FORTiS-S™ sealed linear encoders now with lengths up to 4240 mm
Combining high-accuracy position measurement with robustness and reliability, the FORTiS™ enclosed linear absolute encoder series is designed to provide a solid foundation for CNC machining processes.
Since launch, FORTiS encoders have been adopted by many of the world's leading machine tool builders, who are enjoying the benefits of increased metrology performance, reliable sealing and the highest vibration resistance.
Renishaw now offers FORTiS-S linear encoders in even longer measuring lengths, helping to bring these advantages to larger machines such as giga presses, vertical turning lathes and outsized CNC machine tools.
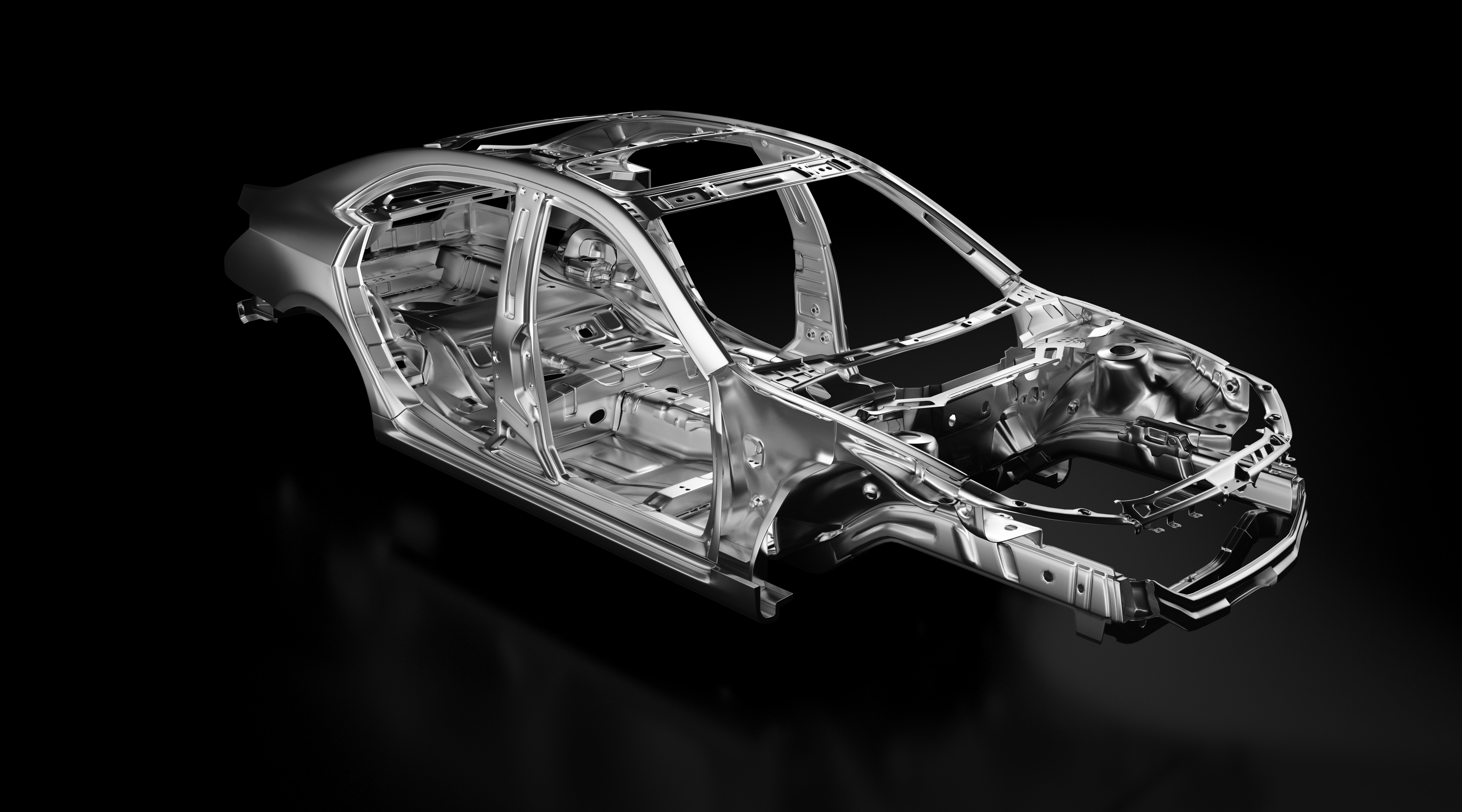
Car chassis
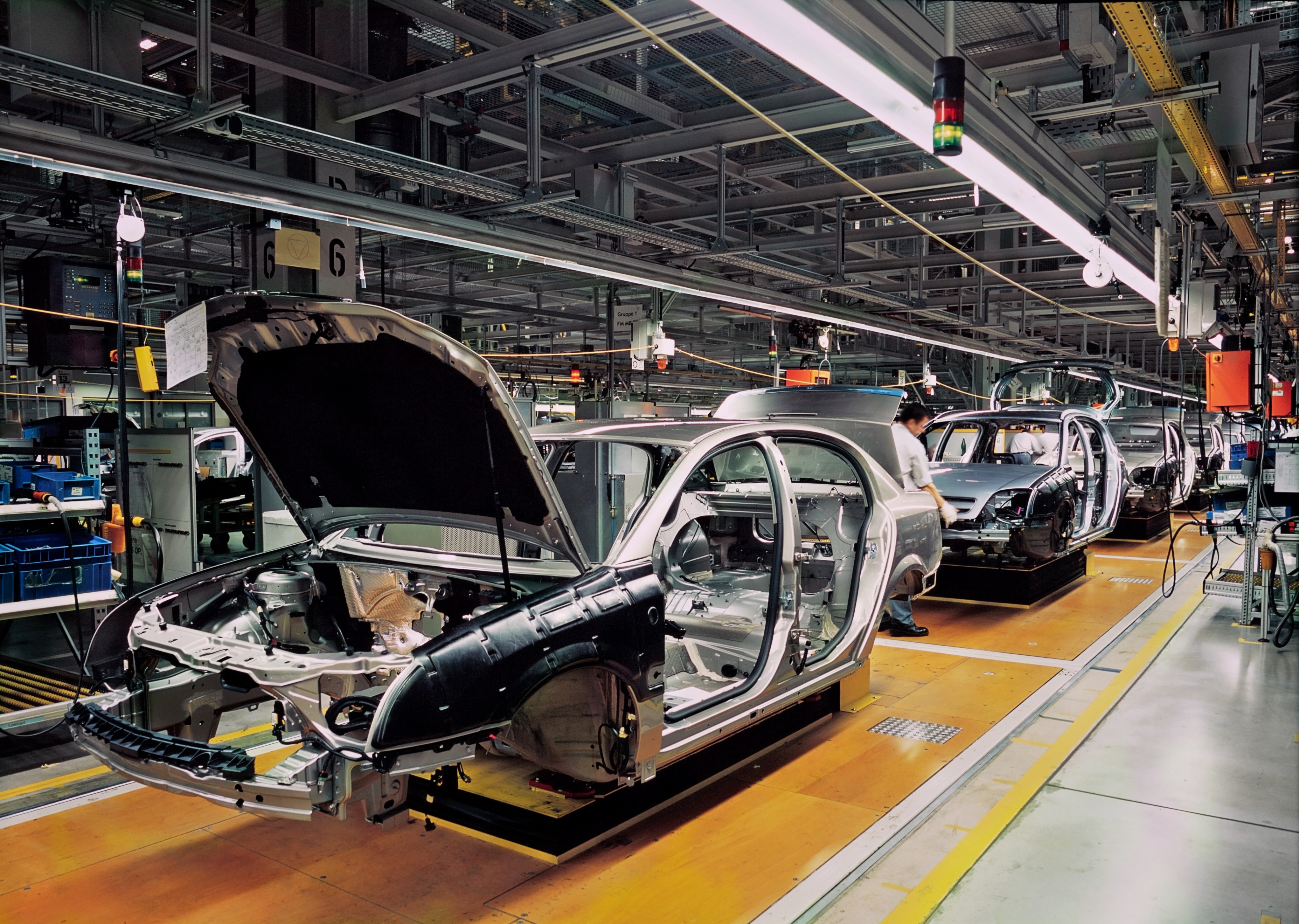
Car frames on a production line
'Giga casting' and ‘mega casting'
Giga casting, also known as mega casting, is an aluminium die casting technology that is being used by the automotive industry for casting large components, such as chassis modules which would traditionally be assembled from multiple stamped steel parts welded together.
