Renishaw encoders support the latest in DUKIN’s CMM design
This case study explores how DUKIN designs CMMs that minimise measurement errors through robust mechanical design and position feedback. The recent expansion of the DUKIN product range to cover a variety of different accuracy and capacity requirements has been supported by Renishaw.
Background
DUKIN Co., Ltd., based in Korea, designs and manufactures a wide range of coordinate measurement machines (CMMs) that meet standard to ultra-high precision levels of metrology requirements in the electronics, automotive, aerospace and other industries.
These CMMs are used to capture three-dimensional measurement data on high precision, machined components such as car engine cylinders and aircraft engine blades as part of a quality control process.
The CMMs integrate either Renishaw optical or laser encoder systems to meet varying metrology challenges.
Linear position encoders are used in conjunction with Renishaw contact and vision probing systems to measure discrete points on a workpiece. This data is then used to ensure that parts meet predetermined tolerances.
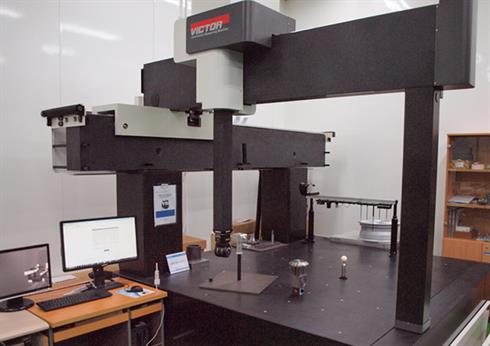
We have adopted Renishaw's TONiC™ encoder series and the ultra-high precision RLE interferometry laser encoder system. The high-performance TONiC encoder is the most widely used and has been integrated into our CHAMP, HERO and VICTOR CMMs. These models are designed for applications in the flat-panel display (FPD), micro-electronics, automotive and aerospace industries, as well as other markets.
DUKIN Co., Ltd. (Korea)
Challenge
Manufacturers require CMMs that achieve high performance and system stability, which is affected by temperature fluctuations and greatly impacts overall accuracy. The instability in linear position measurements taken on the gantry axis affects inspection throughput and measurement accuracy.
Even when deploying Renishaw's high speed 5-axis systems, which synchronise the movement of the 3 axes of the CMM and the 2 axes of the measuring head to inspect the part, the stability of the linear position measurements is important.
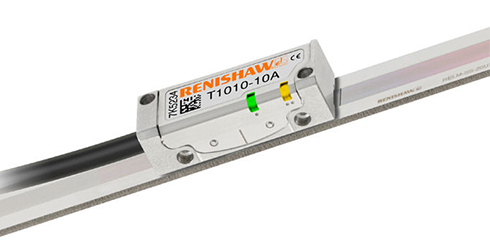
DUKIN use Renishaw's PH20 and REVO® 5-axis probe systems on their CMMs. Robust CMM design is essential to realise the full performance potential of these measurement systems.
System designers at DUKIN deploy robust design principles and use high quality materials and components to minimise the amount of measurement error. These mechanical design approaches are applied in conjunction with software that compensate for errors caused by thermal expansion.
A combination of statistical and theoretical modelling and accurate live measurements of position and acceleration are used for force feed-forward control of the CMM's motor driven axes.
For example, in a CMM bridge design; the X-axis (along the bridge) is driven along two guideways in the Y-axis direction where each shoulder of the bridge is driven by a linear system equipped with a separate servo motor.Solution
To prevent a torque moment in the Z-axis direction and thereby distortion of the bridge structure, force feed-forward control is applied by the controller. This depends on the detected position of the measurement head as it moves along the X-axis guideway and the setpoint acceleration along the Y-axis.
Alternatively, comparison of the accelerations of the Y-axis guideways may provide additional feedback control of the bridge moment. Dependable, high-accuracy, position encoders are vital for these complex control regimes to work. A combination of a priori data and position and acceleration feedback in the X-, Y- and Z- axis directions are used to give the highest-levels of metrology performance.
