja és raklapokra is helyezi a kész alkatrészeket. A vállalat szerint az esztergálócella ára mindössze 18 nap alatt megtérült, ami – valljuk meg – lenyűgöző eredmény.
A Conroe példája kiváló bizonyíték arra, hogy ha kész kiaknázni napjaink fiatal automatizálási szakértőinek lenyűgöző tehetségét, akkor bármelyik gyártóüzem sikerrel alkalmazhatja az olyan új technológiákat, mint a Renishaw programozható Equator készülékét, amelynek használatát ebben az esetben a James Wardell CNC-programozó és Jeff Buck robottechnológus által fejlesztett szoftver és programozás tette lehetővé. A fent nevezett automatizálási csapat következő projektje keretében egy automatikus munkadarabmérő/-válogató cellát alkotott meg a cég egyik ügyfele számára, amelyhez két Equator készüléket, egy FANUC robotot, egy optikai mérőrendszert és több lapos, helytakarékos szállítópályát használtak fel. Az Equator mindkét alkalmazásban jól szemlélteti a programozható összehasonlító vizsgálat előnyeit azzal, hogy lehetővé teszi egy csapágyakhoz való futógyűrű-sorozat gyors, költséghatékony és befogás nélküli, mégis problémamentes mérését gyártóüzemi körülmények között.
A Conroe Machine egy viszonylag fiatal vállalat, amelyet Murray „Tippy” Touchette alapított 2000-ben, azzal az eltökélt szándékkal, hogy az elérhető legmodernebb gyártási technológiával állítsanak elő alkatrészeket. A rövid időn belül 150 fősre bővült cég egy 6000 négyzetméteres klimatizált üzemben működik. Noha a Conroe általános forgácsolóüzemként működik, Houstonhoz közeli elhelyezkedése révén megrendelései jelentős részét olaj- és gázipari vállalatoktól kapja, főként fúróeszközök gyártására. Az iparág egyik szereplőjétől kapott folyamatos megbízásai egyikének keretében a cég támcsapágy-futógyűrűket állít elő a fúrószárak forgatására rásegítő hidraulikus motorokhoz. Ezeket az alkatrészeket folyamatos munkarendben, heti több ezres darabszámban gyártják.
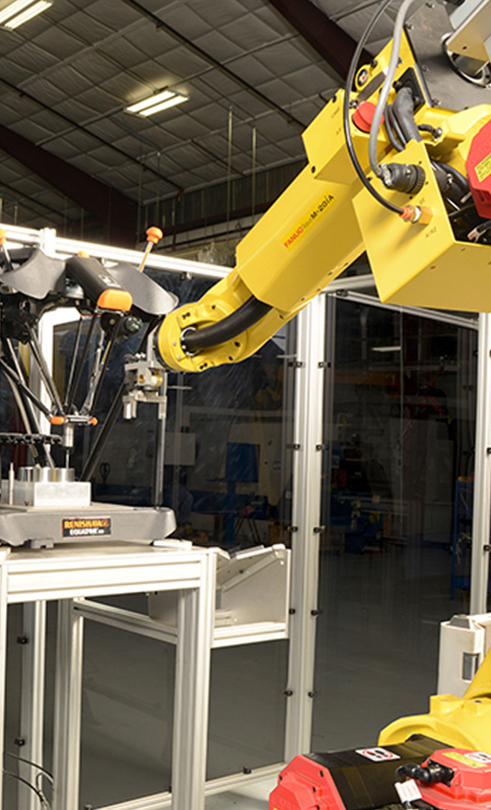
Előrelépés az automatizálás terén
A csapágyakat jelenleg négy olyan Doosan Puma esztergán nagyolják, amelyek eredetileg a nagyolást és a simítást is végezték, és amelyeken korábban négy gépkezelő dolgozott. Ezek a gépek most már két, a gyártóüzem korábbi automatizálási projektjei keretében kialakított cellában taláhatóak, FANUC robotok látják el őket munkadarabokkal, és kizárólag a nagyolási fázist végzik. A félkész alkatrészek a simító forgácsolás előtt 1,7 mm mélységű és HRC 65 keménységű betétedzést kapnak.
„Napi gyártási csúcsteljesítményünk ezzel a két cellával összesen 800-1000, azaz cellánként 400-500 alkatrész.” – magyarázza James Wardell. „A munkadarabok gépekre rakodását és ellenőrzését egyetlen gépkezelő végezte. „Ilyen volumen mellett viszont egyetlen gépkezelő sem képes több munkadarabot ellenőrizni, nekünk ellenben tovább kellett fokoznunk a teljesítményünket.”
Miért pont az Equator?