The cast components have demanding requirements for geometry and structural integrity, but by eliminating large numbers of welding and fastening operations, giga casting offers the potential to achieve reductions in costs, energy usage, manufacturing time and weight.
In this application, a molten aluminium alloy is forced under high pressure into a reusable mould (die) installed on a giga press and the casting is then cooled and solidifies.
Each new casting is trimmed to remove overflows, measured, checked for imperfections, and sent to a CNC machine tool for finishing.
Large CNC machines are used at multiple stages throughout the commissioning, maintenance and ongoing operation of the casting process. One stage is to produce dies for the giga press. These large dies require accurate, high-precision machining, with a particular focus on process stability.
In such situations, the use of linear encoders with predictable thermal behaviour helps ensure the CNC machine produces dies to the required tolerances.
Another stage is the casting finishing, where mounting points are machined to accept the fitting of parts such as suspension components.
At this stage, the CNC machining is a time-critical operation to ensure consistent production flow, so the ability of the machine to carry out the operations quickly, and with precision and reliability, is of paramount importance.
For both of these stages, accurate and high-precision machining with a focus on process stability is essential. The availability of longer FORTiS enclosed encoder scales can significantly optimise the performance of large CNC machine tools.
Vertical turning lathes (VTLs)
VTLs play a crucial role in creating large components for industries such as aerospace, energy, and heavy machinery. To achieve optimal performance, machine designers explore innovations that enhance accuracy, reliability, and service life.
VTLs handle massive workpieces, often several metres in diameter and requiring long cutting cycle times. Precision motion control and closed-loop position feedback is important when creating intricate contours or critical features that sometimes require multiple motion axes to be carefully interpolated together.