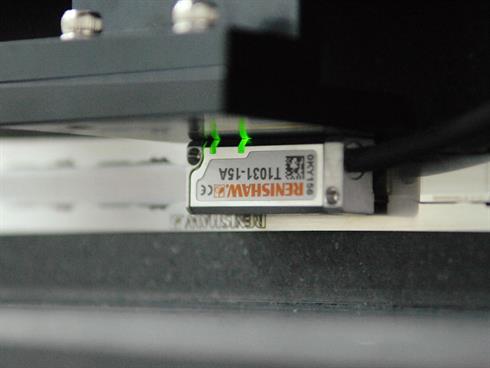
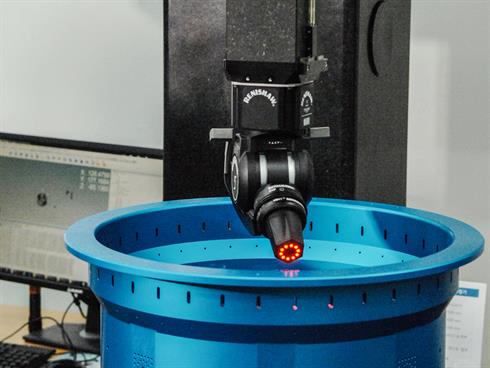
Results
Renishaw encoders and scales are used across the full range of CMMs offered by DUKIN. The TONiC™ incremental encoder system with RTLC linear scale is installed on DUKIN's gantry and bridge-type models. TONiC is Renishaw's compact, non-contact encoder system that offers speeds up to 10 m/s and linear resolutions down to 1 nm for both linear and rotary applications.
RTLC is a low profile stainless steel tape scale featuring a 20 µm pitch. It is accurate to ±5 µm/m and may be ordered in lengths of up to 10 m. Any thermal expansion of RTLC scale is independent of the substrate as it is suspended in a carrier track, which maintains an air gap underneath the scale.
As temperature changes occur in the CMM operating environment, the RTLC scale does not follow the same degree of deformation as the granite base. Thermal compensation is therefore greatly simplified – particularly in temperature controlled environments with the encoder scales and workpiece(s) in thermal equilibrium.
TONiC's dynamic signal processing gives improved signal stability with ultra-low Sub-Divisional Error of typically <±30 nm to help realize superior motion control performance.
DUKIN Technical Manager, Tae Young Ku, explains the important contribution of Renishaw's encoder products: “We offer a wide range of CMM product lines, including standard, high precision and ultra-high precision models, depending on the type of position feedback. We have adopted Renishaw's TONiC encoder series and the ultra-high precision RLE interferometry laser encoder system. The high-performance TONiC encoder is the most widely used and has been integrated into our CHAMP, HERO and VICTOR CMMs.
These models are designed for applications in the flat-panel display (FPD), micro-electronics, automotive and aerospace industries as well as other markets.”
Renishaw's TONiC series is also available with RELM ZeroMet™ scale. RELM has an expansion coefficient of only 0.75 ± 0.35 μm / m / ° C at 20 °C, and is almost unaffected by thermal expansion in the machine substrate when mounted on carrier track. The high accuracy of this scale of ±1 µm/m, will further enhance the accuracy of the CMMs. DUKIN is using RELM scales in its future high-end models.
Furthermore, DUKIN Co. have incorporated different optical and laser Renishaw encoder systems into their CMM series to meet varying challenges. Systems include: Renishaw's TONIC with RGS gold scale (not recommended for new designs, alternative upgrade: RKLC scale), which masters to the substrate, and RLE laser interferometer-based encoder.
About DUKIN Co., Ltd.
DUKIN has a 27-year history and manufactures coordinate measuring machines (CMMs) for well-known international companies such as Samsung, Hyundai and KIA. The business also covers the FPD industry and produces a variety of high-precision equipment for current OLED and flat-panel display (FPD) processes. Products include ELA excimer laser-annealing equipment and automated optical inspection (AOI) equipment, and many use Renishaw's encoder product ranges. DUKIN is a long-time user of Renishaw CMM probes, from the PH10 series, to the later PH20 series, and now the advanced REVO series.
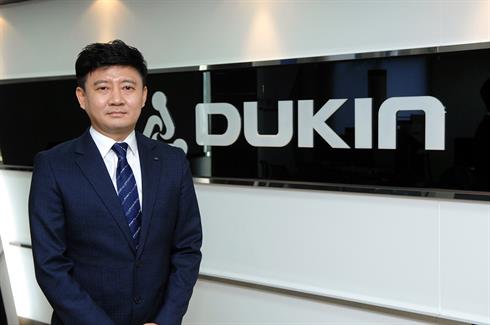