„Fejlődésünk következő lépcsőjeként kitaláltunk egy teljesen automatikus folyamatot a simító megmunkálásra, benne automatikus munkadarab-betöltéssel, gyártás utáni méréssel, automatikus szerszámkompenzációval, munkadarab-gravírozással és a készdarabok dobozolásával/raklapozásával.” „Számos remek ötletünk volt a rendszer komponenseit illetően, kivéve a munkadarab-mérési technológiát, a CNC típusát és a szerszám-kompenzációs szoftvert. A vizsgálatnak gyorsan kell történnie, hogy lépést tudjon tartani a munkadarabok rövid, néha csupán 98 másodperces ciklusidejével. Eredetileg a fehér fényű lézeres vizsgálattal „szemeztünk” a sebessége miatt, ám a munkadarabjaink felülete túlzottan visszaveri a fényt. Fizikai idomszerek és gyártási környezetben használható koordináta-mérőgépek beszerzését is fontolgattuk. A fizikai idomszerek rendkívül drágák és precíz, hosszadalmas kalibrálást igényelnek, a koordináta-mérőgépek pedig nem gyorsították volna a folyamatainkat. Egy másik projekten együttműködve Sheila Schermerhorn, a Renishaw regionális vezetője mutatta be nekünk az Equator készüléket, mint lehetséges megoldást.”
Az általunk használt megmunkáló cellákban történő használatra nem találtunk az Equatorhoz hasonló költséghatékony, közvetlenül a műhelyben használható mérőeszközt.
Conroe Machine (Amerikai Egyesült Államok)
Folyamatszabályozási eszközök és szoftverek
Az Equator a speciális idomszeres mérés kedvező árú, rugalmasan használható alternatívája. Működése az összehasonlító mérési módszeren alapul. Az Equator kalibrálásához egy koordináta-mérőgéppel bemért, ismert méretekkel rendelkező etalon darab használatos, amely a későbbi mérések összehasonlítási alapjaként szolgál. Ismétlési pontossága kalibrálás után közvetlenül 0,002 mm. A gyártóüzem hőmérsékleti változásainak kompenzálására az Equator bármikor újrakalibrálható. Az Equator SP25 mérőfejet használ az érintéses és szkennelő adatgyűjtéshez, és másodpercenként akár 1000 pontot is képes bemérni. A tapintószárakat egy integrált hathelyes cserélőállvány tárolja, a rendszer pedig a MODUS™ Equator szoftverrel programozható. Az Equator kezelése manuálisan, egyszerű nyomógombokkal is lehetséges, ám jelen esetben kivitelének hála ideálisan integrálható volt a Conroe automatizált rendszereibe az EZ-IO automatizálási szoftver használatával.
„2012-ben részt vettünk egy nyílt napon a Hartwig cégnél, ahol láthattuk az Equator készüléket az Okuma ikerorsós, kétportálos esztergájával együtt dolgozni.” mondja Wardell. „Amellett hogy a készülék a mieinkhez hasonló típusú alkatrészek esetében automatizálható, az eszterga Windows® alapú OSP kétpályás vezérlése egy nyílt architektúrájú, PC-alapú kezelőplatform, ami különösen fontos volt számunkra a saját automatikus kompenzáló szoftverünk kifejlesztéséhez.”
Az Equator egy automatizált cellában
Wardell és Buck következő projektje egy olyan cella kialakítása, amely egy Okuma 2SP-250H gépből, egyetlen Equator készülékből, egy gravírozó gépből és egy FANUC M20iA 6 tengelyes robotból épül fel. A gyakorlatban az eszterga két darabot fogadó karusszeljei kb. 300 nyers munkadarabbal kerülnek feltöltésre. Az eszterga kettős portálos berakói viszik a nyersdarabokat az orsókhoz és teszik a készdarabokat egy csúszdára, amely egy szállítópályára továbbítja őket, ahonnan egy robot veszi fel őket. A robot a méréshez az Equator készülékbe helyezi a készdarabot, és ha a minősége megfelelő, akkor a gravírozó géphez viszi azt, majd végül becsomagolja és raklapokra helyezi a kiszállításra kész alkatrészeket.
„Kifejlesztettük saját szerszám-kompenzációs szoftverünket, amely az OSP vezérlésen futtatható.” – teszi hozzá Wardell. „Ez a szoftver az Equator készülék CSV fájlban továbbított mérési eredményeit használja fel arra, hogy korrigálja a szerszámok helyzetét, amikor a munkadarab kívül esik a tűrésen.” A megmunkálás kb. 0,38 mm vastag anyagot választ le a munkadarab minden oldaláról, ±0,025 mm minimális tűréssel és 0,5 mikronos felületi minőséggel. A munkadarabok külső átmérője három-hat hüvelyk között változik. „Az Equator minden gond nélkül, nagy tartalékkal képes mérni az általunk alkalmazott tűrések között” – mondja Wardell.