The FORTiS linear absolute encoder has been designed to help maximise the performance of large machine tools such as VTLs.
Some machines using dual turrets/rams can benefit from employing dual readhead versions of the FORTiS encoder, so both turning heads can use the same scale, simplifying mechanical design.
Featuring high accuracy and predictable thermal behaviour, exceptional positional stability under high vibration, robust double lipseals, and now with measuring lengths up to 4.24 metres, FORTiS encoders are well-matched to the demands of these machines.
Large CNC turning or milling
As demand increases for ever tighter part tolerances, machine builders are choosing fully-closed loop positioning systems, where linear encoders provide direct feedback from the machine's linear axes, to deliver more accurate and more stable position measurements.
Long length FORTiS linear encoders deliver the accuracy, precision and dependability to help the machine designer to build bigger, without sacrificing machine tool performance.
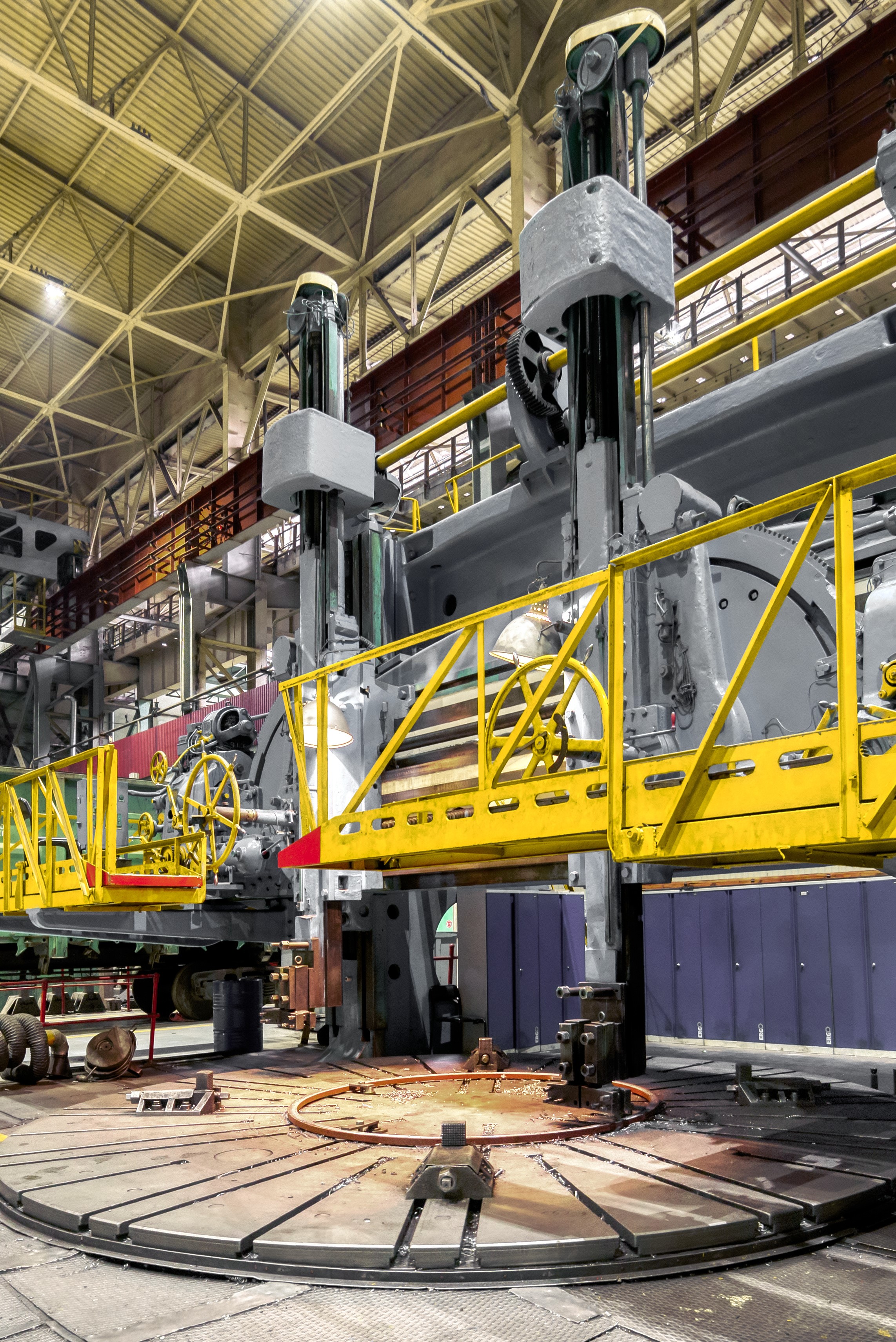
Vertical turning lathe (VTL)
When performing complex, time-consuming machining tasks on large metal billets, where parts need to be right first time — CNC machine accuracy and reliability become even more crucial. FORTiS linear encoders address these requirements effectively. They incorporate tuned mass damping to absorb intense vibrations during heavy cutting operations, and their high-resolution position feedback ensures smoother and more refined finishing.
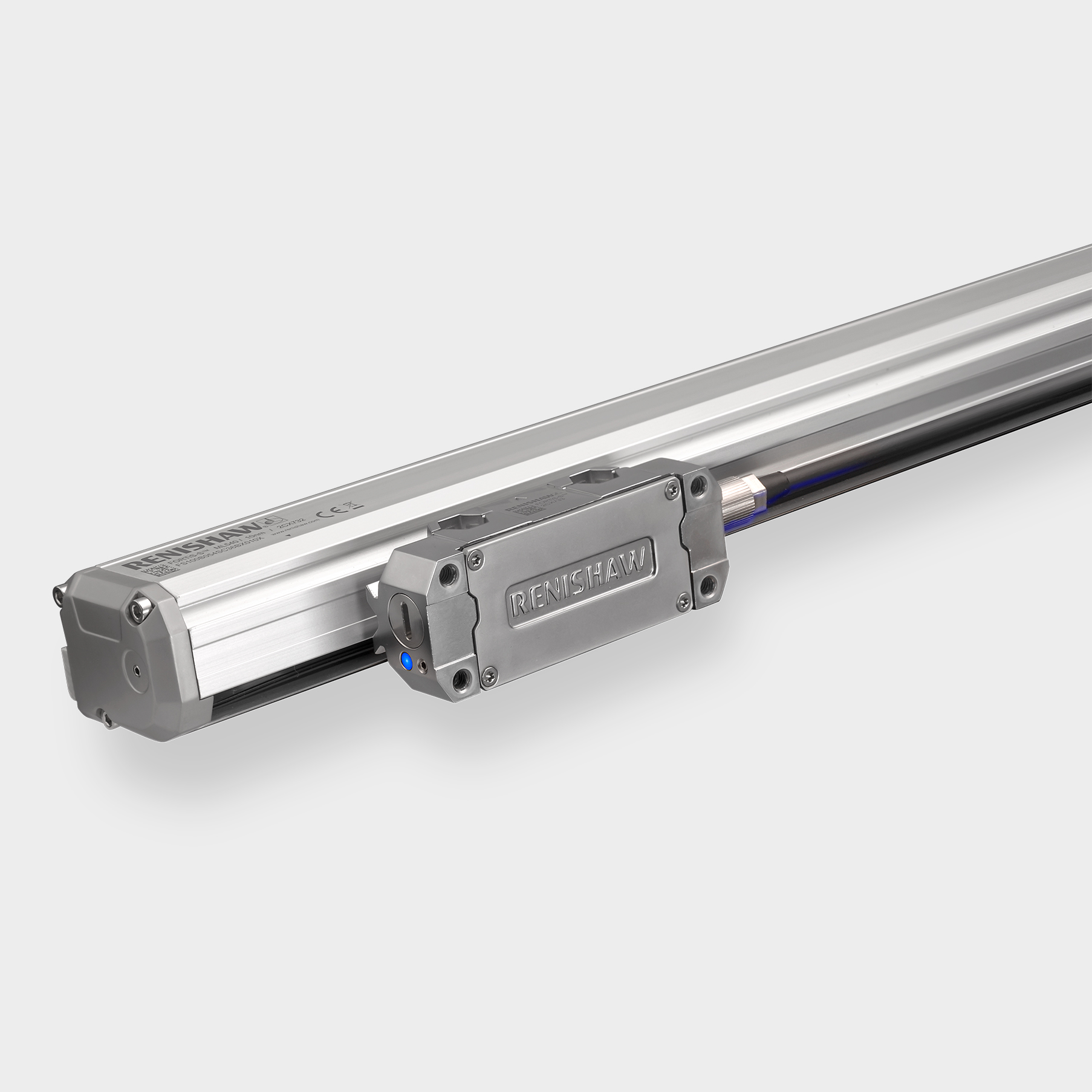
About the FORTiS encoder
The innovative FORTiS enclosed linear absolute encoder series is designed for use in harsh environments such as machine tools. It can also be used in Functional Safety applications up to SiL2 and PLd.
The FORTiS encoder design is built upon industry-proven RESOLUTE™ encoder technology and provides high resistance to the ingress of liquids and solid debris contaminants. It features an extruded enclosure with longitudinally-attached interlocking lip seals and sealed end caps.
The readhead body is joined to a sealed optical unit by a blade, which travels through the DuraSeal™ lip seals along the length of the encoder. Linear axis movement causes the readhead and optics to traverse the encoder's absolute scale (which is fixed to the inside of the enclosure), without mechanical contact.
The FORTiS absolute encoder series is designed to be robust and resistant to a wide range of mechanical shock and vibration effects. All FORTiS‑S encoders and FORTiS-N encoders, when installed with mounting spars, are rated up to 30 g which ensures dependable metrology for demanding motion control applications and even in the harshest environments.
In addition to its extruded enclosure, FORTiS encoders are also protected against contamination by a further level of sealing; the readhead optical unit (which runs inside the enclosure) is itself sealed to prevent contamination by liquids, swarf (cutting chips) and other debris.
Moreover, improved sealing of the FORTiS encoder enclosure reduces air leakage from the air purge system, resulting in lower operating costs and longer system life.
FORTiS encoders feature a range of serial communications protocols including BiSS C, BiSS Safety, Siemens DRIVE-CLiQ, FANUC, Mitsubishi, Panasonic and Yaskawa. The encoder dimensions also ensure space and bolt-hole compatibility with a wide range of alternative current and legacy systems.
Installation of FORTiS encoders is quick and easy. Unlike traditional installation methods, peripheral diagnostic equipment is not essential. Renishaw's patented set-up LED and carefully designed installation accessories ensure intuitive and right-first-time installation that is substantially faster than more conventional systems, even in restricted locations.
Summary
With customers increasing their requirements for higher precision whilst controlling costs, the FORTiS linear encoder meets these demands due to its high performance and durability. Now with increased measuring lengths up to 4.24 metres (167 inches), FORTiS linear encoders help provide the solid foundation for CNC machining processes that are key to the innovations that will shape our world, from increasingly efficient aircraft to giga castings on the next generation of automobiles.