Folyamatszabályozás
„Az általunk gyártott alkatrészek külső és belső átmérője állandó marad, a sugár mindössze 5 mikron ingadozást mutat. A darabokat méret szerint csoportosítjuk, így a tokmánypofák cseréjére, illetve más szerszámozási műveletekre csak ritkán van szükség. Sebességének hála az Equator könnyedén képes lépést tartani a folyamattal. Naponta csak egyszer kalibrálunk, köszönhetően annak, hogy üzemünk 22,2 °C fokra klimatizált.
Vizsgálati elvek és az automatizálás nyújtotta rugalmasság
A darabok vizsgálatakor alkalmazott mérési módszer meglepően egyszerű. „Készítettünk egy, a közepén furattal ellátott alumínium tömböt, amelyet az Equator rögzítőlemez közepén helyeztünk el.” – magyarázza Wardell. „Ennek segítségével határozzuk meg a középpontot és állítjuk fel a koordináta-rendszerünket. Az összes munkadarabot ennek a tömbnek a közepébe helyezzük. Először tapintással meghatározzuk a darab közepét, majd felületi szkenneléssel a többi pontját is. A mérési eljárást úgy terveztük meg, hogy ne legyen hozzá szükség rögzítőkészülékre és a tapintószár cseréjére. A robot az Equator készüléken futó EZ-IO automatizálási szoftver segítségével kiválasztja, melyik mérési programot kell használni az adott alkatrésztípushoz. Pontosan tudjuk, melyek azok a kritikus jellemzők, amelyeket be kell mérnünk annak ellenőrzéséhez, hogy a darab tűrésen belül legyen.”
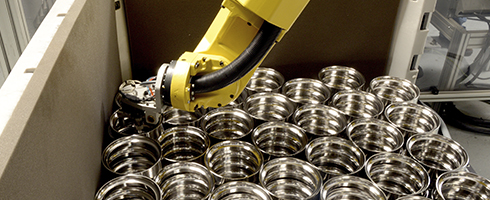
A felhasznált alkatrészek mérése/válogatása
A keményforgácsoló cella jelenleg napi 600-700 készdarabot gyárt, tehát már egy cella is elég a korábbi kettő helyett. A fejlesztés nyomán a cég egy újabb projektbe is belefogott, amelynek középpontjában az egyik ügyfél számára kifejlesztett alkatrész-válogató cella áll. A Touchette által felvázolt koncepció alapján Wardell és Buck egy olyan cella kifejlesztésén dolgozik, amely használt fúrószár-rásegítő hidraulikus motorokból kiszerelt támcsapágy-futógyűrűk mérésére és válogatására szolgál.
Az olajmezőket kiszolgáló szervizműhelyekben szétszerelik, felújítják és újra üzembe helyezik a használt motorokat. „Ügyfelünk korábban a futógyűrűk egyszerű szemrevételezésével döntötte el, hogy az alkatrészek újrafelhasználhatók-e, annak tudatában, hogy néha pazarló módon megfelelő alkatrészek is a szemétbe kerültek.” – osztja meg velünk Wardell. „Célunk egy olyan, csatlakoztatás után azonnal használatba vehető mérő és válogató rendszer létrehozása volt, ami kiiktatja az emberi tényezőt a folyamatból, hogy több jó futógyűrűt lehessen újrafelhasználni ahelyett, hogy a szemétben végeznék.”
A jelen cikk írásakor még fejlesztési fázisban lévő cellába Buck és Wardell két Equator mérőkészüléket, egy FANUC LRMate 200iC 6 tengelyes robotot, több helytakarékos, lapos szállítópályát, egy FANUC iR optikai mérőrendszert, valamint egy, a robot végeffektorain elhelyezett ATI gyors szerszámcserélőt épített be. Az optikai mérőrendszer utasítja az Equator rendszert, melyik cikkszámú darab van a gépben, és mely mérőprogramot kell hozzá futtatni. A jónak bizonyult alkatrészeket a berendezés ezt követően áthelyezi a megfelelő szállítópályára, míg a rossz darabok a selejtszállító pályára kerülnek.
„A rendszert úgy terveztük, hogy egy egységként lehessen kiszállítani, és a motorfelújító üzem dolgozói könnyen használhassák – csak be kell kapcsolni, és alkatrészeket kel helyezni a szállítópályára.” – meséli Buck.
„Az általunk használt megmunkáló cellákban történő használatra nem találtunk az Equatorhoz hasonló költséghatékony, közvetlenül a műhelyben használható mérőeszközt.” – teszi hozzá Wardell. „Azt reméljük, hogy az ügyfelünk számára végzett merész, újszerű cellaintegrációs projekt révén cégünk erre a területre is „betörhet”.”